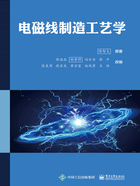
1.2 我国电磁线工业之今昔
1.2.1 电磁线工业发展沿革
绕组线随电机电器的出现而问世,现在已有一个多世纪的历史。最早制造绕组线绝缘物质采用天然材料,如棉纱、麻、草、蚕丝等。天然纤维也是大分子物质,有一定的电气绝缘能力,但是它们的耐热性能差、容易吸潮、机械强度不高,而且来源有限。为了弥补这些不足,早些时候人们还曾使用浸沥青的方法提高天然纤维物质的电气性能。沥青黏度很大,浸渍后漆层很厚,冷却后又变脆,丧失了柔软性,用它作为绝缘材料很不理想,于是人们转而应用干性油制备绝缘漆。
古人很早就懂得用桐油做浸漆,经桐油浸过的布、麻、棕、木材可以制成伞、斗笠、蓑衣、木盆甚至航船,桐油浸过的制品不仅防潮、防水性能良好,而且还有透气性好的特点,其成膜过程还能在自然条件下从外至内干燥透彻,涂膜表面光滑有优良的柔软性。
英国线缆公司(即现在的BICC公司)最早用二甲酚甲醛树脂与桐油反应,制成酚醛类树脂改性的干性植物油成膜物,再用煤油类溶剂溶解,成为油基性绝缘漆(Oil Base Enamell)。用油基性绝缘漆涂制的漆包线称为油性漆包线,它是世界上最早的漆包线。油性漆包线一出现,因其漆膜厚度薄而受到电机设计者和制造者的广泛采用。然而,油性漆包线的漆膜机械强度不高,在绕线圈和向槽内嵌线时易被刮伤或磨损,因此不得不在漆膜外面再绕一层棉纱作为补强层。同时,油性漆本身的耐热等级也只有A级。用油性漆包线绕制的电机不可能大幅度提高耐温等级和使用寿命。我国早期没有制造电机的能力,从日本大量购进的三菱电机几乎都是油性漆包线加单棉纱的绕组线圈。
第二次世界大战后期,美国杜邦化学公司首先发明用己内酰胺制成的聚合物——尼龙(Nylon)(聚酰胺的商品名称)。它立刻成为举世闻名的高强度合成纤维与各种元器件的高强度原材料。从此以后高分子聚合物再也不是实验室里令化学家们头疼的废料,它成了世界上许多专家努力探索、发掘甚至为之献身的广阔天地。半个多世纪以来,高分子聚合物领域变成了对科学技术进步、人类物质文明作出巨大贡献的神奇领域。许多科学家和社会学家把高分子科学的成就与电子科学、原子能科学的成就看成是20世纪中叶三件并驾齐驱的大事情。
1944年,美国和苏联相继成功研究出以电石加水产生的乙炔气体为原料制成的聚乙烯醇高分子材料,然后再和甲醛、乙醛或丁醛进行缩合生成聚乙烯醇缩醛素高分子化合物。它抽丝成纤维就是家喻户晓的维尼纶;它用呋喃甲醛及甲酚作溶剂制成的绝缘漆就是大家都知道的缩醛漆(Cpoly Vinyl Formar),美国称之为福美克斯,苏联称之为维尼弗莱克斯。
缩醛漆和缩醛漆包线的各项性能相比油性漆和油性漆包线有大幅度提高,于是人们将它称为高强度漆包线,因为用这样的线材绕制线圈,完全能放心地取消任何外加的补强材料,这是漆包线发展中一次大的技术飞跃。
几乎同时,欧洲成功研制以对苯二甲酸酯为原料的合成树脂,这种树脂纺成纤维即是“涤纶”,溶解在甲酚溶剂中制成的绝缘漆便是聚酯漆(Polyester),用它制成的漆包线便是聚酯漆包线。
聚酯漆包线的附着力、柔软度、耐高压、耐热冲击等性能并不高于缩醛漆包线,但它的耐热等级却比缩醛漆包线高了一个级别,比缩醛漆包线有更广阔的市场。
聚酯漆包线的出现使人们认识到含有芳香基的高分子树脂,其耐热性优于以脂肪链为主体结构的高分子材料。第二次世界大战结束后,各国都着力发展经济、提高科技水平,机电工业的迅速发展要求绝缘材料的发展也必须跟紧,一个又一个耐热等级越来越高的高分子合成漆在美国、西欧、日本研制成功,且立刻被应用于电气工业。
20世纪60年代至今,漆包线产品不但有了耐热等级在H级以上,温度指数达220级的耐高温品种,而且还研制出许多适用于特殊要求的特种漆包线。例如,自粘直焊性漆包线、耐冷媒漆包线、超导漆包线、无磁性漆包线及耐电晕漆包线。
在绕包线领域里,同样也取得很大发展,除电工纸绕包的纸包线因为十分适用于浸油变压器而保留至今外,其余耐热性差的绕包绝缘材料自20世纪50年代以来逐渐被耐高温材料代替。玻璃纤维是最早代替植物纤维和蚕丝的矿物纤维,玻璃纤维有很好的耐热性和绝缘性,且材料来源丰富。玻璃纤维绕包线最基本的品种是用双层玻璃纤维包裹裸铜线,内层用漆膜、薄膜或云母带等作为绝缘物质,外层加包玻璃纤维,国外在20世纪60年代即将其成功应用于各类电机中。
20世纪30年代之前,中国几乎没有电机制造工业,只有少数修理厂,所用少量线材大都依靠从外国进口。据查找到的资料显示,当时全国电线电缆产品总产量不过才1000吨左右。
1936年,中国电工器材筹备委员会成立,选址于昆明马街子办厂,由英国BICC公司承担人员培训工作并提供技术支撑,1937年起选派技术人员出国培训。1939年7月1日投产,正式更名为中国电工器材厂,即现今昆明电缆厂的前身。当时生产的电工产品种类很多,有电动机、变压器、开关等,在电缆产品中电磁线产品只占很小一部分。
中国电工器材厂培养了我国电线电缆行业的第一代技术专家。抗战胜利后,中国电工器材厂专家代表中国政府分赴东北、华北、上海、接收敌产并在沈阳、天津和上海建厂,这些厂就是后来沈阳电缆厂、天津609厂和上海电缆厂的前身。
中华人民共和国成立后,电线电缆工业受到国家重视和政策鼓励,而且电磁线产品的设备投资少、生产周期短和经济效益良好,适合民族资本家私人投资兴办。在第一个五年计划期间(1953—1957年),上海、天津、北京、广州开办了多家电磁线工厂。天津市漆包线厂的前身大新电工器材厂在1950年创办之初,仅10多名职工,但在1954年就开始研制高强度聚乙烯醇缩醛漆和高强度缩醛漆包线,成为国内最早开发合成树脂绝缘漆的厂家。20世纪50年代中期已拥有170多名职工,成为国内具有影响力的电磁线厂家之一。
1953年,苏联对我国重工业实行援建。在156项援建工程中有许多电缆厂,如沈阳电缆厂、湘潭电缆厂、郑州电缆厂等。在电缆厂内分设电磁线车间,提供了一批苏制г-20型和г-30型漆包机设备。国内电磁线生产厂采用苏联гocT标准。
1956年,国家实行公私合营的赎买政策,在全国范围内对分散的私营电磁线企业进行合并改造,提高各项管理水平,工厂走上了正规化道路,大大有利于提高产品质量和工厂的进一步发展。
1962年是全国“JO2”系列电机统一设计的关键时期,“JO2”电机的耐热等级为B级(130℃)。油性漆包线、缩醛漆包线和棉纱绕包线都未达到B级。聚酯漆包线和双玻璃纤维包线成为B级电机主绝缘体的绕组材料,而且一直沿用至20世纪90年代初期。
我国电磁线工业,尤其是漆包线产品在1962—1966年中,在品种、科技水平、生产工艺和装备上都有很好的发展,一些骨干企业做了很多扎实的技术工作。
1958年5月上海电缆研究所成立,在其帮助下,原天津机电公司组织进行缩醛漆和缩醛漆包线的质量攻关工作。用两年半的时间,解决了大线老化,小线耐刮一直不能达标的问题。保证了当时变压器、互感器、微电动机和电动工具的线材供应问题。
天津绝缘材料厂、常州绝缘材料厂和上海电磁线厂等单位,努力提高聚酯类产品(聚酯漆、聚酯镀膜等)的性能、稳定质量、扩大发展和应用范围,还开发研制了其他耐高温材料。
属于仪表系统的上海中国电工厂在20世纪60年代前期,研制开发了许多供仪表使用的细线和微细线。有些产品已经可以跻身世界先进行列。该厂技术人员设计的多层烘炉(7~8层)、多头收线(20~40头)漆包机显著提高了单台设备产能及劳动生产率,被迅速推广到全国,成为各厂漆包机的主要设备,直至目前还有相当数量的该类设备在运作。对原先从苏联引进的г-20型和г-30型漆包机也做了各种改进;针对当时普遍使用热扎铜杆(黑铜杆)的状况,采用铜杆刨光(剥皮)新工艺,使铜线表面质量得到明显改善;此外还进行了漆包圆铝线的试制。
在提高原有产品质量的同时,天津、上海一些主要厂家先后成功试制美国阿莫科公司(Amoco)已推向市场的AI-220耐高温漆与漆包线。如自粘漆包线、聚氨酯漆包线、复合涂层漆包线等也均取得实验室小试成果,还对漆包铜、铝扁线展开了试制工作。
根据专家们预测,于1965年年末我国电磁线工业水平与当时欧洲、日本等工业先进国家相比,只有10~15年的差距,完全有可能把这个差距进一步缩小。
1977年,在湖南衡山召开全国行业会议,总结了前面几个“五年计划”的成果。1979年原机械工业部在长沙召开电工产品科技发展规划会议,查找差距,确定目标,列出了各项重点课题项目,还在全国行业内进行具体分工承担。“六五计划”期间,电磁线生产有了很大起色,到“六五计划”后期,全国电磁线年产量突破10万吨。1984年,全国电线电缆企业在杭州成立行业协会。
20世纪80年代,经济发展迎来了新的契机,为电磁线工业的进步提供了良好的机会,主要变化如下:
计划经济转变为市场经济,行业增添了新的竞争活力。一大批县级企业和乡镇企业如雨后春笋般兴起,依靠政策优惠及特别适应“短、平、快”的行业特点与老牌国营骨干企业进行激烈的市场竞争,很快便在市场中脱颖而出。根据2001—2002年不完全统计,全国电线电缆厂有5000家左右,其中电磁线厂有800~1000家,90%以上的企业,厂龄在10年左右。
1980年,天津市漆包线厂首先从意大利Sicme公司引进了两台催化燃烧热风循环式卧式漆包机和全套测试仪器;接着,天津市电磁线厂从奥地利MAG公司引进了第一台VL-6型立式漆包扁线机;沈阳电缆厂引进奥地利MAG公司膜带绕包机。引进工程迅速引起了全行业的兴趣,据不完全统计,20世纪90年代初,有30余家工厂用4000余万美元从奥地利、德国、意大利、瑞士、日本和美国引进了120余台多种型号的电磁线制造设备(包括拉丝机、修模设备和检测仪器),占我国电磁线设备总数的10%左右,其中以漆包机为主。原福州电线厂从奥地利MAG公司引进了整个生产车间的设备,这是当时规模最大的引进工程,发挥了良好的经济效益。20世纪初,我国电磁线行业用约1.6亿美元从欧洲、日本等国家和地区购进400~450台/套设备,生产的电磁线约占我国电磁线总产量的35%。从20世纪90年代起,我国漆包线专用设备厂通过全国性技术引进,改进了设计理念、设计方向,由多头低速、多层烘炉的漆包机,转向快速高效的漆包机,国内在绕包机设备上也有了不少改进。
为了尽快提高我国电磁线的产品质量和技术水平,原机械工业部大力开展全行业范围的质量保证活动,了解学习日本的全面质量管理(T.Q.C)模式,推广ISO-9000质量认证体系,实行国内产品认证制度和产品出口UL认证。
为使中国的电磁线产品与国际市场接轨,我国以国际电工委员会(IEC)TC-55分组公告的技术文件为基础,参照工业发达国家和著名企业的技术标准,陆续修订了我国电磁线等级标准。近年来,我国电磁线的出口量不断增加,电磁线制造厂对国外标准十分重视,有的制造商还引用以上标准作为自己企业的内控标准。我国电磁线工业技术与国外的水平差距正在缩小。
随着国民经济进一步发展,国家完成了城乡电网改造工程,提出了开发中西部的宏伟计划并实施了三峡电力工程建设项目。这又为电磁线工业的发展提供了良好的机遇。一些技术含量高,替代进口和起着重要作用的绕组材料先后试制成功并进入市场,如用于三峡电力工程30万千瓦与60万千瓦机组的混合并丝绕包线,用于耐高温电机的聚酰亚胺胶粘烧结膜包线均已在国内形成生产能力。用于高电压、大容量变压器的换位导线国产化任务经过努力探索,由上海申沈电缆联合设备公司组织跨行业技术力量于1989年完成,并在第二年通过验收鉴定,其关键工装的设计技术获得实用新型国家专利。近年来,我国换位导线产品和设备发展十分迅速,已完全替代了进口产品,应用于变频电动机绕组的耐电晕漆包线的研发工作也在生产中得到推广。
根据1999年的全行业统计,20世纪末期,我国的电磁线生产厂经相关部门登记过的近800家,电磁线总产量接近30万吨,基本可以满足国内需求,还有小部分可以出口。我国已经赶上世界电磁线(绕组线)生产大国。21世纪以来,由于经济和电力事业的迅速发展,世界上许多著名的电磁线厂纷纷来中国“落户”,截至2007年年末我国电磁线年总产量突破100万吨。