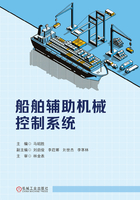
第二节 调节器及其作用规律
在反馈控制系统中,调节器是最重要的组成单元。当控制对象确定后,反映控制对象特性的各种参数也是既定的,因此调节器就对控制系统的动态过程品质起着决定性的影响。调节器的输入是被控量的偏差值e(t),调节器的输出是控制量p(t),用于改变执行机构的位置(如调节阀的开度),最终作用于控制对象。调节器的作用规律是指输出量p(t)与输入量e(t)之间的函数关系,即p(t)=f[e(t)],也就是说给调节器施加一个输入信号后,其输出量按何种方式进行变化。根据调节器输出的变化方向,调节器有两种类型,一是随着测量值的增加,调节器的输出也增加,称为正作用式调节器;另一种是随着测量值的增加,调节器的输出减小,称为反作用式调节器。
在船舶机舱中常用的调节器作用规律有:双位作用规律、比例(P)作用规律、比例积分(PI)作用规律、比例微分(PD)作用规律、比例积分微分(PID)作用规律等五种。这些作用规律中,除了双位作用规律之外,都还有作用强度的问题,例如比例系数的大小衡量着比例作用的强弱,积分时间的大小反映积分作用的强弱,微分时间的大小决定着微分作用的强弱。
一、位式调节器
双位作用规律的特点是,对应被控量的高限emin和低限emax,调节器只有两个输出状态(逻辑0和逻辑1),如图2-6所示。这种作用规律不能使被控量稳定在某个值上,而是使被控量在上限值和下限值之间上下波动。当被控量下降到下限值时,调节器的输出通过执行机构使被控量上升,到达上限值时,调节器的输出状态改变,被控量下降,如此周而复始。当被控量在上、下限之间变化时,调节器输出状态不变。

图2-6 双位作用规律
双位控制广泛应用于允许被控量在一定范围内波动的控制系统中,例如各种液位、压力和温度等的双位控制。下面以浮子式水位双位控制系统和双位式压力调节器为例加以说明。
1.浮子式水位双位控制系统
在机舱中,浮子式水位双位控制例子很多,如热水井的水位控制,主机日用燃油柜的水位控制以及小型辅锅炉的水位自动控制等。图2-7所示为采用浮子式辅锅炉水位进行双位控制的原理图。在锅炉外面的浮子室有汽管和水管分别与锅炉的汽空间和水空间相通,故浮子室内水位与锅炉水位一致。浮子与水位同步变化,浮子杆绕枢轴4转动,通过上、下限销钉5带动扇形调节板框架3绕枢轴4转动,调节板右边的永久磁铁12也跟着转动。当水位上升至接近上限值时,浮子杆与上面的销钉相接触,并带动扇形调节板框架3和同极性永久磁铁12绕枢轴4顺时针转动,当同极性永久磁铁12转至与它同极性的永久磁铁6相同高度时,由于同极性互相排斥,永久磁铁6立即被向上弹开,动触点11立即与静触点7断开,切断电机电源,给水泵停转,停止向锅炉供水。随着外界负荷不断消耗蒸汽,水位会不断降低,浮子连同浮子杆绕枢轴4逆时针转动,但调节板暂时不动。当水位下降到接近下限水位时,浮子杆与下面的销钉相碰,并带动调节板一起转动。当水位下降到下限值时,两同极性的永久磁铁12和6又正好相遇并互相排斥,动触点11立即与静触点7相接触,接通电机电源,并带动给水泵向锅炉供水。随着水位的上升,浮子连同浮子杆绕枢轴4顺时针转动,重复前面的过程。可见,只有水位处在上、下限值时,调节器的输出状态才发生改变,而水位在上、下限之间变化时,调节器的输出状态不变,例如水位从上限值下降时,电机保持断电,水位从下限值上升时,电机保持通电。

图2-7 浮子式辅锅炉水位双位调节器
1—浮子室 2—浮子 3—扇形调节板框架 4—枢轴 5—上、下限销钉 6、12—同极性永久磁铁 7—静触点 8—开关箱 9—转轴 10—转杆 11—动触点
在调节板上对应浮子杆的上、下限位置各有三个销钉孔,调整上、下限销钉5的位置,可调整水位的上、下限值,但如果把上、下限销钉之间的距离调整得太小,虽然可以减小水位的波动范围,但将导致电机起停频繁,这是不利的。
2.双位式压力调节器
双位式压力调节器也称为压力开关。压力开关的种类较多,原理也不尽相同,但其主要的外在功能都是一样的,即根据测量压力的上限值和下限值输出不同的开关量信号,用于船舶辅锅炉的蒸汽压力和日用海、淡水压力等的双位控制。
下面以YT-1226型压力调节器为例加以说明。图2-8为YT-1226型压力调节器的结构原理图。被测量的压力信号P接至测量室,通过波纹管转换为力信号作用于比较杠杆,产生测量力矩。此外杠杆上还作用着由给定弹簧产生的给定力矩和由幅差弹簧产生的幅差力矩。
当输入信号P处在压力的下限值时,比较杠杆处于水平位置。这时动触点离开静触点1,闭合于静触点2。此时,作用螺钉与幅差弹簧盘之间存在一定的间隙,幅差弹簧对杠杆不起作用。当P增大时,杠杆绕支点逆时针转动,通过拨臂使舌簧的下边框左移,通过舌形片使跳簧压缩,贮存弹性能。同时,作用螺钉与幅差弹簧盘的间隙逐渐消失,当杠杆继续转动时,不仅要克服给定力矩,还要克服幅差力矩。当杠杆转过某个角度,即被测量压力P达到上限值时,舌簧舌片正好与舌簧簧片处在同一平面,跳簧有了释放能量的机会,迅速把舌簧簧片弹开,使动触点离开静触点2而与静触点1闭合。当压力P降低时,杠杆绕支点顺时针转动,当杠杆回到水平位置时,舌簧舌片又与舌簧簧片处在同一平面,跳簧再次把舌簧弹开,使动触点离开静触点1,合到静触点2。当压力P在上限值和下限值之间变化时,跳簧保持原状态不变,也就是调节器的输出状态不变。

图2-8 YT-1226型压力调节器结构原理图
给定弹簧调整的是压力开关的下限值,用PL表示,幅差调整旋钮用于调整幅差ΔP,压力开关的上限值PH等于下限值PL加上幅差ΔP,即PH=PL+ΔP。因此,压力开关的上限值是通过调整幅差来设定的。
YT-1226型压力调节器开关给定指针的指示范围是PL=0~0.2MPa,幅差调整旋钮上标记有10个格的刻度档,对应的幅差范围为ΔP=0.07~0.25MPa。幅差调整旋钮所调的格数X可根据公式进行估算。但由于刻度精度比较低,在实际使用时应该进行实验测定或现场调整。
二、比例调节器
比例作用规律(P)是指调节器的输出量p(t)与输入量e(t)成比例变化,即
p(t)=Ke(t)
其中,K称为比例系数。K越大,在输入相同的偏差e(t)时,调节器输出量p(t)也越大,我们就说比例作用越强。反之,K越小,比例作用越弱。采用比例作用规律的调节器,称为比例调节器。其开环阶跃响应特性如图2-9所示。

图2-9 比例作用规律开环阶跃响应特性
1.比例(P)作用的控制过程
图2-10给出了一个对单容(单容控制对象是指只有一个存储物质或者能量容积的控制对象)水柜的水位进行比例规律控制的简单例子。它虽然不能直接用于实际的控制系统,但它所揭示的比例作用规律和特点却具有普遍意义。
图2-10中,水柜中的实际水位h是被控量,其给定值为h0。在初始平衡状态下,给水流量Qi与出水流量Qo相等,水位稳定在h0上,偏差e(t)=0。此时,水柜的出水流量Qo对应水柜的额定负荷,其调节阀开度p(t)为全开的一半左右。这样,不论负荷怎样变化,调节阀开度都有变化的余地,都能对给水流量加以控制。

图2-10 浮子式水位比例控制系统示意图
如果在初始平衡状态下,突然开大出水阀,出水流量阶跃增大(即增大水柜的负荷)。由于给水流量Qi暂时未变,水位会连同浮子和浮子杆一起下移,带动杠杆绕支点顺时针转动,开大给水调节阀,增加对水柜的给水流量Qi,直到Qi=Qo为止,水位才会稳定在比给定水位h0略低的值上。相反,若突然关小出水阀,出水流量阶跃减少(即减少水柜的负荷),水位连同浮子和浮子杆一起上移,通过杠杆作用使调节阀关小,减少给水流量Qi,直到Qi=Qo为止,水位又会稳定在比给定值h0略高的值上。当对水柜施加扰动(出水阀开度变化)后,水位的实际值(浮子的位置)h偏离给定水位h0的数值就是偏差值e。
对照反馈控制系统的组成,不难看出,在上述水位控制系统中,控制对象为水柜,杠杆起到调节器的作用,浮子是测量单元,而给水调节阀就是执行机构,被控量是水位高度h,被控量的设定值实际上就是浮子杆的长度l。
从图2-10可见,p(t)与e(t)的关系为

式中,K=a/b,是比例调节器放大倍数。
改变杠杆长度比a/b,可改变K值。左移可调支点,a减小,b增大,则K减小。反之,则K增大。K是衡量比例作用强弱的参数,K若大,系统出现一个较小的偏差e(t),调节器(本例中是杠杆)就能使调节阀开度p(t)有一个较大的变化,给水流量的变化量也比较大,克服扰动的能力强,其比例作用强。K若小,被控量出现较大偏差e(t)时,调节器指挥调节阀开度变化不大,克服扰动的能力弱,比例作用就弱。
比例作用规律的优点是,调节阀的开度能较及时地反映控制对象负荷的大小。负荷变化大,偏差e(t)就大,调节阀开度能够及时地成比例变化,对被控量控制比较及时。正因为如此,比例调节器的应用比较广泛,它也是其他作用规律(位式作用除外)的基础。但是,比例作用规律存在的缺点也是明显的。当控制对象受到扰动后,在比例调节器的控制作用下,被控量不能完全回到给定值上,只能恢复到给定值附近。被控量的稳态值与给定值之间必定存在一个较小的静态偏差,这是比例作用存在的固有的、不可克服的缺点。
比例作用之所以存在静态偏差是由于调节器的输出与输入之间存在一一对应的硬性关系,从p(t)与e(t)的关系式可以清楚地看出,调节器的输出变化将依赖于偏差的存在而存在。结合系统的工作过程,也不难理解这点。设想在初始平衡状态下突然开大出水阀时,由于Qi<Qo,水位下降,导致出现偏差e(t),在调节器的作用下,给水阀开度增大,给水流量Qi增大,限制了水位的降低并使水位逐渐向给定值靠近,直至Qi=Qo为止,此时的水位必然要比原来略有降低。因为假如水位又回到了原来的设定值,那么偏差e(t)将不再存在,调节器又回到原来的输出,给水阀的开度又将回到原来的开度,最终又将导致Qi<Qo,系统无法平衡。
显然比例作用规律中,如果放大倍数K较大(比例作用越强),那么稳态时只要有一个较小的静态偏差,调节阀就会有一个较大的开度变化以适用负荷的要求。因此,K越大,稳态时静态偏差越小,反之亦然。但不可能通过无限制地增加比例系数的方法来达到消除静态偏差的目的,而且当比例系数大到一定程度时将导致系统发生振荡。
比例控制系统虽然存在静态偏差,但这个偏差值是不大的,与自平衡对象受到扰动后,靠自平衡能力使被控量自行稳定在新稳态值上的变化量相比较要小得多,动态过程进行也要快得多。因此,比例调节器广泛应用于对被控量稳态精度要求不是很高的场合。
2.比例带(PB)
比例系数K虽然可以衡量比例作用的强弱,但K通常是一个带量纲的量,不同控制系统之间,其比例作用的强弱不便于比较。因此,在实际控制系统中,更多地采用一个无量纲的参数来衡量比例作用的强弱,这个无量纲的参数就是比例带(PB),有时也称为比例度δ。
比例带(PB)(或比例度δ)是指调节器的相对输入量与相对输出量之比的百分数,即

式中,e是被控量的变化量(偏差值);Ximax是被控量允许变化的最大范围,称为全量程;被控量的变化量与全量程的比值e/Ximax是调节器的相对输入量;p是调节器的输出量;Xomax是输出量的最大变化范围,p/Xomax是调节器的相对输出量;R=Xomax/Ximax是量程系数,在单元组合仪表(指把控制系统的各功能单元分别制成一台独立的仪表,包括测量仪表、显示仪表、调节器、执行器等,各个仪表之间用统一的标准信号联系)中,R=1。这样,PB=1/K×100%,显然,比例带PB与放大倍数成反比。
比例带(PB)的物理意义可以这样理解,即假定调节器指挥执行机构变化全行程(例如调节阀从全关到全开或从全开到全关),需要被控量的变化量占其全量程的百分数就是比例带。例如PB=100%,说明被控量变化全量程的100%,调节器将指挥执行机构变化全行程的100%,若PB=50%,说明只需被控量变化全量程的一半,调节器就能使调节阀开度变化全行程。若PB=200%,则说明被控量变化了全量程,调节阀的开度只变化了全行程的一半。可见,比例带PB越小,在被控量偏差占全量程百分数相同的情况下,调节器的输出变化也越大,克服扰动能力越强,比例作用也就越强;反之,比例带(PB)越大,比例作用越弱。比例带是比例作用规律极为重要的参数,当组成控制系统的控制对象确定以后,比例带(PB)的大小,对控制系统动态过程品质好坏起着决定性的影响。若(PB)选得太大,比例作用很弱,克服扰动的能力就弱;动态过程虽然很稳定,没有波动,但最大动态偏差emax也大,过渡过程时间ts或许会拖得很长,稳态时静态偏差ε也比较大。若PB选得太小,比例作用很强,稍微出现一点偏差就会使执行机构的动作大幅度变化,容易造成被控量的大起大落,系统的稳定性变差。同时,也会加长过渡过程时间ts。因此,对一个实际控制系统来说,要根据控制对象的特性,调定合适的比例带(PB),以保证一个控制系统具有最佳的动态过程。在一般情况下,控制对象惯性大的控制系统,可使比例带(PB)小一点,如温度、黏度等控制系统,其控制对象惯性比较大,可选定PB=50%左右。反之,对于控制对象惯性小的控制系统,比例带可适当选定大一点,如液位控制系统,其控制对象惯性都比较小,可选定PB=70%~80%。在调节器上都设有比例带调整旋钮,用来设定比例带。比例带的可调范围,对不同类型的调节器不尽相同,一般在5%~300%之内。
3.气动比例调节器
图2-11所示为一个反作用式(指调节器的输入信号增大,而输出信号减小)气动比例调节器,即随着测量值的增加,调节器的输出不断减小。调节器由杠杆、测量波纹管、反馈波纹管、给定弹簧、喷嘴挡板机构和气动放大器组成。其中,测量波纹管的输入来自测量单元输出的标准压力信号,其压力大小反映被控量的实际值。气动放大器的输出一方面作为调节器的输出送到气动执行机构,另一方面作为反馈信号送到反馈波纹管。杠杆主要受到来自测量波纹管的测量力矩M测、来自反馈波纹管的反馈力矩M反和来自给定弹簧的给定力矩M给。在初始平衡态下,这三个力矩处于平衡状态,即M给=M测+M反,杠杆保持平衡,喷嘴与挡板之间的距离保持不变,调节器的输出不变。

图2-11 气动比例调节器
假设测量值发生一个阶跃变化,例如阶跃地减小某个值,则由于M测减小,杠杆失去平衡,将顺时针转动,喷嘴靠近挡板,使得喷嘴背压增加,经过放大器放大之后,调节器的输出也增加。这个增大的输出一方面作为调节器的输出,另一方面送至反馈波纹管,使得M反增加,阻止挡板继续靠近喷嘴。当重新满足M给=M测+M反时,杠杆又恢复到新的平衡,调节器输出不再变化。
设测量值的变化为Δp测,调节器的输出变化为Δp出,由于给定值没有变化,即给定力矩的变化为零,根据杠杆的平衡原理,有
Δp测·F测·l2+Δp出·F反·l3=0
式中,F测和F反分别为测量波纹管和反馈波纹管的横截面积,l2和l3分别为测量力臂和反馈力臂的长度。因此

上式表明,调节器的输出变化和输入变化是成比例的,其中比例系数为

由于测量波纹管和反馈波纹管的截面积通常是相等的,而测量力臂l2是固定不变的,因此移动反馈波纹管的位置,即改变反馈力臂的长度l3可以调整比例调节器的比例系数K,或者说调整其比例带(PB)。比例系数K为负值,表明这是一个反作用式调节器。
在调节器的工作过程中,实际上在杠杆上还会产生一些附加力矩,例如喷嘴气流产生的反作用力矩和杠杆偏转过程中各个弹性部件产生的变形力矩等。但由于附加力矩很小,而且理论上可以证明,只要气动放大器的放大倍数足够大,这些附加力矩是可以忽略不计的,因此在上述的分析过程中对这些附加力矩未予考虑。
以上对比例调节器工作原理的分析表明,比例作用是通过将输出进行直接负反馈实现的,负反馈的强度决定着调节器的比例带。在调节器的实物上一般设有一个比例带调整旋钮,通过比例带调整旋钮可以左右移动反馈波纹管的位置,即调整反馈力臂l3的长度。左移反馈波纹管,l3增长,负反馈增强,K减小,PB增大,比例作用减弱;反之亦然。
应当注意的是,当调节器接入实际的控制系统中时,测量值一般是不会阶跃变化的,而调节器的输出也将送至执行机构,作用于被控对象,形成闭环系统。此时,在调节器的控制作用下,被控量的测量值将朝着偏差减少的方向变化。但无论如何,测量值也不可能恢复到和原来相等,因为假如测量值恢复到原来的大小,则杠杆的位置、喷嘴与挡板的距离以及调节器的输出都将复原,无法适应新的工况下物质或能量的平衡。
三、比例积分调节器
比例积分作用规律是指调节器的输出量随输入量做比例积分变化。采用这种作用规律的调节器叫比例积分调节器,简称PI调节器。显然,在PI调节器中,含有积分作用。
1.积分(I)作用规律
所谓积分作用规律是指调节器的输出与输入的积分成比例,也就是说调节器是一个积分单元,即
p(t)=S0∫e(t)·dt
式中,S0是积分系数。
可以看出,积分输出取决于偏差e(t)的大小和偏差存在时间的长短,只要存在偏差,偏差随时间的积累就不能停止,调节器输出p(t)就会发生变化,直到偏差等于零为止,执行机构才能稳定在某一位置而不再变化。换言之,具有积分作用规律的调节器具有消除静态偏差的能力,这是积分作用规律的突出优点。但是,与比例作用规律相比较,积分作用规律对被控量的控制显得不及时。在比例作用规律中,调节器输出的变化和偏差是同步的,或者说是及时的,而在积分作用规律中,即使偏差很大,在刚开始的时候,由于时间很短,调节器的输出也很小,只有随着偏差存在的时间不断增长,积分作用的输出才越来越大,导致调节器对被控量的控制不及时。在偏差减少时,这种控制不及时表现为不能及时减少使执行机构的动作幅度,从而导致调节过头,造成被控量的大起大落,降低了控制系统的稳定性。图2-12示意性地画出了控制系统在相同扰动情况下,采用比例调节器和积分调节器的控制系统动态过程曲线。图2-12中曲线b是积分控制过程,曲线a为比例控制过程。在出现偏差的初期,由于积分作用控制很不及时,所以最大动态偏差emax较大。后期由于积分作用越来越强,调节过头,造成被控量振荡,系统稳定性降低。正因为积分作用存在这些缺点,在实际控制系统中,极少采用纯积分作用的调节器,而是将积分作用与比例作用相结合,形成比例积分作用规律的调节器,即PI调节器。

图2-12 比例控制和积分控制的比较
2.比例积分(PI)作用规律
比例积分作用是指在比例作用的基础上加入积分作用而得到的一种作用规律,即

式中,K是PI调节器的比例系数,Ti=K/S0是积分时间。
在PI调节器中,比例作用能使调节器的输出及时响应偏差的变化,起着主导作用,而积分作用是辅助的,只是用它来消除静态偏差。
衡量比例积分作用强弱的参数有两个,即比例系数K和积分时间Ti。其中,比例系数K是衡量比例作用强弱的参数,在实际控制系统中,一般不用K而是用比例带PB,比例带的大小对比例作用强弱的影响及比例带的物理意义与比例作用规律相同。积分时间Ti是衡量积分作用强弱的参数,它具有时间的量纲(秒或分)。从比例积分作用规律表达式可以看出,若Ti小,则积分输出部分大,即积分作用强;反之,若Ti大,则积分输出部分小,积分作用弱。
假定给比例积分调节器施加一个阶跃的输入偏差信号,其阶跃量为常数e(在实际系统中,偏差信号一般不会阶跃变化,但在开环实验中,人为地给PI调节器施加一个阶跃的输入信号很容易做到),则

其中,第一项为比例输出,在阶跃输入瞬间,比例作用把输入量e放大到K倍的阶跃输出Ke。由于此时时间t=0,故没有积分输出。第二项Ket/Ti是积分输出,它与时间t保持线性关系,其斜率为Ke/Ti。据此,可画出比例积分调节器开环阶跃输出特性曲线,如图2-13所示。

图2-13 比例积分调节器开环阶跃输出特性
从图2-13可见,在输入阶跃偏差信号的瞬间(t=0),先有一个阶跃的比例输出Ke。此时不论偏差多大,其积分输出为零。以后随着时间的增长,积分呈线性关系输出。当时间进行到t=Ti时,p(t)=2Ke,即调节器的积分输出部分等于比例输出(BC=AB)。由此得到PI调节器中积分时间Ti的物理意义为积分时间Ti是在给PI调节器输入一个阶跃的偏差信号时,其积分输出达到比例输出所需的时间。在工程上,标定或测定调节器积分时间时,一般规定在比例带为100%的条件下进行。
在PI调节器上设有两个旋钮,一个用于整定比例带(PB),另一个用于整定积分时间Ti。Ti的整定一定要合适,既要能保证控制系统稳定性的要求,又要能在较短的时间内使系统消除静态偏差。在整定Ti值时,切忌把Ti值整定得太小,否则由于积分作用太强,将导致系统的稳定性变差。如果Ti值不能进行准确地整定,那么选取Ti时,可以采用宁大勿小的策略。因为Ti值略微偏大时,尽管积分作用偏弱,但只会使消除静态偏差的时间稍长而别无它害。积分时间Ti的整定范围一般在3s至20min之内。控制对象惯性大的控制系统,选取Ti值要大一些。控制对象惯性小的控制系统,选取Ti值可以小一些。
在比例积分调节器中,如果把积分时间Ti设定到∞,则相当于切除积分作用,而成为纯比例调节器。若将积分切除而成为纯比例调节器,则应将比例带(PB)整定在一个恰当值,以获得控制系统满意的动态过程。若要加入积分作用(其Ti不是∞),则此时的比例带(PB)要比纯比例作用时略大一些,以抵制由于积分作用的加入而产生的系统动态过程振荡倾向。比例积分调节器是在实际控制系统中应用最广泛的一种调节器。
3.气动PI调节器
气动比例积分调节器是在气动比例调节器的基础上加上积分作用形成的,图2-14所示为一种典型的比例积分实现方法。它主要由测量波纹管C、给定波纹管G、正反馈波纹管Z、负反馈波纹管F、气动放大器、1∶1跟随器、比例带调节阀Rp、积分阀Ri、积分气容、恒气阻R、杠杆和喷嘴挡板机构等组成。其中,4个波纹管的截面积相同,且以杠杆支点为中心布置成左右对称,即l1=l2,l3=l4。测量波纹管的输入来自测量仪表送来的被控量测量输出,给定波纹管的输入来自给定值旋钮设定的给定压力。气源分别给放大器、喷嘴挡板机构和1∶1跟随器供气。当调节器处在平衡状态时,4个波纹管作用到杠杆上的力矩相互平衡,杠杆静止不动,喷嘴和挡板的间距不变,调节器的输出保持不变。

图2-14 气动比例积分调节器原理图
现假设测量压力阶跃增加,则杠杆失去平衡,顺时针偏转,挡板靠近喷嘴,喷嘴背压升高,经放大器放大后,调节器的输出也阶跃增大。由此可见,这是一个正作用式调节器。
增大的输出分为4路,一路作为调节器的输出送至执行机构;第二路通过恒气阻直接送到负反馈波纹管F;第三路经过比例带调节阀Rp,再经恒气阻送至正反馈波纹管Z;第四路经积分阀Ri向积分气容充气,再经1∶1跟随器送至正反馈波纹管Z,其中1∶1跟随器的输出总是随输入的变化而变化,在气路中起到抗干扰的作用。
在调节器输出增大的初始时刻,由于积分阀和积分气容组成的惯性环节,第四路产生的正反馈暂时不起作用。此时,由于Rp的存在,正反馈和负反馈的强度是不一样的,只要Rp不是全开,那么负反馈强度总是大于正反馈强度,因此其综合效果还是负反馈。这一综合负反馈阻止了杠杆的顺时针偏转,即阻止挡板继续靠近喷嘴,调节器的输出P出也暂时不再增大。显然,测量值增大得越多,即偏差越大,调节器输出的增大也越多,这是一个比例输出的过程。比例带调节阀Rp用于调整综合负反馈的强度,即调整比例带的大小。关小Rp(气阻增大),正反馈减弱,综合负反馈增强,比例作用减弱,比例带(PB)增大;反之,开大Rp(气阻减小),正反馈增强,综合负反馈减弱,比例作用增强,比例带(PB)减小。
但是调节器的输出不会稳定在比例输出上,因为随着时间的增加,由Ri和积分气容组成的惯性环节输出将逐渐增大,通过1∶1跟随器送至正反馈波纹管,使得正反馈逐渐增强,综合负反馈逐渐减弱,调节器的输出将在比例输出的基础上继续增大,这是积分输出过程。由此可见,在气路中,调节器的积分作用是通过惯性环节正反馈实现的。积分阀Ri用于调整积分时间,关小Ri(气阻增大),惯性环节的惯性增大,积分时间Ti增大,积分作用减弱;反之,开大Ri(气阻减小),惯性环节的惯性减小,积分时间Ti减小,积分作用增强。
当调节器接入闭环系统时,在调节器的控制作用下,被控量的测量值将朝着偏差减小的方向变化,即测量值会不断地靠近给定值。当系统达到平衡状态时,调节器的输出不再变化,此时杠杆处于平衡状态,即

式中,pZ、pC、pF和pG分别为正反馈波纹管、测量波纹管、负反馈波纹管和给定波纹管的压力,FZ、FC、FF和FG分别为正反馈波纹管、测量波纹管、负反馈波纹管和给定波纹管的面积,l1、l2、l3和l4为力臂。
根据气路的工作原理,当调节器的输出不再变化时,正、负反馈波纹管的压力将最终达到相等,即pZ=pF。由于FZ=FC=FF=FG,且l1=l2,l3=l4,因此在闭环控制系统达到平衡状态时,必然有pC=pG。换句话说,只要测量值pC与给定值pG之间存在偏差,调节器的控制作用就一直存在,直到pC=pG为止。由此也可以说明比例积分调节器在实际中是如何消除静态偏差的。
四、比例微分调节器
尽管比例调节器的输出能够与偏差同步变化,对系统的控制比较及时,但当控制对象的惯性比较大时,扰动出现的初期,被控量不可能在短时间内出现较大的偏差。而比例控制又是根据偏差大小来改变调节器输出的。因此,在这种情况下,比例控制作用就显得不够及时了。控制对象惯性越大,这种现象越严重。为了克服这种控制不及时的现象,需要在比例调节器的基础上增加微分作用。
1.微分(D)作用规律
所谓微分作用规律是指调节器的内部采用了一个微分环节,其输出与偏差对时间的微分de(t)/dt,即偏差变化速度成比例,表达式为

式中,Sd为微分系数。
显然,微分作用的输出能在偏差绝对值还很小时就根据其变化速度,提前输出一个控制量,及时抵御扰动。从这个意义上说,微分作用具有超前控制的能力,或者说微分作用有抵制偏差出现的能力。上述表达式表示的是理想的微分作用,但这种理想的微分作用在实际中是难以实现的,因此在调节器中微分作用都采用实际微分环节,其开环阶跃响应曲线如图2-15所示。

图2-15 实际微分作用的输出特性
图2-15表明,给实际微分环节施加一个阶跃的偏差输入信号后,它先有一个较大的阶跃输出,起到超前控制作用,尽管偏差依然存在,但微分输出随即按指数规律逐渐减少,最后消失为零。因此,微分作用不能单独应用于调节器并构成控制系统,它只能与比例(P)作用或比例积分(PI)作用结合在一起,组成比例微分(PD)调节器或比例积分微分(PID)调节器。
2.比例微分(PD)作用规律
比例微分作用是指在比例作用的基础上加入微分作用而得到的一种作用规律,即

式中,K是比例微分作用规律中的比例系数,在实际调节器中,不是用K而是用PB来表示PD调节器比例作用的强弱,Td=Sd/K称为微分时间。
在比例微分作用规律中,比例作用是主要的,它决定调节器的最终输出变化量。微分作用只起超前控制的辅助作用。
上述PD作用规律表达式中的微分部分仍然只是理想的微分作用,在实际的PD调节器中采用的是实际的微分环节,PD调节器的开环阶跃响应特性如图2-16所示。特性曲线表明给PD调节器施加一个阶跃的偏差输入信号后,它首先有一个阶跃的比例加微分的复合输出,然后微分输出逐渐消失,最后消失在比例输出上。微分时间Td衡量微分大小输出消失的快慢,或微分输出保留的时间长短。若Td大,说明微分作用消失得慢,则微分作用强;若Td小,说明微分作用消失得快,则微分作用弱。因此,微分时间Td的大小,是衡量微分作用强弱的参数。

图2-16 比例为微分调节器输出特性
在PD调节器上有两个旋钮,一个是比例带(PB)调整旋钮,另一个是微分时间Td调整旋钮。如果把微分时间旋钮调整到Td=0,相当于切除微分作用,这时调节器就成为纯比例调节器。一般来说,控制对象惯性很小的控制系统,其所采用的调节器可不加微分作用。而控制对象惯性大的控制系统,加入微分作用,可以有效地改善控制系统的动态过程。在PD调节器中,加进微分作用后,其比例带(PB)可比纯比例控制时略小些。因为微分作用能实现超前控制,具有抵制偏差出现的能力,尽管PB小一些,也能保证系统动态过程的稳定性,而且较小的PB有利于减小静态偏差。因为PD调节器与比例调节器一样,是不能消除静态偏差的。
3.气动PD调节器
微分作用的特点是在输入变化的瞬间会有较大的输出,然后逐渐消失为零。它可以同比例(P)作用或比例积分(PI)作用结合在一起形成比例微分(PD)或者比例积分微分(PID)调节器。图2-17所示为气动比例微分调节器的一种实现方法。
假设在初始平衡状态下,测量值阶跃增加,则由于挡板靠近喷嘴,放大器的输出也阶跃增加。放大器的输出一路作为调节器的输出,另一路经过由微分阀Rd和微分气室Cd组成的惯性环节送到负反馈波纹管F。由于惯性环节的滞后效应,初始时刻的负反馈强度较小,因此在测量值增大的瞬间,调节器的输出较大。随着惯性环节的输出按指数规律逐渐增强,负反馈也逐渐增强,调节器的输出将按指数规律逐渐减弱,最终负反馈波纹管的压力将稳定在与调节器输出相等的压力上,调节器输出也不再变化。此时

图2-17 气动比例微分调节器原理图
pFFFl1+pGFGl3=pCFCl2
式中,pF、pG和pC分别为负反馈波纹管、给定波纹管和测量波纹管的压力;FF、FG和FC分别为负反馈波纹管、给定波纹管和测量波纹管的面积;且FF=FG=FC;l1、l2和l3为力臂。
若只考虑变化量,则
ΔpFFFl1+ΔpGFGl3=ΔpCFCl2
由于给定值没有变化,即ΔpG=0,因此

当给定值不变时,测量值的变化实际上就是偏差,即ΔpC=e,而当负反馈回路的惯性过程结束时,负反馈波纹管的压力变化和调节器输出压力变化相等,即ΔpF=Δp出,因此

从以上分析可以看出,当测量值阶跃增大时,调节器的输出马上有一个较大的阶跃输出,随后输出逐渐减小,最终稳定在比例输出上面。调节器实现的是一个比例微分作用规律,其初始的阶跃输出包含比例和微分两部分,输出减小的过程就是微分消失的过程。微分消失得快慢取决于反馈回路中惯性环节的惯性大小,可由微分阀Rd进行调整。Rd开度越大,微分消失得越快,即微分时间Td越短,微分作用越弱;反之亦然。当微分消失后,调节器的输出大小与偏差成比例,比例作用的强弱由负反馈波纹管的位置进行调整,左移负反馈波纹管,l1增大,负反馈增强,比例作用减弱,比例带(PB)增大;反之,PB减小。
当调节器用于实际闭环控制系统时,外部扰动将引起测量值的变化,但一般不会是阶跃变化的。在调节器的控制作用下,被控量的测量值将朝着给定值方向变化。由于微分作用的存在,调节器具有超前控制的作用,但由于没有积分作用,比例微分调节器不能实现无差调节。因此只能适用于对静态精度要求不高的场合。
五、比例积分微分调节器
1.比例积分微分(PID)作用规律
把比例、积分和微分作用组合在一起,则构成比例积分微分作用规律,即PID作用规律。在PID作用规律中,仍以比例作用为主,吸收积分作用能消除静态偏差以及微分作用能实现超前控制的优点,功能最为完善。基于这种作用规律的调节器称为比例积分微分(PID)调节器。PID作用规律输出与输入之间关系为

式中,K为比例系数;Ti为积分时间;Td为微分时间。K、Ti和Td的大小与相应的作用强度之间的关系与PI和PD调节器相同。
若给PID调节器输入一个阶跃的偏差信号,并记录其输出响应,则可得到PID调节器的阶跃响应输出特性曲线,如图2-18所示。输出特性曲线表明,当对调节器施加一个阶跃的偏差输入信号后,它首先有一个较大的比例加微分的阶跃输出,然后微分输出逐渐消失。当微分输出消失到接近比例输出时,积分输出才不断地显现出来,使调节器输出不断增加。

图2-18 PID调节器输出特性
PID调节器综合了比例、积分和微分三种作用规律,因此兼有比例作用控制及时、积分作用消除静差和微分作用超前控制的能力。传统的PID调节器都有三个旋钮,分别用于整定比例带(PB)、积分时间Ti和微分时间Td三个参数,只要把PB、Ti和Td三个参数整定得合适,控制系统就能获得良好的动态过程品质。
在实际使用中,可根据具体的需要将PID调节器用作P、PI、PD和PID调节器。例如把积分时间整定为Ti→∞,把微分时间整定为Td=0,则相当于切除积分和微分作用,成为纯比例作用调节器;在纯比例作用的基础上,打开积分作用,则成为PI调节器;在纯比例作用的基础上,打开微分作用,则成为PD调节器;在纯比例作用的基础上,同时打开积分和微分作用,则成为PID调节器。若对被控量的稳态精度要求较高,则调节器中应加入积分作用;若控制系统中控制对象惯性较大,则调节器应加入微分作用;若控制对象惯性较大且要求较高的静态指标,则应加入积分和微分作用。对于PID调节器,往往把积分时间Ti整定得比微分时间Td长,它们之间的关系大致为Ti=4Td~5Td。加进微分作用后,原来整定的比例带PB和积分时间Ti都可以减小一点,这样既能减小最大动态偏差,保证系统的稳定性,又能加快系统的反应速度,使过渡过程时间ts进一步缩短。
在船舶机舱中,还应根据被控对象的特点,避免采用微分作用。如机舱中的锅炉水位等液位控制系统中,就不宜采用PD调节器或PID调节器。这是因为微分作用对干扰信号比较敏感,随船舶的摇摆,微分作用会使给水调节阀的开度忽而大开,忽而大关,造成水位的大起大落,不利于对水位的稳定控制。
2.气动PID调节器
将以上介绍的比例(P)、积分(I)和微分(D)作用的实现方法在同一个调节器里进行适当组合便可以实现气动比例积分微分(PID)调节器。其组合形式主要有两类,一是将三种反馈并行地叠加在一起形成调节器内部的综合反馈,二是在PI调节器前串联一个微分器来实现。下面以船上比较常用的NAKAKITA气动PID调节器实例加以说明。
NAKAKITA气动PID调节器在船舶机舱中常用于冷却水温度控制系统和燃油黏度控制系统,其三种作用规律通过内部综合反馈实现,其结构原理如图2-19所示。

图2-19 NAKAKITA气动PID调节器结构原理
NAKAKITA气动PID调节器中,比较环节是通过位移平衡原理实现的。测量值被送至弹簧管,测量压力的大小决定着弹簧管的张度大小,弹簧管张度的变化通过连接杆件一方面改变测量指针(黑色)的偏转角度,指示当前测量值的大小;另一方面推动比例杆OO′绕O点左右偏转,通过销钉和拨杆改变挡板和喷嘴之间的距离,引起调节器输出变化。而调节器的输出变化将通过波纹管组合引起OO′杆的上下浮动,影响挡板和喷嘴之间的距离,实现位移反馈。这点与前面介绍的气动调节器中基于杠杆的力矩平衡原理不同。
在初始平衡状态下,被控量测量值与给定值相等,黑色的测量指针与红色的给定指针重合。喷嘴和挡板之间的开度不变,调节器有一个稳定的输出。比例波纹管、积分波纹管、积分气室及微分气室压力都相等,并等于调节器的输出压力。
当系统受到扰动时,测量值会离开给定值,出现偏差。假设测量值降低,则弹簧管收缩,FG杆带动GH下移,HENM杆和HED杆将绕E轴顺时针转动。一方面MN杆左移使黑色测量指针朝测量值刻度减小的方向转动;另一方面D点左移使AC杆绕C点顺时针转动,传动杆BO′左移,挡板靠近喷嘴,其背压增大,经放大器使调节器输出压力增大。可见,这是一个反作用式调节器。调节器输出压力增大的同时,将使微分气室中的弹性波纹管立即伸长,挤压微分气室使其压力略有增大。这一增大的压力分为两路,一路直接送至比例波纹管,另一路经积分阀送至积分气室和积分波纹管。比例波纹管内部压力增大而略有伸长,阻止挡板继续靠近喷嘴,但这一负反馈很弱,挡板会大大靠近喷嘴,调节器的输出会大大增加,这就是调节器的微分输出。由于增大的调节器输出经微分阀不断向微分气室充气,负反馈逐渐增强,输出将逐渐减小,最后微分输出将消失在比例输出上。随着积分气室的不断充气,积分波纹管压力不断升高。这一附加的正反馈,又将使挡板靠近喷嘴,调节器输出增大,这就是调节器的积分输出过程。测量值增加的情况在原理上完全相同,只是动作过程相反。
在调节器上有三个调整盘,分别用来调整比例带(PB)、积分时间Ti和微分时间Td,改变积分阀和微分阀的开度可分别调整Ti和Td。开大积分阀,可缩短积分时间,加强积分作用;关小微分阀,可增加微分时间,加强微分作用。反之亦然。比例带调整盘是一个偏心机构,转动比例带调整盘可使喷嘴和挡板一起沿着比例杆上下移动。上移时,传动杆BO′左右移动相同的距离,即输入偏差相同的情况下,挡板开度变化要大,比例作用增强,比例带减小;反之,下移时,比例作用减弱,比例带将增大。
给定值由给定值调整旋钮确定,给定值调整旋钮的角度变化通过连接杆件一方面改变给定指针(红色)的偏转角度,指示当前给定值的大小;另一方面,通过连接杆件带动比例杆OO′绕O点左右偏转,引起调节器输出变化。例如,顺时针旋转给定值调整旋钮将使给定值增大,此时QS杆将绕Q轴逆时针转动,RC杆左移。由于测量值暂时未变,A和D点不动,故BO′杆左移,挡板靠近喷嘴,调节器输出压力增大,其工作过程与测量值降低的情况相同。
根据实际需要,该调节器还可以工作在正作用方式。此时,喷嘴挡板机构在比例杆OO′上的相对位置如图2-20所示。同反作用方式相比,区别在于喷嘴背压的变化将与测量值的变化方向相一致,而不是相反。例如,当测量值减小时,比例杆OO′绕O点逆时针偏转,通过销钉和拨杆的作用将使挡板和喷嘴之间的距离增大,喷嘴背压减小,调节器的输出也减小。调节器的工作方式应该根据控制任务的需要来决定,例如当应用于燃油黏度控制系统时,一般应采用反作用方式。

图2-20 正作用式切换
3.电动PID调节器
在船舶机舱中,有些控制系统是采用电动方式实现的。在电动控制系统中,调节器一般做成电路板的形式,其内部电路多数以运算放大器、电阻和电容等元器件组成。图2-21给出了采用运算放大器实现PID调节器作用规律的基本原理。
图2-21中,ui为调节器的输入信号,即测量值电压与设定值电压相比较获得的偏差电压。uo为调节器的输出电压,一般要经过进一步处理之后才能送至执行机构。运算放大器A1、A2和A3分别实现比例、积分和微分作用,A4起加法器的作用,并使调节器的输出uo与输入ui在符号上相一致。

图2-21 由运算放大器组成的PID调节器
由于

因此

上式表明,调节器的输出在整体上对输入具有比例、积分和微分的作用。调整R4、R2和R5的阻值可以分别调整比例、积分和微分的作用强度。
在实际中,调节器电路往往会因具体的控制系统而异。例如,积分环节和微分环节可能分别采用比例积分和比例微分环节代替,作用规律之间也可能是串联关系。此外,从电路设计的角度,往往还会加上一些抗干扰措施。
4.数字PID调节器
除了气动和常规电动控制系统之外,船舶机舱中越来越多的参数控制系统都采用微型计算机进行控制。在计算机控制系统中,调节器的作用规律是采用软件编程实现的,称为调节器作用规律的数字实现。
图2-22所示是一个由单片机组成的反馈控制系统结构框图,与气动或常规电动系统的最大区别是控制单元采用了单片机系统。被控对象输出的被控量由测量单元和信号处理电路转换成标准电压信号,再经过单片机系统的模/数(A/D)转换电路转换成数字量。设定值在单片机系统上通过键盘与显示装置进行数字设定。单片机将设定值与测量值比较获得偏差,调用控制算法程序计算出控制量,并由数/模(D/A)转换电路转换成模拟量输出,经放大后驱动执行机构动作,作用于被控对象,形成闭环控制。

图2-22 数字式反馈控制系统结构框图
计算机执行上述控制过程并不是像模拟仪表那样连续进行的,而是每隔一定的周期(称为采样周期,用T表示)进行一次测量采样和控制量输出计算,称为采样控制。由于计算机只能根据采样时刻的偏差值计算控制量,因此控制规律中的积分项和微分项不能直接地进行准确计算,只能用数值计算的方法逼近。在采样时刻t=kT(T为采样周期),调节器的PID控制规律可写成以下数值表示形式

式中,uk为k时刻的控制量输出;ek为k时刻的偏差;T为采样周期;K为比例系数;Ti为积分时间;Td为微分时间;u0为控制器的初始输出。只要采样周期T选择合适,这种数值逼近所实现的控制过程与连续控制十分接近,称为“准连续控制”。
上式表示的控制量输出uk实际上代表的是执行机构的位置(例如阀门的开度),所以称为位置式PID控制算法。
若将t=kT时刻的位置式控制量减去t=(k-1)T时刻的位置式控制量

则得到增量式PID控制算法

上式通常写成
Δuk=d0ek+d1ek-1+d2ek-2
其中

综上所述可以看出,位置式PID算法需要保留当前时刻及其之前所有时刻的偏差值,而增量式PID算法则只需保留当前时刻及其之前两个时刻的偏差值。因此,增量式算法有利于简化编程和避免累计误差,在实际中应用更为广泛,图2-23给出了增量式PID控制算法的子程序流程图。CPU除了执行键盘扫描、显示、数据处理和报警等程序模块之外,必须每隔一个固定的周期执行一次对测量值的采样程序和PID控制算法程序。

图2-23 增量式PID控制算法子程序流程图
与常规的气动或电动系统相比,采用计算机控制的反馈控制系统具有更高的控制精度和丰富的附加功能,例如通过键盘(实际上往往只是几个功能按钮)操作,可以在显示器(通常为数码显示器或者液晶显示器)上方便地查看和修改被控量的设定值,查看和修改比例带、积分时间、微分时间和采样周期等调节器参数以及查看被控量的测量值。此外,通过软件编程,还易于实现调节器的参数自整定以及模糊控制和神经网络控制等智能控制算法。
有些控制对象往往会有多个被控量和多个执行机构,称为多输入多输出系统。计算机为了对各个测量值进行分别采样和对各个控制量分别输出,要在系统中设置多路开关切换电路,如图2-24所示。此类控制系统在控制算法上往往比较复杂,若被控量之间存在耦合现象,则还需采取解耦措施。
六、反馈控制系统的参数调整
在反馈控制系统中,一旦各个组成环节安装完成,并且测量单元和执行机构调试完毕,唯一可调的只有调节器参数。为了获得理想的控制效果,只能调整调节器的参数值,即调节器的比例度、积分时间和微分时间。因此,在对调节器进行更换或维修之后,或由于长期运行导致系统性能降低时,都需要对调节器的参数进行调整,确定能获得满意控制效果的调节器参数值。通常也把这种确定调节器参数值的过程称为自动控制系统的整定或调节器参数的整定。

图2-24 多输入多输出反馈控制系统结构框图
但调节器参数的整定也不是万能的,它必须以测量单元和执行机构的正常工作为前提。如果测量单元的量程不对、执行机构动作失灵或执行不到位,那么仅仅通过整定调节器的参数值也难以达到满意的效果。
调节器的参数整定方法有理论计算和工程整定两种。理论计算涉及控制系统的模型辨识问题,难度较大,不适宜在现场进行。因此,在实际中通常采用工程整定的方法。
1.调节器参数对控制系统动态过程的影响
在反馈控制系统的控制方案已经确定,组成该控制系统的仪表已经安装并调校以后,为了能使控制系统符合动态过程品质指标的要求,唯一可改变的只有调节器整定的参数值,即调节器的比例带(PB)、积分时间Ti和微分时间Td。因此,在控制系统安装好准备投入工作的时候,或该系统已经运行了一段时间,各台仪表性能有所降低的时候,都需要对调节器参数进行整定,以便确定或恢复为获得满意的控制效果的调节器的最佳参数值。但是,调节器参数的整定只能在一定范围内起作用。如果控制方案不合理,各种仪表的选型和安装不当,单台仪表没有调校好等,单靠调整调节器的参数值是不能达到控制系统动态品质指标要求的。因此,不能片面强调调节器参数的整定。
前面曾分别讨论过调节器的比例带(PB)、积分时间Ti和微分时间Td对控制过程的影响,但在实际使用中,往往是两个或两个以上参数的联合作用。在这种情况下,调节器参数对控制系统的动态过程影响要复杂一些。目前,PI调节器应用比较广泛,下面着重分析PB和Ti联合运用时对控制过程的影响,并掌握参数整定的一般原则。
图2-25表示出在一个实际控制系统中,通过改变PB和Ti所得到的控制过程曲线图谱。图中曲线(5)表示PB和Ti已经整定合适时,其动态过程进行的情况,其他曲线表示PB和Ti这两个参数在最佳PB0和Ti0附近改变之后控制过程的变化情况。图中,从右到左PB逐渐增大,从上到下Ti值逐渐增大。比较这些曲线,可得出如下结论:
1)PB和Ti增大都意味着控制作用弱,控制过程更加稳定,但被控量的最大动态偏差增大。在这方面PB要比Ti的影响强烈得多,Ti偏大,在控制作用开始阶段,积分作用几乎不起作用,只有在比例作用基本结束时,才慢慢地显出消除静态偏差的积分作用,整个动态过程拖得很长,如图中曲线(7)、(8)、(9)所示。
2)PB和Ti小都意味着控制作用强。减小PB可显著减小最大动态偏差,而减小Ti对减小最大动态偏差不明显。

图2-25 PB和Ti改变时控制过程曲线图谱(控制对象T/T=0.22)
3)由于PB的影响比Ti大。因此要求对PB值整定得要准确一些,而Ti值的准确度可稍差一点。其中,Ti值宁可偏大一点,也不允许偏小,因为Ti值小对减小最大动态偏差的作用不大,且动态过程的稳性会明显降低。Ti偏大一点,可达到对动态稳定性的要求,只是消除静态偏差所花时间稍长一点。
2.PID调节器参数的工程整定方法
所谓整定方法就是确定调节器(PB)、Ti和Td的方法。它可以通过理论计算来确定,但误差太大。目前,应用最多的还是工程整定法,如经验法、衰减曲线法、临界比例带法和反应曲线法。
(1)经验法
经验法又称为现场试凑法,即先确定一个调节器的参数值PB和Ti,通过改变给定值对控制系统施加一个扰动,现场观察判断控制曲线形状。若曲线不够理想,可改变PB或Ti,再画控制过程曲线,经反复试凑直到控制系统符合动态过程品质要求为止,这时的PB和Ti就是最佳值。如果调节器是PID三作用式的,那么要在整定好PB和Ti的基础上加进微分作用。由于微分作用有抵制偏差变化的能力,所以确定一个Td值后,可把整定好的PB和Ti值减小一点再进行现场凑时,直到PB、Ti和Td取得最佳值为止。显然用经验法整定的参数试,直到PB、Ti和Td取得最佳值为止。显然用经验法整定的参数是准确的,但花时间较多。为缩短整定时间,应注意以下几点:
1)根据控制对象特性确定好初始的参数值PB、Ti和Td。可参照在实际运行中的同类控制系统的参数值,或参照表2-1所给的参数值,使确定的初始参数尽量接近整定的理想值。这样可大大减少现场试凑的次数。
2)在试凑过程中,若发现被控量变化缓慢,不能尽快达到稳定值,这是由于PB过大或Ti过长引起的,但两者是有区别的:PB过大,曲线漂浮较大,变化不规则,Ti过长,曲线带有振荡分量,接近给定值很缓慢。这样可根据曲线形状来改变PB或Ti。
表2-1 经验法经验参数表

3)PB过小,Ti过短,Td太长都会导致振荡衰减得慢,甚至不衰减,其区别是PB过小,振荡周期较短;Ti过短,振荡周期较长;Td太长,振荡周期最短。
4)如果在整定过程中出现等幅振荡,并且通过改变调节器参数而不能消除这一现象时,可能是阀门定位器调校不准,调节器或变送器的放大器调校不准,调节阀传动部分有间隙(或调节阀尺寸过大)或控制对象受到等幅波动的干扰等,都会使被控量出现等幅振荡。这时就不能只注意调节器参数的整定,而是要检查与调校其他仪表和环节。
(2)衰减曲线法
衰减曲线法是以4∶1衰减比作为整定要求的,先切除调节器的积分和微分作用,用试凑法整定纯比例控制作用的比例带(PB)(比同时试凑二个或三个参数要简单得多),使之符合4∶1衰减比的要求,记下此时的比例带PBS和振荡周期TS。如果加进积分和微分作用,可按表2-2给出的经验公式进行计算。若按这种方式整定的参数在运行过程中,其动态过程曲线还不够理想,再根据曲线形状,对整定的参数作适当的调整。对有些控制对象,控制过程进行较快,难以从记录曲线上找出衰减比。
这时,只要被控量波动两次就能达到稳定状态,可近似认为是4∶1的衰减过程,其波动一次时间即为TS。
表2-2 衰减曲线法经验公式表

(3)临界比例带法
用临界比例带法整定调节器参数时,先要切除积分和微分作用,让控制系统以较大的比例带,在纯比例控制作用下运行,然后逐渐减小PB,每减小一次都要认真观察过程曲线,直到达到等幅振荡时,记下此时的比例带PBK;(称为临界比例带)和波动周期TK,然后按表2-3给出的经验公式求出调节器的参数值:按该表算出参数值后,要把比例带放在比计算值稍大一点的值上,把Ti和Td放在计算值上,进行现场运行观察,如果比例带可以减小,再将PB放在计算值上。
表2-3 临界比例带法经验公式表

这种方法简单,应用比较广泛。但对PBK很小的控制系统不适用,对被控参数不允许振荡的系统也不适用。
(4)反应曲线法
前三种整定调节器参数的方法都是在预先不知道控制对象特性的情况下进行的。如果知道控制对象的特性参数,即时间常数T、时间迟延τ和放大系数K,则可按表2-4给出的经验公式计算出调节器的参数。利用这种方法整定的结果可达到衰减率φ=0.75的要求。
表2-4 反应曲线法经验公式表

表中公式只适用于有自平衡能力的控制对象。所谓控制对象的自平衡能力是指控制对象在受到扰动后不需要人为干预,经过足够长时间后能够自动地恢复到平衡状态的能力。