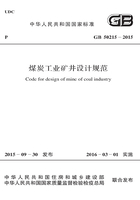
8.1 提升设备
8.1.1 主、副井提升设备的类型及套数应根据矿井设计生产能力、井深、水平个数、辅助提升要求、安全、环境条件及有利加快建设速度等因素,经技术经济比较后确定,并应符合下列规定:
1 矿井应各设主、副井提升设备;小型矿井在满足安全、提升能力要求的前提下,也可选择混合提升方式;对于井深超过700m或生产能力大于5.00Mt/a的矿井,作为人员主要提升的副立井,宜设两套提升设备,其中一套可为交通罐提升设备;
2 提升设备应按其所担负的最终水平提升量进行选择;
3 矿井主斜井、主平硐宜选用带式输送机提升。
增加了“环境条件”,包括气象、地震、工程地质、污染物等因素。
大型矿井(≥5Mt/a)深井(≥700m)主提升常为两套提升设施,以满足提升能力的要求;副提升能力紧张或有较特殊任务(交通罐、多水平、选用平衡锤系统等)时,也常有设置两套提升设备的情况。由于各矿井情况有差别,不能一概而论,故应进行技术经济方案比选后确定。
第3款:增加了“主平硐”,较大型矿井主平硐一般选择带式输送机。
8.1.2 条件适宜的立井宜采用多绳摩擦式提升机。采用多绳摩擦式提升机时,应符合下列规定:
1 选择塔式或落地式提升机,应根据所在地的气候、地震烈度、地基承载力等自然条件,结合总图布置、经济投资、安装、生产、维护、检修状况以及施工占用井口影响矿井建设工期等因素,经综合技术经济比较后确定;
2 当在井塔内设二套提升机时,宜采用同层布置;
3 落地式提升机宜靠近井筒布置;当一个井筒装备两套落地式提升系统时,主井宜采用对侧布置,副井宜采用同侧布置。
本条3款,均为多绳摩擦式提升的规定,而非单绳缠绕式与多绳摩擦式的选择规定。作此修订后,就明确了此条是作为多绳摩擦式提升的相关规定。
主井采用对侧布置,主要是为降低井架和机房高度。主井井口处无窄轨环线,一般情况可以两侧分别布置一座提升机房。
8.1.3 摩擦式提升机防滑安全校验应符合下列规定:
1 摩擦式提升机工作闸或保险闸所产生的制动力矩均不得小于提升最大静荷重旋转力矩的3倍;并应根据设计实用最大不平衡负载,按闸间隙2mm时的弹簧力配备制动器对数;
2 上提重载安全制动时全部机械的减速度不得大于5m/s2;下放重载安全制动时全部机械的减速度不得小于1.5m/s2;在各种载荷和各种提升状态下,安全制动系统所产生的制动减速度计算值不得超过滑动极限。钢丝绳与摩擦轮间摩擦系数的取值不得大于0.25,必须计入由钢丝绳自重所引起的最大不平衡质量差;
3 经安全制动防滑校验,当一级制动装置不能满足防滑要求时,必须采用二级制动装置或恒减速制动装置。
为防止提升系统安全制动时发生钢丝绳与主导轮之间的滑动,保证系统安全运行,特制订本条规定。
第1款:“制动力矩均不得小于提升最大静荷重旋转力矩的3倍”,与《煤矿用多绳摩擦式提升机 安全检验规范》AQ 1036—2007第6.10.2条、《煤矿提升系统工程设计规范》GB/T 51065—2014、《煤矿安全规程》的规定保持一致。
2mm为盘式制动器允许的最大闸间隙。见《煤矿用多绳摩擦式提升机 安全检验规范》AQ 1036—2007第6.10.9条。
第2款:与《煤矿用多绳摩擦式提升机 安全检验规范》AQ 1036—2007第6.11.2条、《煤矿提升系统工程设计规范》GB/T 51065—2014、《煤矿安全规程》的规定保持一致。
第3款:当一级制动装置满足不了安全制动的防滑要求时,采用二级制动或恒减速制动装置,来达到制动时的防滑安全。
删除原规范本条第4款内容,《煤矿提升系统工程设计规范》GB/T 51065—2014中已有规定。
原条文本条第5款内容,归纳并入第2款。
本条原则上维持了原规范的规定。
8.1.4 主井箕斗提升必须采用定重装载,箕斗容积设计必须与提升选型设计所确定的载重量相适应。
定容装载难以保证装载质量的准确性,误差大,对提升系统防滑、电动机容量、主轴转矩、钢丝绳安全系数均可能产生不利影响,严重时甚至导致事故。箕斗容积与设计载重量不相适应时,也会产生类似问题。故规定必须采用定重装载。
本条维持了原规范的规定。
8.1.5 提升设备的卷筒、摩擦轮、天轮、导向轮的直径与钢丝绳公称直径之比值,应符合下列规定:
1 落地式摩擦提升装置的摩擦轮及天轮、有导向轮的塔式摩擦提升装置的摩擦轮,井上不得小于90,井下不得小于80;围包角为180°无导向轮的塔式摩擦提升装置的摩擦轮,井上不得小于80,井下不得小于70;摩擦提升装置的导向轮,不得小于80;
2 井上缠绕式提升装置的卷筒和围包角大于或等于90°的天轮,不得小于80;围包角小于90°的天轮,不得小于60;
3 井下缠绕式提升绞车的卷筒、井下架空乘人装置的主导轮和尾导轮、围包角大于或等于90°的天轮,不得小于60;围包角小于90°的天轮,不得小于40;
4 矸石山提升装置的卷筒和导向轮,不得小于50;
5 倾斜井巷提升系统的游动天轮,围包角小于35°的不得小于20,围包角大于或等于35°的不得小于40;
6 提升设备使用密封式提升钢丝绳时,应将各相应的直径比值增加20%。
原规范中,此条为非强制性条款,现改为强制性条款,并明确了倾斜井巷提升绞车游动天轮的直径与钢丝绳公称直径之比值的规定。
钢丝绳在经过主导轮(含摩擦式提升系统的摩擦轮、缠绕式提升系统的卷筒)、天轮及导向轮、尾绳轮时,受到弯曲应力的作用产生摩擦、疲劳、挤压变形。曲率半径越小,应力越大,故需要制订规定,限制钢丝绳弯曲的曲率半径。
本条规定与《多绳摩擦式提升机》GB 10599—2010第3.3条、《矿井提升机和矿用提升绞车安全要求》GB 20181—2006第4.3.1条、《煤矿提升系统工程设计规范》GB/T 51065—2014、《煤矿在用摩擦式提升机系统安全检测检验规范》AQ 1014—2005第4.2.3条、《煤矿在用缠绕式提升机系统安全检测检验规范》AQ 1015—2005第4.2.5条、《煤矿用多绳摩擦式提升机 安全检验规范》AQ 1036—2007第5.2.9条等标准的规定保持一致。
8.1.6 提升钢丝绳选择应符合下列规定:
1 提升钢丝绳悬挂时的安全系数最低值必须符合表8.1.6的规定;
表8.1.6 提升钢丝绳安全系数最低值

注:H为钢丝绳悬挂高度(m),L为无极绳绞车驱动轮到尾轮的斜长(m)。
2 多绳摩擦式提升主绳应采用对称布置的左、右捻钢丝绳;
3 摩擦式提升的尾绳应至少装设2根,并宜减少与主绳的差重;
4 平衡尾绳宜采用扁钢丝绳,采用圆股或异形股钢丝绳时,应符合现行国家标准《重要用途钢丝绳》GB 8918的有关规定,并应采用带有旋转功能的尾绳悬挂装置与提升容器相连接。
钢丝绳的安全系数定义为实测的合格钢丝破断拉力的总和与钢丝绳所承受的最大静拉力之比。所谓“实测的合格钢丝破断拉力的总和”,明确为F=Kf,式中,K为现行国家标准《重要用途钢丝绳》GB 8918—2006附录A给出的换算系数,f为钢丝绳最小破断拉力。
本条第1款为强制性条款。提升钢丝绳必须有足够的安全系数,主要原因有:
(1)钢丝绳在受拉时,各股、各根钢丝受到的拉应力不可能完全一致,故钢丝绳的破断力要小于钢丝破断拉力的总和。
(2)系统加速时受到加速力的作用,此时钢丝绳承受的拉力大于最大静拉力,安全系数的定义中并未计入加速力。
(3)系统运行时钢丝绳受到冲击荷载、震动等额外应力。
(4)钢丝绳使用寿命内,受到锈蚀、磨损、弯曲与拉伸交变循环而产生应力疲劳等因素的作用。
(5)实际生产中,由于各种技术、管理、故障等原因,钢丝绳所承受的最大静拉力可能会大于设计值。
本条规定了提升钢丝绳新绳悬挂时的安全系数最低值。与《矿井提升机和矿用提升绞车安全要求》GB 20181—2006第4.3.12条、《煤矿提升系统工程设计规范》GB/T 51065—2014的规定保持一致。
现行国家标准《重要用途钢丝绳》GB 8918中钢丝绳单位长度参考重量是充分涂油后的,而平衡用扁钢丝绳单位长度参考重量是不涂油的。设计人员选择时应予注意(请参照现行国家标准《重要用途钢丝绳》GB 8918—2006中6.2.5.1款和现行国家标准《平衡用扁钢丝绳》GB/T 20119—2006表1注3)。
8.1.7 提升设备的运行速度和正常运行加、减速度及加速度变化率应符合下列规定:
1 立井罐笼升降人员时的最大加速度和减速度,不得超过0.75m/s2,升降人员时的最大速度,不得超过0.5 (H为提升高度),且最大不得超过12m/s;
2 立井升降物料时,多绳摩擦式提升的加、减速度不得超过1.2m/s2,单绳缠绕式提升的加、减速度不得超过1.0m/s2;升降物料时的最大速度,不得超过0.6 (H为提升高度)。斜井升降物料时的最大加速度和减速度不得超过0.5m/s2;斜井采用串车升降物料时的最大速度不得超过5m/s;斜井采用箕斗升降物料时的最大速度不得超过7m/s,当铺设固定道床并采用大于或等于38kg/m钢轨时,速度不得超过9m/s;
3 提升系统的加速度变化率不得超过0.5m/s3;
4 采用固定曲轨卸载方式时,滚轮进出曲轨时的速度不得大于1.5m/s;
5 斜井提升容器在甩车道上的运行速度,不得大于1.5m/s。
为保证安全生产,提升设备的最大运行速度和正常运行加、减速度以及加速度变化率必须有所限制。除安全因素外,还要考虑设备运行的经济性。
第1款:与《矿井提升机和矿用提升绞车安全要求》GB 20181—2006第4.4.1条、《煤矿提升系统工程设计规范》GB/T 51065—2014保持一致。
第2款:与《矿井提升机和矿用提升绞车安全要求》GB 20181—2006第4.4.2条和第4.4.3条、《煤矿提升系统工程设计规范》GB/T 51065—2014保持一致;
第3款:本款为新增款,规定了加速度变化率的上限值。
第4款、第5款:原则上维持了原规范的规定。
8.1.8 提升电动机及电控系统的选择应符合下列规定:
1 提升电动机选用交流异步电动机、同步电动机或直流电动机传动及其供电和控制系统时,应根据生产安全需要和提升工艺要求、电动机容量、电源容量、年提升量及投资收益等因素,通过技术经济比较后确定;
2 提升系统宜采用计算机控制,并宜具有联网通信功能;
3 提升机应选用电力电子变流器供电的交、直流传动系统;
4 功率大于1000kW时,宜采用低速直联传动系统;
5 井下提升电动机及其供配电电控设备的型式应选用矿用防爆型;
6 提升电动机功率选择储备系数宜按1.05~1.10选取;
7 提升机与电动机连接装置传动效率的选择,直联可取0.98,行星齿轮减速器可取0.92,平行轴减速器可取0.85~0.90,特定产品可按产品参数特征表中提供的数据选取;
8 计算提升动力学选取井筒阻力系数,立井箕斗提升应取1.15,罐笼提升应取1.20,斜井提升应取1.1;
9 主斜井、主平硐带式输送机的电控系统应满足重载起动和可设定加速度的软起动要求,对下运带式输送机并应满足软制动要求。需调速运行的大型带式输送机的传动装置宜采用交流变频传动系统;
10 主斜井、主平硐带式输送机和带式输送机运输线的配电、控制、保护、闭锁和信号装置的设置应符合现行国家标准《带式输送机工程设计规范》GB 50431和《通用用电设备配电设计规范》GB 50055的有关规定。
删去原条文第3款(斜井提升宜选用交流电动机传动系统),转子外接电阻器的传动系统属于淘汰产品。斜井提升可选变频传动、直流传动等节能高效、调速性能较好的电控系统。
服务年限内若需更换电动机,则在设计时应考虑更换的可能性。如设备基础(尺寸、受力、底盘等)、主导轮、主轴和减速器的扭矩、过卷过放高度、钢丝绳和衬垫、防滑、闸控系统等。
第7款中的特定产品举例:带有平行轴的行星齿轮减速器、进口产品、双电动机传动系统等。
较大倾角的下运带式输送机,正常运行时处于发电制动状态,应设置发电制动装置,将能量回馈到电网。
8.1.9 主井提升能力计算应符合下列规定:
1 主井提升应按每年330d、每天作业时间18h计算;
2 主井箕斗提升不均衡系数,有井底煤仓时可取1.10,无井底煤仓时可取1.20;
3 主井提升设备应留有10%~20%的富余能力;
4 斜井带式输送机提煤,当井底有煤仓时,不均衡系数宜取1.10~1.15;当井底无煤仓时,斜井带式输送机的输送能力应与大巷带式输送机的输送能力相适应。
对于带式输送机运输煤炭(或矸石等物料)的不均衡系数,见本条第4款,本条第2款仅适用于箕斗提升。在单水平提升时,主提升富余能力不宜过大。国家严格控制超能力生产,也规定了严格的扩建审批程序,过大的能力富余将造成浪费。
8.1.10 副井提升能力计算应按四六工作制进行,并应符合下列规定:
1 最大班工人下井时间,立井不应超过30min,斜井不应超过45min;
2 最大班作业时间应按4.5h计算;
3 人员、矸石、支护材料等作业时间宜按下列规定计算:
1)升降工人时的重合率,宜按工人下井时间的1.6倍~1.8倍选取;升降其他人员时间,宜按升降工人时间的20%计算;
2)提升矸石宜按日出矸量的35%计算;
3)下放支护材料宜按日需要量的35%计算;
4)其他作业宜按5次~10次选取;
4 提升设备应能满足运送井下设备最重部件的需要,液压支架宜选择整体运输方式。
副井提升工作制应取四六制,不再考虑三八制,以对应井下工作制度。
普采和综采升降工人时间不再加以区分,均取1.6倍~1.8倍的理由是:四六制后,井下工人交接班时间较长,普采再按1.5倍将难以满足要求。
最大班提升矸石、下放支护材料按每日的35%计量,与《煤矿提升系统工程设计规范》GB/T 51065—2014保持一致,符合四六工作制的特点。
8.1.11 提升容器在井口、井底同时作业时的休止时间应符合下列规定:
1 标称容量6t及以下箕斗,宜为8s;8t~9t箕斗,宜为10s;12t~30t箕斗,可按每吨1s计算;30t以上的箕斗,宜按有关设备部件环节联动时间计算确定,在缺乏计算数值或实测数据时,每增加1t可按0.5s~0.8s计算;
2 普通罐笼进出矿车休止时间应符合表8.1.11的规定;
表8.1.11 普通罐笼进出矿车休止时间(s)

3 普通罐笼单层进出材料车或平板车的休止时间宜按40s计算;双层罐笼沉罐时休止时间宜按88s计算。无轨胶轮车运输,罐笼单层进出车的休止时间应按罐笼承接装置、安全门、无轨胶轮车罐内定位等环节动作时间计算确定;双层罐笼沉罐时,休止时间应按两次单层进出车的休止时间与沉罐时间之和计算确定;
4 单层罐笼每次升降5人及以下时的休止时间宜按20s计算,超过5人,每增加1人应增加1s;双层罐笼升降人员,当两层罐笼同时进出人员时,休止时间应比单层罐笼增加2s信号联络时间;当人员由一个水平进出罐笼时,休止时间应比单层罐笼增加1倍,并应增加6s换置时间;
5 斜井串车提升的休止时间,平车场宜取25s,甩车场宜取20s,井上下甩车时间应按实际运行状况计算。
第3款:增加了采用罐笼升降无轨胶轮车的休止时间的规定内容。
8.1.12 混合提升能力计算应符合下列规定:
1 最大班工人下井时间,立井不宜超过30min,斜井不宜超过45min;
2 最大班作业时间应按5.5h计算;
3 每班提煤、提矸应计入1.25不均衡系数;
4 提升设备应能满足运送井下设备最重部件的需要。
8.1.13 专用提升矸石的设备能力应按每年330d、每天作业时间18h计算,并应取1.2不均衡系数。
8.1.14 采区上、下山轨道提升能力计算应符合下列规定:
1 当只提煤时,提升作业时间每班应按4.5h计算;
2 辅助提升作业时间,每班应按4.5h计算;
3 混合提升作业时间,每班应按5.5h计算;
4 提煤或提矸的不均衡系数应取1.25;
5 单钩提升时,上提下放时间可按重合计算;
6 提升设备应满足运送采区内采掘设备最重部件的需要。
8.1.15 提升机房起重设备的选择应符合下列规定:
1 滚筒直径为2.5m及以上的单绳缠绕式提升机或落地式多绳摩擦式提升机的机房,应设起重机;起重机设备应能满足提升机设备的起吊、安装和检修要求;
2 塔式多绳摩擦式提升机房采用内吊装方式运送设备部件时,宜设置电动超卷扬起重机。