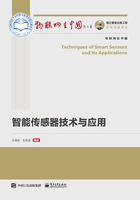
2.3.4 半导体中的掺杂
半导体材料的独特性质之一是它们的导电性和导电类型(N型或P型)都能被控制,结(Junction)是富含电子的区域(N型区)与富含空穴的区域(P型区)的分界处,结的具体位置是电子浓度和空穴浓度相同的地方。在半导体晶圆表面形成结的方法通常是热扩散(Diffusion)或离子注入(Ion Implantation)。通过热扩散,掺杂材料被引入晶圆顶层暴露的表面,并散布在晶圆内;在离子注入中,掺杂材料被射入晶圆表面,其中大部分掺杂原子静止于表面层下。
扩散工艺:扩散是一种材料通过另一种材料的运动,是自然的化学过程。扩散的发生需要两个条件,一是一种材料的浓度必须高于另一种材料的浓度;二是系统内部必须有足够的能量使高浓度材料进入或通过其他材料。在半导体晶圆中应用固态热扩散工艺(Solid-State Thermal Diffusion)形成结需要两步,第一步为淀积(Deposition),第二步为推进氧化(Drive-in-Oxidation),两步都在卧式或立式炉管中进行。
由于一般施主或受主杂质原子的半径都比较大,它们要直接进入半导体晶格的间隙中较为困难,只有当晶圆中出现晶格空位时,杂质原子才有可能占据这些空位,并进入晶圆。为了使晶圆中产生大量晶格空位,必须对其进行加热,令原子的热运动加剧,使某些原子获得足够高的能量而离开并留下空位(同时产生等量的间隙原子,将空位和间隙原子统称为热缺陷)。因此,原子的扩散系数随温度的升高而增加。对于硅来说,在其中形成大量空位所需要的温度为1000℃左右,该温度为热扩散温度。MEMS生产中的扩散指所需要的杂质在一定条件下对硅(或其他衬底)的掺杂,如在硅中掺磷、硼等。从广义上讲,氧化与退火也属于扩散,前者指氧气在二氧化硅中的扩散,后者指杂质在硅(或其他衬底)中的扩散,其目的是改变原材料的电学特性或化学特性。
离子注入工艺:离子注入消除了扩散的限制,也提供了额外优势。在离子注入过程中没有侧向扩散,在室温下进行,杂质原子被置于晶圆下表面,使大范围的掺杂成为可能,可以加强对掺杂的位置和数量的控制。
离子注入是物理过程,其采用与扩散相同的杂质,在扩散中,杂质为液态、气态或固态材料;在离子注入中,只采用气态或固态材料。为了方便使用和控制,离子注入倾向于使用气态材料,包括砷烷(AsH3)、磷烷(PH3)和三氟硼烷(BF3)。离子注入机如图2-11所示。离子源发射离子后,根据离子的电荷—质量比,将磁场调节到适当值,使离子偏转,形成准直射束。这些离子在加速管中被电场加速至具有所需能量,利用X扫描板和Y扫描板对其进行扫描后,撞击放置在法拉第杯中的晶圆。

图2-11 离子注入机
离子注入的几个关键概念如下。
(1)离子种类:指注入晶圆的离子类别,如1B+、11B++、14N+、31P+、31P++、121Sb+、115In+、75As+、28Si+等,这些离子不是原来就以这种形式存在并直接注入晶圆的,而是将不同的化学物质(如BF3、N2、PH3、Sb2O3、InF3、AsH3、SiF4等)电离后通过质量分析磁场及能量分析磁场筛选得到的。
(2)能量:指离子注入晶圆时的能量,该能量通过萃取电场将离子加速获得。常用单位是keV和MeV。对于一种确定的离子来说,能量决定了杂质注入的位置,能量越髙,注入越深。但是对于不同的离子来说,原子质量不同、注入能量相同时会得到不同的杂质分布。有时为了获得更高的能量,会采用双价或更高价态的离子;但在能量较低的情况下,只能用单价离子或离子团,以减小注入深度。
(3)注入剂量:离子注入机在整个注入过程中会一直测算注入剂量,一旦注入剂量达到预设值,离子注入机就会自动终止注入。需要注意,注入剂量和最终晶圆中离子的浓度不同,注入计量是晶圆中离子浓度沿晶圆深度的无限积分。
(4)注入角度:指经过加速的离子注入晶圆的角度,常用的有倾斜角和扭转角。倾斜角是电流束与晶圆表面法线的夹角,扭转角是电流束在晶圆表面的投影与晶圆表面参考线的夹角。
(5)电流束:指在单位时间和单位面积内通过的离子数量,该值直接决定了离子注入的时间。当注入剂量恒定时,电流束越大,离子注入越快,但对机台状态和性能的要求越高。
MEMS中涉及的离子注入工艺是在高真空的复杂系统中,将带电的且具有能量的粒子注入衬底硅的过程,注入能量为1keV~1MeV,注入深度平均可达10nm~10μm,粒子在硅片中的浓度即为杂质离子浓度,符合高斯分布,则有

式中:φ为注入剂量,x为注入深度,Rp为平均投影射程,∆Rp为投影射程的平均标准偏差。离子注入浓度分布的最大浓度Nmax为

为了使施主或受主杂质原子进入晶圆,需要将杂质原子电离成离子,并通过强电场加速使其获得较大动能,然后直接轰击晶圆并注入。采用离子注入工艺进行掺杂时,必然会产生许多晶格缺陷,也会有一些原子处在间隙中。因此,还需要对半导体进行退火处理,以消除晶格缺陷并“激活”杂质。
离子注入工艺可以精确控制杂质的剂量、深度和均匀程度,由于采用低温工艺(可防止杂质再扩散),还可以实现自对准(减弱电容效应)。
与传统的扩散工艺相比,离子注入工艺有以下特点。
(1)杂质浓度分布不同,离子注入工艺的杂质浓度峰值出现在晶圆内部,扩散工艺的杂质浓度峰值出现在晶圆表面。
(2)离子注入工艺在常温甚至低温下进行,时间较短,而扩散工艺需要进行较长时间的高温处理。
(3)离子注入工艺能更灵活地选择注入元素。
(4)由于杂质会被热扩散影响,离子注入工艺形成的波形比扩散工艺的波形好。
(5)离子注入工艺通常只采用光刻胶作为掩膜,而扩散工艺需要淀积一定厚度的薄膜作为掩膜。
(6)离子注入工艺在集成电路制造和MEMS工艺中已经基本取代了扩散工艺,成为最主要的掺杂工艺。