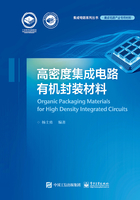
2.4.1 单/双面封装基板
图2.24是代表性单面封装基板的截面结构图[29]。单面封装基板在封装基板的一面放置电子元件,在另一面对元件进行焊接,适用于电子元件较少的电子电路[30]。随着移动电子产品性能的不断更新和电子元件的不断小型化,封装基板的面积尺寸不断变小,制造成本不断降低。目前,在封装基板厚度减薄方面取得了很大进展,总厚度为110μm的封装基板可使用两层厚度为50μm的电介质材料进行生产。采用减法技术的细线线宽和空间间距已被提高到40μm;采用改性半加性技术,可以使电子线路的线宽和间距达到25μm。通常,单面封装基板必须具有足够的厚度,以减少由于铜布线平面的不平衡所引起的基板弯曲。

图2.24 单面封装基板的截面示意图
单面封装基板的制造方法为:首先,在单面覆铜板(1L-CCL)上,通过机械钻孔或激光烧蚀方法形成用于焊球焊盘的开口;然后,按照标准光刻制图方法在铜箔上涂敷光刻胶,经曝光、显影后形成设计的电子电路;最后,采用Ni/Au选择性地进行电镀形成球形焊盘。如果需要,则可以在电子线路图案上涂敷阻焊剂(或采用选择性的Au电镀掩模)。通过引线键合对芯片进行组装,焊球黏结均可采用通常的组装工艺过程进行。单面封装基板几乎不会发生翘曲,不需要进行任何特殊处理。
图2.25是一个典型aS3单面封装基板搭载倒装芯片后的横截面结构。该基板通过环氧塑封形成一个可靠的IC封装。

图2.25 搭载倒装芯片的单面封装基板的横截面结构
如果裸露的布线被完全覆盖且没有空隙,就可以使用裸芯片附着膜或环氧树脂将裸芯片直接黏附在裸露的封装基板上。单面封装基板的球垫开口是直径非常大的盲孔(可达300μm)。对于如此大的孔,采用激光钻孔将是一个相当缓慢和耗时的过程,成本很高。由于封装基板的制造总成本取决于每个基板表面的焊盘大小和数量,激光加工只有在大球道和小垫块的情况下才有成本效益,而采用机械钻孔+电镀通孔的方法则是适宜的。在机械钻孔过程中,在焊盘位置镀铜柱,在半固化片上相同的位置进行机械钻孔;将带预钻孔的半固化片的开孔位置与铜柱位置对准,在层压过程中使半固化片固化,铜柱可在电镀后或层压后刨平,去除铜柱顶部的所有残留树脂碎屑;对铜箔面制作单面电路图案,形成单面封装基板。另一种工艺是基于双图案镀覆工艺,对金属化基板进行第一图案镀覆过程,以形成布线图案,在第二图案镀覆过程中镀覆Cu柱,将预钻孔的半固化片层压在图案和铜柱上后,按照标准的工艺流程进行精加工,得到单面封装基板。