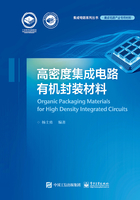
2.2.3 附树脂铜箔(RCC)
在经表面粗化、耐热、防氧化处理的电解铜箔上涂敷一层有机树脂胶液,经加热干燥除去大部分溶剂、低分子挥发物后,使A阶段树脂转化成B阶段树脂,形成黏附着B阶段树脂膜的铜箔,即附树脂铜箔。RCC所用的铜箔为电解铜箔,厚度为12~35μm;是具有高温延伸性(THE)的低轮廓铜箔(Low Profile Copper Foil,LP铜箔);近年来,还出现了极薄铜箔(3μm或5μm)的RCC产品,主要用于制作超精细电路。RCC的附着树脂层厚度(固化前)为50~75μm,有些RCC的附着树脂层包含两层具有不同固化程度的树脂层。这些树脂具有与半固化片相似的性能指标,包括流动度、挥发物、凝胶时间、熔体黏度等。
RCC用黏附树脂以环氧树脂为主,其他包括BT树脂、改性PPE树脂等。目前,市场上RCC产品大约有30多个品种。RCC具有下述特性:①RCC在制作BUM基板的绝缘层时,可采用多层PCB板的真空压制设备及相似的压制工艺条件;②可采用激光进行微细通孔加工,由于RCC不像半固化片一样含有玻璃纤维布,因此可以采用激光刻蚀加工形成微细通孔;③以RCC上附着的绝缘树脂层作为载体,易于实现绝缘层的超薄化及高平坦化;④绝缘树脂选择余地大,有利于提高耐热性、耐湿性,降低介电常数及损耗,降低吸水率,提高图形导线的剥离强度;⑤与感光性绝缘树脂比较,RCC制作的BUM基板工艺简单,与导电层黏结强度高,有利于降低制造成本。
由于RCC具有上述突出的特点,因此近年来,在BUM基板制造中获得了广泛应用。表2.19比较了代表性RCC材料的主要性能。目前,大部分RCC采用与FR-4相似的环氧树脂黏附在铜箔表面上形成的EP/Cu复合材料,主要原因在于BUM基板制作成型工艺应尽量与FR-4 PCB接近,便于生产厂家掌握加工工艺,在已有设备上易实现BUM基板的低制造成本。
表2.19 代表性RCC材料的主要性能

续表

RCC树脂体系的B阶段树脂应具有适宜的熔融流动性,固化成型后应具有高耐热性、高电绝缘性、耐化学腐蚀性、阻燃性等特性。RCC树脂层包含两个不同固化程度的树脂层:内层树脂(靠近铜箔)具有较高的固化程度,已经固化成C阶段树脂,在加热、加压固化过程中不再熔融流动,以确保RCC绝缘层达到一定的厚度,具有优良的介电性能;外层树脂仍然为B阶段树脂,具有适当的熔融流动性,熔体黏度控制在100~1000Pa·s的范围内,在加热、加压固化过程中,熔体树脂对凸凹起伏的内层电路图形可以完全填埋。进一步提高RCC树脂层的厚度尺寸精度,提高成型工艺性,提高固化树脂绝缘性能是RCC材料需要解决的技术难题。
BUM制作工艺要求厚度为50~80μm的RCC所形成的绝缘树脂层的厚度偏差控制在±2μm,以保证整体BUM基板z方向的尺寸精度,有利于制作多层积层电路,提高激光蚀孔的质量和通孔的可靠性,控制多层电路板的特性阻抗精度。由于RCC绝缘树脂层没有玻璃纤维或氧化硅等填料,因此对提高树脂绝缘层的厚度精度带来工艺技术上的挑战。控制B阶段树脂层的涂层厚度精度、各部位厚度偏差、树脂各层的固化程度等可以有效提高树脂绝缘层的厚度尺寸精度。
RCC的成型加工过程也影响着固化后树脂层的厚度偏差。控制树脂熔体黏度及熔体流动性是改善RCC压制成型加工性的关键因素。与半固化片相似,树脂熔体流动性主要由B阶段树脂的固化程度决定。当熔体流动性偏小时,树脂不能充分填充内层线路,造成层间孔隙和层间黏结性差;当熔体流动性偏大时,树脂熔体流失量大,可能造成固化树脂层厚度减少,偏差变大,绝缘性能下降。
随着电子封装技术的快速发展,对RCC材料提出了高耐热性、低热膨胀性、高韧性等要求,尤其是高韧性,对BUM基板用RCC制造技术向更高水平发展提出新的挑战。由于RCC的绝缘树脂为热固性树脂,其中不含任何增强纤维或填料,固化后的树脂耐热性差、模量低、脆性大、热膨胀系数高,导致IC封装在金属丝焊接的高温冲击下出现绝缘树脂层坍塌或崩裂。针对这一问题,日本公司在2000年前后开发出了高Tg、高模量型RCC。所制备的BUM基板的绝缘树脂层膜具有低热膨胀系数((20~30)×10-6/℃)、高模量(4~6GPa)。该RCC的树脂中添加了具有高纯度、高界面黏结性和高分散性的填料,形成了新的界面相控制体系,使树脂与填料的界面实现了高分散与高黏结,有效防止了填料产生二次聚集现象。表2.20是高Tg、高刚度RCC的主要性能。
表2.20 高Tg、高刚度RCC的主要性能

续表
