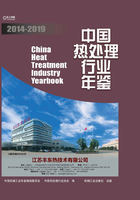
中国热处理行业走进新时代
热处理是装备制造的基础工艺之一,是提升机械零件使用性能水平和保证机械零件质量的核心技术。热处理的技术水平和生产能力为我国航天航空装备、国防军工装备、石油化工装备、水火风核电力装备、高铁地铁轨道机车、海洋工程装备、港口机械、冶金机械、矿山机械、工程机械、轻工机械、园林机械、机床、船舶、汽车、农机、电子、工模具、轴承、紧固件、家用电器等产品制造行业的发展提供了重要支撑。
进入21世纪以来,中国热处理行业协会坚持以建设质量控制严格、科技含量较高、掌握核心关键技术的专精特新企业为基点,瞄准国际同行业先进水平,以绿色制造和服务型制造为方向,以智能制造为目标,以数字化和网络化为重要抓手,着力推广先进热处理技术与装备,促进热处理企业技术改造和质量品牌建设,热处理工艺技术与装备不断创新发展,行业面貌日新月异。当今,我国热处理行业进入了一个崭新的时代。
一、热处理行业实力增强
预计到2020年年底,我国各类热处理加工企业和车间近10000家(其中具有独立法人资格的热处理加工企业约7000家),热处理设备、工艺材料和工装配件制造企业约1000家。20年来,热处理企业数量变化不大,但内涵变化显著。按照国家有关部门确定的年产值超过2000万元为规模以上企业的标准,2000年,我国热处理行业除国有的几十家军工企业和重型机械厂内部的热处理分厂外,几无规模以上企业,而预计到“十三五”末(2020年),我国热处理行业规模以上企业数量将增加到约1500家。2019年,热处理行业生产总值约1200亿元,较2000年(220亿元)增加约1000亿元,翻两番还多;热处理加工企业劳动生产率约40万元/人,热处理装备制造企业劳动生产率约80万元/人,较2000年(6万元/人和8万元/人)分别提高566%和900%。有10家热处理装备企业和工艺材料企业成为上市公司。
2000年,全国热处理企业的生产设备主要为手工操作和继电器开关控制的电加热设备,并且基本上是小型设备。当时以75kW/标准台统计约12万台,总装机容量约为900万kW,年热处理加工能力约为1500万t。现在,随着热处理生产规模和技术装备的发展,现代化的真空炉、多用炉、连续式自动生产线替代了小型箱式炉、井式炉、盐浴炉等落后设备,热处理工艺装备数控化率已达到80%。以150kW/标准台统计,全行业热处理生产设备约为20万台(套),其中电加热设备约占80%,燃气加热设备约占20%,电加热设备装机容量约为2500万kW,每年热处理加工量约为5000万t。我国热处理行业20年发展对比见表1。
表1 我国热处理行业20年发展对比

(续)

二、热处理生产设备升级换代
2000年以前,由于热处理行业经济实力和技术水平所限,只有少数航空航天装备制造企业和重点齿轮制造企业从国外引进密封箱式渗碳炉生产线和真空热处理设备用于热处理加工生产,我国热处理密封箱式渗碳炉生产线和真空加热淬火炉尚处于研制阶段,少数几家合资或外资企业制造的同类热处理装备尚未大量进入市场。彼时的专业热处理加工企业仍以传统的箱式电阻炉、井式电阻炉、台车式电阻炉和盐浴炉为主,甚至一些刚刚起步的民营热处理厂大量使用国有企业淘汰的老旧热处理设备。
现在,中温盐浴炉已被淘汰,传统的“老三炉”已基本被“新三炉”(真空热处理设备、可控气氛热处理设备、感应加热设备)替代,热处理企业的生产设备旧貌变新颜。
“十五”和“十一五”期间,随着外资热处理装备制造企业带入的先进技术和产品增加,我国热处理装备制造企业自主开发和制造能力明显提高,热处理加工企业的经济实力逐年增强,密封箱式渗碳炉生产线、连续式热处理生产线、真空加热淬火炉等得到推广。在此期间,中国热处理行业协会积极推动热处理企业进行规范化管理和节能减排技术改造。“十二五”期间,密封箱式渗碳炉生产线成为普及炉型,真空加热油淬火炉得到推广,真空加热高压气淬炉和真空渗碳炉开发成功。“十三五”期间,真空加热油淬火炉开始普及,真空加热高压气淬火炉和真空渗碳炉推广应用,真空渗氮炉开发成功并在热处理生产企业应用。“十四五”期间可望普及真空淬火炉和真空渗碳炉,推广真空渗氮炉。
现在我国各类真空热处理设备约有14000台,已实现真空退火、真空油淬、真空高压气淬、真空水淬、真空渗碳、真空渗氮、真空渗铝、真空磁场热处理、真空等离子渗氮以及真空溶剂清洗等工艺技术应用,并能够形成不同热处理工艺组合的真空热处理生产线及智能控制系统。
在可控气氛热处理方面,我国热处理行业现有多用渗碳炉、连续渗碳炉、大型井式可控气氛渗碳炉、可控氮势气体渗氮炉等各类可控气氛热处理设备30000多台(套)。渗碳热处理生产线可实现以下功能:工业计算机对炉温、碳势和动作程序的监控及数据的自动采集;对渗碳工艺过程(炉内温度和碳势)进行实时显示及控制,实现渗碳工艺仿真与优化,预测零件渗碳质量;实现系统故障自动诊断、显示及报警;进行渗碳生产工艺过程自动记录及储存,建立可追溯的热处理质量管理系统。
感应热处理设备朝柔性化、自动化、智能化方向发展,具有零件识别、能量控制、工艺参数显示及故障诊断、显示报警等功能的感应淬火机床已在生产中得到广泛应用。数控模拟感应淬火技术和IGBT控制电源水平式龙门淬火机床成熟应用于高铁机车零件和风电配套高精齿轮生产中。ϕ100mm以内棒材使用的节能环保的感应加热调制全自动生产线,可配备硬度计等力学性能检测仪器,使用缺陷无损检测等检测手段以及后期校直装置,能显著提高生产效率,有力支撑了感应热处理的数字化和智能化进程。
三、热处理工艺材料和辅助设备创新发展填补空白
20年前,专用热处理淬火油的概念刚刚在行业中传播,大多数热处理企业使用的淬火油多是普通机油或废弃的变压器油。自20世纪末期美国HOUGHTON公司和德国PETROFER公司在我国设立办事处宣传和销售专用淬火冷却介质以来,我国的专用淬火冷却介质快速发展。现在,专用热处理淬火油已成系列,普通淬火油、快速淬火油、光亮淬火油及真空淬火油等细分产品可满足不同的零件和技术要求。近年来,满足安全生产和环保排放要求的水基PAG淬火冷却介质迅速发展,并且列入国家发展改革委发布的《低碳产品认证目录》,在热处理行业快速推广,现在已有50%以上的零件使用PAG水溶性淬火冷却介质进行淬火。现在,我国热处理行业每年消耗各种类型专用热处理淬火油逾10多万t,PAG淬火冷却介质近10000t。专用淬火冷却介质的应用,大大提高了零件的淬火质量,减小了零件的淬火畸变。
在热处理辅助设备中普及最广的是淬火化冷却介质换热设备。现在已有50%以上的热处理企业采用了空气冷却系统,逾10000台空冷换热器替换了传统的水冷却塔,每年节约用水约1500万m3。近年来,溶剂型真空清洗设备已开始在热处理企业推广使用,解决了螺纹、浅层不通孔等部位的清洗难题,清洗后的工件可以实现真空干燥,省去常规清洗中的烘干等步骤,节能节水,提高了清洗效果和生产效率。
热处理油烟收集和油烟净化技术及装备的发展是热处理行业近几年的亮点。随着行业环保意识的提高,热处理油烟作为热处理的主要大气污染物已成为热处理企业废气治理的重点。“十三五”末期,已有50%以上的热处理企业安装了不同类型的热处理油烟收集处理设施,做到热处理废气达标排放,保护大气环境。
四、突破重大关键零件热处理技术
十几年来,热处理为国产重大装备的关键零件制造做出了突出贡献,突破了G18CrMo2-6核电气缸体热处理和Cr9-Cr12型钢超超临界转子的热处理工艺瓶颈,实现了100万kW发电机超超临界转子热处理、6m轧机支撑辊热处理、模数大于62mm的三峡大型升船机齿条感应淬火、AP1000核岛主设备大锻件热处理、高温气冷堆核岛主设备大锻件热处理和60MW以上火力发电设备耐高温高压厚壁无缝钢管热处理等,达到了超长工件整体热处理变形量小、各部位微观组织与硬度均匀一致。5MW风电齿轮和160km/h、200km/h、250km/h等多个速度等级动车组齿轮热处理形成批量生产能力。在航空航天领域,钛合金紧固件真空/气氛保护水淬热处理生产线符合航空航天标准要求。航天飞船、长征系列运载火箭、北斗导航卫星、空间实验室等许多高端领域采用新型材料(如铝锂合金、镁合金、钛合金等有色金属,以及高温合金、精密合金、贵金属等)关键结构零件(如柔性太阳翼伸展机构、阿尔法对日定向装置、转位机构、对接伺服机构、阀门等)都依托于热处理工艺的创新。热处理为实现我国制造强国伟大目标提供了重要的支撑。
五、节能减排成果贡献突出
热处理是机械制造领域的重点用能行业。我国热处理每年用掉电能总量为200亿kW·h,耗能用掉天然气和液化气约为4亿m3(标准状态),淬火油超10万t,加上其他工艺材料消耗,总计每年约1000万t标准煤,排放二氧化碳约3000万t,排放碳、氮氧化合物1000多万t及少量挥发性有机物(VOCs)等。坚持绿色制造、节能减排是热处理行业多年来的重点工作。2000年,我国热处理加工能力为1500万t,用电约100亿kW·h,热处理企业平均单位能耗约为700kW·h/t(万元产值能耗约1.8t标准煤),高耗能热处理企业平均单位能耗超过1000kW·h/t。到“十三五”末期(2020年),规模以上的骨干企业热处理平均单位能耗将降到400kW·h/t以下(万元产值能耗约1.1t标准煤),部分企业热处理单位能耗已降至340kW·h/t。按平均每吨零件热处理节约300kW·h成果计算,现在全国热处理行业每年节电达150亿kW·h,约合60亿t标准煤;仅节电方面每年减少CO2排放约1180万t、减少SO2排放约35万t。
六、热处理装备制造踏上新台阶
“十二五”期间,我国热处理装备制造体系基本形成。到“十三五”末,我国热处理装备和工艺材料制造已达到或接近国际先进水平,现已能够制造热处理加工所需的各类工艺装备并实现数字化控制,能够根据用户的需求进行新产品开发和工程化配套。现在我国每年可制造各类热处理设备和热处理辅助设备近10000台(套),设备类型包括:真空热处理设备(真空加热油淬炉、真空加热高压气淬炉、低压渗碳高压气淬炉、真空回火炉、真空退火炉及真空烧结炉);真空等离子渗氮炉;可控气氛热处理设备(全密封箱式渗碳炉生产线、1000℃以上高温密封多用炉、数控大型井式渗碳炉、网带渗碳炉生产线、箱式渗氮炉生产线、井式氮势可控渗氮炉、罩式渗氮炉、箱式加热炉、井式加热炉)、连续式热处理设备(网带炉、辊棒炉、链板炉及推杆炉等);IGBT电源和大功率固态感应加热设备;激光热处理设备;淬火机床;数控淬火冷却设备;专用热处理清洗设备;淬火油烟无害化处理及排放设备;淬火冷却介质冷却换热设备;各类硬度计及金相显微镜;各类传感器及精密测控仪表等。以上设备基本上完善了产品标准(包括行业标准和企业标准),部分设备已列入国家重点产品目录(如工业和信息化部重点节能产品目录)。目前,我国热处理装备制造行业的年产值近150亿元,很多产品出口到美国、欧盟、俄罗斯、印度、土耳其、埃及、巴基斯坦、新加坡、泰国、马来西亚、印度尼西亚、缅甸、越南及朝鲜等国家和地区。
七、热处理行业公共服务平台体系建成并发挥作用
针对我国热处理企业大多属于小微型企业、技术力量分散、技术创新能力弱及各类服务需求大的状况,自2010年起,中国热处理行业协会组织骨干会员单位建设热处理行业公共服务平台,为热处理企业提供信息、技术、培训等公共服务。热处理行业公共服务平台于2012年通过机械工业中小企业公共服务示范平台和国家中小企业公共服务示范平台认定,2019年再次通过中国机械工业联合会和工业和信息化部认定。目前,在全国各地已建有各类热处理公共服务示范平台11个,包括热处理装备检测、热处理淬火冷却介质研发与检测、真空热处理节能减排技术与装备、燃气加热热处理装备及技术、热处理渗氮技术与装备、水溶性淬火冷却介质研究与推广、热处理军民融合技术与装备、热处理环保技术与装备、热处理高技能人才培养、热处理传感器研制、热处理信息化等服务平台。平台现有各类实验和检测设备、仪器超过500台(套),各类工作场地4000m2,每年服务热处理行业中小企业超过2000家,组织开展各类服务活动超过500场,服务超过4000人次,深受热处理行业中小企业的欢迎。其中热处理装备检测公共服务示范平台(西安电炉研究所有限公司)被工业和信息化部认定为工业节能与绿色发展评价中心,成为面向企业提供能源审计、能效评估、能源检测、环保技术咨询、清洁生产审核及资源综合利用咨询等服务,并协助行业主管部门开展工业节能和绿色发展政策、标准和规范制定的第三方服务机构。热处理行业服务平台和机械工业智能化渗碳热处理柔性生产装备工程研究中心围绕国家发展改革委《增强制造业核心竞争力三年行动计划(2018—2020年)》、工业和信息化部《产业关键共性技术发展指南(2017年)》和科技部提出的“制造基础技术方向”等,开展了智能热处理车间设计、真空渗碳、真空渗氮、热处理井式炉烟气收集处理、热处理车间环保设施建设、水溶性淬火冷却介质推广、生物热处理淬火油研发等一系列技术研究与服务,为热处理行业技术进步提供了有力支持。
新时期迎来“十四五”,未来5年是我国全面开启社会主义现代化强国建设新征程的重要机遇期,是“两个一百年”奋斗目标的历史交汇期,是实现“制造强国”宏伟目标的关键阶段。作为装备制造业产业链中不可或缺的关键环节,热处理行业任重道远。我们坚信,在第九届理事会的领导下,中国热处理行业协会将继续坚持以习近平新时代中国特色社会主义思想为指导,抓住“新基建”需求给热处理行业带来的发展机遇,推进热处理产业基础高级化,坚持热处理行业高质量发展,实现热处理行业“十四五”规划提出的各项工作目标,努力成为政府信得过、企业靠得住、国际有影响的行业协会,带领中国热处理行业向新的高度努力奋进!
〔撰稿人:中国热处理行业协会佟晓辉〕