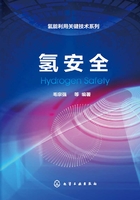
2.4 液氢生产安全
2.4.1 液氢生产
2.4.1.1 液氢的特殊要求与生产工艺流程
常用的可以液化氢气的制冷方法有三种,即J-T节流液化循环、氦膨胀制冷液化循环、氢膨胀制冷液化循环(预冷型Claude系统),分别适用于不同的氢液化规模[16]。对于液化规模5t/d及以上的大规模液氢工厂,均采用预冷型氢透平膨胀机制冷循环。氢气的沸点约20K,临界温度为33K,只有先将氢气冷却到临界温度以下,才有可能进一步通过等熵膨胀或等焓节流的方法降温到20K以下,从而使得氢气液化。在这样低的温区范围下生产和保存液氢,其特殊要求体现在以下几个方面:
①除了氦气之外其他气体在这个温区都会凝固,因此不仅要严格控制原料气氢的杂质成分,而且要对生产和储存液氢的设备、管路系统、容器等进行充分的吹扫置换,避免产生固体颗粒影响系统安全;
②外界热量的入侵会使得氢液化的效率降低和液氢的汽化损耗,因此液氢生产和储存系统的各个环节,都需要高效的绝热方式以及减少热桥的结构设计;
③正氢和仲氢是分子氢的两种自旋异构体,普通氢在常温下含75%的正氢和25%的仲氢,而在低温下正氢向仲氢逐渐转化并释放热量,为了避免液氢储存过程中转化热引起的液氢汽化损耗,必须在生产过程中就完成绝大部分的正仲氢转化过程,成品液氢中的仲氢含量至少要≥95%,长期储运的液氢中的仲氢含量要≥98%。
因此在氢的液化过程中冷却消耗了液化所需能量的绝大部分,包括氢气的降温和正氢向仲氢转化,而其他能耗则主要为压缩流体做功。尽管Peschka[17]的研究指出,液化氢气需要的最小理论能耗为3.92kW•h/kg,而不可避免的传热损失使得实际工程中氢液化的能耗在6.5~15kW•h/kg之间,这与氢液化系统的规模能力和绝热效率有关。
液化氢气的工艺流程具有以下特点:①通过膨胀或节流法制液氢,氢气需要预冷到33K以下;②整个系统需要高效绝热;③液氢温区为20K,液化前需去除氦气以外的其他气体杂质;④系统材料需具备耐超低温与抗氢脆的性能;⑤减少热桥,提高密封性;⑥必须具备正-仲氢转化能力。
根据以上特点,目前工业上制备液氢主要包含以下步骤:①氢气提纯与干燥;②氢气压缩;③氢气冷却;④膨胀/节流液化;⑤正-仲氢转化。图2-7为位于德国Ingolstadt的Linde氢液化生产装置的工艺流程[16],经过PSA纯化的氢气杂质含量低于4mg/kg,压缩到2.1MPa的原料气再在位于液氮温区的低温吸附器中进一步纯化至杂质含量1mg/kg以下,然后送入液化系统。液化的过程中同时进行正仲氢转换,最后生产出仲氢量≥95%的液氢送往容积为270m3的液氢储罐。

图2-7 德国Ingolstadt的Linde氢液化流程
2.4.1.2 液氢生产过程中的氢气纯度控制
为了确保液氢生产和储存的安全,各国标准对生产用原料气和生产储存系统都提出了严格的氢气纯度和杂质含量控制要求。
①俄罗斯GOST R56248—2014《液氢技术标准》[18]规定,液氢容器充装后,容器中所包含的氧杂质含量体积分数应不大于3×10-4%,氮体积分数不大于2×10-2%。并按照批准的技术规范来进行液氢容器的准备和充装。而且吹扫液氢进出管道时,吹扫气体中氧杂质体积分数应不大于3×10-4%,氮体积分数不大于2×10-2%。吹扫持续30min。杂质浓度至少测定三次,氧和氮气各自的体积分数不得超过极限值。
②ISO液氢安全标准ISOTR 15916《Basic considerations for the safety of hydrogen systems》[19]规定,空的液氢罐重新使用时,要确定氧、氮等杂质的积累。当使混合物在限制条件下温热至气态时,储存的氢气中的氧气积累不应超过2%体积分数,并不是液氢中氧、氮的含量。《Hydrogen fuel-Product specification-Part 2:Proton exchange membrane(PEM)fuel cell applications for road vehicles》(ISO14687-2—2012)[20]标准规定,氧含量不大于5ppm,氦含量不大于300ppm,氮含量不大于100ppm。
③EIGA欧洲工业气体协会标准《SAFETY IN STORAGE,HANDLING AND DISTRIBUTIONOFLIQUID HYDROGEN》[21]规定,在压力测试之后并且在将氢气引入系统的任何部分之前,应从系统中除去氧气。如果使用氦气作为惰性吹扫气体去除氧气,则使用冷氢气作为二次吹扫气体以消除氦气。如果使用氮气或其他惰性气体作为吹扫气体去除氧气,则使用温氢气作为二次吹扫气体以消除氮气,然后使用冷氢气冷却系统。通过用惰性气体(氦气或氮气)吹扫,加压和排气,并检查以确保任何残余氧气小于0.5%。但是这并不是液氢中氧、氮的含量。
④美国压缩气体协会标准CGA G-5.3-2011《Commodity specification for hydrogen》[22]中规定,液氢中杂质的总含量与氢纯度有关。氢纯度99.995%时,气体杂质总含量应小于50ppm;氢纯度99.999%时,气体杂质总含量应小于10ppm;氢纯度99.9997%时,气体杂质总含量应小于3ppm。
⑤中国军用标准GJB 2645—96《液氢贮存运输要求》规定氧的体积含量不超过9×10-4,按照流程置换容器内气体8次后,取样进行分析直到满足要求。
液氢系统中杂质所导致的意外事故在国内外均有发生[23],案例如下。
①中科院物理研究所某小型氢液化器的三次爆炸 氢中氮、氧在液氢温度下冻结堵塞了节流阀前的高压管道,把管道炸成了3~5cm长的碎片,曾两次把液氢槽炸开。另一次爆炸是因吸附器温度回升,氮、氧等杂质脱附出来进入汽化器,因管道、阀门被固体杂质堵塞而爆裂,使节流阀炸成2~3cm的碎片。
②国内某工程氢液化器的两次爆炸 两次均为节流阀被固体氧颗粒堵塞,在开关节流阀时发生了爆炸,一次将液氢槽内4条并联的紫铜盘管炸成2~3cm碎片,另一次把节流阀前的高压铜管炸坏。
③国外吨级液氢工厂的爆炸事故 在正常操作情况下,阀入口处氢中氧含量1×10-6,压力3.38MPa,温度33.2K。曾沿着节流阀发生了一次爆炸,结果炸坏了节流阀及其邻近管道而停工检修。
为了达到和维持液氢安全生产过程中所需的氢气纯度,常见的氢气纯化过程控制手段有:
①制备超纯氢生产液氢 曾有文献指出[24],将液化前氢中氧含量的安全阈值定为1×10-9,当使用氧含量小于安全阈值的超纯氢生产液氢时,则氢液化器中不会有固氧积累,从而消除发生爆炸的可能性。在实验室环境中的低温吸附纯化数据表明,在液氮温度下用细孔硅胶或活性炭作为吸附剂,都能制得超纯氢,虽然在经济性上会造成成本增加,但在技术上是可行的,是理论上最好的方法。
②液氢洗涤过滤 当工业中氧含量无法达到10-9量级时,可利用液氢洗涤气氢中的氧,析出的固氧再经过滤,对氢进行再纯化,在洗涤过滤器出口的气氢和液氢混合物内,氧含量可稳定在10-9数量级以上,基本防止了发生固氧爆炸的可能。
③调节液化前氢中的氮、氧浓度比 研究表明,液氢内冻结杂质中的氧、氮比与是否发生固氧爆炸有很大关系,当氧含量为正常空气组分或低于正常空气组分时,不易发生爆炸。例如节流前高压压机渗漏空气,有时也发生固空堵塞节流阀的情况,但不易发生爆炸,所以设法调节氧、氮比,使之小于正常空气组分也是防止爆炸的一个途径。
实践证明,液氢的生产过程通过氢气提纯工艺的优化能够起到良好的防爆效果。
2.4.1.3 液氢生产系统安全
在中国,火箭发射用液氢一般按照符合GJB 71液氢生产技术指标进行要求。而在2019年7月,根据国家标准化管理委员会标准制修订计划,由全国氢能标准化技术委员会提出并归口的《液氢生产系统技术规范》国家标准已完成征求意见稿并即将颁布实施。该标准对民用场景中液氢生产系统的建筑、场地、配置等进行了规范,如:
①液氢生产系统不得设置在人员密集地段和交通要道邻近处,宜设置不燃烧体的实体围墙,其高度不应小于2.5m,该围墙与其他建筑之间的间距不宜小于5.0m。
②液氢生产系统场所的安全出口不得少于两个,且应分散布置。
③液氢生产系统宜布置在独立的单层建(构)筑物内,可采用敞开式或半敞开式,该建(构)筑物的设计应符合GB 50177《氢气站设计规范》的规定。
④液氢生产系统区域内的道路宽度不应小于4m,路面上的净空高度不应小于4.5m。
持续监控氢气的纯度对于液氢安全生产至关重要。杂质固体颗粒可能会堵塞换热器、阀门及组件,造成系统压力突升;若沉积在换热管内表面上会降低传热系数;若固态杂质进入膨胀机内部则会促使活塞卡住或涡轮喷管堵塞失效;固态氧浓度累积到一定程度时,由于氧晶体断裂时会释放能量,即使在无火花的情况下,也会在系统内部引发燃烧或爆炸的可能性。
为了确保氢液化装置的连续安全运行和液氢产品质量,需要对氢液化工艺各关键质量控制点的氢进行分析化验,严格控制氢品质。通常要求检测液氢中的氧、氯、氮、水、甲烷、一氧化碳、二氧化碳的含量,以及有滴状和蒸气状的油和水。关键质量控制点包括:气源、2个吸附器出口、液氢。氢中氧作为安全威胁最大的杂质,其含量检测可使用气相色谱法或微量氧分析仪进行检测,其中燃料电池式与赫兹电池式最为常用。此外,清除氢气中氧的方法有通过金属催化剂还原成水、活性炭或硅胶吸附氧等方式移除,而所生成的水可利用换热器冻结清除,在4~5℃下用氧化铝、硅胶或化学吸收剂如氢氧化钠与氢氧化钾来清除。
氢气中的氮可利用冻结法以及吸附法来移除。吸附法方面,80K低温下活性炭与硅胶具有很高的吸附能力,常被用来清除氢气中的氮、氧、氩气与一氧化碳;冻结法方面,由于在换热器冷端阀门前可能会有许多冻结的固态氮颗粒,可在冷端前加装真空过滤器以去除氮颗粒。另外,在80~100K的温区下可通过吸附法将甲烷去除,而二氧化碳则可采用冻结法或碱洗涤法方式清除。
由此可见,氢气中的杂质气体需通过数道程序才能将杂质浓度降至不超过10-6的体积含量。
液氢生产系统安全的重要措施还包括阀件与管路的设计与选型。液氢系统阀件方面,其材料选择与结构设计要能够确保气密性与绝热性。材料选择需避免阀件发生卡住或者咬死状况,所有活动连接或螺纹连接材料应在低温下具备不同的硬度,且在液氢温区下,活门应该采用软活门座、活门密封垫采用特氟隆或凯尔夫塑料材质;为了保证绝热性与漏热最小,阀件结构设计应尽可能采用加长手柄结构,阀门密封垫在热端而螺纹在冷端,带有波纹管密封的阀门可保证防止氢渗漏,确保气密性。
管路方面,外界环境漏热会导致管路内部因液氢汽化出现气-液两相流,会增大液氢流动阻力、降低液氢流量,影响了液氢的加注或转注,可通过加大系统压力促使液氢过冷,以及采用高效的真空绝热技术来避免管路内两相流产生。带夹套的真空绝热管路还需考虑内管、外管同心配置,内外管之间的支承避免热桥,避免真空丧失导致的绝热性能降低等。
通过液氢生产过程的在线监测和数据分析,已经能够通过数据变化、超标等情况自动预警,大大提高了氢液化装置运行的可靠性和安全性,保证氢液化装置可靠、稳定、安全地运行。