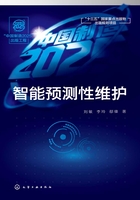
1.2.3 状态维护
状态监测通过监测机械的状态参数(如振动、温度等)变化,来识别一个正在产生的故障。状态监测技术可分为状态检测技术(探测潜在故障的影响,如振动特性变化、温度变化、润滑油颗粒以及化学效应等)、产品质量检测技术(设备制造出来的产品有缺陷常与设备本身的缺陷有直接关系)、主要参数检测技术(如设备的速度、流速、压力、功率、电流等)和基于人类感官的检查技术(如看、听、摸和闻)等。状态监测通常用于一些旋转设备、辅助系统和其他机械,如压缩机、泵、电动机、内燃机、压力机等。一些静态设备,如蒸汽锅炉、管道和热交换器等,则常采用非破坏性实验技术和适用性评估进行定期检查。
状态维护是一种基于状态监测技术的预防性维护策略,试图在正确的时间维护正确的设备。状态维护基于这样一种事实:大量故障不会瞬间发生,实际上故障要发展一段时间。如果发现这种故障过程正在发展,就可以采取措施预防故障或避免严重的后果。在故障发展过程中,可以探测到故障正在发生或将要发生,该点称为潜在故障点P,如图1.6所示。潜在故障是一种可辨认的实际状态,能显示功能故障将要发生或正在发生,例如,显示轴承临近故障的振动、显示金属疲劳的裂纹、显示齿轮临近故障的齿轮箱润滑油中的颗粒、轮胎胎纹过度磨损等。

图1.6 设备性能的P-F曲线
设备性能存在一个由开始劣化并进入潜在故障期的渐变过程,从潜在故障到功能故障的间隔期为P-F间隔。图1.6所示的P-F曲线揭示了故障开始、劣化到故障可被探测到潜在故障点P的一般过程,如果未探测到也未纠正,则性能继续变坏,直到到达设备的功能故障点(F)。如果在P点和F点之间探测到潜在故障,那么可以预防功能性故障或避免故障后果。状态维护就是检查设备的潜在故障,以便采取措施预防故障或避免功能故障的后果。
状态维护的检查频度必须远远小于P-F间隔(故障可探测的潜在故障点到故障发展成为功能故障点之间所需的时间),否则就可能完全漏掉故障。大多数功能故障出现之前,有不止一个(常有几个不同)的潜在故障,每个潜在故障都有一个不同的P-F间隔。例如,轴承功能故障之前,通过振动分析检查出振动特性(P-F间隔1~9个月),通过油质分析检测磨粒(P-F间隔1~6个月),可听见噪声(P-F间隔1~4周),发热(手摸)(P-F间隔1~5天)等。
如图1.7所示,状态维护技术包括数据获取、特征提取、故障检测、故障诊断和故障预测等内容。数据获取可能涉及各种类型的数据信息,如振动、温度、压力、速度、电压或电流、应力/应变/冲击、位置、颗粒计数/组成等。特征提取计算包括快速傅里叶变换、小波变换、自适应时频分析、数据过滤/平滑、温度/压力比、能效等。故障检测算法提醒用户设备存在的潜在问题或未知失效。故障诊断算法用于隔离、识别特定组件或子系统的故障。故障预测算法基于历史和当前的运营概况估计设备的可用使用寿命RUL或失效概率。监督式推理算法协调相互冲突的信息并提供以下维护建议:检查间隔、维修、备件订购、设备停机等。

图1.7 面向复杂设备系统的状态维护技术

图1.8 状态维护优化成本
如图1.8所示,状态维护比计划维护和主动维护等预防性维护以及故障维护在以下方面具有一些优势[9]:
①系统可靠性高,维护成本低;
②维护操作次数的降低减小了人为错误的影响。
状态维护的缺点是:
①较高的安装成本;
②不可预测的维护周期导致了成本分配不均;
③需要维护和检查的部件数量多(包括状态维护系统自身的安装)。