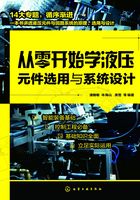
5.1 单向阀
单向阀可分为普通单向阀和液控单向阀。普通单向阀只允许油液往一个方向流动,反向截止。液控单向阀在外控油作用下,反方向也可流动。
5.1.1 普通单向阀
(1)工作原理
普通单向阀一般称为单向阀,其结构简图见图5⁃1。压力油从P1腔进入时,克服弹簧力推动阀芯,使油路接通。压力油从P2腔流出,称为正向流动。当压力油从P2腔进入时,油液压力和弹簧力将阀芯紧压在阀座上,油液不能通过,称为反向截止。

图5⁃1 单向阀的结构和图形符号
1—阀芯(锥阀或球阀);2—阀体;3—弹簧
(2)单向阀的开启条件
要使阀芯开启,液压力必须克服弹簧力Fk、摩擦力Ff和阀芯重量G,即

(5⁃1)
式中 p1——进油腔1油压力,Pa;
p2——出油腔2油压力,Pa;
Fk——弹簧力,N;
Ff——阀芯与阀座的摩擦力,N;
G——阀芯重量(水平放置时为0),N;
A——阀口面积,m2。
单向阀的开启压力pk一般都设计得较小,一般为0.03~0.05MPa,这是为了尽可能降低油流通过时的压力损失。但当单向阀作为背压阀使用时,可将弹簧设计得较硬,使开启压力增高,使系统回油保持一定的背压。可以根据实际使用需要更换弹簧,以改变其开启压力。
(3)典型结构和特点
单向阀按阀芯结构分为球阀和锥阀,图5⁃1(a)为球阀式单向阀。球阀结构简单,制造方便,但由于钢球有圆度误差,而且没有导向,密封性差,一般在小流量场合使用。图5⁃1(b)为锥阀式单向阀,其特点是当油被正向通过时,阻力可以设计得较小,而且密封性较好。但工艺要求严格,阀体孔与阀座孔需有较高的同轴度,且阀芯锥面必须进行精磨加工。在高压大流量场合下一般都使用锥阀式结构。
单向阀按进出口油流的方向可分为直通式和直角式。直通式单向阀的进出口在同一轴线上(即管式结构),结构简单,体积小,但容易产生自振和噪声,而且装于系统更换弹簧很不方便。直角式单向阀的进出口油液方向成直角布置,见图5⁃2,其阀芯中间容积是半封闭状态,阀芯上的径向孔对阀芯振动有阻尼作用,更换阀芯弹簧时,不用将阀从系统拆下、性能良好。

图5⁃2 直角式单向阀的结构
(4)主要性能要求
① 正向最小开启压力pk=(Fk+Ff+G)/A,国产单向阀开启压力有0.04MPa和0.4MPa,通过更换弹簧,改变刚度K来改变开启压力的大小。
② 反向密封性好。
③ 正向流阻小。
④ 动作灵敏。
(5)应用
主要用于不允许液流反向的场合。
① 单独用于油泵出口,防止由于系统压力突升油液倒流而损坏油泵,见图5⁃3(a)。

图5⁃3 单向阀的应用
② 隔开油路间不必要的联系。
③ 配合蓄能器实现保压。
④ 作为旁路与其他阀组成复合阀。常见的有单向节流阀、单向顺序阀、单向调速阀等。
⑤ 采用较硬弹簧作背压阀。如图5⁃3(b)所示,电液换向阀中位时使系统卸荷,单向阀保持进口侧油路的压力不低于它的开启压力,以保证控制油路有足够压力使换向阀换向。
(6)主要故障
① 当油液反向进入时,阀芯不能将油液严格封闭而产生泄漏,特别是p2较低更为严重。应检查阀芯与阀座的接触是否紧密,阀座孔与阀芯是否满足同轴度要求,或当阀座压入阀体孔时有没有压歪,如不符合要求,则需要阀芯与阀座重新研配。
② 单向阀不灵,阀芯有卡阻现象,应检查阀座孔与阀芯的加工精度,并应检查弹簧是否断裂或过分弯曲。应该注意的是,无论是直角型还是直通型单向阀,都不允许阀芯锥面向上安装。
5.1.2 液控单向阀
(1)工作原理
液控单向阀是可以根据需要实现逆向流动的单向阀,见图5⁃4。图中上半部与一般单向阀相同,当控制口K不通压力油时,阀的作用与单向阀相同,只允许油液向一个方向流动,反向截止。下半部分有一个控制活塞1,控制口K通以一定压力的油液,推动控制活塞并通过推杆2抬起锥阀阀芯3,使阀保持开启状态,油液就可以由P2流到P1,即反向流动。

图5⁃4 液控单向阀的工作原理
1—控制活塞;2—推杆;3—锥阀阀芯;4—弹簧
(2)反向开启条件
要使阀芯反向开启必须满足
(pk-p1)Ak-Ff 2>(p2-p1)A+Fk+Ff1+G (5⁃2)
即 pk>(p2-p1)+p1
+
式中 pk——阀反向开启时的控制油压力,MPa;
p1——出油腔油压力,MPa;
p2——进油腔油压力,MPa;
Ak——控制活塞面积,m2;
Ff 2——控制活塞摩擦力,N;
A——锥阀活塞面积,m2;
Fk——弹簧力,N;
Ff1——锥阀芯摩擦阻力,N;
G——阀芯与控制活塞重量之和,N。
由上式可以看出,液控单向阀反向开启压力主要取决于进油腔压力p2和锥阀活塞与控制活塞面积比,也与出油腔压力p1有关。
(3)典型结构和特点
图5⁃5是内泄式液控单向阀,它的控制活塞阀上腔与P1腔相通,所以叫内泄式。它结构简单,制造方便。但由于结构限制,控制活塞面积Ak不能比阀芯面积大很多,因此反向开启的控制压力pk较大。当p1=0时,pk≈(0.4~0.5)p2。若p1≠0时,pk将会更大一些,所以这种阀只用于低压场合。
为了减少出油腔压力p1对开启控制压力pk的影响,出现了图5⁃6所示的外泄式液控单向阀,在控制活塞的上腔增加了外泄口与油箱连通,减少了P1腔压力在控制活塞上的作用面积。此时式(5⁃2)改写为(忽略摩擦力和重力)

(5⁃3)
式中 A1——P1腔压力作用在控制活塞上的活塞杆面积,m2。
A1/Ak越小,p1对pk的影响越小。

图5⁃5 内泄式液控单向阀的结构

图5⁃6 外泄式液控单向阀的结构
在高压系统中,上述两种结构所需的反向开启控制压力均很高,为此应采用带卸荷阀芯的液控单向阀,它也有内泄式和外泄式两种结构。图5⁃7为内泄式带卸荷阀芯的液控单向阀。它在锥阀3(主阀)内部增加了一个卸荷阀芯6,在控制活塞顶起锥阀之前先顶起卸荷阀芯6,使锥阀上部的油液通过卸荷阀上铣去的缺口与下腔压力油相通,阀上部的油液通过泄油口到下腔,上腔压力有所下降,上下腔压力差p2-p1减少,此时控制活塞便可将锥阀顶起,油液从P2腔流向P1腔,卸荷阀芯顶开后,p2-p1≈0,所以式(5⁃2)就变成

图5⁃7 内泄式带卸荷阀芯的液控单向阀的结构
1—控制活塞;2—推杆;3—锥阀;4—弹簧座;5—弹簧;6—卸荷阀芯

(5⁃4)
即开启压力大大减少,这是高压液控单向阀常采用的一种结构。
图5⁃8为外泄式带卸荷阀芯的液控单向阀,该阀可以进一步减少出油口压力p1对p2的影响,所需开启压力为

因为A1<A,所以外泄式液控单向阀所需反向开启控制压力比内泄式的低。

图5⁃8 外泄式带卸荷阀芯的液控单向阀的结构
图5⁃9为卸荷阀芯的结构,由于它的结构比较复杂,加工也困难,尤其是通径较小时结构更小,加工更困难,因此近年来国内外都采用钢球代替卸荷阀芯,封闭主阀下端的小孔来达到同样的目的(见图5⁃10和图5⁃11)。它是将一个钢球压入弹簧座内,利用钢球的圆球面将阀芯小孔封闭。这种结构大大简化了工艺,解决了卸荷阀芯加工困难的问题。但是,这种结构的控制活塞的顶端应加长一小段,伸入阀芯小孔内,由于这个阀芯孔较小,控制活塞端部伸入的一段较细,因而容易发生弯曲甚至断裂。另外,对阀体上端阀芯孔和下端控制活塞孔的同轴度的要求也提高了。
带卸荷阀结构的液控单向阀,由于卸荷阀芯开启时与主阀芯小孔之间的缝隙较小,通过这个缝隙能溢掉的油液量是有限的,所以,它仅仅适合于反向油流是一个封闭的场合,如液压缸的一腔、蓄能器等。封闭的容腔的压力油只需释放很少一点流量便可将压力卸掉,这样就可以用很小的控制压力将主阀芯打开。如果反向油流是一个连续供油的油源,如直接来自液压泵的供油,由于连续供油的流量很大,这么大的流量强迫它从很小的缝隙通过,油流必然获得很高的流速,同时造成很大的压力损失,而反向油流的压力仍然降不下来。所以虽然卸荷阀芯打开了,但仍有很高的反向油流压力压在主阀芯上,因而仅能打开卸荷阀芯,却打不开主阀芯,使反向油流的压力降不到零,油液也就不能全部通过。在这种情况下,要使反向连续供油全部反向通过,必须大大提高控制压力,将主阀芯打开到一定开度才行。
图5⁃12是将两个液控单向阀布置在同一个阀体内,称为双液控单向阀,也叫液压锁。其工作原理是:当液压系统一条通路的油液从A腔进入时,依靠油液压力自动将左边的阀芯推开,使A腔的油液流入A1,同时,将中间的控制活塞的阀芯右推,将右边的阀芯顶开,使B腔与B1腔相沟通,把原来封闭在B1腔通路上的油液通过B腔排出。总之就是当一个油腔是正向进油时,另一个油腔就是反向出油,反之亦然。

图5⁃9 卸荷阀芯的结构

图5⁃10 钢球密封的结构

图5⁃11 钢球式卸荷阀芯液控单向阀的结构

图5⁃12 双液控单向阀的结构
(4)主要性能要求
① 最小正向开启压力要小。最小正向开启压力与单向阀相同,为0.03~0.05MPa。
② 反向密封性好。
③ 压力损失小。
④ 反向开启最小控制压力一般为
不带卸荷阀 pk=(0.4~0.5)p2(p1=0)
带卸荷阀 pk=0.05p2(p1=0)
(5)应用
液控单向阀在液压系统中的应用范围很广,主要利用液控单向阀锥阀良好的密封性。图5⁃13所示为利用液控单向阀的锁紧回路,锁紧的可靠性及锁定位置的精度,仅仅受液压缸本身内泄漏的影响。图5⁃14的保压回路,可保证将活塞锁定在任何位置,并可防止由于换向阀的内部泄漏引起带有负载的活塞杆下落。

图5⁃13 利用液控单向阀的锁紧回路

图5⁃14 防止自重下落回路(保压回路)
在液压缸活塞夹紧工件或顶起重物过程中,由于停电等突然事故而使液压泵供电中断时,可采用液控单向阀,打开蓄能器回路,以保持其压力,见图5⁃15。当二位四通电磁阀处于左位时,液压泵输出的压力油正向通过液控单向阀1和2,向液压缸和蓄能器同时供油,以夹紧工件或顶起重物。当突然停电液压泵停止供油时,液控单向阀1关闭,而液控单向阀2仍靠液压缸A腔的压力油打开,沟通蓄能器,液压缸靠蓄能器内的压力油保持压力。这种场合的液控单向阀必须带卸荷阀芯,并且是外泄式的结构,否则,由于这里液控单向阀反向出油腔油流的背压就是液压缸A腔的压力,因为压力较高而有可能打不开液控单向阀。
在蓄能器供油回路里,可以采用液控单向阀,利用蓄能器本身的压力将液控单向阀打开,使蓄能器向系统供油。这种场合应选择带卸荷阀芯的并且是外泄式结构的液控单向阀,见图5⁃16。当二位四通电磁换向阀处于右位时,液控单向阀处于关闭状态;当电磁铁通电使换向阀处于左位时,蓄能器内的压力油将液控单向阀打开,同时向系统供油。

图5⁃15 利用液控单向阀的保压回路
1,2—液控单向阀

图5⁃16 蓄能器供油回路
液控单向阀也可作充液阀,如图5⁃17所示。活塞等以自重空程下行时,液压缸上腔产生部分真空,液控单向阀正向导通从充液箱吸油。活塞回程时,依靠液压缸下腔油路压力打开液控单向阀,使液压缸的上腔通过它向充液油箱排油。因为充液时通过的流量很大,所以充液阀一般需要自行设计。
(6)主要故障和使用注意事项
液控单向阀由于阀座压装时的缺陷,或者阀座孔与安装阀芯的阀体孔加工时同轴度误差超过要求,均会使阀芯锥面和阀座接触处产生缝隙,不能严格密封,尤其是带卸荷阀芯式的结构,更容易发生泄漏。这时需要将阀芯锥面与阀座孔重新研配,或者将阀座卸出重新压装。用钢球作卸荷阀芯的液控单向阀,有时会发生控制活塞端部小杆顶不到钢球而打不开阀的现象,这时需检查阀体上下两孔(阀芯孔与控制活塞孔)的同轴度是否符合要求,或者控制活塞端部是否有弯曲现象。如果阀芯打开后不能回复到初始封油位置,则需检查阀芯在阀体孔内是否卡住,弹簧是否断裂或者过分弯曲,而使阀芯产生卡阻现象。也可能是阀芯与阀体孔的加工几何精度达不到要求,或者二者的配合间隙太小而引起卡阻。

图5⁃17 液控单向阀作充液阀
液控单向阀在使用中还应注意以下几点。
① 液控单向阀回路设计应确保反向油流有足够的控制压力,以保证阀芯的开启。如图5⁃14所示,如果没有节流阀,则当三位四通换向阀换向到右边通路时,液压泵向液压缸上腔供油,同时打开液控单向阀,液压缸活塞受负载重量的作用迅速下降,造成由于液压泵向液压缸上腔供油不足而使压力降低,即液控单向阀的控制压力降低,使液控单向阀有可能关闭,活塞停止下降。随后,在流量继续补充的情形下,压力再升高,控制油再将液控单向阀打开。这样由于液控单向阀的开开闭闭,使液压缸活塞的下降断断续续,从而产生频振荡。
② 前面介绍的内泄式和外泄式液控单向阀,分别使用在反向出口腔油流背压较低或较高的场合,以降低控制压力。如图5⁃18(a)所示,液控单向阀装在单向节流阀的后部,反向出油腔油流直接接回油箱,背压很小,可采用内泄式结构。图5⁃18(b)中的液控单向阀安装在单向节流阀的前部,反向出油腔通过单向节流阀回油箱,背压很高,采用外泄式结构为宜。

图5⁃18 内泄式和外泄式液控单向阀的不同应用场合
③ 当液控单向阀从控制活塞将阀芯打开,使反向油流通过,到卸掉控制油,控制活塞返回,使阀芯重新关闭的过程中,控制活塞容腔中的油要从控制油口排出,如果控制油路回油背压较高,排油不通畅,则控制活塞不能迅速返回,阀芯的关闭速度也要受到影响。这对需要快速切断反向油流的系统来说是不能满足要求的。为此,可以采用外泄式结构的液控单向阀,如图5⁃19所示,将压力油引入外泄口,强迫控制活塞迅速返回。
(7)选用
① 选用液控单向阀时,应考虑打开液控单向阀所需的控制压力。此外还应考虑系统压力变化对控制油路压力变化的影响,以免出现误开启。

图5⁃19 液控单向阀的强迫返回回路
② 在油流反向出口无背压的油路中可选用内泄式,否则需用外泄式,以降低控制油的压力,而外泄式的泄油口必须无压回油,否则会抵消一部分控制压力。