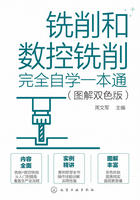
第六节 机械加工工艺规程的制定
一、工艺规程及其作用
在小批量生产中,一般应拟定工艺过程卡片,在批量生产中,除制定工艺过程卡片之外,还应制定工序卡片。
机械加工工艺规程的作用主要有以下三个方面。
① 加工工艺规程是顺利生产的重要保证,按照它组织生产,就能做到各工序科学地衔接,实现优质、高产和低耗。
② 加工工艺规程是生产准备和计划调度的主要依据,使生产均衡顺利地进行。
③ 加工工艺规程是新建、扩建和改造生产系统的基本技术文件。
二、机械加工工艺规程制定
正确的工艺规程必须满足图样的各项技术要求;必须结合本单位的实际情况;必须保证工艺的经济性、技术的先进性和方案的可实施性。
1.资料准备
这些资料与信息包括产品技术信息(完整的图样和技术要求等)、产品的生产信息(生产批量、交货时间等);产品原材料信息(毛坯或材料的供应情况等);生产条件信息(现有生产的设备状况、人员素质等);新技术、新工艺、新材料信息(国内外的先进工艺及生产技术的发展状况等)。
2.计算年生产纲领
通过计算年生产纲领,确定产品的生产类型是大批量、中批量还是单件小批量生产,生产类型是制定工艺规程的重要依据。
3.加工零件的工艺性分析
工艺性分析就是分析影响零件加工难易程度的因素,为采取合理工艺措施奠定基础,包括以下内容,见表3-41。
表3-41 加工零件的工艺性分析

表3-42 在常规工艺条件下零件结构工艺性分析举例



4.毛坯选择
选择毛坯的种类和制造方法时应全面考虑机械加工成本和毛坯制造成本,以达到降低零件生产总成本的目的。
① 毛坯的种类(表3-43)
表3-43 毛坯的种类

② 毛坯选择时应考虑的因素(表3-44)
表3-44 毛坯选择时应考虑的因素


5.拟定工艺过程
包括划分工艺过程的组成,选择定位基准、选择零件表面的加工方法,安排加工顺序和组合工序等。
6.工序设计
包括选择机床和工艺装备、确定加工余量、计算工序尺寸及其公差、确定切削用量及计算工时定额等。
7.编制工艺文件
按照一定的格式和要求编制工艺文件。
三、工艺过程的设计
1.定位基准的选择
选择定位基准时,是从保证工件加工精度要求出发的,因此,定位基准的选择应先选择精基准,再选择粗基准。
(1)精基准的选择原则
选择精基准时,主要应考虑保证加工精度和工件安装方便可靠,其选择原则见表3-45。
表3-45 精基准的选择原则



图3-75 基准不重合误差示例

图3-76 基准重合安装示意

图3-77 自为基准实例
(2)粗基准的选择原则
选择粗基准时,主要要求保证各加工面有足够的加工余量,使加工面与不加工面间的位置符合图样要求,并特别注意要尽快获得精基准面。具体选择时应考虑下列原则,见表3-46。
表3-46 粗基准的选择原则除



图3-78 床身加工的粗基准选择

图3-79 粗基准选择的实例
实际上,无论精基准还是粗基准的选择,上述原则都不可能同时满足,有时还是互相矛盾的。因此,在选择时应根据具体情况进行分析,权衡利弊,保证其主要的要求。
(3)定位基准选择示例
例:如图3-80所示为车床进刀轴架零件,若已知其工艺过程如下。
① 划线。
② 粗精铣底面和凸台。
③ 粗精镗φ33H7孔。
④ 钻、扩、铰φ17H9孔。

图3-80 车床进刀轴架
选择各工序的定位基准。
第一道工序:划线。毛坯误差较大时,采用划线的方法能兼顾到几个不加工面对加工面的位置要求。选择不加工面R21mm外圆和R16mm外圆为粗基准,同时兼顾不加工的上平面与底面距离17mm的要求,划出底面和凸台的加工线。
第二道工序:按划线找正,铣底面和凸台。
第三道工序:粗精镗φ33H7孔。加工要求为尺寸(33±0.1) mm、6±0.1mm及凸台侧面K的平行度0.03mm。根据基准重合的原则选择底面和凸台为定位基准。
第四道工序:钻、扩、铰φ17H9孔。本工序应保证的位置要求为尺寸(5±0.1) mm、(52±0.1) mm及两孔的平行度要求0.02mm。根据精基准选择原则,可以有三种不同的方案。
① 底面和K面为基准 加工两孔采用了基准统一原则。夹具比较简单。
设计尺寸(5±0.1)mm与基准重合;尺寸(52±0.1)mm的工序基准是孔φ33H7的中心线,而定位基准是K面,定位尺寸为(7±0.1)mm,存在基准不重合误差,其大小等于0.2mm;两孔平行度0.02mm也有基准不重合误差,其大小等于0.03mm。因此,此方案基准不重合误差已经超过了允许的范围,不可行。
② φ33H7孔和底面为基准 对尺寸(5±0.1) mm有基准不重合误差,且定位销细长,刚性较差,所以也不好。
③ 底面和φ33H7孔为基准 工件的定位可用平面和一个长的菱形销来实现,三个设计要求均为基准生命,唯φ33H7孔的轴线对于底面的垂直度误差将会影响两孔轴线的平行度,应当在镗φ33H7孔时加以限制。
经过以上分析,第三方案基准基本上重合,夹具结构也不太复杂,装夹方便,故应采用。
2.加工方法的选择
工件表面的加工方法 ,首先取决于加工表面的技术要求,这些技术要求还包括由于基准不重合而提高对某些表面的加工要求,根据各加工表面的技术要求,首先选择能保证该要求的最终加工方法,然后确定各工序、工步的加工方法,如图3-81所示为在加工工艺路线拟定中,表面加工方法的确定过程。

图3-81 表面加工方法确定过程
选择加工方法应考虑的因素见表3-47。
3.加工顺序的安排
(1)加工阶段的划分
表3-47 选择加工方法应考虑的因素

按加工性质和作用的不同,工艺过程一般可分为粗加工阶段、半精加工阶段、精加工阶段和光整加工阶段,其说明见表3-48。
表3-48 加工阶段的划分

(2)加工顺序的安排
① 切削加工顺序的安排(表3-49)
表3-49 切削加工顺序的安排

② 热处理工序的安排(表3-50)
表3-50 热处理工序的安排


③ 辅助工序的安排(表3-51)
表3-51 辅助工序的安排

4.工序的组合
工序组合一般采用工序集中或工序分散的原则。
(1)工序集中
就是将工件的基本加工工序集中在少数几道工序中完成,每道工序加工内容多,工艺路线短。其主要特点如下:
① 可以采用高效机床和工艺装备,生产率高。
② 减少了设备数量以及操作工人人数和占地面积,节省人力、物力。
③ 减少了工件安装次数,利于保证表面间的位置精度。
④ 采用的工装设备结构复杂,调整维修较困难,生产准备工作量大。
(2)工序分散
就是将工件的基本加工工序分散到多道工序内完成,每道工序加工的内容少,工艺路线很长。其主要特点是:
① 设备和工艺装备比较简单,便于调整,容易适应产品的变换。
② 对工人的技术要求较低。
③ 可以采用最合理的切削用量,减少机动时间。
④ 所需设备和工艺装备的数目多,操作工人多,占地面积大。
在拟定工艺路线时,工序集中或分散的程度,主要取决于生产规模、零件的结构特点和技术要求。有时还要考虑各工序生产节拍的一致性。一般情况下,单件小批生产时,采用工序集中,在一台普通机床上加工出尽量多的表面;大批量生产时,既可以采用多刀、多轴等高效、自动机床,将工序集中,也可以将工序分散后组织流水生产。批量生产应尽可能采用效率较高的半自动机床,使工序适当集中,从而有效地提高生产率。对于重型零件,为了减少零件装卸和运输的劳动量,工序应适当集中;对于刚性差且精度高的精密工件,则工序应适当分散。
四、工序的设计
零件在工艺过程设计后,应进行工序设计。主要工作是为每一工序选择机床和工艺装备,确定加工余量、工序尺寸和公差,确定切削用量和工时定额等。
1.机床与工艺装备的选择
① 机床的加工范围应与零件的外廓尺寸相适用。
② 机床的工作精度应与工序要求的精度相适应。
③ 机床的生产率与工件生产类型相适应。
④ 机床的选择应考虑车间现有设备条件,改装设备或设计专用机床。
2.工艺装备的选择(表3-52)
表3-52 工艺装备的选择

3.工序尺寸及公差的确定(工艺计算)
由于工序尺寸是工件在加工时各工序应保证的加工尺寸,因此正确地确定工序尺寸及其公差是工序设计的一项重要的工作。
工序尺寸的计算要根据工件图上的设计尺寸、已确定的各工序的加工余量以及定位基准的转换关系来进行。工序尺寸公差则按各工序加工方法的经济精度选定。工序尺寸及偏差标注在各工序的工序简图上,作为加工和测验的依据。
(1)定位基准与设计基准重合时的工序尺寸确定
对于各工序的定位基准与设计基准重合时的表面的多次加工,其工序尺寸的计算比较简单。此时只要根据工件图上的设计尺寸、各工序的加工余量、各工序所能达到的精度,由最后一道工序开始依次向前推算,直至毛坯为止,即可确定各工序尺寸及公差。
例:某车床主轴箱箱体的主轴孔,设计要求为φ100Js6,Ra0.8μm,加工工序为粗镗→半精镗→精镗→浮动镗四道工序。
确定各工序的基本余量,要根据相关知识及工厂实际经验,具体数值见表3-53中的第二列;再根据各种加工方法的经济精度表格确定各工序尺寸的公差,见表3-53中的第三列;最后由后工序向前工序逐个计算工序尺寸,并得到各工序尺寸及公差和表面粗糙度。
表3-53 主轴孔各工序的工序尺寸及其公差的计算实例

(2)基准不重合时的工序尺寸确定
基准不重合时的工序尺寸确定,要利用“工艺尺寸换算”方法确定。这时要用工艺尺寸(测量、调整、走刀尺寸)代替原设计尺寸。这种尺寸的代换称“工艺尺寸换算”,其目的是保证原设计要求、便于加工、提高生产率。
① 工艺尺寸链 在工件加工过程中,由有关工序尺寸、设计要求尺寸或加工余量等所组成的尺寸链称为工艺尺寸链。它是由机械加工工艺过程、加工的具体方法所决定的。加工时的装夹方式、表面尺寸形成方法、刀具的形状,都可能影响工艺尺寸链的组合关系,如图3-82(b)和图3-83(b)所示。

图3-82 主油箱Ⅲ、Ⅳ轴孔中心距测量尺寸链
工艺尺寸链的特点如下:
a.封闭性。因尺寸链是封闭的尺寸组合,它是由一个封闭环和若干个组成环构成的封闭图形。它具有封闭性,不封闭就不成为尺寸链。
b.关联性。因尺寸链封闭,所以尺寸链中各环都相互关联。封闭环随所有组成环变动而变动。

图3-83 定位基准与设计基准不重合举例
② 工艺尺寸链的计算 生产实践中常用极值法计算尺寸链。此法是按误差综合最不利的情况,即按组成环出现极值(最大值或最小值)时,来计算封闭环的。此法的优点是简便、可靠;其缺点是当封闭环公差小、组成环数目多时,会使组成环公差过于严格。
极值法常用的基本计算公式见表3-54。
表3-54 极值法常用的基本计算公式


③ 工艺尺寸链的应用(直线尺寸链)
a.测量基准和设计基准不重合。
例:车床主轴箱体Ⅲ轴和Ⅳ轴的中心距为(127±0.07) mm。该尺寸拟用游标卡尺直接测量两孔内侧或外侧母线之间的距离来间接保证。已知Ⅲ轴孔直径为φ90mm,Ⅳ轴孔直径为φ65
mm。现采用外卡测量两孔内侧母线之间的距离。为求得该测量尺寸,需要按尺寸链的计算步骤计算尺寸链(图3-82)。
图中,L0=128±0.07mm;L1=40mm;L2为待求测量尺寸;L3=33
mm。L1、L2、L3为增环;L0为封闭环。
把上述数据带入式(3-1)、式(3-3)、式(3-4)中可得:L2=54mm。只要实测结果在L2公差范围之内,就能够保证Ⅲ轴和Ⅳ轴中心距的设计要求。若实测结果超差,却不一定都是废品。因为直线尺寸链的极值算法考虑的是极限情况下各环之间的尺寸联系。从保证封闭环的尺寸要求来看,这是一种保守算法,计算结果可靠。但是,计算中隐含有假废品问题。如本例中,若两孔直径尺寸都在公差的上限,即尺寸L1=40.002mm,L3=33.015mm,则L2的尺寸变成L2=54-0.087mm,因为此时L1+L2+L3=126.93mm,恰好是中心距设计尺寸的下限尺寸。
生产上为避免假废品的产生,发现实测尺寸超差时,应实测其他组成环的实际尺寸,然后在尺寸链中重新计算封闭环的实际尺寸。若重新计算结果超出封闭环设计的要求范围,便确认为废品,否则为合格品。
产生假废品的根本原因在于测量基准和设计基准不重合。组成环环数愈多,公差范围愈大,出现假废品的可能性愈大。因此,在测量时应尽量使测量基准和设计基准重合。
b.定位基准和设计基准不重合。如图3-83所示,按大批量生产采用调整法加工A、B、C面。工艺安排是前面工序已将A、B面加工,以A面为定位基准加工C面。因C面设计基准是B面,定位基准与设计基准不重合,所以需进行尺寸换算。
尺寸链图如图3-83 (b)所示。在尺寸链中,调整法加工可直接保证的尺寸是L2,L0是封闭环,尺寸间接保证。L1为增环,L2为减环。
在设计尺寸中,L1为未注公差,L2需经计算才能得到。为了保证L0的设计要求,首先将L0的公差分配给L1和L2。这里按等差法进行分配。令L1=L2==0.035mm,则标注L1(或L2)的公差得L1=28
mm。TL0表示L0的公差值。
由式(3-1)、式(3-3)、式(3-4)计算L2的基本尺寸和偏差可得L2=15mm。
加工时,只要保证L1和L2的尺寸都在各自的公差范围之内,就一定能满足L0=13mm的设计要求。
本例中,L1和L2原为未注公差,但由于定位基准和设计基准不重合,产生公差的限制,增加加工的难度。本例若采用试切法,则L0的尺寸可直接得到,不需要求解尺寸链。但同调整法相比,试切法生产率低。
4.时间定额的组成
在一定生产条件下,规定完成一件产品或完成一道工序所消耗的时间,叫时间定额。时间定额的组成见表3-55。
表3-55 时间定额的组成

五、提高劳动生产率的工艺途径
提高劳动生产率的主要工艺途径是采用新工艺、新技术、新材料和加强管理。常见方法如下。
1.缩短基本时间
① 提高切削用量 它是提高生产率的最有效办法。目前广泛采用高速加工,采用硬质合金刀具、陶瓷刀具、人造金刚石刀具等。
② 减小切削行程长度 如多把车刀同时加工工件的砂轮越程槽等,均可使切削行程长度减小。
③ 合并工步 用几把刀具或一把复合刀具对工件的几个不同表面或同一表面同时加工,由于工步的基本时间全部或部分重合,可减少工序的基本时间,如图3-84和图3-85所示即为复合刀具和多刀加工的实例。

图3-84 复合刀具加工实例

图3-85 多刀铣削箱体实例
④ 采用多件加工 机床在一次装夹中同时加工几个工件,使分摊到每个工件上的基本时间和辅助时间大为减少。工件可采用平行、顺序和平行顺序加工,如图3-86所示。

图3-86 顺序多件、平行多件和平行顺序多件加工
2.缩短辅助时间
缩短辅助时间有两种方法,其一是使辅助动作机械化和自动化;其二是使辅助时间与基本时间重合。具体说明见表3-56。
表3-56 缩短辅助时间说明


图3-87 辅助时间与基本时间重合的示例