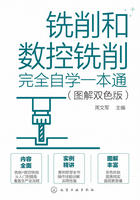
第四节 数控铣刀和刀具系统
一、数控铣常用刀具
根据被加工工件的加工结构、工件材料的热处理状态、加工性能以及加工余量,选择刚性好、寿命长、刀具类型和几何参数适当的刀具,如图3-18所示,是充分发挥数控铣床生产率、获得满意加工质量的前提。

图3-18 常用铣削加工刀具及其加工面
1.数控刀具材料的性能及应用范围
刀具材料是决定刀具切削性能的根本因素,对于加工质量、加工效率、加工成本以及刀具寿命都有着重大的影响。要实现高效合理的切削,必须有与之相适应的刀具材料。数控刀具材料是较活跃的材料科技领域。近年来,数控刀具材料基础科研和新产品的成果集中应用在高速、超高速、硬质(含耐热、难加工)、干式、精细、超精细数控加工领域。刀具材料新产品的研发在超硬材料(如金刚石、Al2O3、Si3N4基类陶瓷、TiC基类金属陶瓷、立方氮化硼、表面涂层材料),W、Co类涂层和细晶粒(超细晶粒)硬质合金体及含Co类粉末冶金高速钢等领域进展速度较快。尤其是超硬刀具材料的应用,导致产生了许多新的切削理念,如高速切削、硬切削、干切削等。
数控刀具的材料主要有高速钢、硬质合金、陶瓷、立方氮化硼和金刚石五类,其性能和应用范围见表3-14。目前数控机床用得最普遍的刀具是硬质合金刀具。
表3-14 数控刀具材料的性能及应用范围

2.数控铣削对刀具的要求
(1)刀具性能方面
数控加工具有高速、高效和自动化程度高等特点,数控刀具是实现数控加工的关键技术之一。为了适应数控加工技术的需要,保证优质、高效地完成数控加工任务,对数控加工刀具材料提出了比传统的加工用刀具材料更高的要求,它不仅要求刀具耐磨损、寿命长、可靠性好、精度高、刚性好,而且要求刀具尺寸稳定、安装调整方便。数控加工对刀具提出的具体要求见表3-15。
表3-15 数控加工对刀具提出的具体要求


(2)刀具材料方面
刀具材料的选择对刀具寿命、加工效率、加工质量和加工成本等的影响很大。刀具切削时要承受高压、高温、摩擦、冲击和振动等作用,因此,刀具材料应具备如下一些基本性能,见表3-16。
表3-16 刀具材料基本性能

3.数控铣削刀具的选用原则
铣刀的选择是数控铣削加工工艺中的重要内容之一,它不仅影响数控铣床的加工效率,而且直接影响加工质量。另外,数控铣床主轴转速比普通铣床高,且主轴输出功率大,因此与传统加工方法相比,数控铣削加工对刀具不仅要求精度高、强度大、刚性好、寿命长,而且要求尺寸稳定、安装调整方便。这就要求采用新型优质材料来制造数控加工刀具,并合理选择刀具结构、几何参数,以满足数控加工的需要。
刀具的选用应考虑工件材质、加工轮廓类型、机床允许的切削用量和刚性以及刀具使用寿命等因素。选用的一般原则如下:
① 应优先选择通用的标准化刀具,特别是硬质合金可转位刀具。
② 为了提高刀具的使用寿命和可靠性,应尽量选用由各种高性能、高效率、长寿命的刀具材料制成的刀具,例如使用各种超硬材料刀具、硬质合金刀具、涂层刀具、陶瓷刀具、CBN刀具等。
③ 为了集中工序,提高生产效率及保证加工精度,应尽可能采用复合刀具。其中,以孔加工复合刀具的使用最为普遍。
④ 应尽量采用各种高效刀具,例如可转位钻头、四刃钻、硬质合金单刃铰刀、波形刃立铣刀、可转位螺旋齿立铣刀(玉米铣刀、模数铣刀和热管式刀具等)。
⑤ 应尽量使用不重磨可转位刀片,少用焊接式刀片,以减少刀具磨损后的更换和预调时间。
4.常用铣刀的种类
(1)面铣刀
面铣刀主要用于加工平面、台阶面等。面铣刀的主切削刃分布在铣刀的圆柱面上或圆锥面上,副切削刃分布在铣刀的端面上。面铣刀按结构可分为整体式面铣刀、硬质合金整体焊接式面铣刀、硬质合金机夹焊接式面铣刀、硬质合金可转位式面铣刀等形式,其说明见表3-17。
表3-17 面铣刀种类及说明


图3-19 整体式面铣刀

图3-20 硬质合金整体焊接式面铣刀

图3-21 硬质合金机夹焊接式面铣刀

图3-22 硬质合金可转位式面铣刀
(2)立铣刀
立铣刀是数控机床上用得最多的一种铣刀,立铣刀圆柱表面和端面上都有切削刃,它们可同时进行切削,也可单独进行切削。立铣刀能够完成的加工内容包括圆周铣削和轮廓加工,槽和键槽铣削,开放式和封闭式型腔、小面积的表面加工,薄壁的表面加工,平底沉头孔、孔面加工,倒角及修边等。
如图3-23所示为整体式立铣刀,材料有高速钢和硬质合金两种,底部有圆角、斜角和尖角等几种形式。该立铣刀的主切削刃分布在铣刀的圆柱面上,副切削刃分布在铣刀的端面上。主切削刃一般为螺旋齿,以增加切削平稳性,提高加工精度。由于普通立铣刀端面中心处无切削刃,所以立铣刀不能做轴向进给,端面刃主要用来加工与侧面相垂直的底平面。

图3-23 整体式立铣刀
为了能加工较深的沟槽,并保证有足够的备磨量,立铣刀的轴向长度一般较长。为改善切屑卷曲情况,增大容屑空间,防止切屑堵塞,立铣刀刀齿数比较少,容屑槽圆弧半径则较大。整体式立铣刀有粗齿和细齿之分,粗齿齿数3~6个,适用于粗加工;细齿齿数5~10个,适用于半精加工。柄部有直柄、莫氏锥柄、7∶24锥柄等多种形式。整体式立铣刀应用较广,但切削效率较低。
如图3-24所示为硬质合金可转位式立铣刀,其基本结构与高速钢立铣刀相差不多,但切削效率大大提高,是高速钢立铣刀的2~4倍,适用于数控铣床、加工中心的切削加工。

图3-24 硬质合金可转位式立铣刀
(3)模具铣刀
模具铣刀由立铣刀发展而成,可分为圆锥形立铣刀(圆锥半角α/2=3°、5°、7°、10°)、圆柱形球头立铣刀和圆锥形球头立铣刀三种;其柄部有直柄、削平型直柄和莫氏锥柄。它的结构特点是球头或端面上布满了切削刃,圆周刃与球头刃圆弧连接,可以做径向的轴向进给。铣刀工作部分用高速钢或硬质合金制造。国家标准规定直径d=4~63mm。如图3-25所示为高速钢制造的模具铣刀;如图3-26所示为用硬质合金制造的模具铣刀。小规格的硬质合金模具铣刀多制成整体结构;φ16mm以上直径的,制成焊接或机夹可转位刀片结构。

图3-25 高速钢模具铣刀

图3-26 硬质合金模具铣刀
(4)键槽铣刀
键槽铣刀如图3-27所示。它有两个刀齿;圆柱面和端面都有切削刃;端面刃延至中心,既像立铣刀,又像钻头。加工时先轴向进给达到槽深,然后沿键槽方向铣出键槽全长。

图3-27 键槽铣刀
按国家标准规定,直柄键槽铣刀直径d=2~22mm;锥柄键槽铣刀直径d=14~50mm。键槽铣刀直径的偏差有e8和d8两种。键槽铣刀的圆周切削刃仅在靠近端面的一小段长度内发生磨损,重磨时,只需刃磨端面切削刃,因此重磨后铣刀直径不变。
(5)鼓形铣刀
如图3-28所示为一种典型的鼓形铣刀。它的切削刃分布在半径为R的圆弧面上,端面无切削刃。加工时控制刀具上下位置,相应改变刀刃的切削部位,可以在工件上切出从负到正的不同斜角。R越小,鼓形刀所能加工的斜角范围越广,但所获得的表面质量也越差。这种刀具的特点是刃磨困难,切削条件差,而且不适用于加工有底的轮廓表面。

图3-28 鼓形铣刀
(6)成形铣刀
成形铣刀一般是为特定形状的工件或加工内容,例如渐开线齿面、燕尾槽和T形槽等专门设计制造的。几种常用的成形铣刀如图3-29所示。

图3-29 几种常用的成形铣刀
除了上述几种类型的铣刀外,数控铣床也可使用各种通用铣刀,但因不少数控铣床的主轴内有特殊的拉刀装置,或因主轴内锥孔有别,需配过渡套和拉钉。
5.常用孔加工刀具
(1)钻孔刀具(其结构见表3-18)
表3-18 钻孔刀具的结构


图3-30 麻花钻的构成

图3-31 外排屑深孔钻

图3-32 内排屑深孔钻

图3-33 扩孔钻

图3-34 中心钻

图3-35 定心钻
(2)镗刀
在机床上用镗刀对大、中型孔进行半精加工和精加工称为镗孔。镗孔的尺寸精度一般可达IT7~IT10。镗刀种类很多,按切削刃数量可分为单刃镗刀和双刃镗刀,结构见表3-19。
表3-19 镗刀结构


图3-36 单刃镗刀

图3-37 微调镗刀

图3-38 双刃镗刀
(3)铰刀
铰孔是用铰刀对孔进行精加工的方法。铰孔往往作为中小孔钻、扩后的精加工,也可用于磨孔或研孔前的预加工。铰孔只能提高孔的尺寸精度和形状精度,减小其表面粗糙度值,不能提高孔的位置精度,也不能纠正孔的轴线歪斜。一般铰孔的尺寸精度可达IT7~IT9,表面粗糙度Ra值可达1.6~0.8μm。
铰孔质量除与正确选择铰削用量、冷却润滑液有关外,铰刀的选择也至关重要。在加工中心上铰孔时,除使用普通标准铰刀外,还常采用机夹硬质合金刀片单刃铰刀和浮动铰刀等,见表3-20。
表3-20 铰刀种类及说明


图3-39 普通标准铰刀
表3-21 铰刀齿数


图3-40 机夹硬质合金刀片单刃铰刀
1, 7—螺钉;2—导向块;3—刀片;4—楔套;5—刀体;6—销

图3-41 浮动铰刀
(4)锪刀
锪刀主要用于各种材料的锪台阶孔、锪平面、孔口倒角等工序,常用的锪刀有平底型、锥型及复合型等。
(5)机用丝锥
机用丝锥主要用于加工M6~M20的螺纹孔。从原理上讲,丝锥就是将外螺纹做成刀具。
(6)螺纹铣刀
螺纹铣刀有圆柱螺纹铣刀、机夹螺纹铣刀及组合式多工位专用螺纹镗铣刀等形式。
① 圆柱螺纹铣刀的螺纹切削刃与丝锥不同,刀具上无螺旋升程,加工中的螺旋升程靠机床运动实现。由于这种特殊结构,该刀具既可加工右旋螺纹,也可加工左旋螺纹,但不适用于较大螺距螺纹的加工。
② 机夹螺纹铣刀适用于较大直径(如D>25mm)螺纹的加工。其特点是刀片易于制造,价格较低,有的螺纹刀片可双面切削,但抗冲击性能较整体螺纹铣刀稍差。因此,该刀具常用于加工铝合金材料。
③ 组合式多工位专用螺纹镗铣刀的特点是一刀多刃,一次完成多工位加工,可节省换刀等辅助时间,显著提高生产率。
螺纹铣削的优点:
① 一把螺纹铣刀可加工具有相同螺距的任意直径螺纹,既可加工右旋螺纹,也可加工左旋螺纹,螺纹铣削可以避免采购大量不同类型和规格的丝锥。
② 加工中产生的切屑是短切屑,因此不存在切屑处理方面的问题。
③ 刀具破损的部分可以很容易地从零件中去除。
④ 不受加工材料限制,那些无法用传统方法加工的材料可以用螺纹铣刀进行加工。
⑤ 采用螺纹铣刀,可以按所需公差要求加工,螺纹尺寸是由加工循环控制的。
⑥ 与丝锥攻螺纹相比,螺纹铣削可以采用更高的切削速度和进给量,极大地提高了生产率。
6.对刀及对刀点和换刀点的确定
(1)对刀点和换刀点的确定
对刀点和换刀点的确定,是数控加工工艺分析的重要内容之一。对刀点是在数控机床上加工工件时,刀具相对工件运动的起点。由于程序也从该点开始执行,所以对刀点又称为起刀点或程序起点。对刀点选定后,即确定了机床坐标系与工件坐标系之间的相互位置关系。
进行数控加工编程时,刀具在机床上的位置由刀位点的位置来表示。刀位点是刀具上代表刀具位置的参照点。不同的刀具,刀位点不同。车刀、镗刀的刀位点是指其刀尖,立铣刀、面铣刀的刀位点是刀具底面与刀具轴线的交点,球头铣刀的刀位点是指球头铣刀的球心。所谓对刀,是指加工开始前,将刀具移动到指定的对刀点上,使刀具的刀位点与对刀点重合。
对刀点的选定原则如下:
① 便于数学处理和编制程序。
② 容易在机床上找正。
③ 加工过程中检查方便、可靠。
④ 引起的加工误差小。
对刀点可以设置在被加工工件上,也可以设置在夹具上,但必须与工件的定位基准有一定的坐标尺寸联系,这样才能确定机床坐标系与工件坐标系的相互关系。为了提高工件的加工精度,对刀点应尽量选在工件的设计基准或工艺基准上。对于以孔定位的工件,可以取孔的中心作为对刀点。车削加工则通常将对刀点设在工件外端面的中心上。当工件上没有合适的部位用来对刀时,也可以以加工出的工艺孔来对刀。成批生产时,为减少多次对刀带来的误差,常将对刀点作为程序的起点,同时也作为程序的终点。
换刀点则是指加工过程中需要换刀时刀具的相对位置点。对数控车床、数控铣床、加工中心等多刀加工数控机床,加工过程中需要进行换刀,故编程时应考虑设置一个换刀位置(即换刀点)。换刀点往往设在工件的外部,以能顺利换刀、不碰撞工件及机床上其他部件为原则。如在铣床上,常以机床参考点为换刀点;在加工中心上,以换刀机械手的固定位置点为换刀点;在车床上则以刀架远离工件的行程极限点为换刀点。选取的这些点,都是便于计算的相对固定点。
(2)对刀方法
对刀的准确程度将直接影响加工精度。因此,对刀操作一定要仔细,对刀方法应同零件加工精度要求相适应,生产中常使用百分表、寻边器和对刀仪对刀。
数控铣削加工常用的对刀方法见表3-22。
表3-22 数控铣削加工常用的对刀方法

二、典型刀具系统的种类
1.整体式刀具系统
整体式刀具系统如图3-42所示,它是把刀柄和工作头做成一体,使用时刀柄直接夹住刀具,根据不同刀具选用不同品种和规格的刀柄。这种刀柄的优点是刚性好、使用方便可靠,缺点是规格品种多,给生产和管理带来不便。

图3-42 整体式刀具系统
我国为满足工业发展的需要,制定了“镗铣类整体数控工具系统”标准(简称为TSG工具系统),TSG工具系统如图3-43所示。

图3-43 镗铣数控机床工具系统
整体式刀具系统工具锥柄代号由四部分组成,各部分意义如下:

例如:JT-45-Q32-120
JT—表示工具柄型代号。
45—对圆锥柄表示锥度规格。
Q32—表示工具的规格。
120—表示刀柄的工作长度。
它所表示的工具为:自动换刀机床用7∶4圆锥工具柄(GB/T 10944),锥柄为45号,前部为弹簧夹,最大夹持直径32mm,刀柄工作长度(锥柄大端直径φ57.15mm处到弹簧夹头前端面的距离)为120mm。工具柄部型式代号见表3-23。工具的用途代号及规格参数见表3-24。
表3-23 工具柄部型式代号

表3-24 工具的用途代号及规格参数

2.模块式刀具系统
模块式刀具系统(TMG)是将整体式刀杆分解成柄部(主柄)、中间连接块(连接杆)、工作部(工作头)三个主要模块(部分),然后通过各种连接结构,在保证刀杆连接精度、刚性的前提之下,将三模块连接成一个整体,如图3-44所示。使用者可以根据所加工零件的尺寸、精度要求及工艺要求来组合这三模块。模块工具刀柄克服了整体式工具刀柄功能单一、加工尺寸变动不便的不足,具有灵活、快速、经济可靠的优点。

图3-44 模块式刀具系统
模块式刀具系统各模块型号内容及表示方式说明如下:


工作头有弹簧夹头、莫氏锥孔、钻夹头、铰刀、立铣刀、面铣刀、镗刀等多种,可根据不同的工艺要求,选用不同功能和规格的工作头。