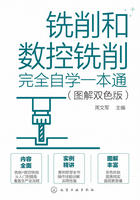
第一节 铣削用量的选择
一、铣削的基本运动与铣削用量
1.基本运动
铣削是利用铣刀旋转、工件相对铣刀做进给运动来进行切削的。铣削过程中包括两个运动:主运动和进给运动。
① 主运动。是指由机床或人力提供的主要运动,它使刀具和工件之间产生相对运动,从而使刀具前刀面接近工件。铣削是以铣刀旋转为主运动,它能使刀具从工件上切除多余的部分。
② 进给运动。是指由机床或人力提供的附加运动,它使刀具和工件之间产生附加的相对运动,加上主运动,即可不断地或连续地切除金属,并得到所需几何特征的已加工表面。铣削是经工件相对铣刀的移动为进给运动的。它有两种形式,一种是断续进给运动,另一种是连续进给运动。
2.铣削用量的内容
在铣削过程中,所选用的切削用量,称为铣削用量。铣削用量包括铣削速度、吃刀量和进给速度,其说明见表3-1。
表3-1 铣削用量


由上述可知,铣刀的轴线所处的位置不同,背吃刀量和侧吃刀量的测量方向是不同的。
二、确定铣削用量的原则
粗加工时,在机床动力和工艺系统刚性允许的前提下,以及具有合理的铣刀寿命的条件下,首先应选用较大的被切金属层的宽度,其次是选用较大的被切金属层的深度(厚度),再选用较大的每齿进给量,最后根据铣刀的寿命确定铣削速度。
精加工时,为了保证获得合乎要求的加工精度和表面粗糙度,被切金属层应尽量一次铣出;被切金属的深度一般在0.5mm左右;再根据表面粗糙度要求,选择合适的进给量;然后确定合理的铣刀寿命和铣削速度。
三、被切金属层深度(厚度)的选择
面铣时的背吃刀量ap、周铣时的侧吃刀量ae,即是被切金属层的深度。当铣床功率和工艺系统的刚性、强度允许,且加工精度要求不高及加工余量不大时,可一次进给铣去全部余量。当加工精度要求较高或加工表面粗糙度Ra小于6.3μm时,铣削应分粗铣和精铣。端面铣削时,铣削深度的推荐值见表3-2。当工件材料的硬度和强度较高时,应取较小值。当加工余量较大时,可采用阶梯铣削法。
表3-2 端面铣削时背吃刀量ap的推荐值

周铣时的侧吃刀量ae,粗铣时可比端面铣削时的背吃刀量ap大。故在铣床和工艺系统的刚性、强度允许的条件下,尽量在一次进给中,把粗铣余量全部切除。精铣时,可参照端面铣削时的ap值。
阶梯铣削法用的阶梯铣刀如图3-1所示,它的刀齿分布在不同的半径上,而且各齿在轴向伸出的距离也各不相同。半径愈大的刀齿在轴向伸出的距离愈小,即后刀齿的位置比前刀齿在半径上小ΔR的距离。而在轴向,则比前刀齿多伸出Δap的距离。能使工件的全部加工余量沿铣削深度方向分配到各齿上。若采用图3-1(b)所示的由两组刀齿组成的铣刀铣削时,由于一组有三个刀齿,故每齿的进给量和切削厚度增大3倍,而切削宽度则减小,切出窄而厚的切屑。用阶梯铣削法既降低了铣削力,又有利于排除切屑,故可减少振动和功率消耗。

图3-1 阶梯铣刀和阶梯铣削
另外,阶梯铣刀的刀齿在排列时,把最后一个刀齿(如图3-1所示中是刀齿Ⅲ)在轴向安装得比前一刀齿只伸出0.5mm左右,刀齿的几何参数符合精加工要求。此时的阶梯铣削,可使粗铣和精铣在一次进给中完成,以提高生产效率。此法也可用于普通面铣刀上。
四、铣削用量的选用
1.选择铣削用量的原则
合理的选择铣削用量直接关系到铣削效果的好坏,即影响到能否达到高效、低耗及优质的加工效果,选择铣削用量应满足如下基本要求:
① 保证铣刀有合理的使用寿命,提高生产率和降低生产成本。
② 保证铣削加工质量,主要是保证铣削加工表面的精度和表面粗糙度达到图样要求。
③ 不超过铣床允许的动力和转矩,不超过铣削加工工艺系统(刀具、工具、机床)的刚度和强度,同时又充分发挥它们的潜力。
上述三项基本要求,选择时应根据粗、精加工具体情况有所侧重。一般在粗铣加工时,应尽可能发挥铣刀、铣床的潜力和保证合理的铣刀使用寿命;精铣加工时,则首先要保证铣削加工精度和表面粗糙度,同时兼顾合理的铣刀寿命。
2.铣削用量的选择顺序
① 要选用较大的背吃刀量。
② 要选用较大的每齿进给量。
③ 要选用适宜的主轴转速。
3.铣削用量的合理选用
在铣削过程中,如果能在一定的时间内切除较多的金属,就有较高的生产率。显然,增大吃刀量、铣削速度和进给量,都能增加金属切除量。但是,影响刀具寿命最显著的因素是铣削速度,其次是进给量,而吃刀量对刀具的影响最小。所以,为了保证必要的刀具寿命,应当优先采用较大的吃刀量,其次是选择较大的进给量,最后才是根据刀具的寿命要求,选择适宜的铣削速度。
粗铣时,进给量的提高主要是受力齿强度及机床、夹具等工艺系统刚性的限制。铣削用量大时,还受机床功率的限制。因此在上述条件下,可尽量取得大些。
精铣时,限制进给量的主要因素是加工精度和表面粗糙度。每齿进给量越大,表面粗糙度值也越大。在表面粗糙度要求较小时,还要考虑到铣刀刀齿的刀刃或刀尖不一定在同一个旋转的圆周或平面上,在这种情况下铣出的平面,将以铣刀一转为一个波纹。因此,精铣时,在考虑每齿进给量的同时,还需考虑每转进给量。
表3-3推荐的数值为各种常用铣刀在对不同工件材料铣削时的每齿进给量,粗铣时取表中的较大值;精铣时取表中的较小值。
表3-3 每齿进给量fz值的选取 单位:mm

五、铣削速度的选择
合理的铣削速度是在保证加工质量和铣刀寿命的条件下确定的。铣削时影响铣削速度的主要因素有刀具材料的性质和刀具的寿命、工件材料的性质、加工条件及切削液的使用情况等。
1.粗铣时铣削速度的选择
粗铣时,由于金属切除量大,产生的热量多,切削温度高,为了保证合理的铣刀寿命,铣削速度要比精铣时低一些。在铣削不锈钢等韧性和强度高的材料,以及其他一些硬度和热强度等性能高的材料时,产生的热量更多,则铣削速度应降低。另外,粗铣时由于铣削力大,故还需考虑机床功率是否足够,必要时可适当降低铣削速度,以减小铣削功率。
2.精铣时铣削速度的选择
精铣时,由于金属切除量小,所以在一般情况下,可采用比粗铣时高一些的铣削速度。提高铣削速度的同时,又将使铣刀的磨损速度加快,从而影响加工精度。因此,精铣时限制铣削速度的主要因素是加工精度和铣刀寿命。有时为了达到上述两个目的,采用比粗铣时还要低的铣削速度,即低速铣削。尤其在铣削加工面积大的工件,即一次铣削宽而长的加工面时,采用低速制,可使刀刃和刀尖的磨损量极小,从而获得高的加工精度。
表3-4推荐的数值是一般情况下的铣削速度,在实际工作中需按实际情况加以修改。
表3-4 粗铣时的铣削速度
