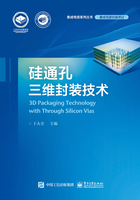
2.4 Via-last技术
Via-last技术集成方案中的TSV是芯片制造工艺完成之后进行的,可以从圆片背面加工TSV,也可从圆片正面加工TSV。目前产业界量产的主要是从圆片背面加工TSV,与正面焊盘直接形成电互连通道。最典型的产品应用是CMOS图像传感器(CMOS Image Sensor,CIS)产品。图2-8所示的是一种典型的从圆片背面加工TSV的Via-last技术集成方案。主要流程:①由制造厂加工CMOS器件及多层互连线之后,做必要正面工艺(根据需要可加工用于钎焊的金属焊盘或者微凸点);②借助承载圆片的保护,对衬底进行减薄;③在背面刻蚀深孔;④沉积绝缘层并填充导电材料,获得TSV;⑤在背面加工互连层及凸点,形成有效互连;⑥拆掉承载圆片,用于后续操作。针对CIS应用,承载圆片一般使用透光的玻璃衬底,最终不需要拆除,在圆片背面加工TSV、金属再布线层(Redistribution Layer,RDL)、钝化层和焊球,实现3D圆片级封装集成。

图2-8 从圆片背面加工TSV的Via-last技术集成方案
从圆片背面加工的TSV可以完全填充,如图2-9所示。这种完全填充型适合密度较高的TSV加工。TSV也可部分填充,仅在侧壁覆盖一层金属,典型填充效果如图2-10所示。部分填充TSV技术适用于对密度要求不高的场合,如CIS产品等[47]。

图2-9 完全填充型Via-last TSV

图2-10 部分填充型Via-last TSV
采用圆片-圆片异质键合后将键合的上层圆片减薄,再利用Via-last技术,将键合界面的圆片金属层连接到圆片背部引出,是实现超细节距互连的一个重要方案。IMEC在2017年就实现了1.4μm节距的圆片异质键合[48]。为了进一步实现高密度3D互连,2019年,IMEC研究出了1.4μm超细节距的Via-last技术[49]。在该工艺中,圆片-圆片异质键合后,上层圆片要减薄到5μm,然后在涂胶、光刻后进行干法刻蚀,其光刻胶选用厚度为2μm的正性深紫外胶(Fujifilm KrF DUV)。如图2-11所示,刻蚀后,实际TSV在顶部介质硬掩模下是0.85μm,在TSV中部直径减小到0.70μm,在孔底部直径为0.65μm。高保型原子层沉积TiN介质层嵌入氧化介质层中,用来阻挡刻蚀底部金属铜时,铜二次沉积到孔侧壁氧化层后扩散,同时保护底部介质层刻蚀开窗时侧壁氧化层不被攻击。为降低成本,分别采用传统的物理气相沉积钽和铜作为阻挡层和种子层。利用30nm碱性电镀种子层增强剂来修复不连续铜种子层,获得了无孔隙电镀铜填充。通过开尔文和菊花链测试结构对TSV进行测试,良率达100%。采用可控的I-V测试方法研究了TSV介质层的可靠性,结果证实,微缩的0.7μm×5μm TSV具有高击穿电压、高可靠性。

图2-11 铜填充0.7μm×5μm TSV的投射电镜图片
还有一些研究机构采用从正面加工Via-last型TSV,典型工艺流程如图2-12所示[50]。首先在完成正面工艺的衬底正面依次刻蚀钝化层、介质层和硅衬底,获得TSV深孔;然后进行填充和平坦化,获得盲孔TSV;接着刻蚀钝化层并在正面加工一层再布线层,实现TSV正面与电路的连接;再借助承载圆片的支撑,对衬底进行减薄,实现TSV背面露头,并在背面加工再布线层和焊盘;接下来在背面键合第二张承载圆片,将正面的承载圆片去除,并在正面加工微凸点,完成衬底加工;最后该芯片可以进行正面堆叠芯片的焊接。

图2-12 从正面加工Via-last型TSV的典型工艺流程