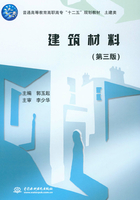
4.1 硅酸盐水泥
凡由硅酸盐水泥熟料、0~5%的石灰石或粒化高炉矿渣、适量石膏磨细制成的水硬性胶凝材料,称硅酸盐水泥。硅酸盐水泥分为两种类型,不掺加混合材料的称为Ⅰ型硅酸盐水泥,代号P·Ⅰ;在硅酸盐水泥熟料粉磨时掺加不超过水泥质量5%的石灰石或粒化高炉矿渣的称为Ⅱ型硅酸盐水泥,代号P·Ⅱ。
4.1.1 硅酸盐水泥的生产工艺
1.硅酸盐水泥的原料及化学成分
生产硅酸盐水泥的原料主要是石灰质原料和黏土质原料两类。石灰质原料(如石灰石、白垩、石灰质凝灰岩等)提供CaO;黏土质原料(如黏土、页岩、黄土等)提供SiO2、Al2O3及少量Fe2O3。当以上两种原料提供的化学组成不能满足要求时,还要加入少量校正原料(黄铁矿渣、铁矾土废料及石英矿、硅藻土等)进行调整。
硅酸盐水泥生产原料的化学组成见表4.1。
表4.1 硅酸盐水泥生产原料的化学组成

2.硅酸盐水泥的生产工艺
水泥生产过程可概括为“两磨一烧”,其工艺流程如图4.1所示。
图4.1 硅酸盐水泥生产工艺流程
水泥生料的配比不同,硅酸盐水泥熟料的矿物比例和技术性质也就不同。
水泥生产的关键环节是煅烧,水泥熟料的各种矿物成分都是在这一过程中形成的。生料在窑内的煅烧过程要经历干燥、预热、分解、熟料烧成及冷却等几个阶段。在不同的阶段其反应大致如下:
100~200℃ 生料被加热,水分逐渐蒸发而干燥。
300~500℃ 生料被预热。
500~800℃ 黏土质原料脱水并分解为无定形Al2O3和SiO2。
600℃以后 石灰质原料中的CaCO3开始分解成CaO和CO2。
800℃左右 生成铝酸一钙;也有铁酸一钙和硅酸二钙开始生成。
900~1000℃ 铝酸三钙和铁铝酸四钙开始生成,所有的CaCO3分解完毕。
1100~1200℃ 大量生成铝酸三钙和铁铝酸四钙,硅酸二钙生成量达最大。
1300~1450℃ 铝酸三钙和铁铝酸四钙呈熔融状态,产生的液相把CaO及部分硅酸二钙溶解于其中,在此液相中,硅酸二钙吸收CaO化合成硅酸三钙。这一过程是煅烧水泥的关键,必须有足够的时间和温度,使水泥熟料中游离氧化钙的含量减少,以保证质量。
4.1.2 硅酸盐水泥熟料的矿物组成及其特性
1.硅酸盐水泥熟料的矿物组成
硅酸盐水泥熟料的主要矿物组成及其含量见表4.2。
除上述四种主要矿物组成外,还有少量的游离氧化钙(f-CaO)、氧化镁(f-MgO)、三氧化硫(SO3)和碱(K2O、Na2O)等,其总含量一般不超过水泥质量的10%,它们对水泥的性能都会产生不利影响。
表4.2 硅酸盐水泥熟料的主要矿物组成及其含量

在生产水泥时,熟料中还掺入3%~5%石膏(CaSO4·2H2O)共同磨细,其目的是为了调节水泥的凝结时间。
2.硅酸盐水泥熟料的矿物特性
硅酸盐水泥的性能是由其组成矿物的性能决定的,因此,要了解水泥的性质就必须了解每种矿物的特性。从应用角度考虑,对水泥性能的要求有水化硬化速度、强度、水化热多少、干缩大小及耐腐蚀性等。硅酸盐水泥熟料中各种矿物特性见表4.3。
表4.3 硅酸盐水泥熟料矿物特性

从表4.3中可以看出,硅酸盐水泥中各种熟料矿物特性不同,改变熟料中的矿物组成比例关系时,可制成不同性质的水泥。如适当提高水泥中的C3S的含量,可制成高强水泥,用于高强度混凝土工程;提高C3S和C3A的含量,可制成快硬高强水泥,用于抢修工程;降低C3S和C3A的含量,适当提高C2S的含量,可制成中、低热的大坝水泥,可用于大体积混凝土工程。
4.1.3 硅酸盐水泥的水化、凝结硬化及其影响因素
水泥加入适量的水调成水泥浆后发生化学变化,生成多种水化物的过程,称之为“水化”。水泥加水拌和的初期是具有一定流动性和可塑性的浆体,经自身的物理和化学变化后,逐渐变稠失去塑性,但尚无强度,这一过程称之为“凝结”。随着水化反应的不断进行,产生强度,并逐渐发展成坚硬的水泥石,这一过程称之为“硬化”。水泥的水化、凝结硬化是一个连续的、复杂的物理、化学变化过程。
1.硅酸盐水泥的水化
硅酸盐水泥加水后,其熟料的各种矿物很快与水发生水化反应,生成各种水化物,并放出一定的热量。其反应式为
在水泥中掺入少量石膏,与水化铝酸三钙化合,生成高硫型水化硫铝酸钙晶体(俗称钙钒石)。
生成的水化硫铝酸钙难溶于水,沉积在水泥颗粒表面,阻碍水泥颗粒与水接触,使水泥水化延缓,达到调节水泥凝结时间的目的。随着水化的进行,当石膏耗尽后,钙钒石继续与水化铝酸三钙反应,生成低硫型水化硫铝酸钙(3CaO·Al2O3·CaSO4·12H2O)晶体。
综上所述,硅酸盐水泥水化后,生成的水化物有水化硅酸钙和水化铁酸钙凝胶体、氢氧化钙、水化铝酸钙和水化硫铝酸钙晶体。当水泥完全水化时,水化硅酸钙约占70%,氢氧化钙约占20%。
2.水泥的凝结硬化
水泥的凝结硬化是一个连续复杂的物理、化学变化过程。学者们对水泥凝结硬化机理进行了大量的试验研究,归纳简述如下:
(1)水泥加入少量拌和水以后,水泥颗粒表面开始与水化合,生成水化物,其中结晶体溶解于水中,胶体以极细小的质点悬浮于水中。同时由于水泥颗粒存在着微裂缝和缺陷,水分渗透到水泥颗粒内部,产生物理分散作用,剥落成小块儿进入液相,暴露出水泥颗粒新的表面,再继续水化。由于水化、溶解、再水化、再溶解,使水泥颗粒周围的溶液很快成为水化产物的过饱和溶液。
(2)溶液达到饱和后,水化硅酸钙从溶液中析出形成胶体,胶体的质点凝聚成凝胶,堆积在水泥颗粒周围,水泥继续水化不通过溶解过程,而直接发生固相反应生成水化物凝胶体。水化继续进行,新生水化物增多,自由水分减少,凝胶体变稠,有凝胶体包裹的水泥颗粒,借助范德华力(表面吸附作用)凝结成多孔的空间网络,形成凝聚结构。这种结构在振动的作用下可以破坏,凝聚结构形成的同时,水泥浆发生凝结,开始失去塑性,也就是水泥的初凝,但这时还没有强度。
(3)随着以上过程的不断进行,固相不断增多,液相不断减少,结晶连生体不断增大,凝胶和结晶体互相贯穿,新生水化物不断填充凝聚结构的空隙,使结构逐渐紧密,最终达到水泥浆完全失去塑性,即水泥表现为终凝,开始硬化,这个阶段称为凝结期。
(4)继续水化形成的凝胶体,进一步填充水泥颗粒间的毛细孔,由于水化和蒸发,使自由水分不断减少,使浆体逐渐产生强度而进入硬化阶段。
水泥的水化、凝结硬化过程如图4.2所示。
图4.2 水泥的水化、凝结硬化过程示意图
1—未水化水泥颗粒;2—水泥凝胶;3—氢氧化钙和含水铝酸钙结晶;4—毛细管孔隙
在水泥的水化、凝结硬化过程中,各阶段是互相交错进行的,而且以水泥颗粒表面开始,逐渐向水泥颗粒的内核深入进行。开始时水化速度加快,水泥的强度增长快,但由于水泥水化不断进行,堆积在水泥颗粒周围的水化物不断增多,阻碍水和水泥未水化部分的接触,水化减慢,强度增长也逐渐减缓。但无论时间多久,水泥颗粒的内核很难完全水化。试验证明,只要保持环境潮湿,水泥石的强度在几十年以后仍能增长。
由于熟料矿物在水泥石强度发展过程中所起的作用,可以认为硅酸三钙在最初4个星期以内对水泥石强度起着决定作用;硅酸二钙在4个星期以后才发挥其强度作用,大约经过1年,与硅酸三钙对水泥石发挥相等的作用;铝酸三钙在1~3d或稍长的时间内,对水泥石强度起着有益作用,但以后可使水泥石强度降低。对铁铝酸四钙在水泥水化时所起的作用,认识还存在分歧,多数人认为由于水化铁酸一钙胶体在铁铝酸四钙周围析出形成薄膜,因而延缓了水泥的水化进程。
3.影响水泥凝结硬化的主要因素
水泥的凝结硬化过程,也是水泥强度发展的过程。为了正确使用水泥,并在使用中采取有效措施改善水泥的性能,必须了解影响水泥凝结硬化的因素。影响水泥凝结硬化的因素主要有以下八个方面:
(1)矿物组成。不同矿物成分和水起反应时所表现出来的特点是不同的,如C3A水化速率最快,放热量最大而强度不高;C2S水化速率最慢,放热量最少,早期强度低,后期强度增长迅速等。因此,改变水泥的矿物组成,其凝结硬化情况将产生明显变化。水泥的矿物组成比例是影响水泥凝结硬化的最重要的因素。
(2)石膏掺量。石膏起缓凝作用的机理可解释为:水泥水化时,石膏能很快与铝酸三钙作用生成水化硫铝酸钙(钙钒石),钙钒石很难溶解于水,它吸附在水泥颗粒表面形成保护膜,从而阻碍了铝酸三钙的水化反应,控制了水泥的水化反应速度,延缓了凝结时间。石膏掺量少,起不到缓凝的作用,掺量过多,其自身凝结快,适得其反。
(3)水泥的细度。在矿物组成相同的条件下,水泥磨得越细,水泥颗粒平均粒径小,比表面积大,水化时与水的接触面大,水化速度快,相应地水泥凝结硬化速度就越快,早期强度就越高。
(4)水泥浆的稠度(水胶比)。水泥浆的水胶比是指水泥浆中水与水泥等所有胶凝材料的质量之比。当水泥浆中加水较多时,水胶比较大,此时水泥的初期水化反应得以充分进行;但是水泥颗粒间被水隔开的距离较远,颗粒间相互连接形成骨架结构所需的凝结时间长,所以水泥浆凝结较慢。水泥浆的水胶比较大时,多余的水分蒸发后形成的孔隙较多,造成水泥石的强度较低,因此水泥浆的水胶比过大时,会明显降低水泥石的强度。
(5)环境温度和湿度。在适当温度条件下,水泥的水化、凝结硬化速度较快。温度越高,水化反应越快,水化物增长越快,凝结硬化加速,水化热越多。相反,温度降低,则水化反应减慢,强度增长变缓。但高温养护往往导致水泥后期强度增长缓慢,甚至下降。
水的存在是水泥水化反应的必要条件。当环境干燥时,水泥浆中的水分将很快蒸发,以致水泥不能充分水化,硬化也将停止;反之,水泥的水化将得以充分进行,强度正常增长。
(6)龄期(时间)。水泥的凝结硬化是随时间延长而渐进的过程,只要温度、湿度适宜,水泥强度的增长可持续若干年。
(7)外加剂。外加剂能影响C3S和C3A的水化、凝结硬化,从而影响到水泥的水化、凝结硬化性能。如掺加缓凝剂(木质素系、糖蜜系等)就会延缓水泥的水化、硬化,影响水泥早期强度的发展;如掺加早强剂(氯化钙、硫酸钠等)就能促进水泥的水化、硬化,提高早期强度;如掺加速凝剂(711型、红星一型等),能使水泥中的石膏失去缓凝作用,使水泥在较短的时间内迅速凝结硬化,早期强度显著提高。
(8)储存条件。水泥在储存期间,在空气中的水分和CO2的作用下,会使水泥发生缓慢的水化和碳化,而降低强度。储存3个月,强度降低10%~15%;储存6个月,强度降低20%~30%;储存1年,强度降低25%~40%。因此,水泥的有效储存期一般为3个月。如果储存过程使水泥受潮,水泥颗粒表面发生水化而结块,会严重降低强度。
4.1.4 硅酸盐水泥的技术性质
1.化学指标
(1)氧化镁含量。在水泥熟料中存在游离氧化镁,它的水化速度很慢,而且水化产物为氢氧化镁,不仅体积膨胀,当水泥已凝结硬化后才开始水化,产生体积膨胀,破坏已硬化的水泥石结构,出现龟裂、弯曲或崩溃等不安定现象,可以导致水泥石结构裂缝甚至破坏,而且氢氧化镁松软无胶结能力。因此,氧化镁是引起水泥体积安定性不良的原因之一。
(2)三氧化硫含量。水泥中的三氧化硫主要是生产水泥的过程中掺入的石膏,或者是煅烧水泥熟料时加入的石膏矿化剂带入的。如果石膏掺量超过一定限量,在水泥硬化后,石膏与水化铝酸钙反应生成水化硫铝酸钙(3CaO·Al2O3·3CaSO4·31H2O),使体积约增大1.5倍,造成水泥石膨胀开裂,导致水泥石结构破坏。因此,三氧化硫也是引起水泥体积安定性不良的原因之一。
(3)烧失量。烧失量是指水泥经高温灼烧处理后的质量损失率。水泥中未煅烧组分产生,如未烧透的生料、石膏带入的杂质掺和料,或者水泥受潮后,会导致烧失量增加。因此,烧失量是检验水泥质量的一项指标。
烧失量的测定方法是以水泥试样在950~1000℃下灼烧15~20min,冷却至室温称量。如此反复灼烧,直到恒质量,计算灼烧前后水泥质量损失百分率。
(4)不溶物含量。不溶物是指水泥经过酸(盐酸)和碱(氢氧化钠溶液)处理后,不能被溶解的残余物。它是水泥中非活性组分,主要由生料、混合材料和石膏中的杂质产生。
(5)氯离子含量。水泥混凝土是碱性的,钢筋氧化保护膜也是碱性的,故一般情况下,在水泥混凝土中的钢筋不致锈蚀。但如果水泥中氯离子含量较高,氯离子会破坏保护膜,加速钢筋锈蚀。
硅酸盐水泥的化学指标应符合《通用硅酸盐水泥》(GB 175—2007)的规定,参见表4.4。
表4.4 硅酸盐水泥化学指标(GB 175—2007)%

(6)碱的含量(选择性指标)。碱含量是指水泥中氧化钠和氧化钾的含量。水泥中的碱和骨料中的活性二氧化硅反应,生成膨胀性的碱硅酸盐凝胶,导致混凝土开裂的现象,称为碱骨料反应。因此,当使用活性骨料时,要选用低碱水泥。GB 175—2007中规定,水泥中碱含量(按Na2O%+0.658 K2O%)不得大于0.60%或由供需双方商定。
2.物理力学性质与指标
(1)细度(选择性指标)。细度是指水泥颗粒的粗细程度。同样矿物成分的水泥,颗粒越细,与水接触的表面积越大,水化反应越快,早期强度越高。但颗粒过细,硬化时收缩较大,易产生裂缝,容易吸收水分和二氧化碳而失去活性。另外,颗粒细则粉磨过程中的能耗大,水泥成本提高,因此细度应适宜。国家标准《通用硅酸盐水泥》(GB 175—2007)中规定,硅酸盐水泥、普通硅酸盐水泥的细度为比表面积不小于300m2/kg。
(2)标准稠度用水量。在检验水泥的凝结时间和体积安定性等技术指标时,必须在规定的稠度下进行,所测得的技术指标才有可比性。这个规定的稠度称为标准稠度。水泥净浆达到标准稠度时,拌和水的质量占水泥质量的百分数,称为标准稠度用水量。水泥标准稠度用水量用水泥标准稠度测定仪测定。硅酸盐水泥的标准稠度用水量一般在21%~28%之间。
水泥中熟料的成分、水泥的细度、混合材料的种类及掺量等因素影响水泥的标准稠度用水量。
(3)凝结时间。水泥的凝结时间分初凝时间和终凝时间。初凝时间是指标准稠度的水泥净浆自加水时起至水泥浆开始失去塑性的时间;终凝时间是指自加水时起至水泥浆完全失去塑性的时间。
水泥的凝结时间对施工有着重大意义。为保证水泥混凝土、水泥砂浆有充分的时间进行搅拌、运输、浇捣或砌筑,水泥的初凝时间不应过早。为使浇捣完毕的混凝土尽快硬化并具有一定的强度,以利于下一步施工,所以水泥的终凝时间又不宜太迟。
国家标准《通用硅酸盐水泥》(GB 175—2007)中规定:硅酸盐水泥的初凝时间应不早于45min,终凝时间不迟于390min。实际上,硅酸盐水泥的初凝时间一般为1~3h,终凝时间一般为4~6h。凡初凝时间不符合规定者为废品,不得用于任何工程;终凝时间不符合规定者为不合格品,可降低强度等级使用。
(4)体积安定性。体积安定性是指水泥在硬化过程中体积变化是否均匀的性质。安定性不良的水泥,在硬化时体积膨胀而使水泥石裂缝,降低构筑物的质量,甚至引起严重的质量事故。
引起体积安定性不良的原因,主要是由于水泥中所含游离氧化钙(f-CaO)或游离氧化镁(f-MgO)或三氧化硫(SO3)过多所造成的。水泥中的f-CaO和f-MgO都是过烧的,水化速度很慢,当水泥已凝结硬化后才开始水化,产生体积膨胀,破坏已硬化的水泥石结构,出现龟裂、弯曲或崩溃等不安定现象。当石膏掺入量过多时,在水泥硬化后,石膏与水化铝酸钙反应生成水化硫铝酸钙(3CaO·Al2O3·3CaSO4·31H2O),使体积约增大1.5倍,造成水泥石开裂。
用沸煮法检验f-CaO是否引起安定性不合格,按照《标准稠度用水量、凝结时间、安定性检验方法》(GB/T 1346—2001)中的规定,其具体方法是将标准稠度的水泥净浆装入雷氏夹中沸煮后测其膨胀值;另一种方法是将标准稠度的水泥净浆做成试饼沸煮后检验是否有裂纹、弯曲。用压蒸法检验f-MgO对安定性的影响,一般不作该项试验,在《通用硅酸盐水泥》(GB 175—2007)中的规定,水泥中MgO的含量不得超过5.0%。用水浸法检验SO3对安定性的影响,一般不作该项试验,在《通用硅酸盐水泥》(GB 175—2007)中规定,SO3的含量不得超过3.5%。GB 175—2007规定,水泥安定性必须合格。三项中有一项不合格的水泥必须作废品处理,禁止在工程中使用。
(5)强度与强度等级。水泥的强度是评定其质量的重要指标。
在《水泥胶砂强度检验方法(ISO法)》(GB/T 17671—1999)中规定,水泥的强度是按规定的配合比(水泥和标准砂的质量比为1∶3,水胶比为0.5),制成40mm×40mm×160mm的标准试件,在标准温度(20℃±1℃)的水中养护,分别测定其3d和28d的抗折强度和抗压强度。根据28d抗压强度来确定水泥的强度等级,其3d抗压强度及各龄期抗折强度也均不得低于规定的强度值。
硅酸盐水泥分42.5、42.5R、52.5、52.5R、62.5和62.5R等六个强度等级。依据水泥3d的强度又分为普通型和早强型(R型)两种类型。早强型水泥3d的抗压强度可以达到28d抗压强度的50%,同强度等级的早强型水泥3d的抗压强度较普通型的可以提高10%~24%。各强度等级硅酸盐水泥的各龄期强度不得低于表4.5中的数值。
表4.5 硅酸盐水泥各龄期强度值(GB 175—2007)

(6)水泥的水化热。水泥在凝结硬化过程中放出的热量,称为水泥的水化热。水化放热量和放热速度不仅决定于水泥的矿物成分,还与水泥细度、水泥中所掺混合材料及外加剂的品种、数量等有关。水泥矿物进行水化时,铝酸三钙放热量最多,硅酸三钙放热量稍低,硅酸二钙放热量最低。水泥细度越细,水化放热量越多,放热速度也越快。水泥的水化热大部分在水化初期(7d内)放出,以后逐渐减少。
水泥的水化热对一般混凝土工程的冬季施工有利,但对大体积混凝土工程有害。由于大体积混凝土水化热积聚在内部不易放出,使混凝土内外产生较大温差,并由此产生较大的温差应力,使混凝土开裂。因此,大体积混凝土不宜用硅酸盐水泥,而应选用水化热低的水泥。
(7)密度与堆积密度。硅酸盐水泥的密度主要取决于熟料的矿物组成,一般为3.05~3.20g/cm3。硅酸盐水泥的堆积密度除与矿物组成和细度有关外,主要取决于水泥堆积时的紧密程度,疏松堆积时的堆积密度为900~1200kg/m3,紧密状态下可达1400~1700kg/m3。在进行混凝土配合比设计时,通常取水泥的密度为3.1g/cm3,水泥的堆积密度为1300kg/m3。
4.1.5 水泥石的腐蚀与防止
硅酸盐水泥硬化后的水泥石,在正常使用条件下具有较好的耐久性,但在某些腐蚀性液体或气体介质中,使得水泥石结构逐渐遭到破坏,强度降低甚至使整个工程遭到破坏,这种现象称为水泥石的腐蚀。
1.水泥石腐蚀的主要方式
(1)溶出性腐蚀(软水腐蚀)。在水中含有重碳酸盐,水泥石中的Ca(OH)2和水中的重碳酸盐反应,生成CaCO3积聚在已硬化的水泥石孔隙内和覆盖在水泥石表面,形成密实的保护层,阻止外界水的浸入和内部Ca(OH)2的析出,保护了水泥石,因此水泥石不会被溶解。但是在不含或含极少重碳酸盐的软水中,如雨水、雪水、工业冷凝水、蒸馏水等,能使Ca(OH)2溶解,如果软水是流动的或有压力的,则溶解的Ca(OH)2就会被带走,使Ca(OH)2继续溶出。由于水泥石中的Ca(OH)2浓度降低,其他水化物也会分解而溶出,如此继续发展,水泥石结构就会遭到破坏。
(2)盐类腐蚀。
1)硫酸盐腐蚀。在海水、湖水、盐沼水、地下水及某些污水中常含有钠、钾、铵等的硫酸盐,它们与硬化的水泥石中Ca(OH)2起置换作用,生成硫酸盐。
硫酸盐与水泥石中的Ca(OH)2发生反应生成石膏结晶,石膏进一步与水泥石中的水化铝酸钙反应,生成水化硫铝酸钙:
3CaO·Al2O3·6H2O+3(CaSO4·2H2O)+19H2O═══3CaO·Al2O3·3CaSO4·31H2O
由于水化硫铝酸钙含水量大,结晶时体积膨胀,比原有体积增大1.5倍以上,对已硬化的水泥石起极大的破坏作用。由于水化硫铝酸钙(钙钒石)的结晶呈针状,故通常称为“水泥杆菌”。
2)镁盐腐蚀。在海水及地下水中,常含有大量的镁盐,主要是硫酸镁和氯化镁,它们与水泥石中的Ca(OH)2起置换作用:
MgSO4+Ca(OH)2+2H2O═══CaSO4 ·2H2O+Mg(OH)2
MgCl2+Ca(OH)2═══CaCl2+Mg(OH)2
生成的氢氧化镁松软而无胶凝能力,氯化钙易溶于水,二水石膏则易引起硫酸盐的破坏作用。因此,硫酸镁对水泥起着镁盐和硫酸盐的双重腐蚀作用。
(3)酸类腐蚀。
1)碳酸腐蚀。在工业污水、地下水中常溶解有较多的二氧化碳,这种水对水泥石腐蚀作用是通过下面方式进行的。
开始时二氧化碳与水泥石中的氢氧化钙作用生成碳酸钙,反应式为:
Ca(OH)2+CO2+H2O═══CaCO3+2H2O
生成碳酸钙再与含碳酸的水作用转变成重碳酸钙,此反应为可逆反应。反应式为:
CaCO3+CO2+H2OCa(HCO3)2
生成的重碳酸盐Ca(HCO3)2易溶于水,当水中含有较多的碳酸,并超过平衡浓度,使上述反应始终向生成Ca(HCO3)2的方向进行。从而导致水泥石中的氢氧化钙通过转变为易溶的重碳酸钙而溶失。造成水泥石中的Ca(OH)2浓度降低,导致水泥石结构破坏。
2)一般酸性腐蚀。在地下水或工业废水中,常含有有机酸和无机酸,这些酸类与水泥石中的Ca(OH)2发生反应,如盐酸和硫酸:
2HCl+Ca(OH)2═══CaCl2+2H2O
H2SO4+Ca(OH)2═══CaSO4 ·2H2O
生成的CaCl2易溶于水,石膏(CaSO4·2H2O)在水泥石孔隙内结晶,体积膨胀,使水泥石遭到破坏,而且还会进一步造成硫酸盐侵蚀,对水泥石结构的破坏性更大。
2.腐蚀的防止
水泥石腐蚀的原因有内因和外因之分。内因一是由于水泥水化物中的氢氧化钙及其他成分,能一定程度地溶于水(特别是软水);氢氧化钙、水化铝酸钙等都是碱性物质,若环境水中有酸类或某些盐类时,能与其发生化学反应,若新生成的化合物或易溶于水、或无胶结能力、或因结晶膨胀而引起内应力,都将导致水泥石结构的破坏。二是水泥石不密实,使侵蚀性介质进入内部引起破坏。外因是侵蚀性介质的存在。因此,可采取相应的防止措施。
(1)根据腐蚀环境的特点,合理地选用水泥品种。采用水化产物中氢氧化钙含量较少的水泥,可提高抵抗淡水等侵蚀作用的能力;采用铝酸三钙含量低于5%的抗硫酸盐水泥,可提高抵抗硫酸盐腐蚀的能力。
(2)提高水泥石的密实度。由于水泥的实际用水量是水泥水化时理论需水量的2~3倍,多余的水蒸发后形成毛细管通道,腐蚀介质容易渗入水泥石内部,造成水泥石的腐蚀。在实际工程中,可采取合理设计混凝土配合比、降低水胶比、正确选择骨料、掺外加剂、改善施工方法等措施,提高砂浆或混凝土的密实度。
(3)加做保护层。当水泥制品所处环境腐蚀性较强时,可用耐酸石材、耐酸陶瓷、塑料、沥青等,在混凝土或砂浆表面做一层耐腐蚀性强且不透水的保护层。
4.1.6 硅酸盐水泥的特性与应用
1.早期强度高
硅酸盐水泥凝结硬化快,早期强度和强度等级都高,可用于对早期强度有要求的工程,如现浇混凝土楼板、梁、柱,预制混凝土构件;也可用于高强度混凝土和预应力混凝土工程。
2.抗冻性较好
硅酸盐水泥石结构密实且早期强度高,所以抗冻性好,适用于严寒地区遭受反复冻融及抗冻性要求较高的混凝土工程。
3.干缩小、耐磨性好
硅酸盐水泥硬化时干缩小,不易产生干缩裂缝,适用于干燥环境的混凝土工程。由于干缩小,表面不易起粉,因此,耐磨性较好,适用于道路工程。早强型(R型)硅酸盐水泥由于水化热大,凝结时间短,适用于快速抢修工程和冬季施工,但适用于混凝土远距离输送或高温季节施工的混凝土。
4.抗碳化性能较好
碳化是指水泥石中的氢氧化钙与空气中的二氧化碳和水发生化学反应,生成碳酸钙的过程。碳化会引起水泥石内部的碱度降低,钢筋混凝土中的钢筋因钝化保护膜的破坏而锈蚀。硅酸盐水泥硬化后水泥石中含有较多的氢氧化钙,碳化时水泥的碱度降低少,对钢筋的保护作用强,因此,适用于空气中二氧化碳浓度较高的环境,如热处理车间等。
5.水化热大
硅酸盐水泥中的水泥熟料多,其硅酸三钙和铝酸三钙含量多,故其水化热大,因此有利于冬季施工,适用于冬季施工的混凝土工程,但不宜用于大体积混凝土(一般是指长、宽、高均在1m以上)工程,因为容易在混凝土构件内部聚集较大的热量,产生温度应力造成混凝土结构破坏。
6.耐腐蚀性差
由于硅酸盐水泥水化后含有较多的氢氧化钙和水化铝酸钙,因此,其耐软水和耐化学腐蚀性差,不能用于受流动的软水和有水压作用的混凝土工程,也不能用于受海水和矿物水作用的混凝土工程。
7.耐热性差
当水泥石处于250~300℃的高温环境时,其中的水化硅酸钙开始脱水,体积收缩,强度下降。氢氧化钙在600℃以上会分解成氧化钙和水,高温后的水泥石受潮时,氧化钙与水作用生成氢氧化钙,体积膨胀,造成水泥石的破坏,因此硅酸盐水泥不适用于温度高于250℃的耐热混凝土工程,如工业窑炉和高炉的基础。