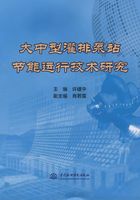
1.4 离心泵叶轮三维数字化优化设计
1.4.1 计算模型
本书中以一离心泵叶轮作为计算模型进行叶轮的水力优化设计。该离心泵进口直径Ds=400mm,出口直径Dt=300mm,叶轮直径D2=558mm,出口宽度b2为35mm,叶轮叶片数为6,水泵转速n=1470r/min,泵的设计流量Qd=1500m3/h,扬程H=115m。通过叶轮木模图对叶轮进行三维实体造型,如图1-8所示。为简化计算,在后述优化过程中使用叶轮的单流通通道进行CFD数值模拟和优化计算。

图1-8 叶轮及单流通实体造型图
1.4.2 数值模拟设定
(1)网格划分。离心泵叶轮内部流场具有较强的三维性,数值模拟要求较高,在模拟的过程中,计算网格的生成是十分重要的一个环节,网格划分质量的好坏直接影响计算结果的准确性和精确性,进而影响数值模拟的可靠性。本研究项目在优化计算开始时先采用粗网格进行数值计算,用较粗的网格对计算模型进行划分并找到较好的优化方案,给出一个较接近最终结果的初场;另外对于计算工作量非常大的自动优化设计过程,如果每一次计算都采用细网格计算,其计算量和计算时间是庞大且难以承受的。然后再在此基础上用细网格划分进行修改验证以得到最终的优化方案,这样就可以在较短的时间内得到较为良好的优化方案。为排除网格不同而造成的计算误差,本研究项目在对离心泵叶片进行优化的过程中均采用相同的网格分布的计算网格。
经网格无关性检查后,最终确定本研究项目中离心泵单流道叶片优化过程中迭代计算所使用的网格如图1-9(a)所示。网格生成过程中进行了较为细致的调整,分布对叶片头部、尾部及壁面附近进行了加密,放大图如图1-9(b)所示。三维单流道叶片计算网格节点数为16558个,网格总数为68219个。

图1-9 叶轮单流道网格图
(2)边界条件。边界条件对离心泵内部流场有着非常重要的影响,只有施加了既与实际情况相吻合的边界条件,又与湍流模型相适应,才能得到有参考价值的内部流场。对离心泵内部流场进行数值计算时,应用进口、出口、壁面和对称面三类边界条件。
1)流场进口。计算流场的进口设置在单通道叶轮的进口,采用均匀来流的质量流量作为进口边界条件。如设计工况下的质量流量:

2)流场出口。计算流场的出口设置在单通道叶轮的出口,采用压力出口。
3)固壁边界。所有的表面都是流体与固体接触的面,如叶轮的前后盖板、叶片正背面都是壁面类型的边界。固壁上满足采取无滑移的壁面边界条件。对于壁面的移动,凡是跟随叶轮一起旋转的壁面都采用移动的壁面,且移动的方向和速度与叶轮旋转的方向和速度一致,而其余壁面均为静止,速度值为零。
4)周期性边界条件。计算中取一个叶片单通道作为计算域。在叶片前后延伸区的周向边界上,出于物理上的考虑,在单通道叶片的上游和下游延伸段以及顶部间隙的吸力侧施以周期性边界条件。
(3)数值计算参数设置。本文采用SST(Shear Stress Transport)k-ω模型进行离心泵叶轮的CFD计算,SST k-ω模型是从k-ε模型中发展衍变而来。通常SST k-ω会比k-ε模型更有效。SST k-ω湍流模型的处理方法是:在近壁面采用k-ω模型,在边界层外部采用k-ε模型,在边界层内则混合使用两种模型,并利用一个混合加权函数Fi的大小来进行加权平均。在求解时,采用高精度差分格式和方根RMS残差格式,求解精度设为1e-4。
1.4.3 目标函数和约束条件
本节使用上述的优化方法对离心泵的叶轮进行优化设计,以叶轮的效率最高作为目标函数进行迭代优化计算。叶轮的效率定义为:

其中:


式中:Pu为叶轮的有效功率,W;P为叶轮轴功率,W;Q为叶轮进口处的流量,m3/s;H为叶轮的理论扬程,m;PT,inlet为叶轮进口处总压,Pa;PT,outlet为叶轮出口处总压,Pa;M为叶轮绕中心轴的力矩之和,N·m;ω为叶轮转动的角速度,rad/s。
在优化设计中,还需对第三章叶轮参数化后的产生设计变量进行取值范围的上、下界限与约束,称之为约束条件。本文的约束条件见表1-2。
表1-2 设计参数的约束条件

1.4.4 优化过程运行
(1)DOE实验设计及结果分析。在搭建好的离心泵叶轮优化平台上,选择正交矩阵法对第3章所述的所有设计变量进行DOE试验设计,选中所有设计变量,iSIGHT会根据所选的正交矩阵实验设计对每一变量共进行2个水平、32次试验,每一方案自动生成网格,并完成相应的数值模拟计算。正交试验方案运行完成图如图1-10所示。
DOE反复迭代计算结束后,利用iSIGHT对DOE结果进行后处理分析。图1-11显示了所有设计变量对目标函数变化贡献率的Pareto图,图中在负半轴分布的设计变量代表着对目标函数呈现负贡献率,在正半轴分布的设计变量代表着对目标函数呈现正贡献率。
由图可以看出每个设计参数的改变对计算结果的贡献率存在较大差异,最大的达到22%左右.而最小的几乎可以忽略不计。18个设计变量中,轴面型线的设计变量和流面型线的设计变量均对离心泵在设计工况的效率呈现出不同的影响程度,对提高叶轮效率的设计变量的影响程度依次为P4Z,L 2Theta2,L 1Theta3,P7Z,L 3Theta3,L 2Theta3,对降低叶轮效率的设计变量的影响程度依次为P8Z,P10Z,P3Z,L 2Theta4,L 3Theta1,P2Z。因此可以看出,叶轮轴面流道的控制变量和叶片型线中间控制变量对叶轮的效率影响更大。

图1-10 32次正交试验方案运行完成图

图1-11 设计变量对效率贡献图
(2)优化运行。在第3章的离心泵叶轮优化设计平台施加遗传算法全局搜索和二次序列规划方法局部寻优的优化策略组合,启动设计平台进行优化求解,优化过程曲线如图1-12所示,图中记录了叶轮效率在优化过程中的变化图。经219次迭代优化计算后,寻找到目标函数的全局最优解,优化过程自动结束。最终得到的叶轮最优效率为0.916。
经自动优化设计过程后,设计变量均有所改变。离心泵叶轮的效率由原来的89.50%提高到91.67%,水力性能得到了提高。优化前后叶片的各参数值见表1-3。可看出,叶轮的轴面型线改变较小,但叶片进口边的位置(P10)有了比较明显的改变。同时,前、后盖板和中间流面的流面型线在叶片进口出了也有改变。

图1-12 优化过程曲线图
表1-3 优化前后叶片参数对比

根据原始叶轮和单工况点优化叶轮的轴面型线和流面型线参数,绘制叶轮的轴面投影图、流面型线图和三维图并进行比较,如图1-13所示。从对比图可看出,原始叶轮的进口边呈直线形状,而经优化后,单工况点优化叶轮的进口边呈曲线形状,同时,叶片的进口安放角有所增大,出口安放角基本保持不变。

图1-13 优化结果对比图
1.4.5 优化结果分析
(1)验证计算。为了提高优化速度,在上述优化过程中计算所使用的网格属于比较粗的非结构网格,为进一步对对优化结果进行验证,并使离心泵内流场的预测结果达到完全精确的水平,因此需要用细网格对优化结果重新进行划分,并进行更加精确的数值计算。对优化前的原始叶轮和优化后的设计工况叶轮进行网格的重新划分,在ANSYS-TurboGrid中直接读入叶轮的几何模型,根据本研究项目的离心泵叶片形状生成拓扑结构,并最终生成高质量的结构化网格。网格生成图如图1-14所示,总节点数为290586个,总网格数265788个。网格检查合格后,导入CFX进行数值模拟。设置收敛残差为1e-5。
(2)外特性对比分析。图1-15为计算得到的原始叶轮和设计工况优化叶轮的性能曲线的比较,从图中可以看出,在小流量工况下,两个叶轮的水力效率基本持平。但在设计工况附近,通过对叶轮轴面型线和叶片型线控制参数的改变,叶轮的水力效率明显提高,设计工况点较原始叶轮提高约3%。同时,叶轮的扬程在这个工作范围内均有所提高。外特性曲线表明,经优化后的叶轮的水力性能得到明显改善。
(3)设计工况内流特性结果分析。优化前后的叶轮的压力分布对比如图1-16所示。图1-16为原始叶轮和单工况点优化叶轮在叶片20%、50%、80%展向上的叶片表面压力分布对比图。从图1-16中可看出,在各个叶片展向上,单工况点优化叶轮叶片表面的压力差均大于原始叶轮叶片表面的压力差,压力差的增大表示叶片做功能力的增强,因此单工况点优化叶轮较原始叶轮的做功能力显著提高,在叶轮的水力特性上表示出扬程和效率的上升。

图1-14 验证计算结构网格图

图1-15 叶轮性能曲线对比图
在20%展向上,原始叶轮和优化叶轮呈现出较为不同的叶片表面压力分布。在叶片进口处,原始叶轮的吸力面的压力大于压力面的压力,由此可知原始叶片在进口处为负冲角,因而流体在此处可能出现流动脱流和漩涡的产生。但优化叶轮的叶片进口处叶片表面压力差没有出现明显的减小,基本为逐渐增加,因此流体从叶片进口到出口持续地受到叶轮对其做功,并在叶片后部达到最大值,随后逐渐减少。但同时,也可看出优化叶轮的整体叶片表面压力分布较原始叶轮在从叶片进口到出口均有不同程度的下移,原始叶轮的压力最低点约为-0.75MPa,而优化叶轮的最低点达到-0.9MPa,因此在此展向上优化叶轮的气蚀性能有所下降。

图1-16 叶片表面压力分布对比图(设计工况)
在50%展向上,可看出原始叶轮和优化叶轮的压力分布范围基本相似,但分布形状不尽相同。原始叶轮在叶片进口处仍呈现负冲角;优化叶轮的压力面与原始叶轮基本相同,但优化叶轮的吸力面在叶片中前部平稳上升,在后部迅速增加,表现出在叶片中后部较为宽的表面压力差,原始叶轮的吸力面曲线则一直呈上升趋势,因此优化叶轮的做功能力较原始叶轮有所增加。
在80%展向上,原始叶轮在叶片进口处突然出现压力的突降,因此在此处极易导致低能流体在端部的大量聚积而形成通道涡,造成水力性能的损失。同时,通道涡在向下游发展过程中,会不断地卷吸端壁和叶片吸力面新产生的低能流体,使得更多的低能流体被卷入到通道涡的发展过程中,给下通道带来较大的损失值,严重时涡会堵住整个流通通道。
图1-17为设计工况时叶轮在轴面的平均轴面速度(Cm)分布图。从图中可较为明显地看出原始叶轮的速度分布范围为3.5m/s到10.0m/s,而单工况点优化叶轮的速度范围增加为4.5m/s到11.0m/s。在流体由轴向流动向径向流动的转变时,由于叶片进口形状的改变,单工况点优化叶轮在靠近前盖板处的轴面速度分布较原始叶轮更为均匀。原始叶轮在此次速度的迅速增加及不均匀分布会导致此处低压区和流动漩涡的形成,造成水力性能的损失和效率下降。同时,在叶轮出口处,原始叶轮在从前盖板到后盖板的轴面平均速度呈逐渐上升趋势,而单工况点优化叶轮在从前盖板到后盖板的轴面平均速度基本呈同一速度,流动分布的均匀性可使流体在流入蜗壳形成均匀的速度环量。

图1-17 叶轮平均轴面速度分布图(设计工况)