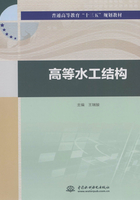
2.1 概述
2.1.1 碾压混凝土坝发展概况[2-4]
1975年,美国陆军工程团在位于巴基斯坦的塔贝拉调水工程输水隧洞的出口修复施工中,首次采用了未经筛洗的砂砾石加少量水泥拌和混凝土,经振动碾压,修复被冲毁的部位。在42d内浇筑了35万m3混凝土,日平均浇筑强度为8400m3,显示了碾压混凝土快速施工的巨大潜力。
1981年3月,日本建成了世界上第一座碾压混凝土重力坝——高89m的岛地川坝,1982年美国建成了世界上第一座全碾压混凝土坝——高52m的柳溪坝,此后碾压混凝土筑坝技术便在世界各国获得广泛应用,发展十分迅速。截至2005年年底,世界上已建、在建或规划的坝高超过15m的碾压混凝土坝有319座 (以重力坝为主)。
我国于1978年开始进行碾压混凝土筑坝技术的研究,1979年在龚嘴水电站第一次进行了碾压混凝土野外试验,1984年采用碾压混凝土建成了铜街子水电站左岸牛石溪沟1号坝,1986年在福建坑口建成了我国第一座碾压混凝土重力坝,即坝高56.8m的福建坑口坝。1993年,建成了当时世界上最高的普定碾压混凝土拱坝,坝高75m。2001年,建成目前世界上最高的四川沙牌碾压混凝土拱坝 (坝高132m)及厚高比最小(0.17)的甘肃龙首碾压混凝土双曲拱坝 (坝高80m)。截止2007年年底,我国已建和在建碾压混凝土坝有126座,最高的为龙滩碾压混凝土重力坝,坝高216.5m。2004年以来相继开工的光照 (坝高200.5m)、大花水 (坝高134m)、武都 (坝高119m)、景洪 (坝高110m)、金安桥 (坝高156m)等,标志着我国碾压混凝土坝建设达到新的水平。目前已建的红水河龙滩水电站碾压混凝土重力坝,坝高216.5m,坝体混凝土总方量达700万m3,其中碾压混凝土方量约占65%,是目前世界上最高和体积最大的碾压混凝土重力坝,该坝2007年作为中国代表荣获国际碾压混凝土工程里程碑奖。沙牌碾压混凝土拱坝经受住了2008年5月12日汶川地震的严峻考验,在国际坝工界具有里程碑意义,作为碾压混凝土高拱坝的代表,为碾压混凝土筑坝技术的进一步推广应用起到了新的推动作用。
2.1.2 碾压混凝土材料特点及其施工技术
2.1.2.1 碾压混凝土材料特点[5,6]
碾压混凝土是由水泥、掺合材料、水、砂、石子及外加剂等六种材料所组成的。我国筑坝碾压混凝土由于掺用较大比例的掺合材料,故一般使用强度等级不低于32.5MPa的普通硅酸盐水泥 (也称 “普通水泥”)或硅酸盐水泥。为了适应碾压施工,碾压混凝土拌和物属超干硬拌和物。拌和物粘聚性差,施工过程中粗骨料易发生分离,为减少以至避免粗骨料的分离现象,一般都限制粗骨料最大粒径不大于80mm,且适当减小最大粒径级粗骨料所占的比例。砂中细粉 (在我国系指小于0.16mm的颗粒)含量对改善碾压混凝土的性能有不可忽视的作用。我国水利水电行业标准 《水工碾压混凝土施工规范》(SL53—94)推荐碾压混凝土使用的人工砂中,细粉含量达到10%~22%。
为适应碾压混凝土的连续、快速碾压施工,一般不在混凝土中设置冷却水管以降低混凝土的温升。因此,碾压混凝土中水泥用量应尽可能降低。但是,为了满足施工对拌和物工作度及坝体设计对混凝土提出的技术性能要求,碾压混凝土的水泥用量又不宜过小。这就存在着矛盾。解决矛盾的可行而有效的方法是在碾压混凝土中掺用较大比例的掺合材料。外加剂是碾压混凝土必不可少的组成材料之一。碾压混凝土中胶凝材料用量少、砂率较大,为了改善拌和物的施工性能,必须掺入减水剂。减水剂的掺入可以降级拌和物的VC值 (vibratingcompactedvalue,即在固定振动频率及振幅和固定压强条件下,拌和物从开始振动碾压至表面泛浆所需时间的秒数),改善其黏聚性或抗离析性能。碾压混凝土的大面积铺筑施工特点,要求拌和物具有较长的初凝时间,以减少冷缝出现,改善施工层面黏结特性,为此必须掺入缓凝剂。在严寒地区使用的碾压混凝土,还有必要考虑掺入引气剂,以提高混凝土的抗冻性。由于碾压混凝土拌和物的干硬性以及掺合材料的吸附性,因此碾压混凝土拌和物掺入外加剂的量略大于常态混凝土。
碾压混凝土虽属混凝土但又有别于常态混凝土。碾压混凝土拌和物与常态混凝土拌和物比较,骨料用量较多、水泥用量较少,虽掺用一定量的掺合材料,但胶凝材料用量仍较少。拌和物不具有流动性,坍落度为零,黏聚性小,一般不泌水。拌和物在振动压实机具所施加的动压力作用下,胶凝材料将由凝胶转变为溶胶 (即发生液化)而具有一定的流动性。固相颗粒位置得到重新排列,颗粒之间产生相对位移,彼此接近。小颗粒被挤压填充到大颗粒之间的空隙中,空隙里的空气受挤压而逐渐逸出,拌和物逐渐密实。因此,碾压混凝土拌和物的振动压实既具有混凝土的基本特点,也具有土石料压实的某些特征。碾压混凝土的特定施工方法要求拌和物必须具有适当的工作度——即能承受住振动碾在其上行走不陷落,又不能过于干硬,以免振动碾难于甚至无法将其碾压密实。工作度用VC值表示,VC值的大小应根据振动碾的能量、施工现场温度、湿度条件加以确定,一般选用5~15s较合适。VC值是控制碾压施工质量的重要指标,常用维勃稠度测定仪测定。
概括起来,碾压混凝土呈现出干、贫混凝土的材料特点;干即材料的用水量较少,是超干硬性无坍落度混凝土;贫即材料的水泥用量少,以较大掺量粉煤灰代替水泥,单位体积混凝土水泥用量比常态混凝土少。
硬化后的碾压混凝土与常态混凝土比较,技术性能有其明显的特点:由于碾压混凝土中掺用较大比例的掺合料,而多数掺合料早期水化反应较少,使碾压混凝土硬化早期强度较低,后期强度增长较大;碾压混凝土的绝热温升明显低于常态混凝土,最高温升出现时间明显推迟,温降缓慢;碾压混凝土的自生体积变形及干缩变形明显小于常态混凝土。
在实际工程中碾压混凝土的性能受施工质量影响较大。施工层面的黏结质量对碾压混凝土的性能影响尤其突出。
根据工程经验,我国常用的碾压混凝土材料配合比见表2.1[6]。
表2.1 我国碾压混凝土材料经验配合比

2.1.2.2 碾压混凝土坝施工技术[6,7]
碾压混凝土筑坝的特点是快速连续施工。如果整个生产系统的任一个环节出现故障、不协调或不配套的情况都会影响工程进度及碾压混凝土筑坝特点的发挥,故必须按要求有序地进行施工。
碾压混凝土筑坝的施工工序为:铺筑前的准备→拌和→运输→卸料和平仓→碾压→成缝→缝面处理→异种混凝土浇筑→养生和防护→埋设件施工→特殊气象条件下的施工。
碾压混凝土的施工工艺流程为:骨料筛分→配料→拌和→运输→入仓→摊铺→振动碾压→切缝 (设计诱导孔)→养护→水平缝处理→下一个施工层循环。
我国的碾压混凝土坝施工技术采用大面积薄层连续浇筑的方法。混凝土摊铺和碾压的层厚一般为30cm,这样可以防止骨料分离,压实振动波易传到层底。为保证层间黏结良好,层间允许间隔时间从下层混凝土拌和物拌和加水时起到上层混凝土碾压完毕为止,需控制在混凝土初凝时间以内,且混凝土拌和物从拌和到碾压完毕的历时应不超过2h,这些要求是确定浇筑层厚和仓面面积时需要考虑的基本条件。
碾压混凝土振动碾压遍数一般为6~7遍,连续浇筑3~4层后宜间歇2~3d。对施工缝和冷缝采用刷毛、冲洗以后铺设砂浆层的方法进行处理,对于连续浇筑的碾压混凝土,要求施工层面具有足够的抗渗性和层间黏结强度。
2.1.3 碾压混凝土坝的特点[2,15]
碾压混凝土坝是以建造土石坝的施工方法来建造混凝土坝。碾压混凝土坝断面尺寸与常态混凝土坝相似。由于碾压混凝土坝不设纵缝,采用通仓薄层铺料、连续上升的施工方法,因此避免了常态混凝土施工中的分仓、设置键槽及接缝灌浆管路、坝块间歇上升等问题。同时由于采用大仓面施工,能有效提高各类运输、平仓和碾压设备的生产效率,最终可提高施工速度,使工程工期缩短,有利于工程及早发挥效益。此外,碾压混凝土坝与土石坝相比,断面尺寸小,工程量小,而且用与土石坝相同的机械施工,因此,碾压混凝土坝的施工工期比土石坝短。
碾压混凝土坝大量采用粉煤灰代替水泥,故水泥用量少,有可能降低材料成本。由于不设纵缝,模板工程量减少,从而节省了工程投资。同时由于水泥用量少,水泥水化热温升低,可简化或不采用温控措施,从而大大节约温控费用。此外,和土石坝相比,碾压混凝土坝体积小,可节省建筑材料。由于坝基宽度减小,减少了开挖和基础处理范围,并可使施工导流及泄洪建筑物的长度缩短。由于中小型碾压混凝土坝可在几个月铺筑、碾压完毕,因此允许大大降低施工导流标准,从而降级工程造价。
概括起来,碾压混凝土坝主要有以下四方面的特点[2,15]:
(1)碾压混凝土筑坝改变了常态混凝土筑坝用振捣器插入混凝土振捣密实的方法,而是用振动碾压机在层面振动碾压,大仓面碾压施工。
(2)碾压混凝土筑坝新技术具有节省水泥、施工简便、缩短工期、造价低廉等优点。
(3)碾压混凝土属干、贫混凝土,以较大掺量粉煤灰代替水泥,单位体积混凝土所用水泥量比常态混凝土少,其单位混凝土散发的水化热要比常态混凝土少,绝热温升也将较低,具有温控简单的有利条件。
(4)碾压混凝土坝不能像常态混凝土坝施工中的柱状块所具有那么大的散热表面积,这是温控方面的不利条件。
2.1.4 碾压混凝土坝的类型及其特点
2.1.4.1 按坝型分类[2]
按照坝型的不同,碾压混凝土坝可分为以下两类:
(1)碾压混凝土重力坝。碾压混凝土重力坝的工作原理与常规重力坝相同,只是在混凝土材料和坝体构造上要适应碾压混凝土的施工方法。
1)剖面选择。为适应碾压混凝土的施工工艺特点,坝体剖面一般力求简单,在满足稳定的条件下,最好是上游面垂直,下游面单一边坡。但是对于高度在100m以上的重力坝,为了节省混凝土方量,也可采用上游面为折坡或斜坡的剖面型式。如棉花滩碾压混凝土重力坝的上游坝坡采用1∶0.0667的坡度,基本垂直。棉花滩碾压混凝土重力坝挡水坝段横剖面如图2.1所示[2]。
图2.1 棉花滩碾压混凝土重力坝挡水坝段横剖面图 (单位:m)
2)排水系统。在重力坝内设置排水系统,能够大大减小扬压力,从而增加坝体的稳定性。在碾压混凝土重力坝内放置预埋件形成排水体系,是比较理想的。但无论采用填碎石塑料膜保护或者用钢管,都不能保证竣工后排水通畅。因为在碾压混凝土施工过程中,上述设施很容易被压碎或错位。最可靠的方法是碾压施工完成后再钻孔形成排水系统。有的工程由于下游水位过高,形成较大的浮托力,则采用设在下游廊道的抽排设施,以保证坝体内的扬压力维持在最低水平。
3)坝体的分缝分块。碾压混凝土重力坝不设纵缝,是否设横缝及横缝分法与所在地区及施工条件有密切关系。我国碾压混凝土重力坝建设的实践表明,在亚热带地区或冬季寒冷地区,必须设横缝,以利于温度控制。另外,施工条件也起一定的控制作用。例如为了保证层面结合良好,必须在下层混凝土初凝前对上层混凝土进行碾压;而仓面的大小又受混凝土拌和、运输能力的制约,通常以横缝作为仓面的分界线比较合适。横缝的结构有永久横缝 (切缝)和诱导缝两种,间距一般为15~20m。
4)下游坡处理与溢流坝面消能。我国碾压混凝土重力坝的下游坡大多数都是用混凝土预制块形成阶梯状,各工程根据起重机容量及施工条件情况,所采用的块体不同。最常用的是长方形块体,靠自重稳定来形成下游坡。国外常在溢流坝面采用阶梯形消能,其原理是利用坝面的加糙进行沿程消能。我国福建的水东碾压混凝土重力坝,在1∶0.65的下游坡上采用预制混凝土块,形成宽0.585m、高0.9m的阶梯,下连消力池,实践证明消能效果良好。
(2)碾压混凝土拱坝。
1)体型选择。碾压混凝土拱坝的平面布置型式与常态混凝土拱坝相似。如普定拱坝采用的是定圆心、变半径、变中心角的等厚、双曲非对称拱坝。而沙牌拱坝的体型则是通过对三心圆单曲拱坝和抛物线双曲拱坝两种代表性方案比较后确定的。两种方案在满足拱坝的稳定和应力条件方面无大的差别,其中双曲拱坝的工程量比较小。但从国内外碾压混凝土拱坝施工技术水平和实践经验来看,单曲拱坝体形简单,有利于加快碾压混凝土施工速度及保证施工质量。因此,沙牌拱坝的坝型选用了三心圆单曲拱坝。
2)断面选择。碾压混凝土拱坝的断面选择也与常态混凝土拱坝无本质区别。
3)分缝型式。碾压混凝土拱坝的分缝除要考虑满足温控防裂等要求外,还应充分考虑碾压混凝土大仓面快速施工的要求。我国的溪柄溪拱坝因河谷较窄又处于温和气候条件,施工时间可选在寒冷低温的冬季,因此可不必分缝。其他的碾压混凝土拱坝都考虑了分缝问题,缝的型式主要有诱导缝和横缝等。如普定拱坝采取的是坝肩一道正式横缝,坝体两道诱导缝的分缝型式。诱导缝内设有灌浆管,在缝张开时能够多次灌浆。沙牌拱坝的坝体分缝问题通过多个分缝方案进行比较,考虑到设诱导缝较简单,并可实现全断面通仓碾压施工,因此确定采用4条诱导缝的方案。
2.1.4.2 按坝体材料分区不同分类[2,6]
按照坝体材料分区的不同,碾压混凝土坝可分为以下两类:
(1)“金包银”型式的碾压混凝土坝 (RCD)。“金包银”型式的碾压混凝土坝的坝体内部采用碾压混凝土填筑,外部用常态混凝土 (一般2~3m厚)进行防渗和保护。如日本的岛地川坝、玉川坝,我国的水口坝、观音阁坝和白石坝等均采用了这种型式。某 “金包银”型式碾压混凝土坝断面如图2.2所示。
(2)全碾压混凝土坝型式 (RCC)。全碾压混凝土坝的坝体全断面采用碾压混凝土,利用碾压混凝土自身防渗或只在上游面设立薄膜防渗层。如美国的上静水坝,我国的普定坝和江垭坝等均采用了这种型式。江垭碾压混凝土重力坝横剖面如图2.3所示[2],该坝坝高128m,坝顶长度327m,大坝混凝土总量130万m3;大坝中部设中孔和表孔联合泄洪;坝体断面除在基础齿槽、垫层、溢流面、中孔及廊道周边、闸墩、导墙和坝顶细部结构等部位采用常态混凝土外,其他部位均采用碾压混凝土;坝体上游防渗层 (A1区)采用二级配富胶凝材料碾压混凝土 (90d龄期强度等级为C20,抗渗等级为 W12),坝体在高程190m以下 (A2区)采用三级配碾压混凝土 (90d龄期强度等级为C15),高程190m以上(A3区)为三级配碾压混凝土 (90d龄期强度等级为C10)。
图2.2 “金包银”型式碾压混凝土坝横剖面图 (单位:m)
(a)溢流坝段;(b)挡水坝段
图2.3 江垭碾压混凝土重力坝横剖面图 (单位:m)
(a)溢流坝段;(b)挡水坝段
1—中孔进水口;2—中孔弧门;3—表孔弧门;4—灌浆廊道;5—检查廊道;6—基础排水廊道
A1—二级配碾压混凝土;A2、A3—三级配碾压混凝土
上述两类按坝体材料分类的坝型,不同的国家根据本国的实际情况又一般采取不同的型式及坝体材料配比,存在一定的差异。日本、美国和中国碾压混凝土坝的常用型式及坝体材料配比的对比见表2.2[6]。
表2.2 日本、美国和中国碾压混凝土坝常用型式及坝体材料配比对比表

2.1.4.3 按胶凝材料用量分类[2]
按照胶凝材料用量的不同,碾压混凝土坝可分为以下几类:
(1)富浆碾压混凝土坝。这类坝的碾压混凝土中,胶凝材料用量为180~250kg/m3,其中混合材料占60%~75%,水胶比在0.5~0.7之间,多采用二级配。碾压混凝土的施工性能和硬化后的性能都好,尤其是层面结合质量好,有利于防渗,既可用作坝体的内部混凝土,也可用作坝体上游面防渗层。美国上静水坝是富浆碾压混凝土坝的代表,该坝使用的碾压混凝土中胶凝材料用量为246kg/m3,其中水泥用量76kg/m3,粉煤灰掺量达69%。上静水坝采用富浆混凝土的指导思想是:克服粗骨料分离,改善施工层面结合质量,提高混凝土抗剪性能以缩小坝体剖面。这类碾压混凝土坝存在的主要问题是混凝土的绝热温升较高,坝体温控有一定困难。
(2)中等胶凝材料碾压混凝土坝。这类坝的碾压混凝土中,胶凝材料用量为140~170kg/m3,其中混合材料占50%~70%。由于胶凝材料用量相对较少,水泥用量较低,碾压混凝土的绝热温升小,有利于温控,一般可用作坝体的内部混凝土,而在坝体上游面另设防渗层。我国大多数碾压混凝土坝是中等胶凝材料碾压混凝土坝。普定、江垭坝的碾压混凝土中,胶凝材料用量为150kg/m3,粉煤灰掺量占40%~60%,骨料为三级配。实践证明,这两座坝的施工性能良好。
(3)RCD坝。这类坝是日本特有的,其碾压混凝土中胶凝材料用量为120~130kg/m3,其中混合材料占25%~30%,水胶比在0.70~0.95之间。由于抗渗性能不高,只用作坝体内部混凝土,在坝体上游面常设置一定厚度的常态混凝土作为防渗层。
(4)贫浆碾压混凝土坝。这类坝的碾压混凝土中,胶凝材料的用量不超过110kg/m3,其中混合材料不超过30%,水胶比在0.95~1.50之间。这种碾压混凝土的强度较低,抗渗性及耐久性较差。然而作为坝体的内部混凝土,具有较好的低热性能。美国的柳溪坝、盖尔斯威尔坝等均采用的是这种混凝土。