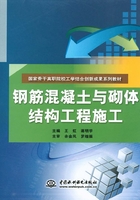
1.4.4 钢筋连接
钢筋连接方法有绑扎连接、焊接连接和机械连接。绑扎连接由于需要较长的搭接长度,浪费钢筋,且连接不可靠,故宜限制使用;焊接连接的方法较多,成本较低,质量可靠,宜优先选用;机械连接无明火作业,设备简单,节约能源,不受气候条件影响,可全天候施工,连接可靠,技术易于掌握,适用范围广。
1.4.4.1 绑扎连接
采用绑扎连接受力钢筋的绑扎搭接接头宜相互错开。绑扎搭接接头中钢筋的横向净距


不应小于钢筋直径,且不应小于25mm。
钢筋绑扎搭接接头连接区段的长度为1.3l1(l1为搭接长度),凡搭接接头中点位于该连接区段长度内的搭接接头均属于同一连接区段。同一连接区段内,纵向钢筋搭接接头面积百分率为该区段内有搭接接头的纵向受力钢筋截面面积与全部纵向受力钢筋截面面积的比值,如图1.92所示。同一连接区段内,纵向受拉钢筋搭接接头面积百分率应符合设计要求,无设计具体要求时,应符合下列规定。
图1.92 钢筋绑扎搭接接头连接区段及接头面积百分率
(图中所示搭接接头同一连接区段内的搭接钢筋为两根,各钢筋直径相同时,接头面积百分率为50%)
(1)对梁类、板类及墙类构件,不宜大于25%。(2)对柱类构件,不宜大于50%。
(3)当工程中确有必要增大接头面积百分率时,对梁类构件,不应大于50%;对其他构件可根据实际情况放宽。
纵向受力钢筋绑扎搭接接头的最小搭接长度应符合表1.40的规定。受压钢筋绑扎接头的搭接长度,应取受拉钢筋绑扎接头搭接长度的0.7倍。
表1.40
纵向受拉钢筋的最小搭接长度
注 两根直径不同钢筋的搭接长度,以较细钢筋的直径计算。
在梁、柱类构件的纵向受力钢筋搭接长度范围内,应按设计要求配置箍筋。当设计无具体要求时,应符合下列规定:箍筋直径不应小于搭接钢筋较大直径的0.25倍。受压搭接区段的箍筋间距不应大于搭接钢筋较小直径的10倍,且不应大于200mm。受拉搭接区段的箍筋间距不应大于搭接钢筋较小直径的5倍,且不应大于100mm。
(4)当柱中纵向受力钢筋直径大于25mm时,应在搭接接头两个端面外100mm范围内各设置两个箍筋,其间距宜为50mm。
1.4.4.2 焊接连接
钢筋焊接代替钢筋绑扎,可达到节约钢材、改善结构受力性能、提高工效、降低成本

的目的。常用的钢筋焊接方法有闪光对焊、电阻点焊、电弧焊、电渣压力焊、气压焊、埋弧压力焊等,各适用范围见附表6。
1.闪光对焊
钢筋闪光对焊是利用钢筋对焊机,将两根钢筋安放成对接形式,压紧于两电极之间,通过低电压强电流,把电能转化为热能,使钢筋加热到一定温度后,即施以轴向压力顶锻,产生强烈飞溅,形成闪光,使两根钢筋焊合在一起。
图1.93 钢筋闪光对焊原理
1—焊接的钢筋;2—固定电极;3—可动电极;4—机座;5—变压器;6—平动顶压机构;
7—固定支座;8—滑动支座
(1)钢筋闪光对焊工艺种类。钢筋对焊常用的是闪光焊(图1.93)。根据钢筋品种、直径和所用对焊机的功率不同,闪光焊的工艺又可分为连续闪光焊、预热闪光焊、闪光—预热—闪光焊和焊后通电热处理等。根据钢筋品种、直径、焊机功率、施焊部位等因素选用。
1)连续闪光焊。当钢筋直径小于25mm、钢筋级别较低、对焊机容量在80~160kV·A的情况下,可采用连续闪光焊。连续闪光焊的工艺过程,包括连续闪光和轴向顶端,即先将钢筋夹在对焊机电极钳口上,然后闭合电源,使两端钢筋轻微接触,由于钢筋端部凸凹不平,开始仅有较小面积接触,故电流密度和接触电阻很大,这些接触点很快熔化,形成“金属过梁”。“金属过梁”进一步加热,产生金属蒸汽飞溅,形成闪光现象,然后再徐徐移动钢筋保持接头轻微接触,形成连
续闪光过程,整个接头同时被加热,直至接头端面烧平、杂质闪掉。接头熔化后,随即施加适当的轴向压力迅速顶锻,使两根钢筋对焊成为一体。
2)预热闪光焊。由于连续闪光焊对大直径钢筋有一定限制,为了发挥对焊机的效用,对于大于25mm的钢筋,且端面较平整时,可采用预热闪光焊。此种方法实际上是在连续闪光焊之前,增加一个预热过程,以扩大焊接端部热影响区。即在闭合电源后使钢筋两端面交替接触和分开,在钢筋端面的间隙中发出断续的闪光而形成预热过程。当钢筋端部达到预热温度后,随即进行连续闪光和顶锻。
3)闪光—预热—闪光焊。这种方法是在预热闪光前,再加一次闪光的过程,使钢筋端部预热均匀。
4)通电热处理。RRB400级钢筋对焊时,应采用预热闪光焊或闪光—预热—闪光焊工艺。当接头拉伸试验结果发生脆性断裂,或弯曲试验不能达到规范要求时,应在对焊机上进行焊后通电处理,以改善接头金属组织和塑性。
通电热处理的方法是:待接头冷却至常温,将两电极钳口调至最大间距,重新夹住钢筋,采用最低的变压器级数,进行脉冲式通电加热,每次脉冲循环,应包括通电时间和间歇时间,一般为3s;当加热至750~850℃,钢筋表面呈橘红色时停止通电,随后在环境温度下自然冷却。

(2)对焊设备及焊接参数(图1.94)。
1)对焊设备。钢筋闪光对焊的设备是对焊机。对焊机按其形式可分为弹簧顶锻式、杠杆挤压弹簧顶锻式、电动凸轮顶锻式、气压顶锻式等。
2)对焊参数。为了获得良好的对焊接头,应合理选择恰当的焊数参数。闪光对焊工艺参数包括:调伸长度、闪光留量、闪光速度、顶锻留量、顶锻速度、顶锻压力及变压器级次。采用预热闪光焊时,还有预热留量和预热频率等参数。钢筋闪光对焊各项留量,如
图1.94所示。
图1.94 闪光对焊各项留量图解
L1、L2—调伸长度;a1+a2—烧化留量;b1+b2—预热留量;c1+c2—顶锻留量;
c′1+c′2—有电顶锻留量;c″1+c″2—无电顶锻留量;a1.1+a2.1—一次烧化
留量;a1.2+a2.2—二次烧化留量
3)调伸长度。它是指钢筋从电极钳口伸出的长度。调伸长度过长时,接头易旁弯、偏心;过短时,则散热不良,接头易脆断。甚至在电极处会发生熔化,同时冷却快,对中碳钢会发生淬火裂纹。所以,应随着钢筋牌号的提高和钢筋直径的加大而增长,主要是缓解接头的温度梯度,防止在热影响区产生淬硬组织。当焊接HRB400、HRB500等级别钢筋时,调伸长度宜在40~60mm内选用。
4)闪光留量。闪光(烧化)留量是指在闪光过程中,闪出金属所消耗的钢筋长度。闪光留量的选择,应根据焊接工艺方法确定。当连续闪光焊时,闪光过程应较长。烧化留量应等于两根钢筋在断料时切断机刀口严重压伤部分(包括端面的不平整度),再
加8mm。
闪光—预闪光焊时,应区分一次烧化留量和二次烧化留量。一次烧化留量应不小于10mm。预热闪光焊时的烧化留量应不小于10mm。
5)闪光速度(又称烧化速度)。它是指闪光过程进行的快慢,闪光速度应随钢筋直径的增大而降低。在闪光过程中,闪光速度是由慢到快,开始时接近于零,而后约为1mm/
s,终止时达1.5~2mm/s。这样的闪光比较强烈,能保证两根钢筋间的焊缝金属免受氧化。
6)预热留量。它是指采用预热闪光焊或闪光—预热—闪光焊时,在预热过程中所消耗的钢筋长度。其长度随钢筋直径增大而增加,以保证端部能均匀加热,并达到足够预热温度。宜采用电阻预热法。预热留量应为1~2mm,预热次数应为1~4次;每次预热时
间应为1.5~2s,间歇时间应为3~4s。
7)预热频率。对 HRB235级钢筋宜高些,一般为3~4次/s;对 HR8335级、HR8400级钢筋宜适中,一般为1~2次/s。
8)顶锻留量。它是指钢筋顶锻压紧后接头处挤出金属所消耗的钢筋长度。顶锻留量的选择,应使顶锻过程结束时,接头整个断面能获得紧密接触,并具有一定的塑性变形。在进行顶锻时,首先在有电流作用下顶锻,使接头加热均匀、紧密结合,以消除氧化作用,然后在无电流的作用下结束顶锻。因此,顶锻留量又分为有电顶锻留量和无电顶锻留量两项。随着钢筋直径的增大和钢筋级别的提高而增加,其中有电顶锻留量约占1/3,焊接RRB400级钢筋时,顶锻留量宜增大30%。顶锻留量应为4~10mm,并应随钢筋直径的增大和钢筋牌号的提高而增加。其中,有电顶锻留量约占1/3,无电顶锻留量约占2/3,焊接时必须控制得当。
焊接HRB500钢筋时,顶锻留量宜稍微增大,以确保焊接质量。生产中,如果有RRB400钢筋需要进行闪光对焊时,与热轧钢筋比较,应减小调伸长度,提高焊接变压器级数,缩短加热时间,快速顶锻,形成快热快冷条件,使热影响区长度控制在钢筋直径的0.6倍范围之内。
9)顶锻速度。它是指挤压钢筋接头时的速度。顶锻速度应越快越好,特别是在开始顶锻的0.1s内应将钢筋压缩2~3mm,使焊接口迅速闭合不致氧化;在断电后,以6mm/s的速度继续顶锻至终止。总之,顶锻速度要快,压力要适当。
10)变压器级次。它用以调节焊接电流的大小。应根据钢筋级别、直径、焊机容量及焊接工艺方法等具体情况选择。钢筋直径较小,焊接操作技术较熟练时,可选用较高的变压器级次,电压下降5%左右时,应提高变压器级次一级。
(3)对焊接头的质量检验。钢筋对焊完毕,应对接头质量进行外观检查和力学性能试验。
1)外观检查。钢筋闪光对焊接头的外观检查,应符合下列要求。a.每批抽查10%的接头,且不得少于10个。
b.焊接接头表面无横向裂纹和明显烧伤。c.接头处有适当的墩粗和均匀的毛刺。
2)拉伸试验。对闪光对焊的接头,应从每批随机切取6个试件,其中3个做拉伸试验,3个做弯曲试验,其拉伸试验结果,应符合下列要求。
a.3个试件的抗拉强度,均不得低于该级别钢筋的抗拉强度标准值。b.在拉伸试验中,至少有两个试件断于焊缝之外,并呈塑性断裂。
当检验结果有1个试件的抗拉强度低于规定指标,或有两个试件在焊缝或热影响区发生脆性断裂时,应取双倍数量的试件进行复验。复验结果,若仍有1个试件的抗拉强度不


符合规定指标,或有3个试件呈脆性断裂,则该批接头即为不合格。
3)弯曲试验。弯曲试验的结果,应符合下列要求。
a.由于对焊时上口与下口的质量不能完全一致,弯曲试验做正弯和反弯两个方向试验。
b.冷弯不应在焊缝处或热影响区断裂,否则不论其强度多高,均视为不合格。
c.冷弯后,外侧横向裂缝宽度不得大于0.15mm,对于 HRB400级钢筋,不允许有裂纹出现。当试验结果,有两个试件发生破断时,应再取6个试件进行复验。复验结果,当仍有3个试件发生破断,应确认该批接头为不合格品。
2.电弧焊
钢筋电弧焊是以焊条作为一级,钢筋为另一极,利用焊接电流通过上传产生的电弧热进行焊接的一种熔焊方法。其工作原理是:以焊条作为一极,钢筋为另一极,利用送出的低电压强电流,使焊条与焊件之间产生高温电弧,将焊条与焊件金属熔化,凝固后形成一条焊缝。
(1)钢筋电弧焊接头形式。钢筋电弧焊包括帮条焊、搭接焊、坡口焊、窄间隙焊和熔槽帮条焊等5种接头形式。
1)帮条焊。帮条焊时,用两根一定长度的帮条将受力主筋夹在中间,并采用两端点焊定位,然后用双面焊形成焊缝:宜采用双面焊[图1.95(a)];当不能进行双面焊时,方可采用单面焊[图1.95(b)]。帮条长度应符合:当帮条牌号与主筋相同时,帮条直径可与主筋相同或小一个规格;当帮条直径与主筋相同时,帮条牌号可与主筋相同或低一个牌号。
帮条焊接头或搭接焊接头的焊缝厚度s不应小于主筋直径的0.3倍;焊缝宽度b不应小于主筋直径的0.8倍。
图1.95 钢筋帮条焊接头
d—钢筋直径;l—帮条长度
图1.96 钢筋搭接焊接头
d—钢筋直径;l—搭接长度
2)搭接焊。搭接焊的焊缝厚度、焊缝宽度、搭接长度等技术参数,与帮条焊相同。焊接时应在搭接焊形成焊缝中引弧;在端头收弧前应填满弧坑,并使主焊缝与定位焊缝的

始端和终端熔合,如图1.96所示。
3)坡口焊。坡口焊有平焊和立焊两种接头形式(图1.97)。坡口尖端一侧加焊钢板,钢板厚度宜为4~6mm,长度宜为40~60mm。坡口平焊时,钢垫板宽度应为钢筋直径加10mm;坡口立焊时,钢垫板宽度宜等于钢筋的直径。
图1.97 钢筋坡口焊接头
钢筋根部的间隙,坡口平焊时宜为4~6mm,坡口立焊时宜为3~5mm,其最大间隙
均不宜超过10mm。
坡口焊接时,焊接根部、坡口端面之间均应熔合一体:钢筋与钢垫板之间,应加焊2~3层面焊缝,焊缝的宽度应大于V形坡口的边缘2~3mm,焊缝余高不得大于3mm,并平缓过渡至钢筋表面。焊接过程中应经常清渣,以免影响焊接质量。当发现接头中有弧坑、气孔及咬边等缺陷时,应立即补焊。
4)熔槽帮条焊。熔槽帮条焊是将两根平口的钢筋水平对接钢做帮条进行焊接。焊接时,应从接缝处垫板引弧后连续施焊,并使钢筋端部熔合,防止未焊透、气孔或夹渣等现象的出现。待焊平检查合格后,再进行焊缝余高的焊接,余高不得大于3mm,钢筋与角钢垫板之间,应加焊侧面焊缝1~3层,焊缝应饱满。
(2)电弧焊接头的质量检验。电弧焊的质量检验,主要包括外观检查和拉伸试验两项。
1)外观检查。电弧焊接头外观检查时,应在清渣后逐个进行目测,其检查结果应符合下列要求。
a.焊缝表面应平整,不得有凹陷或焊瘤。b.焊接接头区域内不得有裂纹。
c.坡口焊、熔槽帮条焊接头的焊缝余高,不得大于3mm。
d.预埋件T字接头的钢筋间距偏差不应大于10mm,钢筋相对钢板的直角偏差不得
大于4°。
e.焊缝中的咬边深度、气孔、夹渣等缺陷允许值及接头尺寸的允许偏差,应符合规范的规定。
外观检查不合格的接头,经修整或补强后,可提交二次验收。

2)拉伸试验。电弧焊接头进行力学性能试验时,在工厂焊接条件下,以300个同接头形式、同钢筋级别的接头为一批,从成品中每批随机切取3个接头进行拉伸试验,其拉伸试验的结果,应符合下列要求。
a.3个热轧钢筋接头试件的抗拉强度,均不得低于该级别钢筋的抗拉强度。b.3个接头试件均应断于焊缝之外,并应至少有2个试件呈延性断裂。
3.电渣压力焊
钢筋电渣压力焊是将钢筋安放成竖向对接形式,利用电流通过渣池产生的电阻,在焊剂层下形成电弧过程和电渣过程,产生电弧热和电阻热,将钢筋端部熔化,然后加压使两
根钢筋焊合在一起。适用于焊接直径14~40mm的热轧 HRB235级~HRB335级钢筋。
这种方法操作简单、工作条件好、工效高、成本低,比电弧焊节省80%以上,比绑扎连接和帮条搭接焊节约钢筋30%,可提高工效6~10倍。适用于现浇钢筋混凝土结构中竖
向或斜向钢筋的连接(图1.98~图1.100)。
图1.98 电渣焊构造
1、2—钢筋;3—固定电极;4—活动电极;5—药盒;6—导电剂;
7—焊药;8—滑动架;9—手柄;10—支架;11—固定
(1)焊接设备与焊剂。电渣压力焊的设备为钢筋电渣压力焊机,主要包括焊接电源、焊接机头、焊接夹具、控制箱和焊剂盒等。焊接电源采用BXz1000型焊接变压器;焊接夹具应具有一定刚度,使用灵巧,坚固耐用,上下钳口同心;控制箱内安有电压表、电流表和信号电铃,能准确控制各项焊接参数;焊剂盒由铁皮制成内径为90~100mm的圆形,与所焊接的钢筋直径大小相适应。
电渣压力焊所用焊剂,一般采用HJ431型焊药。焊剂在使用前必须在250℃温度下烘烤2h,以保证焊剂容易熔化,形成渣池。
焊接机头有杠杆单柱式和丝杆传动式两种。杠杆式单柱焊接机头,有单导柱夹具、手柄、监控表、操作把等组成。下夹具固定在钢筋上,上夹具利用手动杠杆可沿单柱上下滑动,以控制上钢筋的运动和位置。丝杆传动式双柱焊接机头,有伞形齿轮箱,手柄、升降丝杆、夹紧装置、夹具、双导柱等组成。上夹具在双导柱上滑动,利用丝杆螺母的自锁特


性,使上钢筋易定位,夹具定位精度高,卡住钢筋后无需调整对中度,电流通过特制焊把钳直接加在钢筋上。
图1.99 杠杆式单柱焊
1—钢筋;2—焊剂盒;3—单导柱;4—固定
夹头;5—活动夹头;6—手柄;7—监控
仪表;8—操作把;9—开关;10—控
制电缆;11—电缆插座
图1.100 杆传动式双柱焊接机头
1—伞形齿形轮箱;2—手柄;3—升降丝杆;4—夹紧装置;5—上夹头;
6—导管;7—双导柱;8—下
夹头;9—操作盒
(2)焊接参数。钢筋电渣压力焊的焊接参数,主要包括焊接电流、焊接电压和焊接通电时间,这3个焊接参数应符合规范有关规定。
(3)焊接工艺。钢筋电渣压力焊的焊接工艺过程,主要包括端部除锈、固定钢筋、通电引弧、快速施压、焊后清理等工序,具体工艺过程如下。
1)钢筋调直后,对两根钢筋端部120mm范围内,进行认真地除锈和清除杂质工作,以便于很好地焊接。
2)在焊接机头上的上、下夹具,分别夹紧上、下钢筋;钢筋应保持在同一轴线上,一经夹紧不得晃动。
3)采用直接引弧法或铁丝圈引弧法引弧。直接引弧法是通电后迅速将上钢筋提起,使两端头之间的距离为2~4mm引弧;铁丝圈引弧法是将铁丝圈放在上下钢筋端头之间,电流通过铁丝圈与上下钢筋端面的接触点形成短路引弧。
4)引燃电弧后,应先进行电弧过程,然后加快上钢筋的下送速度,使钢筋端面与液态渣池接触,转变为电渣过程,最后在断电的同时,迅速下压上钢筋挤出熔化金属和熔渣。
5)接头焊完毕,应停歇后,方可回收焊剂和卸下焊接夹具,并敲掉渣壳:四周焊包应均匀,凸出钢筋表面的高度应大于或等于4mm。
(4)电渣压力焊接头质量检验。电渣压力焊的质量检验,包括外观检查和拉伸试验。在一般构筑物中,应以300个同级别钢筋接头作为一批;在现浇钢筋混凝土多层结构中,应以每一

楼层或施工区段中300个同级别钢筋接头作为一批;不足300个接头的也作为一批。
1)外观检查。电渣压力焊接头,应逐个进行外观检查:其接头外观结果应符合下列要求。
a.接头处四周焊包凸出钢筋表面的高度,应大于等于4mm。b.钢筋与电极接触处,应无烧伤缺陷。
c.两根钢筋应尽量在同一轴线上,接头处的弯折角不得大于4°。
d.接头处的轴线偏移不得大于钢筋直径的0.1倍,且不得大于2mm。外观检查不合格的接头应切除重焊,或采取补强焊接措施。
2)拉伸试验。电渣压力焊接头进行力学性能试验时,应从每批接头中随机切取3个试件做拉伸试验。
4.气压焊(图1.101)
钢筋气压焊是利用氧乙炔火焰或其他火焰对两钢筋对接处加热,使其达到塑性状态或熔化状态,并施一定压力使两根钢筋焊合。这种焊接工艺具有设备简单、操作方便、质量优良、成本较低等优点,但对焊工要求严格,焊前对钢筋端面处理要求高,被焊两钢筋的直径差不得大于7mm。
图1.101 钢筋气压焊设备组成
1—氧气瓶;2—乙炔瓶;3—钢筋;4—焊接夹具;5—加压器;6—多嘴环形加热器
(1)焊接设备。钢筋气压焊的设备,主要包括氧、乙炔供气装置、加热器、加压器及焊接夹具等。
供气装置包括氧气瓶、溶解乙炔气瓶(或中压乙炔发生器)、十式回火防止器、减压器及输气胶管等。溶解乙炔气瓶的供气能力,应满足施工现场最大钢筋直径焊接时供气量的要求;当不能满足时,可采用多瓶并联使用。
加热器为一种多嘴环形装置,有混合气管和多火口烤枪组成。氧气和乙炔在混合室内按一定比例混合后,以满足加热圈气体消耗量的需要,应配置多种规格的加热圈,多束火焰应燃烧均匀,调整火焰应方便。
焊接夹具应能牢固夹紧钢筋,当钢筋承受最大轴向压力时,钢筋与夹头之间不得产生
相对滑移,应便于钢筋的安装定位,并在施焊过程中能保持其刚度。
(2)焊接工艺。钢筋处理、安装钢筋、喷焰加热、施加压力等过程。
1)气压焊施焊之前,钢筋端面应切平,并与钢筋轴线垂直。在钢筋端部2倍直径长度范围内,清除其表面上的附着物。钢筋边角毛刺及断面上的铁锈、油污和氧化膜等,应清除干净,并经打磨,使其露出金属光泽,不得有氧化现象。
2)安装焊接夹具和钢筋时,应将两根钢筋分别夹紧,并使两根钢筋的轴线在同一直线上。钢筋安装后应加压顶紧,两根钢筋之间的局部缝隙不得大于3mm。
3)气压焊的开始阶段采用碳化焰,对准两根钢筋接缝处集中加热,并使其内焰包住缝隙,防止端面产生氧化。当加热至两根钢筋缝隙完全密合后,应改用中性焰,以压焊面为中心,在两侧各1倍钢筋直径长度范围内往复宽幅加热。钢筋端面的加热温度,控制在1150~1300℃;钢筋端部表面的加热温度应稍高于该温度,并随钢筋直径大小而产生的温度梯差确定。
4)待钢筋端部达到预定温度后,对钢筋轴向加压到30~40MPa,直到焊缝处对称均匀变粗,其隆起直径为钢筋直径的1.4~1.6倍,变形长度为钢筋直径的1.3~1.5倍。气压焊施压时,应根据钢筋直径和焊接设备等具体条件,选用适宜的加压方式,目前有等压法、二次加压法和三次加压法,常用的是三次加压法。
(3)气压焊接头质量检验。钢筋气压焊接头的质量检验,分为外观检查、拉伸试验和弯曲试验三项。对一般构筑物,以300个接头作为一批:对现浇钢筋混凝土结构,同一楼层中以300个接头作为一批,不足300个接头仍作为一批。
1)外观检查。钢筋气压焊接头应逐个进行外观检查,其检查结果应符合下列要求。a.同直径钢筋焊接时,偏心量不得大于钢筋直径的0.15倍,且不得大于4mm;对不
同直径钢筋焊接时,应按较小钢筋直径计算。当大于规定值时,应切除重焊。
b.钢筋的轴线应尽量在同一条直线上,若有弯曲,其轴线弯折角不得大于4。
c.墩粗直径d不得小于钢筋直径的1.4倍,当小于此规定值时,应重新加热墩粗:墩粗长度L不得小于钢筋直径的1.2倍,且凸起部分应平缓圆滑。
d.压焊面偏移不得大于钢筋直径的0.2倍,焊接部位不得有环向裂纹或严重烧伤。2)拉伸试验。从每批接头中随机切取3个接头做拉伸试验,其试验结果应符合下列
要求。
a.试件的抗拉强度均不得小于该级别钢筋规定的抗拉强度。b.拉伸断裂应断于压焊面之外,并呈延性断裂。
当有1个试件不符合要求时,应再切取6个试件进行复验:复验结果,当仍有1个试件不符合要求时,应确认该批接头为不合格品。
3)弯曲试验。梁、板的水平钢筋连接中应切取3个试件做弯曲试验,弯曲试验的结果应符合下列要求。
a.气压焊接头进行弯曲试验时,应将试件受压面的凸起部分消除,并应与钢筋外表面齐平。弯心直径应比原材弯心直径增加1倍钢筋直径,弯曲角度均为90°。
b.弯曲试验可在万能试验机、手动或电动液压弯曲试验器上进行处在弯曲中心点,弯至900,3个试件均不得在压焊面发生破断。


当试验结果有1个试件不符合要求,应再切取6个试件进行复验。当仍有1个试件不符合要求,应确认该批接头为不合格品。压焊面应复验结果。
1.4.4.3 机械连接
钢筋的机械连接是指通过连接件的机械咬合作用或钢筋端面的承压作用,将一根钢筋的力传递至另一根钢筋的连接方法。钢筋机械连接方法,主要有钢筋锥螺纹套筒连接、钢筋套筒挤压连接、钢筋墩粗直螺纹套筒连接、钢筋滚压直螺纹套筒连接(直接滚压、挤肋滚压、剥肋滚压)等,经过工程实践证明,钢筋锥螺纹套筒连接和钢筋套筒挤压连接,是目前比较成功、深受工程单位欢迎的连接接头形式。
1.钢筋锥螺纹套筒连接
钢筋锥螺纹接头是一种新型的钢筋机械连接接头技术。国外在20世纪80年代已开始使用,我国于1991年研究成功,1993年被国家科委列入“国家科技成果重点推广计划”,此项新技术已在北京、上海、广东等地推广应用,获得了较大的经济效益(图1.102)。
图1.102 钢筋锥螺纹套筒连接
1—已连接的钢筋;2—银螺纹套简;3—待连接的钢筋
钢筋锥螺纹套筒连接是将所连钢筋的对接端头,在钢筋套丝机上加工成与套筒匹配的锥螺纹,将带锥行内丝的套筒用扭力扳手按一定力矩值把两根钢筋连接成一体。这种连接方法,具有使用范围广、施工工艺简单、施工速度快、综合成本低、连接质量好、利于环境保护等优点。
2.钢筋套筒挤压连接
带肋钢筋套筒挤压连接是将两根待接钢筋插入钢套筒,用挤压设备沿径向挤压钢套筒,使钢套筒产生塑性变形,依靠变形的钢套筒与被连接钢筋的纵、横肋产生机械咬合而成为一个整体的钢筋连接方法,如图1.103所示。由于是在常温下挤压连接,所以也称为钢筋冷挤压连接。这种连接方法具有操作简单、容易掌握、对中度高、连接速度快、安全可靠、不污染环境、实现文明施工等优点。
图1.103 钢筋套筒挤压连接
1—已挤压的钢筋;2—钢套筒;3—未挤压的钢筋