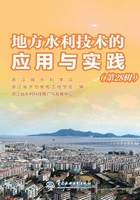
某泵站基坑开挖过程有限元模拟分析研究
翁新海1王 芊2翁郁馨3
(1.浙江省水利水电勘测设计院;2.广西电力设计研究院;3.浙江省工业大学建筑工程学院)
【摘 要】 本文以宁波某泵站基坑工程为例,用有限元软件的H-S模型对基坑的分步开挖过程进行模拟,了解基坑周边土体变形规律,为类似基坑开挖及支护工程提供依据。
【关键词】 深基坑;H-S模型;三维有限元
1 工程概况
强排泵站工程位于宁波市江东区江东南路东侧,小塘河北侧琴桥东公园内。工程由泵站、上游连接段、顶管工作井(兼作出水池)、出水管道、顶管接收井、出口涵管等组成。其中,设计泵站规模10m3/s,为3台立式潜水轴流泵,单泵设计流量为3.33m3/s,底板高程-1.95m,泵站为基坑,长15m,宽11.2m,基坑底部高程为-3.05m,基坑最深处为6.05m,基坑安全级别为三级。
2 场地工程地质条件
场地从上到下依次由人工填土、淤泥质黏土、粉质黏土等土层组成。
Ⅰ层:人工填筑土(r Q)。顶管工作井位置:ZK101揭露该孔位厚度为3.00m左右,其中厚度0~0.05m为硬塑料地板,厚度0.05~0.25m为混凝土块,厚度0.25~1.20m为杂填土,由碎石、碎砖块和混凝土块组成,粒径5~25cm、厚度1.20~3.00m为含泥碎石。
Ⅱ层:淤泥质黏土(m Q4)。灰色,饱和,流塑状态,厚层状,高压缩性,切面光滑,干强度高,韧性高,无摇振反应,偶夹黑色腐殖质,该层场地内均有分布,顶板高程-0.41~0.65m,层厚10.70~14.40m。
Ⅳ层:粉质黏土夹粉土。局部相变为黏质粉土(m Q4)灰色,粉土稍湿,粉质黏土呈可塑~软塑,切面稍粗糙,干强度中等,韧性中等,无摇振反应。该层场地内大部分地段有分布,层厚2.10~4.40m。
土层物理力学指标建议值表见表1。
表1 土层物理力学指标建议值表

3 几何模型建立
基坑长15.6m、宽11.2m、深6.05m,属于三级工程,根据基坑的实际尺寸,首先用PLAXIS 2D建立几何模型进行模拟分析。接着确定模型的土层边界,土层边界长度选定3倍基坑长度,土层边界定为宽50m、深40m,根据实际的钻孔柱状图,划分不规则的土层,同时确定标准固定边界,下边界任意方向变形为零,左右两边限制了水平位移。在拉森钢板桩周围建立了界面单元。
土层从上至下分别为人工填筑土、淤泥质黏土、粉质黏土、粉质黏土(第二层)以及黏质粉土,土层各个变化节点严格按照实际钻孔柱状图进行,左右两侧的板结构为拉森钢板桩,长度为15m,桩顶在地表处,嵌固深度为9m。周围正负号代表了界面单元,用来模拟钢板桩与土接触位置的折减,两侧T形点对点锚杆代表的是横向钢支撑,锚杆间距是一半的基坑宽度。其中第二层土的实线代表基坑的底部高程-3.05m。各层土的参数根据土工试验数据见表2。
表2 岩土数据组参数

土体模型所需要的岩土数据参数是根据现场钻孔取出的岩芯进行土工试验得到的数据,其中各土层的渗透系数见表3。
在基坑支护结构的数值模拟中,钢板桩墙由板结构来模拟,其中板单元的主要参数有轴向刚度EA、抗弯刚度EI、泊松比ν、容重w、被动土压力弯矩Mp、主动土压力弯矩Np,具体见表4。横向钢支撑由点对点锚杆进行模拟,锚杆数据组参数见表5。
表3 土层渗透系数

表4 板单元数据组参数

表5 锚杆数据组参数

有限元网格划分如图1所示,有限元程序在建立好模型与定义材料信息之后,能够自动生成有限元网格,在PLAXIS 2D中网格主要有6节点单元和15节点单元两种,本次选择全局加密程度为中等,并在拉森钢板桩周围加密网格,共划分了5853个节点,692个单元,8304个应力点。有限元网格划分是执行计算前必不可少的操作步骤,网格划分的好坏对计算结果有着直接的影响。

图1 有限元网格划分
几何模型建立好之后进行初始条件计算的步骤。此工程在进行施工时基坑底部土体为弱透水性,没有渗透和渗流等问题,并且施工过程为干挖,故不考虑孔隙水压,地下水位线设置在基坑底部。PLAXIS中初始地应力的生成包括K0过程和重力加载两种方式。K0过程只适用于基坑底部、基坑表面土体和地下水头均保持水平的情况。但本文模拟的基坑土层为不均匀土层,因此采用重力加载的办法来生成初始应力。重力加载方法将使初始应力的计算产生位移。由初始应力计算出的位移实际上并不存在,由于基坑是按实际情况模拟的,因此初始应力不影响后续开挖步骤,选择重置位移为零即可。本工程一共有四个计算步骤:①重力加载过程生成初始应力;②重置位移为零并设置钢板桩及开挖第一层土,高程为0m;③在0m的高程上安装横向钢支撑;④开挖至基坑底部,高程为-3.05m。
4 H-S模型计算结果分析
选用H-S强化土模型进行计算,土体黏聚力c以及内摩擦角φ的取值与M-C模型下的取值相同,不同的是3个模量的取值,其中主固结仪加载中的切线刚度为高级参数,一般取3倍的割线刚度。同时强化土模型增加了刚度应力水平相关幂指数以及卸载-重加载泊松比,本案例均选用缺省值。PLAXIS 2D中H-S模型所使用的岩土数据组参数见表6。
表6 H-S模型的岩土数据组参数

Hardening-Soil强化土模型下各施工步骤下塑性点位置如图2~图4所示。与摩尔-库仑M-C模型总体分布规律相似,由图2~图4可得:不同施工步骤下塑性区域的变化以及基坑水平位移都发生了较大的变化。
如图2所示,可以看出摩尔-库仑点的分布位置主要在基坑开挖面与钢板桩结构接触的位置,拉伸截断点主要位于两侧钢板桩后的地表区域,而强化点的位置主要分布在开挖面以下一定深度的土层内并呈拱形。

图2 第二计算步骤下塑性点位置

图3 第三计算步骤下塑性点位置

图4 第四计算步骤下塑性点位置
如图3所示,安装钢支撑之后,可以发现塑性区域有较为明显的减小,摩尔-库仑点消失,拉伸截断点零散地分布在地表位置,并向远离基坑的方向移动,强化点依然存在在基坑开挖面以下,帽盖强化点与强化点的区域也变小并且变得分散。
如图4所示,开挖至基底,即基底高程为-3.05m时,摩尔-库仑点仍然出现在开挖面以下与钢板桩结构相接触的位置,且摩尔-库仑点分布的区域变大,向钢板桩内侧一定深度土体延伸。拉伸截断点继续朝着远离基坑一侧移动,强化点则均匀地填满拉森钢板桩长度范围以内基坑开挖面以下的土层,并向基坑底部以下的土层延伸。
对比以上各施工工序下的水平位移云图如图5~图7所示,可以看出安装钢板桩并开挖土体至0m高程时,基坑水平位移为40.11mm,最大位移产生的位置在基坑左侧与拉森钢板桩相接触的地表位置,左右两侧位移分布规律相同,安装钢支撑之后,基坑水平位移为40.12mm,数值与第一步相差不大,最大位移产生的位置也没有改变,但是左侧水平位移的影响范围略有减少,这是由于钢支撑的安装对水平位移的控制具有很好的作用,限制了水平位移的进一步发展。如图7所示,开挖完成之后,基坑最大水平位移为37.09mm,比上两步都减小,可以看出此时钢支撑对减小基坑水平位移的效果,但是影响范围随着土层开挖深度的提高也扩大了,此时最大水平位移发生的位置移动到右侧开挖面与钢板桩接触的位置并向上下两侧逐渐减小,影响的区域逐渐向远离基坑的位置扩散并随着距离的增加逐渐减小,左右两侧形成一个对称的分布规律。

图5 开挖第一层土时基坑水平位移云图

图6 安装钢支撑时基坑水平位移云图

图7 开挖至高程为-3.05m时基坑水平位移云图
5 模拟数据与实测变形数据对比分析
水平位移的变化量很好地反映了基坑的变形,是衡量基坑稳定性的重要数据。根据监测数据确定测斜钻孔CL101在几何模型中的位置,对比模拟结果中CL101位置处X方向水平位移的变化值与监测数据是否吻合。测斜管最大位移数据表见表7。基坑周围土体Y方向水平位移图如图8所示。
表7 CL101测斜孔最大位移数据表

基坑北侧CL101孔,在PLAXIS 3D分析下得出在X方向的最大位移为6.5mm,可以看出最大位移产生的位置均在地表处。而从监测结果得到CL101孔的最大日增量为3mm,累计最大水平位移为8.3mm,并且发生在管口1.5m处,与模拟分析的数值差距不大,但发生的位置略有差异。
由图8可以看出,基坑周边土体水平位移在钢支撑所在一侧即基坑南侧达到最大值,为90.34mm,在基坑北侧达到的最大值为61.95mm,且随着深度加深水平位移变化趋势也是相似的,均在-2~-3m处达到最大值。与监测数据水平位移图相比较,分布趋势较为一致。

图8 基坑周边土体Y方向水平位移图
6 结语
整个工程基坑开挖过程分析较少,基坑支护设计往往比较保守,用PLAXIS对整个开挖过程进行了模拟,了解基坑开挖过程中土体的变形规律,模型分析结果与工程实际情况的吻合性较好,通过对开挖过程的模拟分析,可以作为基坑支护的设计依据。
参考文献
[1] 曹明杰,曹鑫,徐政治.泵站基坑开挖中的地下连续墙有限元结构计算[J].南水北调与水利科技,2014(6):204-208.
[2] 陈书申,詹素华.开挖深度悬殊的相邻基坑的支护稳定分析[J].福建建筑高等专科学校学报,2002,2:63-65.
[3] 刘宗振,王岩.基于PLAXIS 3D的板桩墙基坑支护数值模拟[J].当代化工,2014,(8):1580-1583.