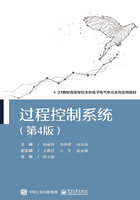
3.4 气动调节阀的选型

第14讲
调节阀是自动控制系统的执行部件,其选择对控制质量有较大的影响。调节阀选型中,一般应考虑以下几点:
①根据工艺条件,选择合适调节阀的结构形式和材质。
②根据工艺对象的特点,选择合理的流量特性。
③根据工艺参数,计算出流量系数,选择合理的阀口径。
下面仅就上述提出的问题进行简要的论述。
3.4.1 调节阀结构形式的选择
不同结构的调节阀有其各自的特点,适应不同的需要。在选用时,要注意:
①工艺介质的种类、腐蚀性和黏性;
②流体介质的温度、压力(入口和出口压力)、比重;
③流经阀的最大、最小流量,正常流量及正常流量时阀上的压降。
在一般情况下,应优先选用直通单、双座调节阀。直通单座阀一般适用于泄漏量要求小和阀前、后压降较小的场合;直通双座阀一般适用于对泄漏量要求不严和阀前、后压降较大的场合,但不适用于高黏度或含悬浮颗粒的流体。
对于高黏度或含悬浮颗粒的流体,气-液混相或易闪蒸的液体,以及要求直角配管的场合,可选用角形阀。
对于浓浊浆液和含悬浮颗粒的流体以及在大口径、大流量和低压降的场合,可选择蝶阀。
三通调节阀既可用于混合两种流体,又可以将一种流体分为两股,多用于换热器的温度控制系统。
隔膜阀具有结构简单、流道阻力小、流通能力大、无外漏等优点,广泛用于高黏度、含悬浮颗粒、纤维及有毒的流体。
此外,根据需要还可选用波纹管密封阀,低噪声阀、自力式调节阀等。对于特殊工艺生产过程,还需选用专用调节阀。其他阀型及适用范围可参阅有关参考文献。
3.4.2 调节阀气开与气关形式的选择
在调节阀气开与气关形式的选择上,应根据具体生产工艺的要求,主要考虑当气源供气中断或调节阀出现故障时,调节阀的阀位(全开或全关)应使生产处于安全状态。例如,进入工艺设备的流体易燃易爆,为防止爆炸,调节阀应选气开式。如果流体容易结晶,调节阀应选气关式,以防堵塞。
通常,选择调节阀气开、气关形式的原则是不使物料进入或流出设备(或装置)。一般来说,要根据以下几条原则进行选择。
①首先要从生产安全出发。当出现气源供气中断,或因控制器故障而无输出,或因调节阀膜片破裂而漏气等故障时,调节阀无法正常工作以致阀芯恢复到无能源的初始状态(气开阀恢复到全关,气关阀恢复到全开),应能确保生产工艺设备的安全,不致发生事故。例如,锅炉的汽包液位控制系统中的给水调节阀应选用气关式。这样,一旦气源中断,也不致使锅炉内的水蒸干。而安装在燃料管道上的调节阀则大多选用气开式,一旦气源中断,则切断燃料,避免发生因燃料过多而出现事故。
②从保证产品质量出发。当因发生故障而使调节阀处于失气状态时,不应降低产品的质量。例如,精馏塔的回流调节阀应在出现故障时打开,使生产处于全回流状态,防止不合格产品的蒸出,从而保证塔顶产品的质量,因此,选择气关阀。
③从降低原料、成品和动力的损耗来考虑。如控制精馏塔进料的调节阀就常采用气开式,一旦调节阀失去能源(即处于全关状态),就不再给塔进料,以免造成浪费。
④从介质的特点考虑。精馏塔塔釜加热蒸汽调节阀一般选气开式,以保证在调节阀失气时能处于全关状态,从而避免蒸汽的浪费和影响塔的操作。但是如果釜液是易凝、易结晶、易聚合的物料,调节阀则应选择气关式,以防调节阀失气时阀门关闭、停止蒸汽进入而导致再沸器和塔内液体的结晶和凝聚。
当以上选择阀气开、气关形式的原则出现矛盾时,主要要从工艺生产的安全出发。当仪表供气系统故障或控制信号突然中断,调节阀阀芯应处于使生产装置安全的状态。
3.4.3 调节阀流量特性的选择
目前国产调节阀流量特性有直线、等百分比和快开三种。它们基本上能满足绝大多数控制系统的要求。快开特性适用于双位控制和程序控制系统。调节阀流量特性的选择实际上是指直线和等百分比特性的选择。
选择方法大致可归结为理论计算方法和经验法两类。但是,这些方法都较复杂,工程设计多采用经验准则,即从控制系统特性、负荷变化和阀阻比S值大小三个方面综合考虑,选择调节阀流量特性。
1.从改善控制系统控制质量考虑
线性控制回路的总增益,在控制系统整个操作范围内应保持不变。通常,测量变送装置的转换系数和已整定好的控制器的增益是一个常数。但有的被控对象特性却往往具有非线性特性。例如,对象静态增益随操作条件、负荷大小而变化。因此,可以适当选择调节阀特性,以其放大系数的变化补偿对象增益的变化,使控制系统总增益恒定或近似不变,从而改善和提高系统的控制质量。例如,对于增益随负荷增大而变小的被控对象应选择放大系数随负荷增加而变大的调节阀特性。如匹配得当,就可以得到总增益不随负荷变化的系统特性,被控对象与调节阀的匹配如图3-21所示。等百分比特性调节阀正好满足上述要求,因而得到广泛采用。

1—对象静态特性;2—调节阀流量特性;3—补偿后的特性
图3-21 被控对象与调节阀的匹配
2.从配管状况(S100值大小)考虑
调节阀总是与设备、管道串联使用,其工作流量特性不同于调节阀理想流量特性,必须首先根据“l”中的要求选择希望的工作流量特性,然后考虑工艺配管状况,最后确定调节阀流量特性。表3-5可供选用时参考。
表3-5 配管状况与阀工作流量特性关系

由表3-5可以看出,当阀阻比S100=1~0.6时,调节阀理想流量特性与希望的工作流量特性基本一致;但在阀阻比S100=0.6~0.3时,如果希望的工作流量特性为直线型,则考虑配管状况(S100值大小)后,应选择理想流量特性为等百分比特性的调节阀。
对于被控对象特性尚不十分清楚的情况,建议参考表3-6的选择原则,确定调节阀流量特性。
表3-6 调节阀理想流量特性选择原则

注:为正常流量时的阀压降;
为管道系统总压降;
为正常阀阻比。
3.4.4 调节阀口径的确定
调节阀口径的选择非常重要,它直接影响工艺生产的正常运行、控制质量及生产的经济效果。选择口径过小,则调节阀最大开度下达不到工艺生产所需的最大流量。选择口径过大,则正常流量下调节阀总是工作在小开度下,调节阀的调节特性不好,严重时可导致系统不稳定。另外,还会增加设备投资,造成资金浪费。因此必须根据工艺参数认真计算口径,选择合适的调节阀。
目前选定调节阀口径的通用方法是流通能力法(简称C值法)。因此调节阀口径的选择实质上就是根据特定的工艺条件(即给定的介质流量、调节阀前后的压差及介质的物性参数)进行流量系数C的计算,然后再按C值选择调节阀的口径,使得通过调节阀的流量满足工艺要求的最大流量且留有一定的裕量。
该方法首先利用给定的条件和参数,计算出最大流量系数,并对其进行圆整;然后根据圆整后的额定流量系数
的值,查表3-1决定阀的口径(公称直径Dg和阀座直径dg);最后再对选定的阀进行开度和可调比验算。选定调节阀口径的具体步骤如下。
1.确定计算流量系数需要的主要数据
为了计算出流量系数C的值,必须首先确定所需的各项参数,如最大流量、正常流量和最小流量;阀前压力、阀后压力;阀阻比;流体密度及其他修正系数等。
(1)正常流量和最大流量
正常流量就是工艺装置在额定工况下稳定运行时流经调节阀的流量,用来计算阀的正常流量系数
。
最大流量是计算最大流量系数
的一个重要参数,它通常为工艺装置运行中可能出现的最大稳定流量的1.15~1.5倍。最大流量与正常流量之比
不应小于1.25。当然,也可以由工艺装置的最大生产能力直接确定
。它如果选得过小,将不能满足生产要求,如果选得过大,将会使调节阀经常处于小开度下工作,可调范围变小,严重时会引起系统振荡、噪声大,系统不稳定和降低阀芯的寿命,尤其是高压调节阀更要注意这一点。
(2)阀压降
阀压降的确定关系到阀径计算选定的正确性、控制特性的好坏和设备动力消耗的经济性。阀压降对于简单的压力、液位控制系统较容易确定。对复杂的控制系统必须使用计算机求得或用实验确定。根据不同的已知条件,阀压降
通常采用以下几种方法确定。
①利用阀阻比S100确定阀压降。
根据式(3-28)给定的全开阀阻比S100的计算公式,可得调节阀全开时的压降为

(3-47)
式中,为调节阀全开时的压降;
为管道系统中除调节阀外其余各部分压降之和。
在计算流量系数时,阀压降可用调节阀全开时的压降
近似代替。
②按管路系统中阀前后定压点的压差确定阀压降Δp。
定压点就是在该点处压力不随流量的变化而改变。阀前定压点,如车间总管、风机出口,阀前总管等;阀后定压点,如炉膛压力、喷嘴前压力、容器内压力或需要保持的某点压力等。设阀前定压点压力为,阀后定压点压力为
,则

③如已知原动机(风机、泵等)的特性和管路系统的阻力变化特性,原动机特性和管路特性曲线如图3-22所示,则阀的计算压差为流量在给定的最大值时具有的二者的压力差,即

式中,为原动机在
下的最小压力;
为管路系统在
下的最大压力。
④如已知或测得最大流量时管路系统的阻损及管路起点可能的最小压力
,则阀的计算压差可由下式确定。

⑤要求阀前后保持恒压的系统,如已知管路中阀前可能的最小压力和控制器整定值的范围
和
,这时阀的计算压差可由下式确定。

⑥如已知阀开度最小时的最小流量和阀压差
,以及阀开度最大时的最大流量
,可根据下式计算压差。

⑦当没有条件仔细计算阀压降时,也可以根据工艺管道的直径D来估算阀的公称直径Dg。一般调节阀的公称直径Dg可等于或小于管道直径D的0.5~0.75倍,即

但这时工艺管道内流体的流速最好不要超过表3-7所示范围。

图3-22 原动机特性和管路特性曲线
表3-7 管道内流体的正常流速

2.求调节阀应具有的最大流量系数
①如果工艺提供的流量为最大流量,在计算最大流量时阀压降为
,则根据表3-2中的公式计算得到的流量系数C即为最大流量系数
。
②如果工艺提供的流量为正常流量,在正常流量条件时阀压降
,则根据表3-2中的公式计算得到的流量系数C即为正常流量系数
的值。它与最大流量系数
的关系如下。

式中,m称为流量系数放大倍数,它由式(3-48)确定。

(3-48)
式中,为最大流量与正常流量之比;
为正常阀压降与管道系统总压降之比,即正常阀阻比;
为计算最大流量时的阀阻比。
● 对于调节阀上下游均有恒压点的场合

(3-49)
● 对于装在风机或离心泵出口的调节阀,其下游有恒压点的场合

(3-50)
式中,为流量由正常流量增大到计算最大流量时风机或泵出口压力的变化值。
3.对最大流量系数进行圆整确定额定流量系数
根据选定的调节阀类型,在该系列调节阀的各额定流量系数中,选取不小于并最接近最大流量系数的一个作为选定的额定流量系数,即C100。
4.选定调节阀口径
根据与上述选定的额定流量系数值,利用表3-1确定与其相对应的调节阀口径Dg和dg,即为选定的调节阀公称直径和阀座直径。
5.调节阀相对开度的验算
由于在选定值时是根据标准系列进行圆整后确定的,故需要对计算时的最大流量
进行开度验算。调节阀工作时其相对开度应处于表3-8所示范围。
表3-8 调节阀相对开度范围

阀门的最小开度不能太小,否则流体对阀芯、阀座冲蚀严重,容易损坏阀芯,致使特性变坏,甚至调节失灵。最大开度也不能过小,否则将调节范围缩小,阀门口径偏大,调节特性变差,不经济。
对于直线特性和等百分比特性的调节阀,其相对开度进行验算公式分别为

式中,C为不同相对行程l时,阀的相应流量系数;R为调节阀可调范围,目前国产阀一般为30,也有50的,但很少使用。
6.调节阀可调比验算
对于选定的调节阀也要对其可调比进行验算。串联管系中工作的调节阀可以通过式(3-44),即

验算其可调比。
①对于调节阀上、下游均有恒压点的场合

②对于调节阀装于风机或离心泵出口,而下游又有恒压点的场合

【例3-1】某控制系统拟选用一台直线特性气动直通单座调节阀(流开形)。已知流体为液氨。最大计算流量条件下的数据为:=26200kPa;
=24500kPa;
=10.86m3/h;
=0.58kg/m3;
=0.1964×10-6m2/s;
=20mm。
解:由液体理化数据手册查得=l1378kPa;
=1621kPa。
(1)阻塞流判别
由表3-3查得柱塞形单座调节阀(流开形)的=0.9,则

产生阻塞流最小压降

因为,故为阻塞流。
(2)Cmax值计算
根据表3-2知流量系数的计算机公式为

(3)低雷诺数修正

由于Re>3500,故以上计算出的流量系数不必作低雷诺数修正。
(4)初选Cl00值
查表3-1得知,额定流量系数比0.583大且最接近的一个为C100=0.8,对应的单座阀公称直径Dg=3/4'',阀座直径dg=8mm。
(5)管件形状修正
因为D1/Dg=20/19=1.05,所以不必作此项修正。
(6)调节阀相对开度验算
调节阀为直线特性,最大流量时的相对开度

<80%,可满足要求。
(7)调节阀可调比验算
由于没有提出Qmax/Qmin的要求,对调节阀的可调比不作验算。
【例3-2】某化肥厂合成氨车间拟选一台气动单座调节阀(流开形)。已知流体为氨气。正常流量条件下的数据为:=410kPa;
=330kPa;
=271.5K;
=252m3/h;
=0.771kg/m3;
=0.7;n=1.3;
=25mm;Qmax/Qmin=16。
解:由气体理化数据手册查得Z=1;k=1.32。
(1)阻塞流判别
查表3-3知柱塞形单座调节阀(流开形)的=0.72,则

由于,故为阻塞流。
(2)Cn值计算
根据表3-2知流量系数的计算公式为

(3)Cmax值计算



(4)口径选定
由表3-1中选C100=5,对应的调节阀口径Dg=dg=20mm。
(5)管件形状修正
因为D1/Dg=25/20=1.25,所以不必作此项修正。
(6)调节阀相对开度验算
对于直线特性调节阀,其正常流量时开度

因此满足要求。
(7)调节阀可调比验算
假设调节阀上下游均有恒压点,则


足以满足Qmax/Qmin=16的要求。
【例3-3】某蒸汽厂选择气动双座调节阀(流开形)。已知流体为过热蒸汽。正常流量条件下的数据为:=1500kPa;
=100kPa;
=368℃;Ws=400kg/h;
=5.09kg/m3;
=0.48;n=1.25;
=45mm;Qmax/Qmin=9。
解:由气体理化数据手册查得k=1.29。
(1)阻塞流判别
查表3-3知柱塞形双座调节阀的=0.70,则

由于,故为非阻塞流。
(2)Cn值计算


(3)Cmax值计算



(4)口径选定
由表3-1中选C100=16,对应的调节阀口径Dg=dg=32mm。
(5)管件形状修正
因为D1/Dg=45/32=1.4,所以对双座阀可不必作此项修正。
(6)调节阀相对开度验算
对于等百分比特性的调节阀,其正常流量和最大流量时的相对开度分别为


因此满足要求。
(7)调节阀可调比验算
假设调节阀上下游均有恒压点,则


满足Qmax/Qmin=9的要求。