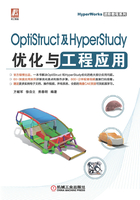
2.7 工程实例
2.7.1 轨道支撑柱安装位置优化(1D)
为了在山坡上建造图2-97所示的类似过山车轨道的结构,需要在轨道的下方安装一些z方向的金属支撑柱,由于不同位置的载荷大小、方向各不相同,本例对支撑柱的安装位置进行优化。轨道部分作为非设计空间保留。本例使用梁单元。
优化需要考虑40个工况,每个工况的位移约束都是支撑柱底部的全约束,每个工况载荷的施加位置及大小方向各不相同。

图2-97 类似过山车轨道的结构模型

操作视频
优化三要素
优化目标:最小化轨道的最大位移。
设计约束:设计空间的剩余体积小于50%。
优化变量:所有支撑柱单元。
操作步骤
Step 01 创建设计变量,props只选择support_design,如图2-98所示。

图2-98 创建拓扑优化设计变量
Step 02 创建体积百分比响应,props只选择support_design,如图2-99所示。

图2-99 创建体积百分比响应
Step 03 创建位移响应,nodes选择轨道上的所有节点,如图2-100所示。

图2-100 创建位移响应
Step 04 创建位移的目标参考,如图2-101所示。neg reference表示响应为负值时的参考值,这里未设置,使用默认值-1.0。pos reference表示响应为正值时的参考值,这里设置为1.0。因为OptiStruct只能进行单目标优化,所以需要先把多个目标进行加权计算得到一个目标。这里设置的就是参考值ri,Wi是响应值。最终的优化响应公式为


图2-101 创建位移目标参考
Step 05 创建优化目标为最小化最大位移,如图2-102所示。

图2-102 创建优化目标
Step 06 提交计算并查看优化结果。为了更好地显示梁单元,在HyperView的Preferences>Options下拉菜单中将所有1D单元显示为圆柱,如图2-103所示。
优化结果密度云图如图2-104所示。

图2-103 显示梁单元为圆柱

图2-104 优化结果密度云图
2.7.2 使用加权柔度响应进行多工况模型的拓扑优化(2D)
本例主要介绍如何使用加权柔度响应进行多工况模型的拓扑优化,模型如图2-105所示。

图2-105 优化模型

操作视频
优化三要素
优化目标:最小化加权柔度。
设计约束:优化区域的体积百分比小于20%。
设计变量:其余所有单元。图2-105中垫圈区域和底部弯钩为非设计区域。
操作步骤
Step 01 打开bracket1_start.hm。
Step 02 创建拓扑优化设计变量。进入Analysis>optimization>topology面板的create子面板,设置如图2-106所示,props激活后在模型中选择design,单击create按钮完成创建。

图2-106 创建拓扑优化设计变量
Step 03 创建加权柔度响应。进入Analysis>optimization>responses面板,设置响应类型为weighted comp,单击loadsteps设置加权系数都为1.0,然后单击create按钮创建加权柔度响应,如图2-107所示。

图2-107 创建加权柔度响应
Step 04 创建体积百分比响应。设置响应类型为volumefrac,单击create按钮创建体积百分比响应,如图2-108所示。

图2-108 创建体积百分比响应
Step 05 创建设计约束。进入Analysis>optimization>dconstraints面板,response选择volfrac,upper bound设置为0.2,如图2-109所示。

图2-109 创建体积百分比约束
Step 06 创建优化目标。进入Analysis>optimization>objective面板,response选择wcomp,如图2-110所示。

图2-110 创建优化目标
Step 07 提交优化计算。进入Analysis>OptiStruct面板,设置如图2-111所示。从求解器的对话框中单击Results按钮打开后处理。

图2-111 提交优化计算
Step 08 结果后处理。单击HyperView工具栏上的contour按钮,然后单击Apply按钮显示云图。单击HyperView工具栏上的Iso按钮,然后单击Apply按钮显示iso图,如图2-112所示。

图2-112 包含云图的优化结果密度iso图
从优化已经大致可以看出材料的分布方式,但是存在一些问题。
1)右侧两个螺栓孔附近完全没有材料,原因是分析模型中假定螺栓孔1~6自由度的约束刚度是无穷大。实际上,螺栓的承载能力也是有限的,可以施加约束反力作为设计约束。如果实际上是销钉或剪切螺栓,螺栓部位实际上是可以绕轴转动的,这样可以把更多的载荷传到右侧的螺栓。
2)材料的多少无法确定,因为没有考虑详细的位移和应力约束。
3)无法反映厚度方向的材料分布,如果零件最终是铸造件,这样的优化是不合理的。
对于注塑件或者焊接的钢板,经常通过增加加强筋的方式提高刚度。下面仍然针对上述模型进行2D拓扑优化设计变量的基准厚度(Base Thickness)设置,如图2-113所示,这里还添加了成员尺寸约束(Mindim和Maxdim,可选)。新的优化结果如图2-114所示。由于有基准厚度存在,优化结果中下半部分的材料基本都移除了。

图2-113 设计变量设置

图2-114 新的优化结果云图
2.7.3 转向节与挂钩结构拓扑优化(3D)
1.转向节结构优化
图2-115所示转向节是汽车的重要零件,需要考虑多种工况,零件制造方式为压铸,因此,优化时需要考虑铸造件的拔模问题。螺栓等与外部连接的部位必须作为非设计空间保留。
转向节优化需要考虑7个工况,具体请参考分析文件。各载荷作用点与结构上孔的连接位置如图2-116所示。可以认为载荷作用点与孔的内壁相连。希望降低重量,但结构的应力不能超过200MPa。本例会用到拔模约束和多工况加权柔度响应。
优化三要素
优化目标:最小化加权柔度。
设计约束:设计空间的剩余体积小于20%。
优化变量:设计空间的所有单元。

操作视频
操作步骤
Step 01 使用HyperMesh或者其他CAD软件(如Evolve)创建优化空间。本例的模型是优化空间的网格,构建好的模型如图2-117所示。

图2-115 转向节结构

图2-116 载荷作用点及连接位置

图2-117 优化空间网格模型
Step 02 创建设计变量,props只选择Design,设置如图2-118所示。还需要设置y方向拔模(使用draw面板),type为split。为了改善优化效果,设置最小成员尺寸为1.0。

图2-118 创建设计变量
Step 03 创建体积百分比响应,如图2-119所示。

图2-119 创建体积百分比响应
Step 04 创建加权柔度响应。各个工况的加权系数如图2-120所示。

图2-120 创建加权柔度响应
Step 05 创建体积百分比约束,如图2-121所示。

图2-121 创建体积百分比约束
Step 06 创建优化目标为最小化加权柔度,如图2-122所示。

图2-122 创建优化目标
Step 07 查看优化结果,如图2-123所示。作为对比,不施加拔模约束的优化结果如图2-124所示。

图2-123 优化结果密度iso图

图2-124 不施加拔模约束的优化结果
Step 08 分析验证。分析验证可以精确检验优化得到的结果。为了进行验证需要先根据拓扑优化的结果在CAD软件中进行重新建模(包括圆角),然后在HyperMesh中进行有限元建模。本例提供了已经创建好的模型,如有兴趣可以自己进行强度验证。
拓展:如何将拓扑优化解读为CAD设计?
拓扑优化得到的结果取决于设计空间、载荷工况以及拔模约束、最小尺寸等优化设置。优化的结果既不是唯一的,也不是最终的。实际工程中各个工况的加权系数选取通常需要先使用1.0进行一轮优化,然后再尝试不同的系数。也可以先对每一个工况进行单独优化,目的是理解优化结果中不同部位的材料和工况的关系。还可以使用第5章介绍的网格变形、形状优化、自由形状优化技术进行局部优化以解决应力集中等问题。
拓扑优化结果常常可以解读为多种设计方案,对不同方案分别建模并进行有限元验证后能够选出最合适的设计。
优化设计的环节存在迭代,为了加快优化计算速度,大部分时候会先忽略不起主导作用的非线性因素,等得到优化设计方案之后再进行非线性的分析验证,这样可以节约大量时间。另一种减少线性优化计算量的常用方法是将非设计空间创建为超单元。
2.3D挂钩拓扑优化
这里将挂钩优化修改为使用3D六面体单元,如图2-125所示,这样就有了更多的设计自由度。通常最好先用最简单的设置进行一轮优化研究以确定在给定载荷下结构的最优数学解是什么样的。这个例子是在2D模型的基础上增加了一个z向载荷的工况,同时放开了约束部位绕轴转动的自由度。

图2-125 优化空间
本例提供了各种不同设置的模型。
优化三要素
优化目标:最小化加权柔度。
设计约束:优化区域的体积百分比≤20%。
设计变量:所有设计区域的单元。图2-125垫圈区域和底部弯钩为非设计区域。
操作步骤
Step 01 打开bracket3d_start.hm。
Step 02 创建拓扑优化设计变量。进入Analysis>optimization>topology面板的create子面板,设置如图2-126所示。type选择PSOLID,props选择design,单击create按钮完成创建。

图2-126 创建拓扑优化设计变量
Step 03 响应、约束、目标、设置。步骤同2D案例,设置完成后提交计算。
Step 04 后处理。单击HyperView工具栏上的Iso按钮,然后单击Apply按钮显示iso图,如图2-127所示。截面图如图2-128所示。除了以上示意图,还可以查看位移等优化结果。

图2-127 优化结果iso图(一)

图2-128 优化结果iso截面图
由于没有任何额外约束,这个结果是数学最优值,施加制造约束后的模型都需要付出相应代价,如果性能和目前的结果比较接近说明制造约束没有大幅度降低产品的性能。
首先施加挤压约束。只需要在3D设计变量的基础上增加挤压约束,如图2-129所示。node path选择图2-130所示的节点。阈值为0.2时的iso图如图2-131所示。

图2-129 挤压约束

图2-130 挤压约束选择节点

图2-131 优化结果iso图(二)
更常见是使用拔模约束,将Draw Type设置为split,同时需要取消挤压约束,如图2-132所示。阈值为0.2时的iso图如图2-133所示。

图2-132 设置拔模约束

图2-133 优化结果iso图(三)
如果把拔模类型切换为single(见图2-134),则阈值为0.2时的iso图如图2-135所示。

图2-134 设置单向拔模

图2-135 优化结果iso图(四)