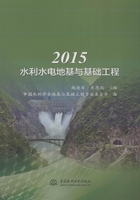
大华桥水电站围堰防渗墙施工技术对比分析
魏礁
(中国水利水电第八工程局有限公司基础公司)
1 工程简介
大华桥水电站上游临时土石围堰及下游土石围堰基础防渗采用混凝土防渗墙+墙下帷幕结构,堰基及堰体防渗采用塑性混凝土防渗墙,墙厚0.8m,防渗墙深入基岩不少于1.0m,下游防渗墙下设帷幕灌浆。上游临时土石围堰防渗墙轴线长度103m,防渗墙施工平台高程为1418.00m,防渗墙最大深度39m。下游土石过水围堰防渗墙轴线长度约106m,防渗平台高程为1412.00m,最大深度42m。
2 施工工艺
(1)场地平整。围堰填筑完成后用用振动碾采用无振2遍+有振6遍碾压平整。
(2)场地经平整后进行施工平台和导墙的建造。导墙采用梯形断面,浇筑C15混凝土,内设受力钢筋,以增强导墙的抗弯性能,加大接头管起拔时导墙荷载能力。
(3)在防渗墙施工时,沿防渗轴线每10~20m布设一个先导孔,进行先导孔的钻探施工,以判定防渗墙轴线部位基岩的顶板高程,以及防渗墙部位的轴线地质情况,便于指导防渗墙的施工,确保防渗墙每个部位的嵌岩均达到设计标准。尤其是对两岸堰肩处的地质情况进行复查。
(4)防渗墙成槽施工采用“钻劈法”,槽孔分为一期、二期槽。
(5)固壁泥浆:针对本工程强漏失等地层特性,防渗墙造孔施工以黏土浆液为主、遇漏失地层要多填黏土和碎石渣,用冲击钻进行挤压密实。清孔换浆采用新制黏土泥浆,确保浇筑前孔内淤积达标。
(6)墙段连接采用“接头管法”。一期槽浇筑时下设起拔接头管形成接头孔,二期槽施工时钻凿接头孔、并用钢刷刷洗接触面形成可靠地连接。
(7)灌浆预埋管下设采用φ110钢管,φ22钢筋制作保持架,焊接为一整体桁架。每段桁架高度根据槽孔孔深分段制作。吊车起吊,孔口连接,整体下设。根据槽长调整钢筋保持架的长度。
(8)混凝土采用泥浆下直升导管法浇筑,导管开浇顺序为自低处至高处,导管距孔底15~25cm左右,采用压球法开浇。
(9) 防渗墙质量检查采用注水检查和钻孔取芯相结合的检查方案。
3 上下游防渗墙施工条件
大华桥水电站围堰工程包括上游围堰和下游围堰,两道围堰距离约500m,地质条件基本相同。上游围堰堰顶高程1418.00m,长103m,堰顶宽15m。上游围堰处于河道转弯段,河流方向呈由西北向西南变化方向,左岸冲刷较严重,破碎带较发育,加之右岸导流隧洞爆破不充分,分流效果不理想,致使上游围堰水流流速较快,截流时难度加大,合龙时使用钢筋笼及大块石较多,防渗墙造孔难度较大,同时截流后堰前水位较高对围堰上游面冲刷严重,渗流流量较下游更大。下游围堰堰顶高程1412.00m,长106m,堰顶宽度55m。下游围堰处河道平直,水流平稳,河床与两岸岩体较完整,而且导流隧洞出口距下游围堰较远,出口水流对下游围堰基本没有影响。
上下游围堰填筑施工严格按照设计图标注的尺寸和要求进行施工,控制填筑边线和堰体坡度,力求避免欠填并将超填控制在规范规定的范围以内。现场填筑层厚按80cm进行控制,上游围堰共分7层,下游围堰共分两层,大面采用18t振动碾碾压,岸坡地带及其他局部边角部位采用2.1t夯板压实,碾压参数根据现场试验确定为静碾2遍+有振6遍。为确保后续防渗墙施工质量,在填筑料现场摊铺过程中,采用人工剔除粒径大于0.8m的石渣料,并且在防渗墙3m范围内严格控制填筑料,主要填筑闭气料以便防渗墙施工。上下游围堰水上部分填筑工艺基本相同,上游围堰体型较高、较窄,下游围堰矮、宽。水下部分由于上游围堰截流原因,填筑材料选择性小,填筑大块石钢筋笼较多,后期防渗墙造孔过程中不可控风险较大。
总体而言,上游围堰水文、地质、场地条件比下游围堰差,施工难度大。
4 施工措施
4.1 导墙施工
冲击钻施工平台布置在防渗墙轴线的下游侧,施工道路及倒浆平台布置在防渗墙上游侧,施工用的电力线路布置在防渗墙轴线下游侧。防渗墙导墙为梯形钢筋钢筋混凝土结构,防渗墙导墙高1.5m,顶部宽0.5m,底部宽1m。导墙及施工平台布置图见图1。
导墙作为防渗墙导向和定位的关键结构,导墙位置的准确性和导墙的稳定性直接影响到防渗墙的质量。为确保导墙位置准确,导墙施工前进行放样,立模时对模板进行复核,浇筑完成后再次对导墙的位置及高程进行定位。在钻机施工过程中,导墙两边土体的侧向压力,钻机的压力,以及导墙内侧空腔会影响导墙的稳定,严重时甚至倒塌。因此施工时在导墙内侧每个20m左右浇筑一段横向支撑杆,起到支撑导墙作用。
图1 防渗墙导墙及施工平台布置结构图
4.2 先导孔施工
为了更加准确了解防渗墙部位地质情况,判定防渗墙轴线部位基岩顶面高程,指导防渗墙的施工。上下游围堰防渗墙施工前,沿防渗墙轴线分别布置一排先导孔,通过先导孔钻探施工取芯,对轴线及堰肩地质情况进行复查。
防渗墙先导孔在防渗墙施工前进行,每隔10m左右布设一个先导孔。采用履带式冲击钻机从防渗墙顶高程钻至基岩面,由于钻孔时高压风将废渣冲出孔口,因此通过冲击钻机渣情况可以初步判断是否入岩,然后换地质钻机进行取芯,根据芯样再次验证基岩面。
4.3 槽孔划分
上下游防渗墙槽段均分一期、二期槽,两期槽段连接采用接头管法。综合考虑地层、墙体深度、设备能力、施工总体方案及工期要求确定槽段划分:
上游围堰防渗墙划分2~18号共17个槽段,标准一期、二期槽段长度均为6.4m、主孔宽度0.8m,副孔宽度为2 m。防渗墙端头两个槽段根据现场实际情况槽长分别为2号槽长8m,18号槽长7.6m。下游围堰防渗墙也分为17个槽段,标准Ⅰ期槽段长度5.4m,Ⅱ期槽长7.1m,主孔宽度0.8m,副孔宽度分别为1.3m、1.5m。端头槽段深度较浅根据施工需要长度调整为10.8m和8.6m。
施工过程中槽段划分为两期施工,设备安排合理。施工中Ⅰ期槽短Ⅱ期槽长的施工方式施工速度稍快,但施工工效主要由钻孔工艺影响,槽段长度对工效影响不明显。
4.4 钻劈法造孔
钻劈法成槽工艺指采用冲击钻机进整个槽段。对于含孤块石和硬岩较多的地层,“钻劈法”施工较为实用。本工程于深覆盖层中进行混凝土防渗墙施工。覆盖层主要为石渣料,在表层和深层部位有大的孤石、块石层,针对本工程地质特点和槽深分布情况,本工程上下游防渗墙均采用“钻劈法”成槽工艺。
造孔施工时,为保证顺利施工,不出现塌孔事故,根据孔内浆液的实际情况,直接将黏土以及适量的纯碱(Na2CO3)等添加剂等投入槽孔内,通过冲击钻头的冲砸作用直接在孔内造浆护壁。泥浆在施工中可以起到保持孔壁稳定、悬浮钻渣以及冷却钻具的作用。此外防渗墙施工时,在上下游防渗墙施工平台附近备足堵漏材料,造孔时发生漏浆,迅速组织人力、设备向槽内投入黏土、碎石土、锯末、水泥、高水速凝材料等堵漏材料,并及时向槽内补浆,以避免塌槽事故的发生。
除了以上措施,上游围堰钻进过程中,采取主副孔基本平行钻进的方法,同一槽段共3主孔2副孔,交叉排列。两台钻机钻进时先施工2个相邻主孔,待钻孔至一定深度时,同时移机一台打第3个主孔,另一台打副孔,之后第一台机打两处小墙,第二台机打另一个副孔,最后两台机打最后两处小墙。施工过程中可以做到干扰最小。主孔先一个槽段3个主孔与2个副孔钻进深度高差保持在2m左右,基本上平行下降,使泥浆护壁更完整,孔壁安全系数更大,不易垮孔。对上部松散层多次用回填块石、石渣充填,反复夯实,使防渗墙两侧土体“固若金汤”。
4.5 强漏失地层成槽应对措施
4.5.1 常规措施
(1)投置堵漏材料。防渗墙施工时,在上下游防渗墙施工平台附近备足堵漏材料,造孔时发生漏浆,迅速组织人力、设备向槽内投入黏土、碎石土、锯末、水泥等堵漏材料,并及时向槽内补浆,以避免塌槽事故的发生。
(2)大孤石处理措施。大块径孤石岩性坚硬,冲击钻进工效低,孤石形状不规则,易歪孔,修孔时间长,影响进度和工期,提前对探明的大孤石进行爆破处理。
4.5.2 非常规措施
(1)采用高水速凝材料堵漏。高水速凝材料是一种新型堵漏材料,具有高亲水性能、速凝、膨胀作用,能快速堵漏。
(2)在上游面铺设闭气料铺盖。施工时在上游围堰上游面增加一层3m厚的黏土铺盖,黏土可减小上游水渗流量,同时水在渗漏过程中携带黏土颗粒进入围堰中,增加了围堰内黏土成分含量,对围堰进行补强作用,有利于防渗墙成槽。
(3)预注浓浆处理。根据本工程的地质情况,在防渗墙施工中,易形成大面积塌孔、漏浆等现象发生,严重影响施工的安全、进度和质量等,在防渗墙施工前,充分利用截流后施工平台形成过程的时间段对防渗墙轴线范围内揭示的强漏失区进行了预灌浓浆处理。
4.6 防渗墙终孔深度与岩面鉴定
槽孔终孔深度以地质详勘报告和先导孔资料为基础,由地质监理、设计代表与施工单位的地质工程师结合施工现场取样综合判断后确定。对地质情况与设计图纸出入较大的,由监理、设计和防渗墙施工单位以及业主等单位的有关人员进行现场鉴定后确定最终深度。
孔深原则上按嵌入下伏基岩不小于1.0m进行控制。相邻两主孔终孔深度差小于1m,其中间副孔深度与较深的主孔之差为相邻两主孔孔深之差的1/3;相邻主孔终孔深度之差大于1m,其中间副孔取岩样进行基岩鉴定确定,其终孔深度与较深主孔深之差在1m以内,且副孔孔底高程不高于两主孔高程的中间位置。
实际操作时,参考设计图纸以及先导孔详细资料中的入岩深度,在接近基岩面时开始留取反循环抽出的岩样,每钻进20cm取样一次,当岩层风化程度变化剧烈、地质条件明显异常时,加密取样。所有岩样在编号后予以保留,并填写基岩鉴定表,经相关单位进行鉴定签认。
4.7 施工泥浆及原材料选用
根据地层条件和现场天然建筑材料性质及储量,本工程采用黏土泥浆护壁。配制泥浆时按需添加适量泥浆处理剂,如纯碱(Na2CO3)、CMC等,利于水化,形成胶体。
造孔施工时,根据孔内浆液的实际情况,直接将黏土以及适量的纯碱(Na2CO3)等添加剂等投入槽孔内,通过冲击钻头的冲砸作用直接在孔内造浆护壁。
新制黏土泥浆性能指标见表1。
表1 新制黏土泥浆性能指标

4.8 清孔换浆和接头孔刷洗
槽孔终孔且孔形验收合格后,即开始进行清孔换浆工作,Ⅱ期槽终孔后进行接头孔的刷洗。清孔换浆结束后1h,在槽孔底部1.0m部位取样,进行泥浆试验。现场检查槽孔内淤积厚度最小为2cm,最大为8cm,泥浆比重在1.0~1.1g/cm3之间。马式漏斗黏度16~22s;含砂量2%~4.4%。满足设计规定的要求。
二期槽接头孔的刷洗采用具有一定重量的圆形钢丝刷子,通过调整钢丝绳位置的方法使刷子对接头孔孔壁进行施压,在此过程中,利用钻机带动刷子不断的由孔底至孔口进行往返运动,从而达到对孔壁进行清洗的目的。接头孔壁洗刷结束后,刷子钻头基本不带泥屑,孔底淤积没有增加现象。
4.9 起拔接头管
接头管下设采用25t吊车下设,在Ⅰ期防渗墙浇筑后,混凝土达到初凝时间前,混凝土浇筑4~6h后开始微动接头管检查起拔力,接头管经常微动或少量起拔接头管,降低混凝土握裹力,在混凝土初凝后,接头管全部起拔。
4.10 混凝土制备与浇筑
4.10.1 墙体材料物理力学性能指标
上游围堰防渗墙墙体厚不小于80cm,抗压强度不小于20MPa,抗渗等级不小于W6,渗透系数小于K=10-7cm/s,
4.10.2 混凝土原材料
普通混凝土防渗墙所用的水泥、粗和细骨料、外加剂及水等材料,遵守DL/T 5199—2004第8款有关规定,以及JGJ 63—89的有关规定。
4.10.3 混凝土配合比
混凝土性能按下列指标要求进行控制:
(1)入槽坍落度:18~22cm。
(2)扩散度:34~40cm。
(3)坍落度保持15cm以上时间不小于1.0h。
(4)初凝时间:≥6h。
(5)终凝时间:≤24h。
(6)混凝土密度:≥2100kg/m3。
4.10.4 混凝土拌和及运输
混凝土由临时混凝土加工系统提供,拌制好的熟料采用6~8m3混凝土拌和车输送至浇筑槽口。
4.11 混凝土浇筑导管和下设
4.11.1 导管下设
导管下设前进行配管和作配管图,导管按照配管图依次下设,每个槽段布设2根导管,导管距槽孔端部或接头管壁距离保持在1.0~1.5m,导管间距控制在4.0m以内,当孔底高差大于25cm时,导管中心置放在该导管控制范围内的最低处。导管底口距槽底距离控制在15~25cm。
4.11.2 混凝土开浇及入仓
混凝土搅拌车运送混凝土进槽段储料罐,再分流到各溜槽进入导管。混凝土开浇时采用压球法开浇,每个导管均下入隔离塞球。开始浇筑混凝土前,先在导管内注入适量的水泥砂浆,并准备好足够数量的混凝土,以使隔离的球塞被挤出后,能将导管底端埋入混凝土内。槽孔内混凝土上升速度为1.5~2m/h,并连续上升至高于设计规定的墙顶高程。
4.11.3 浇筑过程的控制
(1)导管埋入混凝土内的深度保持在1~6m之间。
(2)槽孔内混凝土面高差控制在0.5m以内。每30min测量一次混凝土面,每2h测定一次导管内混凝土面,在开浇和结尾时适当增加测量次数。
(3)不合格的混凝土严禁进入槽孔内。
(4)浇筑混凝土时,孔口设置盖板,防止混凝土散落槽孔内。槽孔底部高低不平时,从低处浇起。
(5)混凝土浇筑时,在机口或槽孔口入口处随机取样,检验混凝土的物理力学性能指标。
5 结语
大华桥上下游防渗墙能如此快速完成质量和工期目标,成功的关键在于:
(1)施工资源配置合理,工作量安排与实际设备匹配,每一台机设备的任务都提前明确,精细控制,使工期大大缩短。
(2)人员分工明确,员工责任心强,各司其职,各负其责,工作效率高。
(3)在施工的过程中,没有停止对工艺创新改进的探索:如对传统的钻劈法进行了部分改进和辅助保证措施。如导墙中间浇筑支撑导墙,对抗导墙两边土体的侧向压力,钻机的压力,增加导墙的稳定性。对松散层多次回填夯实,抛投黏土、碎石土、锯末、水泥等堵漏材料及高水速凝材料堵漏。上下游围堰防渗墙施工过程中,我们也进行了施工工艺比较,上游防渗墙槽段划分Ⅰ、Ⅱ期槽同样长度,施工布置方便,钻孔成槽采取主副孔平行下降,既提高了钻孔效率,同时又减小了塌孔风险。下游围堰防渗墙槽段划分Ⅰ期槽短,Ⅱ期槽长,施工时先施工的Ⅰ期槽速度较快,后期二期槽施工时由于Ⅰ期槽施工使围堰结构趋向稳定,槽长较长并未使施工速度减慢,但下游围堰防渗墙为了减少移机,主副孔未平行下降,造成两次垮孔,造成不必要的损失。上游防渗墙施工时在上游面增加黏土铺盖,减小垮孔概率,提高成槽效率。
综上所述大华桥上、下游围堰防渗墙工程完工后,上下游围堰渗流量非常小,基坑抽水效果良好,圆满完成了旁人眼中的“不可能”,提前实现了围堰防渗质量和工期目标。上、下游围堰施工过程中几项工艺方面的改进和辅助措施,对防渗墙施工工艺完善有一定的借鉴意义,可供大家参考探讨。