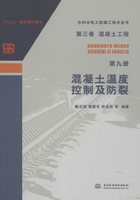
1.3 混凝土温控防裂技术的发展
1.3.1 20世纪90年代前的历史回顾
根据1938年3月、4月美国混凝土杂志(A.C.I)34卷“大体积混凝土裂缝”一文提供的资料,波尔德坝采取的温控措施包括:纵横缝均为15m,混凝土的水泥用量为223kg/m3,采用低热水泥,浇筑层厚1.5m,并限制间歇期,以及预埋冷却水管进行人工冷却;另从美国土木工程杂志(A.S.C.E)1959年8月的“垦务局对拱坝裂缝控制的实施”和动力杂志(Power division)1960年2月的“T.V.A对混凝土重力坝的裂缝控制”,两篇文章中可以看出,美国在对水工大体积混凝土温控防裂方面,在20世纪60年代初已经逐渐形成了比较定型的一种设计、施工模式,所采取的控制措施包括:①采用具有低水化热水泥,或一部分用活性掺合料来代替;②采用低水泥含量减少总的发热量;③限制浇筑层厚度和最短的浇筑间歇期;④采用人工冷却混凝土组成材料的方法来降低混凝土浇筑温度;⑤在混凝土浇筑以后,采用预埋冷却水管,通循环水来降低混凝土内部最高温度的峰值;⑥对混凝土外露面覆盖保温等措施。
苏联在20世纪60年代中,建设在安加拉河上的坝高125m,坝体混凝土近1400万m3,以及建设在叶尼塞河上,于1972年建成的克拉斯诺亚尔斯克水电站,坝高124m,坝体混凝土435万m3,这两个工程,虽然在设计施工方面,对大体积混凝土的温控问题也采取了比较严格的措施,还是出现了不少的裂缝,一直到1977年兴建在纳伦河上的高215m,坝体混凝土320万m3的托克古尔水电站建成后,才宣布他们在温控防裂方面取得成功。
我国于20世纪60年代兴建,70年代建成的丹江口水电站工程,在60年代浇筑的100万m3混凝土时,出现大量的裂缝,经过停工整顿,并集中设计、施工、科研和大专院校的科技力量,在现场进行了历时数年的调查研究工作,总结了设计施工经验,于1964年复工浇筑的200多万m3混凝土后,没有再发现严重危害性的贯穿裂缝或深层裂缝,一般的表面裂缝也很少出现。在这一时期,采取的三条主要措施是:①严格控制基础允许温差,新老混凝土上下层温差和内外温差;②严格执行新浇筑混凝土的表面保护;③提高混凝土的抗裂能力(极限拉伸值和Cv值)。
表面保护是总结了丹江口水电站前期浇筑的100万m3混凝土的经验教训以后,提出来的防止裂缝的一项有效措施,达到预防表面裂缝的效果,在2~7d内,日平均气温下降7℃以上,就要保温。
另外,要求按不同季节控制混凝土的内部最高温度,按冬季(12月至次年2月)24~27℃,春秋季(3—5月,9—11月)32~36℃,夏季应不大于40℃。要确保以上的温控标准,在高温和较高温季节,都必须采取预冷骨料或加冰拌和等人工冷却措施,以控制浇筑温度。
1.3.2 温控发展的趋势
大体积混凝土温控发展有70多年,逐步形成了完善的理论和措施,我国在新中国成立后,从丹江口水电站工程开始,经历了葛洲坝水利枢纽工程、三峡水利枢纽工程的温控发展的几个阶段,丹江口、葛洲坝和三峡水利枢纽工程都是温控技术发展的节点,特别是三峡水利枢纽工程的完工,温控技术得到了长足的进步。温控的未来发展趋势,在以往成熟的技术基础上,逐渐与其他行业和现代科技相结合,形成标准化、个性化和自动化等温控技术的形式。
(1)标准化、模块化的工艺。温控的标准化,是指在温控措施中,通过严格的施工工艺,达到满足每个单项措施的要求,比如拌和楼冷却过程中,骨料的冷却程度与冷却时间和冷风的温度有关。因此,设计时考虑到最大的生产量时,骨料在一次、二次预冷仓内受冷风的时间达到相应的要求,冷风的风温控制、骨料仓内骨料的堆高的控制均需达到某种标准等。
将复杂的工艺模块化,比如冷却水厂的模块化,以往在大坝冷却通水的生产中,均是建设制冷水生产厂,冷水厂布置在拌和楼附近或者布置在大坝附近为砖混结构,占地面积一般都在120m2以上,建成后直到完成大坝通水冷却任务时才能被拆除;近几年我国水电行业规模的扩大,冷水站也进行了模块化设计,用一个集装箱来安放一台冷水机组,包括冷水箱、冷却塔和相关管道阀门系统,整个集装箱就是一个冷水站,体积约为9.2m(长)×2.8m(宽)×2.6m(高),大大减少了占地面积,方便布置和拆移,可以就近布置在马路上,拆移时分为2大件,单件重量小于30t,集装箱安放在大坝入仓设备覆盖范围内,利用起吊设备安装冷水站。模块化的设计,既方便布置,亦降低成本,并且就近的布置可以降低冷水的温度回升。
(2)个性化、高效能的方案。温控不同的措施有不同的特性,同一个措施的不同阶段也有不同的特点,针对这些特点采取个性化的、高效能的方案,有效地控制温度在允许值以内。比如初期冷却通水,混凝土水泥水化热一般在前7d释放80%以上。因此,混凝土内部最高温度出现在前7d内,针对这个特点,在最高温度出现前,加大冷却通水的流量,降低混凝土内部温度峰值,在最高温度出现后,减少制冷水的流量,使混凝土内部温度缓慢下降;另外在高标号区、重点区域,采用加密冷却水管铺设间距,加大制冷水通水流量,也是个性化和高效能的温控方案。
(3)自动化、智能化的控制。在拌和楼的出机口温度控制中,绝大多数采用的自动化和智能化的控制,包括加冰、加制冷水和冷却的骨料等,随着科技的发展,在温控其他措施上也采用自动化和智能化的控制方式,比如冷却通水的自动化和智能化,采用温度传感器、流量计和电动阀门等控制系统,自动收集通水数据、计算分析混凝土内部温度,判断温度是否满足设计要求,自动控制流量和是否保持通水或者判断使用多大的通水流量,达到自动化、智能化,减少人力资源和人工采集数据的误差,这种智能系统已经在锦屏水电站大坝施工中成功地应用。
(4)系统化、综合化的措施。温控与防裂的措施是综合性的措施,单项的措施往往难以达到防裂的要求,需要通过系统化的控制方法,从拌和楼、入仓浇筑、冷却通水、表面养护等混凝土生产一条龙的各个环节中去控制,通过综合措施来实现,出机口温度控制、入仓和浇筑温度的控制、冷却通水等来实现最高温度的控制,如果其中某一项措施不到位,势必增加下一项的控制难度,影响控制效果甚至不能满足设计要求。
温控措施中,每个单项措施控制温度的回升值有限,假设拌和楼出机口温度没有得到控制,对浇筑温度控制带来直接的影响,浇筑温度不能控制就会给冷却通水带来压力,而冷却通水的消减最高温度峰值大约在4~6℃,超出这个范围就可能超出设计要求。因此,温控每项措施都需要严格实施。
(5)精细化、数字化的目标。在温控防裂技术的发展过程中,由粗放式的工艺逐渐发展为精细、高标准、严要求的工艺,如浇筑过程中的仓面覆盖,以往要求不高,现在在开仓浇筑之前,隔热被必须准备齐全,施工中有专人负责盖被。冷却通水过程中对流量、水温的稳定性以及进出口的转换时间等均按要求操作,每一项措施都是以高标准来要求。
在数字化方面,与大坝施工过程进行同步的反演分析,从开工到投入运行,进行全坝、全过程的有限元仿真计算,施工期即可了解各坝块的温度场和应力场,并可根据当时的实际状态和施工计划预报后续时间及运行期坝体的应力场和安全系数,可以在施工期及时针对性的调整措施,以达到无缝大坝的要求。