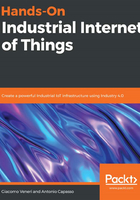
The fieldbus
Field or fieldbus networks are computer network implementations for connecting control devices, such as PLCs, and devices on the workshop or field, such as sensors or actuators. In a typical scenario, sensors and actuators are connected to the controller either directly, through the input or output modules of its cabinet, or through a serial line from the remote input and output cabinets. Using a field network, however, such devices become the nodes of a computer network and so they must have some processing capacity to be able to communicate through the network.
These networks differ from the preceding networks because of the following points:
- They have very short messages that are exchanged frequently.
- They deliver the messages within a short and deterministic time interval.
- They address the messages to many nodes simultaneously. An example of a message of this kind might be a closing order set to all of the valves of a system.
These characteristics lead to the creation of lean networks, where just levels 1, 2, and 7 of the OSI model are defined, leaving the intermediate levels empty. This reduced model of the OSI model is called an Enhanced Performance Architecture (EPA) model, and is shown in the following diagram:
Fieldbus networks provide the following advantages:
- They have a simplified architecture, since they are scalable and flexible.
- They have less wiring, with a reduction in installation and maintenance costs.
- They can handle more complex and bidirectional information, since the fieldbus devices can operate signal processing locally. This allows the fieldbus devices to do the following:
- Linearize or convert the signals into engineering units
- Send information about their state to the controller
- Carry out close regulation loops
- They have a local processing capability. This makes the response time less critical since many of the necessary operations, including the closed-loop regulations, are carried out by the device itself autonomously.
- They can carry out calibrations of sensors and actuators through software from a terminal connected to the network.
- They can provide robustness in their transmissions, since digital transmissions are intrinsically less sensitive to noise than analogical transmissions. They can also implement techniques for the recognition and correction of transmission errors.
Even if all of the devices that require networks such as these are located at the lower level of the CIM hierarchy (on the field level), they need different functionalities. For this reason, there are three different classes of field networks—the sensor bus operating at the bit level, the device bus operating at the byte level, and the control bus operating at the level of blocks of bytes. This is depicted in the following diagram:
- Sensor bus: The sensor bus usually implements just the first two levels of the OSI model, that is , the physical and data links. Its primary purpose is to reduce the wiring; the typical length of a message is one byte. Usually, the devices that are already available are connected to the network through a multiplexer. The most common sensor buses are CAN, Seriplex, ASI, and LonWorks. An example of a connected device could be a proximity sensor without internal diagnostics.
- Device bus: This allows the transfer of messages that are up to 16-32 bytes in size. In addition to the first two OSI levels, it implements some features belonging to level 7, the application level. Device buses also allow us to send a simple diagnostic. The most common device buses are CAN, DeviceNet, Profibus DP, LonWorks, SDS, and Interbus-S. An example of a connected device could be a photocell or a temperature sensor with internal diagnostic functions.
- Control bus: This allows for the communication of blocks of bytes, which can be up to several thousands of bytes. It implements levels 1, 2, and 7 of the OSI model, as well as an additional level called the user level. The devices developed for connecting to a control bus include predefined algorithms that are configured through the network so that they can adapt them to a specific application. They also include a real-time internal cache which checks and updates all data continuously, making them available to all other devices on the network. An example of a connected device could be a valve with an embedded flow regulator and self-diagnosis and configuration capabilities. The most popular control buses are WorldFIP, Profibus, Modbus, and DeviceNet.
An interesting comparison between industrial networks and the fieldbus is available at https://www.automazioneindustriale.com/le-reti-ethernet-industriali-crescono-piu-dei-fieldbus/amp/. This can be seen in the following diagram: