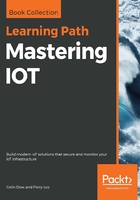
MEMS microphones
MEMS devices can also be used for sound and vibration detection. These types of MEMS devices are related to the accelerometers previously covered. For IoT deployments, sound and vibration measurements are common in the industrial IoT and predictive maintenance applications. For example, an industrial machine that rotates or mixes a load of material in chemical manufacturing, or in centrifuges to separate mixtures, needs precise leveling. A MEMS sound or vibration unit will typically be used to monitor the health and safety of such equipment.
This type of sensor will require an analog-to-digital converter of sufficient sampling frequency. Additionally, an amplifier is used to strengthen the signal. The impedance of a MEMS microphone is in the order of several hundred ohms (which requires careful attention to the amplifier used). A MEMS microphone can be analog or digital. An analog variety will be biased to some DC voltage, and will be attached to a codec for analog-to-digital conversion. A digital microphone has the ADC close to the microphone source. This is useful when there is signal interference from cellular or Wi-Fi signals near the codec.
The output of a digital MEMS microphone can either be pulse density modulated (PDM), or sent over I2S format. PDM is a high sampling rate protocol that has the ability to sample from two microphone channels. It does this by sharing a clock and data line, and sampling from one of the two microphones on different clock periods. I2S doesn't have a high sampling rate, and the decimation at audio rates (Hz to kHz range) results in fair quality. This still allows multiple microphones to be used in sampling, but may not require an ADC at all, since the decimation is happening in the microphone. A PDM, with its high sampling rate, will need to be decimated by a digital signal processor, or DSP.