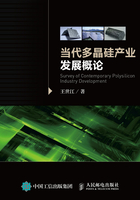
1.3 发展历程
1.3.1 全球多晶硅产业发展回顾
(1)多晶硅研发中试期
高纯硅材料的研制工作自19世纪就已开始,早在19世纪60年代,人们就开始尝试制备超纯硅。1822年,瑞典化学家Berzelius首先使用钾还原四氟化硅制备出单质硅,但直到1951年,美国杜邦公司才使用类似的方法建设了全球首家多晶硅提纯工厂,供美国的电子公司生产高频二极管,该方法也被称为杜邦法。由于当时锌的纯度不易提升,生产的硅纯度不高,产品用途未能扩大。日本尝试改进该生产工艺,生产出电阻率达到1 000 Ω/cm的多晶硅,以将其应用于高压器件上,但是始终未获得成功。由于氢气更易于提纯和回收重复利用,其生产成本也相对较低。1953年,贝尔实验室用氢替代锌来还原四氯化硅,并在钽丝上沉积多晶硅,制备出P型电阻率达到1 000 Ω/cm的多晶硅,该方法也被称为贝尔法。西门子公司是欧洲首家从事电子管研发的公司,为解决硅基整流管的原料问题,也投入多晶硅提纯研发工作,于1955年成功研发出用氢气还原三氯氢硅,在硅芯发热体上沉积硅的工艺技术,并于1957年建厂进行工业规模化生产,此即为西门子法。1958年,西门子公司将该方法授权给德国Wacker公司使用,德国Wacker公司的多晶硅产量也从1959年的530 kg提升至1969年的60吨。1956年,英国国际标准电气公司的标准电信实验所成功研究出通过硅烷热分解制备多晶硅的方法,被称为硅烷法。1959年,日本的石冢研究所也同样成功研究出该技术。美国和日本的一些多晶硅企业开始采用杜邦法或贝尔法建立多晶硅工厂,如日本大阪钛、东海电极公司等。20世纪50年代初,国外多达16家(美国4家、日本6家、欧洲6家)企业研究多晶硅的生产方法,产生了如杜邦法、贝尔法、碘化法、皮齐尼法和硅烷法等制备多晶硅的方法。当时,由于半导体产业刚刚兴起,市场规模不大,多晶硅企业也处于各自为战的状态,独立进行研究和开发他们各自的多晶硅工艺。早期的企业主要是顾虑到自有的工艺技术一旦被竞争对手获取,会导致自己在产品质量和生产成本竞争方面处于不利地位,因此很多技术都处于独立开发状态。
(2)多晶硅工业化起步期
20世纪60年代早期,受制于锗在半导体领域的应用,硅材料市场有所波动,由于杜邦法和贝尔法提炼的多晶硅纯度不高,部分多晶硅企业开始放弃杜邦法或贝尔法,开始引入技术逐步成熟的西门子法,如日本信越化学公司开始从当时的联邦德国引进西门子公司的三氯氢硅还原技术。在此带动下,日本的大阪钛、室素电子公司等都开始改用三氯氢硅氢还原法,西门子法逐步奠定了其在硅工业的地位。同时,日本窒素公司也开始将西门子技术输入到我国,在洛阳建立了年产能3吨的多晶硅生产线。到20世纪60年代后期,由于锗材料做出的器件耐热性差,工作不稳定,且锗是稀有材料,大批量生产困难,市场开始转向硅材料,原有的生产商不能满足半导体行业对多晶硅需求数量更大、纯度更高以及成本更低的要求,摩托罗拉、德州仪器、孟山都公司等一些半导体设备和电路制造商开始自主生产多晶硅供企业使用。由于硅材料的应用范围从最初的整流器、二极管扩大到可控硅、晶体硅、集成电路等,市场需求量扩大,多晶硅产量也由20世纪50年代的百公斤量级提升至20世纪60年代的百吨量级。
(3)低成本多晶硅发展期
20世纪70年代,随着彩电、无线电收发两用机、台式电子计算机、电子表等消费品走入市场,集成电路市场生产规模开始扩大,硅材料的市场需求也随之水涨船高。因而更多的企业加入到硅材料生产领域,尤其是一些半导体企业为保障硅材料供应,也纷纷涌入上游生产环节。据不完全统计,全球硅料生产企业多达上百家。但全球多晶硅市场曾在1971年和1974年出现过两次萎缩,同时,受石油危机的影响,能源价格暴涨,多晶硅企业生产成本大增,一些硅料厂亏损严重,部分企业此后又逐步放弃了硅料生产业务。也正是由于石油危机的发生,美国开始加大对地面光伏发电的支持力度,大力支持低成本的多晶硅生产技术开发,多晶硅产业的发展开始掀起一波高潮。1978年~1985年间,美国能源局拨款8亿美元用于研发生产多晶硅的低成本方法,喷气推进实验室负责该项目的实施工作。一些企业比如西屋(用金属钠还原四氯化硅)、Battelle(用金属锌还原四氯化硅)、Schumacker(裂解三溴硅烷)和 Aerochem(利用金属钠气体还原四氯化硅)等公司也投入数百万美元发展传统的或者新型的多晶硅生产技术,但受政策影响,美国能源局和喷气推进实验室的多晶硅研究项目大多没有实现商业化生产。
(4)多晶硅整合期
到了20世纪80年代,在个人计算机和存储器发展的带动下,半导体市场又掀起新一轮高潮,对硅材料产业发展起到极大的促进作用。美国Ethyl公司研究使用化肥工业的副产物四氟化硅制备硅烷,并使用流化床法工艺技术于1983年投资1.5亿美元研发粒状硅,而全球最大的单晶硅生产商日本信越半导体和三菱材料也入股美国Hemlock公司,仙童半导体公司通过Great Western Silicon生产自己的多晶硅产品,在此过程中硅材料产业的集中度不断提高。一些此前研发的生产技术又受到重视,如美国联合碳化物公司采用并发展了20世纪60年代日本小松公司的金属钟罩系统作为年产1 200吨工厂的技术。Tokoyama Soda和Nippon Kokan两家日本公司分别从Great Western Silicon公司购买了石英钟罩反应器和化学回收技术用于年产1 000吨的工厂。而美国Ethyl公司(后被美国MEMC公司所有)和美国德州仪器公司则使用流化床法生产多晶硅等。半导体硅的用量一直在增长,1965年为30吨/年,到1988年已经达到5 500吨/年,平均每年的增长率为15%。
在20世纪80年代后期,受美国对日本的半导体反倾销政策的影响,全球多晶硅市场需求在1987年左右再次出现较大萎缩,一批多晶硅企业开始退出该领域,如美国德州仪器公司、美国通用电子公司等,行业整合也在加速。日本小松电子收购美国联合碳化合物公司,美国MEMC公司收购美国Ethyl公司和意大利诺贝尔公司等,市场也逐渐集中到七大多晶硅厂商手中。而这几家工厂在20世纪90年代也开始大规模扩产,美国Hemlock公司分别在1997年和1998年各新增1 500吨产能,使其总产能在1999年达到6 200吨,Asimi公司在美国Butte建设年产能为2 000吨的多晶硅工厂,三菱则在美国建设产能为1 500吨的多晶硅工厂。日本Tokuyama公司则分别在1997年和1999年新增1 000吨和1 500吨产能,使总产能达到3 700吨。德国Wacker公司将产能从1996年的2 800吨增加至2000年的5 000吨。1990年~1999年全球多晶硅产量如图1-16所示。

图1-16 1990年~1999年全球多晶硅产量情况
(5)多晶硅腾飞期
到了2000年之后,随着德国EEG法案的出台,光伏市场快速发展,对多晶硅市场需求快速拉大,但当时的多晶硅工厂主要供应电子级多晶硅料,太阳能级多晶硅料供应来源主要是多晶硅工厂不能满足电子级硅料的产品,以及半导体单晶厂的头尾料。按照2005年全世界1 818 MWp的太阳电池产量,以及多晶硅消耗量12吨/ MWp计算,2005年太阳电池用多晶硅的总需求量为2.18万吨。多晶硅厂商供应了1.5万吨,半导体行业废弃的硅可被光伏产业重新利用的约0.3万吨(按1.5万吨的20%计算),3 800吨的缺口则由历年的库存补足。由于供求关系紧张,多晶硅原材料的价格持续上涨,推动资本开始源源不断投入到太阳能级多晶硅领域。
美国Assimi公司于2002年开始在Mose Lake建设的年产2 000吨的多晶硅工厂是全球第一家直接生产太阳能级多晶硅料的企业,此后,Hemlock、Wacker 等传统多晶硅企业也逐步在2005年开始通过扩产提高太阳能级多晶硅产品供应。与此同时,中国和韩国的一些企业也开始涌入多晶硅领域,并逐渐改变保持了多年的多晶硅生产格局。截至2015年底,全球最大的5家多晶硅企业中,中国江苏中能、韩国OCI和中国新疆特变电工分列第1、第3和第4位。全球多晶硅产量也达到近34万吨,约为2000年的16倍。
2000年~2008年全球多晶硅产量情况如图1-17所示,20世纪主要多晶硅生产商如表1-5所示。

图1-17 2000年~2008年全球多晶硅产量情况
表1-5 20世纪主要多晶硅生产商

1.3.2 我国多晶硅产业发展回顾
(1)萌芽期
早在20世纪50年代,我国一些研究机构已开展多晶硅料的工艺研究工作。北京有色金属研究总院于1955年起,在缺少技术和资料的情况下,自行摸索锌还原四氯化硅工艺(杜邦法)和氢还原四氯化硅工艺(贝尔法),并且在短短两三年时间内相继实现了这些工艺的中试生产,并于1958年开始研究西门子法,在摸索中解决了还原炉的高压启动等工艺,成功生产出高纯硅材料。北京玻璃厂(原605厂)研发使用氢气还原四氯化硅,在石英管中沉积多晶硅。上海901厂在多晶硅生产方面也开始了一些工作。苏联也派来一些专家协助北京有色金属研究总院等进行多晶硅工艺提纯等相关工作,但这个时期的多晶硅生产主要还属于工艺研究阶段,并没有形成规模。
(2)摸索期(1964年~1996年)
我国多晶硅产业化始于1964年,北京有色金属研究院338室(硅材料研究室)及相关配套的人员、装置和职能管理部门内迁至四川峨眉县,成立峨嵋半导体材料厂(代号为739厂),建设产能为803千克/年的多晶硅工厂,并于1965年8月实现第一炉硅料产出。次年,洛阳单晶硅厂(代号740厂)也从日本窒素公司引进一条产能为3吨的多晶硅生产线,这也是我国首次从国外引进多晶硅生产线。在消化吸收的基础上,1968年,739厂援建了华山半导体材料厂(代号741厂),并于1971年投产。739厂、740厂和741厂也形成了我国三大硅材料生产基地。同时,受当时大力发展电子工业的指示影响,国内对多晶硅的需求量剧增,冶金部在1967年召开的半导体硅材料生产座谈会上号召“利用大厂一角搞半导体”,全国多个地方开始创建多晶硅项目。20世纪70年代,多晶硅年产量达到近8吨/年,行业经历了一个阶段的盲目发展时期,20世纪70年代中后期,小型生产厂家多达30余家,形成了冶金、化工、电子、轻工、酿酒、建材等多行业齐干多晶硅的局面。这些工厂基本采用改良西门子法,技术水平低、生产规模小、各种消耗指标高、产品质量不稳定,加之生产成本逐年增加等因素,改革开放后,受市场经济冲击,我国绝大部分多晶硅生产企业因亏损而相继停产或转产,到1983年减少为18家;尤其是到了20世纪80年代后期,由于市场萎缩,加上电子器件及整机引进造成的积压,市场对材料的需求增速大幅放缓,至1987年,多晶硅工厂数量缩减为7家。受市场以及企业经营效益等因素影响,中国有色金属总公司拟整合峨嵋半导体材料厂、洛阳单晶厂和华山半导体厂,成立中国四佳半导体材料有限公司,并将工厂搬迁至西安,但后来受各种因素影响最终未能成型。20世纪90年代,上海棱光(原上海石英玻璃厂)引进了摩托罗拉20世纪80年代初就已停产的年产150吨的多晶硅生产线,但由于市场和技术问题,该生产线主要处于断续生产状态。到了1993年,全国只有原峨嵋半导体材料厂、洛阳单晶硅厂、上海棱光股份有限公司和重庆天源化工厂4家单位在生产多晶硅产品,而到1996年则只剩下原峨嵋半导体材料厂和洛阳单晶硅厂2家。这些生产厂生产规模小、工艺技术落后、消耗大、成本高,全国的多晶硅总产能始终在年产数十吨的规模上徘徊。我国在1990年~1996年多晶硅产量情况如表1-6所示。
表1-6 我国多晶硅产量情况

(3)起步期(1997年~2005年)
20世纪90年代末期至21世纪初,全国在产的多晶硅工厂仅峨嵋半导体厂和洛阳单晶硅厂(该工厂也于20世纪90年代末期停产),国家也在这个时期开始大力支持大型多晶硅工厂的发展。自1996年开始,在国家经贸委的支持下,峨嵋半导体厂通过“双加”工程,将多晶硅产能提升至50吨/年。面对当时工业规模小、生产工艺落后、综合利用率低、能耗高、产品质量标准低、市场竞争力低等形势,国家经贸委支持峨嵋半导体厂实施100吨/年多晶硅产业化关键技术研究,该项目于2000年初通过国家鉴定。同年,国家发展计划委员会批准以峨嵋半导体材料厂的技术和人才为基础,组建四川新光硅业科技有限公司,建设年产1 000吨多晶硅产业化项目。该项目引进了俄罗斯技术和美国CDI技术等,于2002年开工建设,并于2007年建成投产,是我国首条千吨级多晶硅生产示范线。2003年,洛阳中硅在国家发改委重点行业结构调整专项资金的支持下,在洛阳建设年产300吨多晶硅产业化项目,2005年10月投产,这也是我国首条产业化示范线,标志着多晶硅规模化生产技术体系形成,打破了国外多年的技术封锁和市场垄断,也是从这时候开始,国外单项技术开始进入中国。1997年~2005年我国多晶硅产量情况如表1-7所示。
表1-7 1997年~2005年我国多晶硅产量情况

(4)发展期(2005年~2009年)
虽然21世纪初全国在产的多晶硅工厂仅1~2家,但2005年之后,受太阳能级多晶硅市场需求影响和在多晶硅生产线示范项目的带动下,国内资本开始大举进入多晶硅领域,多晶硅产业规模迅速扩大。据工信部调研数据显示,截至2009年底,已建、在建和拟建的多晶硅生产企业达52家,其中有48家企业采用改良西门子法,4家采用硅烷法;此外,另有30家企业探索利用物理冶金等方法进行低成本多晶硅生产技术研发。国内多晶硅的投产企业由2006年的2家增至2009年的24家,年产量也从两三百吨发展至两万吨,使我国光伏产业原材料的自给率由几乎为零提高至50%左右,为我国光伏产业摆脱对外依赖进口的局面,实现产业健康发展奠定了基础。当时,此24家已投产的多晶硅企业,已投产项目设计总产能在万吨以上的企业有一家,即江苏中能;而投产企业产能在3 000吨以上的企业还有赛维LDK、洛阳中硅、重庆大全等,其余17家已建多晶硅生产线设计产能为1 000~3 000吨,小于1 000吨的多晶硅企业有6家。多晶硅企业多数布局于内蒙古、四川、河南等中西部省区。多晶硅(尤其是采用西门子工艺)的生产成本受电价因素影响较大,另外,地区产业政策、下游市场对产业布局也有较大的影响,因此投资项目大部分集中在中西部电能资源丰富的地区。而东部部分地区如江苏省因对该产业关注早,整体产业链发展较快,也带动了本地多晶硅产业的快速发展。国内企业通过技术引进、改进,尤其是通过大型还原炉、加压还原炉等技术的应用,多晶硅生产综合能耗不断降低,已从2005年的平均300~400度/千克降至160~200度/千克,部分企业能耗指标已接近国际先进水平(还原电耗:60~70度/千克,综合电耗:150~160度/千克)。采用改良西门子法的企业基本掌握千吨级规模化生产关键技术,在大规模合成、高效提纯、低电耗还原、四氯化硅氢化等关键技术环节取得突破;关键设备的国产化进程加速,生产工艺不断优化,大规模化生产的稳定性逐步提高。也有部分企业研究硅烷法和冶金法生产工艺,该方法生产的多晶硅纯度较高,但由于硅烷法要消耗金属钠或镁等还原剂,且硅烷易燃易爆,当时企业正在对该技术进行摸索验证。这个时期对于光伏行业而言属于“拥硅为王”,多晶硅工厂也是呈现大上快上的建设态势,这也为多晶硅产业后续发展埋下隐患。2009年我国多晶硅企业情况如表1-8所示。
表1-8 2009年我国多晶硅企业情况

(续表)

我国国内多晶硅企业地区分布情况如表1-9所示。
表1-9 国内多晶硅企业地区分布情况

(5)市场调整期(2009年~2013年)
在多晶硅利润率大增的情况下,各路资本纷纷涌入多晶硅投资领域,使多晶硅产能虚增。根据2009年的全国数据调查,在当时全国52家多晶硅企业中,已建成项目的设计产能为44 010吨,在建项目的设计产能为68 450吨,拟建产能更是高达10万吨以上,产能已经远超出当时市场需求。同时,少部分多晶硅工厂因不完全掌握改良西门子多晶硅生产技术或片面追求经济效益,生产的副产物没有得到较好处置,导致四氯化硅污染环境的事件发生。政府于2009年出台了《关于抑制部分行业产能过剩和重复建设引导产业健康发展若干意见的通知》(国发38号文),将多晶硅行业定为产业过剩行业。四川发改委2009年7月起暂停多晶硅等6个行业的扩大产能项目。更有媒体报道商务部拟将多晶硅行业列入六大“高能耗高污染”行业名单中,限制多晶硅产品出口及来料加工贸易等。多晶硅也被冠以“高能耗、高污染”的帽子,国家收紧了多晶硅项目审批权限,同时,银行业对多晶硅行业收紧银根,导致多晶硅扩产、技改等受到一定抑制。2009年,受全球次贷危机的影响,全球光伏市场增速快速下滑,多晶硅产品价格也快速下滑,从2008年的近500美元/千克下降至2009年的40美元/千克,部分企业开始出现亏损。幸运的是,2009年、2010年德国和意大利光伏市场开始快速扩大,多晶硅产品价格又开始回暖,增长至2010年的近90美元/千克。但到2011年之后,受太阳能光伏市场增速放缓和国外多晶硅企业对我国倾销的影响,多晶硅产品价格大跌,企业也出现大面积亏损,很多企业开始停产甚至破产。至2013年上半年,全国在产的多晶硅企业仅为7家(江苏中能、大全新能源、亚洲硅业、新特能源、黄河上游、四川永祥、神州硅业),多晶硅产品价格也跌至15美元/千克,多数产能在1 000~3 000吨之间的多晶硅工厂倒闭。
(6)市场恢复期(2013年至今)
2013年,国务院出台《关于促进光伏产业健康发展的若干意见》(国发24号文),国内光伏市场开始规模化扩大,再加上我国相继对美、韩、德等出台多晶硅反倾销、反补贴等政策,国内多晶硅市场需求开始扩大,产品价格也逐步提升,国内多家多晶硅企业开始复产。至2013年底,国内开工企业已达到15家,多晶硅产能也达到16万吨。国家也开始简政放权,将多晶硅项目审批权限下放到地方,多晶硅项目投资开始加大,多家企业开始扩产或新建多晶硅工厂,而多晶硅生产线投资也大幅下降,已从2005年~2010年的7亿~10亿元/千吨下降至2013年的2亿~4亿元/千吨,同时,多晶硅生产布局更加优化,逐步往能源价格洼地如西北等地区转移,生产设备也更为先进。在以上因素的影响下,多晶硅生产成本逐步下降,部分企业如新特能源、大全新能源、亚洲硅业等企业生产成本已降至13美元/千克以下的全球领先水平,产品质量也基本上达到电子级三级品要求。我国多晶硅企业历经近50年的发展,终于在质量完全能满足太阳能光伏产品需求的基础上,实现成本全面领先于国外企业。预计随着新多晶硅工厂的进一步投产,已经完全具备实现太阳能级多晶硅进口替代基础,并且有望在电子级多晶硅领域也实现进口替代。
[1].半导体物理学基础(讲义),雷敏生。