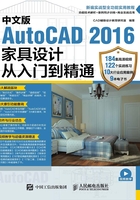
1.3 实木家具制造工艺
目前市场上家具种类繁多,可粗略地分为实木家具、板式家具、软体家具、金属家具、塑料家具、玻璃家具、竹藤家具等。接下来3节介绍常见的家具种类的制造工艺,如实木家具、板式家具、软体家具。希望读者通过阅读这些内容,可以大致了解这几类家具的制作知识。
实木家具的制造工艺包括实木配料、毛料加工、净料加工、胶合与弯曲加工等工序,本节简要介绍各工序的操作流程。
1.3.1 实木材料的特性
实木家具所选用的材料包含以下所述的特性。
◆选用家具传统用材,适合做线形零件。
◆质量较轻而强度较高。
◆容易加工及涂饰。
◆热、电、声的传导性小。
◆具有天然的纹理和色泽。
◆吸湿性及稳定性较高。
1.3.2 实木家具的结合方法
实木家具由若干零部件按照一定的结合方式装配而成,其常用的结合方式有榫结合、胶结合、木螺钉结合、连接件结合等,见表 1‑3。
表3-1 实木家具的结合方法

续表


图 1‑2 直角榫

图1‑3 燕尾榫

图1‑4 木螺钉样式
1.3.3 配料工艺
配料方式有单一配料法、综合配料法,根据具体的施工要求来选用。配料工艺分为4种,如先横截再纵解工艺、先纵解再横截工艺等。
1 配料方式
单一配料法
在同一锯材上配制出一种规格的方材毛料。这种方式容易操作,但是余料数量较大,出材率稍低。
综合配料法
在同一锯材上配制出两种以上规格的方材毛料。这种方式能够提高木材的利用率,但是效率稍低。
2 配料工艺
先横截再纵解工艺
根据零件的长度要求,先将板材横截锯成一定规格的长度,同时截掉锯材的一些缺陷,如开裂、腐朽、节子等,再将其纵向锯解成方材或者弯曲件的毛料。
先纵解再横截工艺
根据零件的宽度或者厚度尺寸要求,先将板材纵向锯解成长条,然后根据零件的长度要求,将长条横截成毛料。
先画线再锯解工艺
根据零件的规格、形状等要求,用零件样板在板面上画好线,再锯解。
先粗刨再锯解工艺
通过粗刨加工,将木材的缺陷、纹理、色泽表露出来,然后根据这些情况合理配料,对于节子、裂纹等缺陷可以根据用料要求进行修补,以提高配料质量和出材率。
如图 1‑5所示为先粗刨再锯解的工艺流程。

图1‑5 工艺流程图
1.3.4 毛料出材率
使用毛料出材率来表示锯材配料的材料利用程度,指毛料材的体积与锯成毛料所耗用的成材材积之比。在生产中提高毛料出材率的措施如下所述。
选择合理的配料工艺,在选择成材配料方案时,应该尽量采用画线套裁,或者粗刨后画线然后锯解的配料方案,可以使毛料出材率分别提高9%和12%左右。
尽可能实行零部件尺寸规格化,按照零件的尺寸规格要求选用相应规格的锯材,如此可充分利用板材的幅面,锯出更多的毛料。
材料上的节子、裂纹、局部腐朽、钝棱等缺陷,假如是零部件允许的缺陷,在不影响家具质量的情况下,没有必要过分去除,应尽量修补。
在配料时,应该根据板材质量,将各种长度规格的毛料搭配下锯。
将配料时剩下的小料加工成细木工板、碎料板等以代替拼板使用,将小料在长度、宽度和厚度方向上进行胶拼,使窄料变宽、短料变长、薄料变厚。对于弯曲零件,假如先将板材预先拼成宽板再锯解,也可提高木材利用率。
1.3.5 加工余量
加工余量指将毛料加工成形状、尺寸和表面质量等方面都符合设计要求的零件时所切去的那部分材料,即毛料尺寸和零件尺寸之差。
工序余量
工序余量指为了消除上道工序所留下来的形状与尺寸误差,而从工件表面切去的那一部分木材。因此,工序余量应该是相邻两工序的工件在某个尺寸方向上的尺寸之差。
总加工余量
总加工余量是为了获得形状、尺寸和表面质量都符合于技术标准要求的零部件时,从毛料表面切去的木材总量。所以,总余量等于各工序余量之和。假如毛料是湿料,还要加上毛料的干缩余量。
在生产实践中,生产人员总结了一些加工余量的经验值,见表 1‑4。
表1-4 加工余量经验值

1.3.6 毛料加工
为了获得准确的尺寸、形状和光洁的表面,必须对方材毛料进行再加工。首先加工出准确的基准面,作为后续工序加工的基准,再逐一加工其他面,这被称为毛料加工。
1 基准面加工
基准面指作为精确加工定位基准的表面,作为加工基准的边为基准边。
基准面一般包括平面(大面)、侧面(小面)和端面3个面。根据不同的加工要求,不同的零部件不一定需要这3个基准面,有的仅需要将其中的一个或两个面精确加工成定位基准。有的零件加工要求不高,可以在加工基准面的同时加工其他表面。
基准面的加工通常采用平刨加工和铣削加工两种方式。
平刨加工
平刨加工又可分为手工进料平刨加工以及机械进料平刨加工两种。
手工进料平刨加工在生产中使用广泛,可以消除毛料的形状误差以及锯痕等,常用平刨床进行加工。对基准面的平直度要求较高的零件,需要用平刨床进行加工。这是因为手工进料对工件的垂直作用力较小,工件弹性变形就小,因此刨削后弹性恢复变形小,刨削面的平直度高。
机械进料方式主要有压轮进料、履带进料及尖刀进料装置等。是在手工进料平刨机上增设了自动进料装置而构成的,其原理是对毛料表面施加一定的压力后所产生摩擦力来实现进给的。
铣削加工
在毛料加工工艺中,铣床可以加工基准面、基准边以及曲面。
在加工基准面时,将毛料靠住导尺进行加工,这种方法适合宽薄或宽长的板材侧边加工。加工曲面时需要夹具、模具,夹具样模的边缘必须与所要求加工的形状相同,而且具有精确度高和光滑度好等特点,毛料固定在夹具上,样模边缘紧靠挡环移动就可以加工出所需要的基准面。
侧基准面加工时,如果要求它与基准面之间呈一定角度,就必须使用具有倾斜刃口的铣刀,或通过刀轴、工作台面倾斜来实现。
2 相对面加工
基准面加工完成后,为使零件规格尺寸和形状达到要求,还需要加工毛料的其他面,使之平整光洁,这种类型的加工称之为相对面加工。相对面加工通常指毛料宽度和厚度上的加工。相对面加工可以在单面压刨、三面刨、四面刨和铣床上进行加工,有时候也可以使用平刨和手工刨加工。
刨床加工
压刨常用于相对面与相对边的加工,能将工件刨成一定厚度和光洁的平表面。此外,压刨还可以加工相对面为曲面或者平面很窄的工件。
双面刨可对实木工件相对的两个平面进行加工,来获得等厚的几何尺寸和两个相对的平整表面。四面刨可以同时加工相对面和相对边,生产效率和加工精度较高。
如图 1‑6所示为压刨床及压刨床作业。

图1‑6 压刨床及压刨床作业
铣床加工
在基准面加工后,可以在铣床上利用带模板的夹具来加工相对面。在加工时,要根据零件的尺寸,调整样模和导尺之间的距离或采用夹具。该方法适合于宽毛料侧面的加工,表面光洁度、尺寸精度都较高,但生产效率远低于单面压刨,且生产安全性也较低。
1.3.7 净料加工
毛料经过刨削、锯截等加工后,其形状、尺寸及表面光洁度都达到了规定的要求,制成了净料。按照设计要求,还需要进一步加工出各种榫头、榫眼、孔、型面、曲面、槽簧等,并且进行表面修整加工,使其符合设计要求。
1 榫结合的分类与应用
榫结合是框架式实木家具结构中的一种基本结合方式。榫卯接合的基本组成是榫头和榫眼,在工件的端部加工榫头的工序称为开榫。
榫结合的分类与应用见表 1‑5。
表1-5 榫结合的分类与应用

续表

与整体榫相比,插入榫可以节约木材5%~6%,还可以简化工艺过程,大幅度提高生产率。同时,插入榫结合也可以为家具部件化涂饰和机械化装配创造有利的条件。
圆榫的结合强度比直角榫低,但多数榫的结合强度远超过了可能产生的破坏应力,另外还可以通过圆榫的数目来提高强度,因此在一般情况下使用圆榫都能满足使用要求。
2 榫结合的技术要求
为保证家具结合强度,榫头与榫眼必须符合一定的要求。为提高直角榫的结合强度,应该合理确定榫头的方向、尺寸及榫头与榫眼的配合公差,见表1‑6。
表1-6 直角榫结合技术要求

榫头与榫眼的尺寸定义如图 1‑7所示。

图1‑7 榫头与榫眼的尺寸定义

图1‑7 榫头与榫眼的尺寸定义(续)
圆榫结合的技术要求见表 1‑7。
表 1-7 圆榫结合的技术要求

1.3.8 型面和曲面的加工
锯材配料后,加工成直线形方材毛料,其中一些需要制成曲线形毛料,将直线形或曲线形的毛料进一步加工成型面即净料的加工过程。由于功能或造型的要求,家具的有些零部件需要加工成各种型面或者曲面。
1 直线形零件的加工
直线形零件的断面呈一定型面,而长度方向上为直线。所以一般采用成型铣刀进行加工,可以在下轴铣床、四面刨等机床上加工。刀刃相对于导尺的伸出量即为需要加工型面的深度,加工时工件沿导尺移动进行铣削。
2 曲线形零件的加工
曲线形零件的断面无特殊型面或者呈简单曲线形,长度方向呈曲线形,这种形式多见于椅后腿、沙发扶手、望板等。这类零件可在铣床使用样模夹具进行加工,样模边缘的形状要符合所加工的零件形状,在样模表面要有定位与夹紧装置。当样模边缘沿挡环移动时,刀具就能在工件表面加工出所需的曲线形表面。
3 雕刻加工
目前市场上很多夹具表面都有一些雕刻图案,具有装饰零件、美化夹具外形的作用,如在中式家具中就大量使用雕花来进行装饰,如图 1‑8所示。在进行加工时,通常是在上轴铣床之类的机床上进行加工的,如在零件的表面雕刻线型,如图 1‑9所示为在为门制作凹凸造型。
在工作台上需要有仿型定位销,仿型定位销与刀轴的中心应在同一垂直线上,样模边缘应紧靠仿型定位销移动,即可加工出所需要的曲线形状。
上述方法适用于零、部件侧面的加工,但是生产率较低。此外,利用上轴铣床雕刻加工时,可以将设计完成的花纹首先做成相应的样模,接着将其安装在仿型定位销上,再根据图案的断面形状来选择端铣刀。加工时样模的内边缘沿仿型定位销移动,刀具就能在零件表面雕刻出所需要的花纹图案。

图1‑8 中式条案雕花装饰

图1‑9 铣床雕刻加工
4 回转体零件的加工
回转体零件如圆柱形、圆台形的脚、腿、拉手等,其加工基准为中心线,其断面呈圆形。这类零件的加工主要在车床上进行,可以在工件的长度上加工成同一直径,还可车削成各种断面形状或在表面上车削出各种花纹。在车削前,先找准零件两端的中心位置,再将零件两端的中心对准车床两端的顶针,并且利用车床尾部的顶针将零件夹紧。启动车床后,工件做高度运动,车刀便开始加工零件了。
5 复杂外形零件的加工
复杂外形零件,例如,家具中的弯形腿、鹅冠脚等。这类零件的断面和长度方向都呈复杂外形,是由平面与曲面或曲面与曲面构成的复杂形体。
加工前,按弯脚形状、尺寸要求先做一个样模,接着在铣床上将仿型轮紧靠样模,样模和工件做同步回转运动。加工时,仿型铣刀既做旋转切削运动,又跟随仿型轮按样模旋转轨迹做同步纵向和横向的平面进给运动,直到加工完成。
1.3.9 表面修整
在对家具进行刨削、铣削等加工过程中,因为受到设备的加工精度、加工方式、刀具、工艺系统的弹性变形以及工件表面的残留物、加工搬运过程的污染等因素的影响,使得加工工件表面出现了毛刺、凹凸不平、撕裂、压痕等缺陷。家具零部件表面的质量会直接影响后续的油漆工序以及家具成品的质量,所以必须通过表面修整加工来解决表面存在的缺陷。
表面修整加工的方法主要是采用各种类型的砂光机进行砂光处理,如图1‑10所示为常见的几种砂光机。砂光是利用砂光机对工件表面进行修整的一种加工方法,利用各种砂带将零部件表面砂磨平整、光滑。砂光机上的切削工具是砂带,砂带的粗细是由砂带的粒度号决定的,实木砂光机使用的粒度号主要有800、400、200、120、100、80、60、40 等,数值越大,粒度越细,能得到的零部件表面越平滑。

图1‑10各种样式的砂光机
1.3.10 胶合加工
在家具生产中,尺寸较大的实木会因为木材的干缩和湿胀特性,使得零件产生翘曲变形、开裂等问题,而且零件尺寸越大,这种问题就越严重。通常情况下宽度尺寸为600~700mm的零件,尺寸上的变化可以达到10~20mm,这会严重影响家具的质量及外观。
在实木家具生产中,幅面较大的板件往往是通过小料加压胶合而成宽幅面的集成板,较长的零部件通过短料接长,较厚的板件通过较薄的板件胶压而成,最后加工成所需的规格尺寸和形状零件,这种加工工艺称之为胶合。
胶合工艺不仅可以节约材料,提高木材利用率,还可以同时改善家具的质量与性能。
1 方材胶合的种类
长度方向上的胶合
1 对接
对接的胶合面是断面,由于木材端面不容易加工光滑、渗胶多,难以获得牢固的胶合强度,通常情况下只用于覆面板芯板和受压胶合材的中间层。因此,木材长度方向的胶合通常采用斜面接合或齿榫接合。
2 斜面接合
为了提高木材横截面的胶接强度,将木材的端面锯成斜面,如图1‑11所示,以增加其胶接的面积。木材端头的斜面越长,胶接面积越大,结合强度就越高。
3 指形榫接合
将木材两端加工成指形榫进行胶接,如图1‑12所示。有些指形呈现在木材的上、下表面,有些呈现在木材侧面,应该根据产品的需求来确定指形的位置。使用指形榫胶接,其接合强度大,损耗的材料少,同时也方便实现机械化生产,是使用最广泛的胶合方式。

图1‑11 斜面接合

图1‑12 榫接合
宽度方向上的胶合
1 平拼
将侧面刨切平整、光滑,再利用胶黏剂进行胶合,拼板时不用开槽和打眼。在拼板的背面可以有1/3的倒棱,因此在材料利用上比较经济。但是这种方式的胶接强度低,表面容易发生凹凸不平的现象。不过这种方法工艺简单,接缝严密,是常用的拼板方法。
2 裁口拼
将侧面刨切成阶梯形表面,再利用胶黏剂进行胶合。这种胶合方式的强度比平拼的要高,拼板表面的平整度也要好得多。但是材料消耗会相应增加,比平拼要多消耗6%~8%的材料。
3 槽榫拼
将侧面刨切成直角形的槽榫或榫槽,再利用胶黏剂进行胶合,这种胶合的强度更高,表面平整度较好,材料消耗与裁口拼接方式基本相同。在胶缝开裂时,仍然可以掩盖住缝隙。拼缝密封性好,经常用于面板、门板、旁板等的拼接。
4 指形拼
将侧面刨削成指形槽榫,胶接面上有两个以上的小指形。这种拼接方式接合强度最高,拼板表面平整度高,拼缝密封性也好,经常用于高级面板、门板、搁板、望板、屉面板等的拼接。
5 插榫拼
将侧面刨削成平整光滑的表面,利用圆榫、方榫或竹钉与胶接合。这种拼接方式可以提高胶结合强度,节约木材,材料消耗量与平拼基本相同。
6 穿条拼
将结合面刨削成平整光滑的直角榫,利用木条与胶结合。这种拼接方式能提高胶合强度,节约木材。材料消耗与平拼基本相同,工艺比较简单。
厚度方向上的胶合
厚度尺寸较大的方材,可以充分利用小材胶合而成,以提高稳定性,并且节约材料。厚度胶拼主要采用平面胶合的方式。在胶拼前,要使锯材表面平整光滑,厚度均匀,不能有过多的缺陷。
2 胶合的工艺条件
胶黏剂的性能包括胶黏剂的固体含量、黏度、聚合度、p H值等,但是胶黏剂的固体含量和黏度对胶合强度影响较大。在胶合前,首先要根据胶合材料的种类和胶合部位的使用要求来选择胶黏剂。
涂胶量
以胶合表面单位面积的涂胶量表示,其与胶黏剂种类、浓度、黏度、胶合表面粗糙度及胶合方法等有关。涂胶量过大,胶层厚度大,胶合强度反而低。胶涂量过少,不能形成连续胶层,则胶合不牢。黏度高的胶黏剂容易涂胶过度,通常情况下合成树脂涂胶量小于蛋白质胶。
陈化时间
陈化时间指材料被涂胶黏剂后至加压胶合的时间,它与胶合室温、胶液黏度及活性期有关。陈化可以使胶液充分湿润胶合表面,使胶液扩散、渗透,并排除胶液中的空气,提高胶层的内聚力,也可以使胶黏剂中的溶剂挥发,确保胶层浓缩到胶压时所需的黏度。
陈放时间
陈放时间是指材料被胶合后,从卸压到进行下一道工序加工这段时间。陈放是为了让板件性能更适合加工。无论冷压或热压,都需要一段时间才可以使得胶合反应完成。
胶层固化条件
固化指胶黏剂在浸润了被胶合材料表面后,胶黏剂由液态变成固态的过程。方材胶合时,控制好压力、温度和时间是保证胶合质量的重要条件。
1 胶合压力
胶合时所加的压力能保证胶合表面之间必要的紧密接触,形成薄而均匀的胶层。压力大小应该随着胶合木材的树种、表面加工质量、胶液特性、涂胶量等条件而变化。
2 胶合温度
提高胶合时的温度,可以加速胶层固化,缩短胶合时间。但是温度过高,有可能使胶发生分解,胶层变脆。但是温度太低,可能会因胶液尚未充分固化而使得胶合强度降低,严重的会无法胶合。
3 加压时间
加压时间指胶液凝固前开始加压到胶液固化为止的一段时间 ,加压时间的长短取决于胶液的固化速度。
1.3.11 弯曲加工
为满足家具的造型及使用功能需要,有些零部件常做成曲线或曲面,其线条流畅,形态各异。经常使用的加工方式有两种,一种是锯制加工,另一种是加压弯曲成型。
加压弯曲
方材弯曲加工时,首先将配制好的直线形方材毛料进行软化处理,然后利用模具加压弯曲成所要的曲线形状的过程。在实木弯曲时,在凸面产生拉伸力,在凹面产生压缩力,中间一层既不受拉伸力也不受压缩力,称为中性层。
方材经过软化处理后应该立即进行弯曲,将已经软化好的木材加工弯曲成要求的形状。加压弯曲的方法主要有手工和机械两种方式。
1 手工弯曲
手工弯曲即用手工木夹具来进行加压弯曲。夹具用金属或木材制成的样模、金属夹板(要稍大于被弯曲的工件,厚0.2~2.5mm)、端面挡块、楔子和拉杆等组成。这种方式适用于加工数量少、形状简单的零件。
2 机械弯曲
使用机械对大批量的木材进行弯曲,通常采用U形曲木机和回转型曲木机进行加工。U形曲木机用于加工各种形状不对称、不封闭的零件,如椅腿、椅子扶手等。回转型曲木机可以弯曲各种封闭的零件,如圆环形椅子座圈等。
干燥定型
在工件弯曲后进行干燥处理,可以降低木材的含水率,除去残余应力,以免回弹,保持弯曲零件尺寸的稳定性。弯曲工件的干燥常采用热空气干燥方法,但是干燥温度不能过高,通常为60~70℃,干燥的时间为15~40个小时。
在干燥的过程中,将弯曲毛料连同模具和金属带固定在定形架上(或者卸去模具和金属带,仅将弯曲毛料固定在定形架上,以确保弯曲毛料的尺寸稳定),然后将工件送进可以控制温度和湿度的热空气干燥室内。
弯曲零部件的加工
因为方材毛料弯曲后,其加工表面或加工基准已经不准确,假如需要达到高质量的要求,还需要进行再次加工。其加工方式与方材毛料的加工近似,只是需要重新确定基准和型面加工后,还要根据要求进行铣榫头和开榫眼加工,再进行砂磨修整即可。
1.3.12 装配工艺
家具都是由若干零件、部件接合而成的,按照设计图样和相关的技术标准,使用相应的工具或机械设备,将零件接合成部件或将零、部件接合成为成品的过程,称为装配。
将零件接合成部件,称为部件装配。将零、部件接合成为成品,称为总装配。因为家具的类型较多,其装配工艺也不大相同。结构简单的家具,可以由零件直接装配成成品。而结构复杂的家具则需要先把零件装配成部件,部件经过修整加工后再装配成成品。
通常情况下家具的装配工艺流程如图 1‑13所示。

图1‑13 家具装配工艺流程