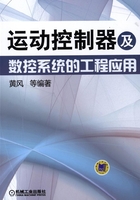
第1篇 运动控制器应用案例
第1章 大型包装机多轴同步运行控制系统的设计开发及伺服系统的调试
本章论述了基于三菱运动控制器构建多轴高精度同步运行系统的技术方案,特别介绍了在实际调试由运动控制器和伺服电动机构成的控制系统中,对伺服电动机的调试和排除影响系统稳定性因素的过程,对实际使用运动控制器和伺服电动机有很实际的帮助。
1.1 项目背景及主控制系统方案
1.1.1 项目背景
某机床厂客户生产的大型包装机,其主要功能及动作要求如下:
1)包装机有8个运动工步,每个运动工步配置有1个运动轴,8个运动轴要求同步运行。
2)包装机由于工步多、分布长,每个工步有不同的输入/输出(I/O)点,还有模拟量输入信号和高速计数信号。
3)在主操作屏上要求采用触摸屏进行数据输入和显示。
4)控制系统采用上位机进行生产管理和远程监控。
为满足大型包装机的复杂动作要求,经过综合技术经济分析,决定以三菱运动控制器为核心,以三菱QPLC为主控,以CC-LINK总线为网络,构建大型包装机的控制系统。
1.1.2 主控制系统方案
控制系统方案如下:
1)8个运动轴的控制采用三菱Qmotion运动控制器加上伺服电动机。由于包装机的核心技术要求是8个运动轴“同步运行”,而在三菱的运动控制单元中,只有Qmotion运动控制器有“同步运行”控制功能,所以必须采用“Qmotion运动控制器”。
2)顺序控制部分采用三菱Q02UCPU,Q02UCPU负责处理来自CC-LINK现场总线传送的各工步的输入/输出信号、A-D/D-A信号和高速计数信号。
Q02UCPU与触摸屏GOT连接,实现对外部开关信号和数据信号的处理。
1.2 电气控制系统设计方案
1.2.1 包装机核心技术要求——多轴同步运行
包装机的核心技术要求是在上电后的各种工作状态(点动、手轮)下8个工步的辊筒的线速度一致,不仅是线速度一致,而且要求保证在整个自动运行中的“相位”一致(即各轴的相对位置始终一致,即使在加减速过程中也必须一致。由于加减速过程中实际速度有滞后于指令速度的现象,各轴的相对相位会发生变化,就造成了相对相位的变化)。
1.2.2 同步控制设计方案
1.电气主控系统硬件的构成
为了构成8轴同步运行系统,在三菱现有产品序列中,只有“运动控制器+SSCNET3+MR-J3-B”的构成方式。这种方式有以下优点:
1)MR-J3-B伺服系统是可以使用“光纤电缆构成的SSCNET3高速串行通信”伺服系统。运动控制器通过SSCNET3与各伺服系统相连,通信速度为50MB/s(相当于单向100MB/s)。系统响应能力很高。
2)通信周期高达0.44ms,使运行更加平滑。
3)光纤抗干扰能力强,并且可减少布线误差,最长布线距离可达800m。
4)控制器和伺服放大器之间进行大量数据的实时发送与接收。伺服驱动器的信息可在“运动CPU”中处理。
2.虚模式
为了实现多轴同步运行控制,三菱运动控制器提供了一种“虚模式”的程序构建方式,用于实现多轴同步运行。
1)在虚模式模式下,实际伺服电动机由一套“电子软元件构成的机械传动系统”驱动,而这些电子软元件是“运动控制器”内部所特有的软元件。
这套“电子软元件构成的机械传动系统”由以下元件构成:
①驱动源——虚电动机及同步编码器。
②传动元件——齿轮、离合器和差速齿轮。
③输出模块——圆筒、丝杠、圆盘和凸轮。
必须注意:这些元件都是电子软元件。
2)“电子软元件构成的机械传动系统”与实际伺服电动机的关系由虚模式中“输出模块”的参数来设定。
3)由于实际上没有这套“机械传动系统”,所以就称为“虚模式”。
4)主要利用虚模式构建“同步运行系统”。
由于电子软元件代表的机械部件具有足够的柔性,所以其构成的“机械传动”系统也具有足够的柔性,可以满足实际需要的运动要求。
3.使用虚模式构成的“同步系统”
图1-1所示是根据包装机的实际运行要求,用虚模式中的电子软元件构成的一套多轴机械传动系统。图1-1中的电动机、传动轴、齿轮、辊筒(输出模块)全部是电子软元件,但这些电子软元件全部可以设置参数而赋予其工作性能(如齿轮齿数比)。
通过设置输出模块的参数建立起输出模块与实际伺服电动机的关系。
图1-1 用虚模式构成的多轴机械传动系统
在图1-1中,只要通过运动程序向“主虚拟电动机”发出指令,各实际伺服电动机就能够按照图1-1中这套机械传动系统运行。在设定的机械系统参数都相同时,各伺服电动机就按“同一速度运行”。由于MR-J3-B伺服系统是使用“SSCNET3高速串行通信”,运动控制器通过SSCNET3与各伺服系统相连,通信周期为0.44ms,从而保证了同步运行的要求。
在这套“虚模式电子机械传动系统”的驱动下,可以实现点动(JOG)运行、手轮运行和自动运行。
1.3 伺服系统调试
在大型包装机项目中,伺服电动机所驱动的对象是大型辊筒。辊筒这类负载对象运动起来不像滚珠丝杠驱动的工作台负载那样有所约束,而是辊筒直径越大惯性越大,旋转速度越快电动机负载越大。这类负载对伺服电动机的工作性能要求很高,在实际调试中遇到诸多问题。
1.3.1 同步运行精度超标
在驱动8轴作“同步运行”时,遇到最严重的问题是“同步运行”精度超标。为了分清是机械系统还是电气系统引起的问题,在显示屏上仔细地观察了正常运行时各轴的速度(在Qmotion运动控制器内有专门软元件显示伺服电动机速度),观察发现第1轴速度波动很大,在不同的速度段都存在3~10r/min的速度波动,而其他轴未出现速度波动,显然是第1轴的速度波动引起了同步运行精度误差。
1.3.2 对第1轴速度波动的原因分析
1)电动机基本性能不足。
2)机械负载过大。
3)伺服电动机运行参数未优化。
1.3.3 对电动机工作状态的测试
首先对电动机工作运行状态进行测试,采用专门的测试软件MR-Configrator进行测试,测试结果见表1-1。
表1 电动机工作负载测量表
注:PA08为位置环增益;PA09为自动调谐响应等级;PB06为负载惯量比。
对电动机工作负载测量表中的数据分析:
1)电动机负载(力矩)随运行速度的增加而增加。
2)电动机负载始终在额定范围之内。
3)电动机峰值负载未超过额定值。电动机峰值负载是指在加减速过程中出现的最大值。实际工作区域是不含加减速阶段的。
在不同速度下的实际工作区域都观察到:电动机速度有3~10r/min的波动。
从测试数据分析可知:电动机的工作负载在额定范围之内。所以可以得出结论:电动机选型没有问题。
1.3.4 对机械负载进行分析
第1轴的机械负载有下列特点:
1)辊筒质量不大,比其他轴辊筒质量小。
2)带有偏心齿轮箱。
3)带有间歇性凸轮机构。
虽然有“偏心齿轮箱”和“间歇性凸轮机构”等不利因素,但是这些不利因素已经综合反映在工作负载上。而且本机的第5轴配用同功率的伺服电动机,辊筒质量比1轴大2倍,但实际运行中没有速度波动。所以出现的问题令人迷惑。
1.3.5 对伺服电动机工作参数进行调整
伺服电动机工作参数也是影响电动机正常运行的因素。为此必须优化工作参数。包装机在正常工作时主要是作速度控制运行,相关的伺服参数调整如图1-2所示。
图1-2 伺服参数调整
1.第1级重要参数
参数“负载惯量比PB06”和“自动调谐响应等级PA09”是确定整个伺服系统响应等级的主要参数。
1)在系统自动调谐时,“负载惯量比PB06”由“反馈电流”和“反馈速度”所确定。即反馈电流越大,说明负载越大(负载惯量就越大)。反馈速度越低于指令值,说明负载越大(负载惯量越大)。
在实际调试中观察到有实际速度高于指令速度的现象,这说明设定的“负载惯量比”大于实际机械的“负载惯量比”,伺服系统加大了对伺服电动机的驱动,所以导致了伺服电动机的速度变大。
当实际速度低于指令速度时,说明设定的“负载惯量比”小于实际机械的“负载惯量比”,伺服系统对伺服电动机的驱动不足,所以导致了伺服电动机的速度变小。
调试的第一步是正确估算“负载惯量比”。先降低“自动调谐响应等级PA09”(7~9),然后逐步升高“负载惯量比”。
1轴带两辊筒和一齿轮箱,齿轮箱在偏心位置。电动机功率15kW,额定速度下的电流为额定电流的20%~40%。此时调节惯量比为28.8,尚可运行;调节惯量比为33.6,电动机出现鸣叫。所以选择惯量比为28.8是可行的。然后根据速度的超前和落后再减小惯量比。
调试时逐步降低“负载惯量比PB06”,先向下调至抖动后再向上,在1500r/min时不抖。因为电动机要求的惯量比在10以下,因此要逐步测定惯量比。惯量比设定过小,运行抖动;惯量比设定过大,则速度超过指令速度。
2)“系统响应等级PA09”是最重要的参数,对系统运行影响最大。当1轴PA09=12时,震荡很大;PA09=7时,震荡消除。因此,应该逐步增大该参数。该参数对系统刚性影响最大,其设置范围为0~300,出厂时设置为7。
2.第2级伺服参数
1)PB07——模型环增益。参数PB07是用于设置到达“目标位置”的响应增益。增加参数PB07值可以提高指令响应性以改善运动轨迹性能。参数PB07还是属于改善位置控制功能的参数,所以简称PG1。参数PB07对消除加减速过程中各轴的相位误差有重要作用。
2)PB08——位置环增益。参数PB08用于增加位置控制响应级别,以抵抗负载干扰的影响。参数PB08值设置较大时,响应级别增大,但会导致震荡及噪声。本参数不能用于速度控制模式。
3)PB09——速度环增益。参数PB09值设置较大时,响应级别增大,但可导致震荡以及噪声。本参数对速度控制尤为重要。
PB09是最重要的参数之一,调节范围为1~3000。应该逐步上调,直至振动为止;然后往下调,遇有振动,设置共振频率抑制。该参数的单位是rad/s。
4)PB10——速度积分时间补偿。参数PB10用于设置速度环的积分时间常数。PB10值设置较小时,响应级别增大,但会导致震荡以及噪声。以不振动为原则,从大到小调节。
在系统作速度控制时,第1级重要参数为:PB06、PA09、PB09和PB10,第2级重要参数为PB07和PB08。
小结:对以上所有参数在可能的范围内进行了调节,但是仍然无法消除1轴的速度波动,因此,可以判断不是伺服电动机运行参数的问题。
1.4 对系统稳定性的判断和改善
对伺服电动机驱动的机械系统而言,影响系统稳定性的因素除了机械负载的大小以外,还有“转动惯量比”这一因素。
三菱MR-J3系列的伺服电动机要求转动惯量比小于10。目前的系统能够满足这一指标吗?由于包装机传动系统复杂,机械制造厂家本身未计算每一轴的机械系统“转动惯量”,而是比照经验来选取的伺服电动机。既然第5轴在大负载的情况下能够稳定运行,为何第1轴不能够稳定运行?而且第1轴一直出现速度波动的现象,所以一定是有一“固定因素”在起作用。
1.4.1 减速比的影响
再一次检查机械电气配置及参数时,发现第1轴的减速比为2.4,而其余各轴的减速比为6。显然这是问题的根源。由于减速比对负载转矩及惯量比影响极大,特别对于“负载惯量”是成“平方反比”的关系。以下详述减速比的影响。
假设负载惯量为J0,负载惯量折算到电动机轴的惯量为JL,减速比为n,则
JL=J0(1/n)2
因此,假设5轴和1轴的负载惯量J0相同,由于减速比不同,则J0折算到电动机轴的负载惯量为
5轴
JL5=J0(1/n)2=(1/36)J0=0.0278J0
1轴
JL1=J0(1/n)2=J0(1/5.76)=0.17J0
由此可见,1轴的负载惯量是5轴负载惯量的6.1倍,或5轴的负载惯量是1轴负载惯量的16.4%。所以,1轴有偏心负载和间歇性负载的共同作用,负载不大但形式恶劣。间歇性负载也是引起波动的原因之一,但关键是由于减速比的影响,实际负载折算到电动机轴的负载惯量较大。因此,5轴电动机实际上的负载惯量小,而1轴电动机实际上的负载惯量大。由于三菱伺服电动机要求转动惯量比小于10,超出该指标后系统不稳定,所以减速比是造成1轴速度不稳的原因。
1.4.2 改变机械系统减速比提高系统稳定性
为了消除速度波动,对机电系统做了如下改善:
1)将1轴齿轮箱减速比改为5。
2)更换1轴伺服电动机为HA-LP15K24,其基本性能为15kW、2000r/min。
在以上的机电配合下,原转动惯量为0.17J0,改换减速比后的转动惯量为0.04J0,转动惯量下降76%,这样就大大改善了电动机的负载状况。而1500r/min电动机的转动惯量为295,2000r/min电动机的转动惯量为220,假设当前惯量比=0.17J0/(295×0.0001)=5.76J0,更换后的惯量比=0.04J0/(220×0.0001)=1.82J0,即更换后的惯量比仅为原来的31.5%。
选择额定速度为2000r/min的电动机,是为了提高整机的运行速度。经过机电部分的同时改善,整机系统的稳定性得到大大提高,消除了第1轴的速度波动,保证了包装机的同步运行精度。
1.5 结束语
采用三菱Qmotion运动控制器通过虚模式可以构成高精度多轴同步运行系统。在进行伺服系统调试时,要充分注意检查机电配合,判断机电系统的稳定性,然后通过调整伺服系统的参数可以使伺服系统在最佳状态下运行。