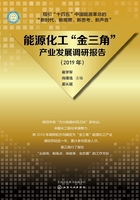
1.1 中国煤化工产业具有良好的发展基础
中国“缺油、少气、富煤”的资源禀赋,催生了深度加工煤、转化煤的煤化工产业,包括传统煤化工和现代煤化工。现代煤化工兴起于21世纪初,但它又并非一个进入新世纪后才诞生的全新产业,它脱胎于传统煤化工,与在中国已有60多年积淀发展的煤焦化、煤头合成氨等传统煤化工是一脉相承的,仅仅是中国煤化工这个体系在不同的发展阶段、不同的历史时期、不同的环境条件之下不同的表现形式而已。科学地认识现代煤化工,就应该将煤化工作为一个整体的体系,并纵观整个历史发展的进程,而不是静止地、孤立地和割裂地来看传统煤化工或现代煤化工。确立了系统认识论这一正确的方法,我们才能看清现代煤化工的真容和全貌,当前社会上针对现代煤化工的诸多质疑、迷惑、分歧等,才有可能追根溯源、解开谜团,得到比较科学可靠的解答。
新中国成立后,为满足国民经济建设急需的钢铁和粮食生产,煤焦化、煤头氮肥工业应运而生。进入21世纪,针对国际油价出现新一轮大幅上涨、国内原油对外依存度节节攀升的现实情况,煤制油、煤制气、煤制烯烃等现代煤化工破茧而出。时代背景不同,煤炭转化的重点方向和煤化工的工艺技术路径也各异,但它们都有一个共同的基础依托,那就是中国的国情及资源禀赋——“缺油、少气、富煤”。
我国氮肥生产从20世纪30年代起步, 初期只有5家生产企业,主要以焦炭为原料。新中国成立后,为了尽快让中国人吃饱肚子,国家开始高度重视发展氮肥工业,在前后近40年的时间中,氮肥工业的建设投资占化肥工业总投资的80%以上。
20世纪50年代中期,永利宁厂用无烟块煤代替焦炭制取合成氨原料气的试验成功,为利用我国比较丰富的无烟煤资源、扩大氮肥原料来源、加快发展氮肥工业创造了条件,其实这也宣告中国煤化工的诞生。与此同时,我国焦化工业也蹒跚起步,1958年我国建成了首个拥有自主知识产权的机械化焦炉——北京焦化厂58型焦炉,随后在钢铁工业快速发展的带动下,我国焦化工业也步入发展快车道。
1958年,我国开始自主建设小氮肥示范厂。进入20世纪60年代初,在消化吸收国外援建中型氮肥厂的基础上,国内建设了多套小型氮肥装置,主要以无烟块煤为原料生产合成氨。以此新工艺路线为依托,我国很快形成了县县都有小氮肥厂的盛况,到80年代小氮肥行业的鼎盛时期,全国一度出现1500多家小氮肥企业,小氮肥成为这一时期全国氮肥行业发展的主力军。
立足中国丰富的煤炭资源,在党和国家的大力支持下,小氮肥为中国农业和工业生产立下了不朽功勋。1959年10月28日,毛主席亲临安徽蜀山化肥厂(合肥化肥厂)视察后,大加赞赏:“一个化肥厂可以解决一个公社问题,一亩地几十斤化肥就基本解决了。”陈云同志为新中国的化肥工业尤其是小氮肥的发展呕心沥血,奠定了我国以煤头为主导的氮肥工业的雏形。朱镕基总理也关注小氮肥的发展,1999年12月25日,他针对氮肥工业作了重要批示,在对中国氮肥工业协会“关于继续扶持小氮肥产品结构调整”的报告上朱总理批示:小氮肥的技术改造应予以重视……小氮肥以煤为原料,对维持煤炭生产有好处。
在自主发展小氮肥的同时,我国也曾经走过了一段引进国外技术装备发展大氮肥的探索之路。20世纪70年代,我国引进了13套30万吨/年合成氨的大型化肥厂。20世纪80~90年代,由于农业发展对化肥的强烈需求,我国又陆续引进了以渣油、块煤、水煤浆、天然气为原料的18套大型合成氨和氮肥装置,且引进的技术更加多样化,涉及煤头、油头、气头等多种工艺路径。但总体来说,我国氮肥工业主要是依靠自己的力量发展起来的,这主要体现在持续数十年的技改升级和技术装备自主创新之上。
20世纪50年代末至60年代初,我国就开发了以煤(焦)为原料的合成氨技术和碳化法生产碳铵技术,先后编制了2000吨/年、3000吨/年合成氨县级氮肥厂,以及1万~2.5万吨/年专区级氮肥厂和5万吨/年合成氨的省级氮肥厂的定型设计,开启了我国氮肥工业大规模建设的新篇章。20世纪80~90年代,“两煤变一煤”“两水闭路循环”技术的成功开发,大幅度降低了合成氨能耗和水耗;碳铵改产尿素、尿素“4改6”“6改10”技术的推广,显著提高了高浓度氮肥的比例。
我国合成氨企业的煤制气技术长期采用的是固定床水煤气炉,以无烟块煤为原料,面临炉型老化、技术落后、能源利用率低、原料价格高等问题,必须进行大的技术改造,尤其是要研发简单可行又可就地取得原料的洁净煤气化技术,降低生产成本,改善生产环境。基于此,进入20世纪90年代末,我国开始自主开发大型氮肥技术,以华鲁恒升水煤浆气化30万吨/年合成氨大氮肥国产化项目为契机,氮肥工业陆续开发出一批拥有自主知识产权的新型水煤浆和干粉煤煤气化、大型气提法尿素等一系列重大技术成果,包括水煤浆气化、粉煤气化、节能型低温甲醇洗和液氮洗、一氧化碳等温变换、常温精脱硫、醇烷烃化气体净化、大型低压氨合成、大型低能耗空分设备等,有力地促进了氮肥产业核心竞争力的提升。目前氮肥行业已具备10万等级空分、3000吨级水煤浆气化、2000吨级干粉煤气化、大型低温甲醇洗、液氮洗、60万吨级氨合成、80万吨级尿素等装置的设计制造能力。自主大氮肥技术体系的快速发展,不仅让能耗、物耗、排放“三高”的小氮肥逐步退出了历史舞台,同时终结了中国依靠国外技术建设大氮肥装置的历史,也为进入新世纪以后快速崛起的我国现代煤化工产业发展奠定了技术基础。
从结构调整的演变来看,20世纪90年代,在高油价和石油深加工技术进步的双重压力下,我国以天然气、轻油、重油、煤炭作为合成氨原料的多元并立格局有了很大的变化。基于装置经济性考虑,轻油和重油型合成氨装置已经不具备市场竞争力,绝大多数装置被迫停车,或开始进行以“原料结构和产品结构调整”为核心内容的技术改造。原料结构调整包括轻油型装置的“油改煤”(采用Shell或Texaco煤气化工艺,以煤炭替代轻油)、渣油型装置的“油改气”(采用天然气部分氧化工艺,以天然气替代渣油)或“渣油劣质化”(使用脱油沥青替代渣油);产品结构调整包括转产或联产氢气、甲醇等。合成氨工业优化原料路线、实现制氨原料多元化稳步推进。
从理论上来说,天然气是生产合成氨最理想的原料,且装置改造时改动工作量最小、投资最省,理应予以优先考虑。但由于我国富煤而缺油少气,煤炭的储量约为天然气与石油储量总和的百倍以上,随着进入新世纪以后国内油气原料的瓶颈越来越突出,顺应“原料劣质化”的现实要求,以煤炭为原料生产合成氨和尿素逐渐成为我国氮肥工业的主流。数十年间,煤头、气头、油头合成氨工艺在国内全部得到了系统的实践和验证,但历史最终选择了煤头工艺,煤基合成氨最终成为中国氮肥工业的绝对主导。这实在是一个大浪淘沙始见金的过程,充分验证了煤化工深植于中国,是中国能源和原材料革命的必然结果。
经过60多年的持续发展,如今的中国煤头氮肥工业,早已今非昔比。全国合成氨总产能一度达到8000万吨/年,自1991年成为全球最大氮肥生产国、2003年首次成为净出口国、2007年成为世界最大出口国以来,中国多年稳居合成氨和氮肥工业规模世界第一的宝座。煤头氮肥工业的大发展,不仅让中国人的饭碗里主要装中国产的粮食有了坚实的物质基础,也形成了广泛的世界影响力和产业竞争力。继氮肥产品大批量走出国门后,近年来,中国成套的自主化煤头氮肥技术装备体系也开始向海外输出,在印度、越南等国家落地生根,使中国煤化工的国际影响力进一步外延。
随着源于煤头氮肥工业的自主大型煤气化技术装备的崛起,随着2004年前后国际油价的新一轮起飞,内因和外境的双重影响下,中国的现代煤化工顺势而起,并步入发展的快车道。在现代煤化工崛起的过程中,传统煤化工为其输送了关键的技术、人才甚至是资金,做好了各方面的准备和铺垫。从这个意义来说,现代煤化工脱胎于传统煤化工,是中国煤化工一脉相承的1.0版本和2.0版本,都深植于中国的土壤,有着长期的积淀,厚积之后才得以薄发。从这个意义来说,中国现代煤化工产业具有良好的发展基础。