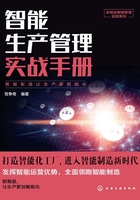
五、智能制造的新模式
《智能制造工程实施指南(2016—2020)》明确指示:“针对原材料工业、装备工业、消费品工业等传统制造业环境恶劣、危险、连续重复等工序的智能化升级需要,持续推进智能化改造,在基础条件好和需求迫切的重点地区、行业中选择骨干企业,推广数字化技术、系统集成技术、关键技术装备、智能制造成套装备,开展新模式试点示范,建设智能车间/工厂,重点培育离散型智能制造、流程型智能制造、网络协同制造、大规模个性化定制、远程运维服务,不断丰富成熟后实现全面推广,持续不断培育、完善和推广智能制造新模式,提高传统制造业设计、制造、工艺、管理水平,推动生产方式向柔性、智能、精细化转变。”
智能制造新模式关键要求如下。
1.离散型智能制造
车间总体设计、工艺流程及布局数字化建模;基于三维模型的产品设计与仿真,建立PDM,关键制造工艺的数值模拟以及加工、装配的可视化仿真;先进传感、控制、检测、装配、物流及智能化工艺装备与生产管理软件高度集成;现场数据采集与分析系统、MES与PLM、ERP系统高效协同与集成。
2.流程型智能制造
工厂总体设计、工艺流程及布局数字化建模;生产流程可视化、生产工艺可预测优化;智能传感及仪器仪表、网络化控制与分析、在线检测、远程监控与故障诊断系统在生产管控中实现高度集成;实时数据采集与工艺数据库平台、MES与ERP系统实现协同与集成。
3.网络协同制造
建立网络化制造资源协同平台,企业间研发系统、信息系统、运营管理系统可横向集成,信息数据资源在企业内外可交互共享。企业间、企业部门间创新资源、生产能力、市场需求实现集聚与对接,设计、供应、制造和服务环节实现并行组织和协同优化。
4.大规模个性化定制
产品可模块化设计和个性化组合;建有用户个性化需求信息平台和各层级的个性化定制服务平台,能提供用户需求特征的数据挖掘和分析服务;研发设计、计划排产、柔性制造、物流配送和售后服务实现集成和协同优化。
5.远程运维服务
建有标准化信息采集与控制系统、自动诊断系统、基于专家系统的故障预测模型和故障索引知识库;可实现装备(产品)远程无人操控、工作环境预警、运行状态监测、故障诊断与自修复;建立产品生命周期分析平台、核心配件生命周期分析平台、用户使用习惯信息模型;可对智能装备(产品)提供健康状况监测、虚拟设备维护方案制定与执行、最优使用方案推送、创新应用开放等服务。
相关链接:海尔集团引领智能制造新模式
海尔集团创立于1984年12月26日,是一家全球领先的美好生活解决方案服务商。在互联网和物联网时代,海尔从传统制造企业转型为共创共赢的物联网社群生态,率先在全球创立物联网生态品牌。
1.创造智能制造新模式
2017年岁末的一份惊喜,对于海尔意义非凡:来自美国电气与电子工程师协会(英文简称“IEEE”)新标准委员大会的消息,正式通过了一项由海尔主导的大规模定制通用要求标准建议书。这是唯一一次由中国企业牵头制定国际标准。史无前例!
过往,福特和丰田创造了工业时代的世界制造模式,影响至深。但是,随着与互联网的深度融合,制造业正在发生巨变:由企业主导的大规模制造逐渐向用户需求驱动下的大规模定制转型。
这是未来物联网时代,全球制造业的方向—智能制造。下图展示的是海尔互联工厂一角。

海尔互联工厂一角
海尔,从2012年开始规划建设互联工厂,大踏步向智能制造探路,到目前成功搭建中国独创、全球引领的工业互联网平台COSMOPlat,其智能制造的实践已经开花结果—几年间,互联工厂借助前期交互平台,实现了与终端用户需求的无缝对接,并通过开放平台整合全球资源,迅速响应用户个性化需求,从而完成大规模定制。
2.打造“海尔互联工厂”样板
时至今日,依托全球首创工业互联网平台COSMOPlat(COSMO取自希腊语,意指“宇宙”,Plat是指“平台”),海尔走出了一条“中国智造”的发展新路—从2015年试水互联网工厂转型,到2017年两年间8个“以用户为中心、用户全流程参与定制”的互联工厂全面落地,定制占比57%,订单交付周期缩短50%,效率提升50%。而在互联工厂基础上不断升级的COSMOPlat,也于2017年正式提供社会化服务,打造“海尔互联工厂”样板。
2017年4月26日,全球工业技术顶尖平台—德国汉诺威国际工业展上,德国工业4.0鼻祖人物齐尔克在海尔展台旁驻足许久。吸引他的,是海尔实体冰箱互联工厂制造示范线。这条长11米、宽7米、高2.5米的模拟流水线,展示了从原料自动上线、半成品组装、激光打印、视觉检测等7个工站、11个节点,真实还原了海尔全流程智能制造体系。如下图所示。

德国汉诺威国际工业展海尔展台
3.构建工业互联网平台—COSMOPlat
COSMOPlat,它是海尔在这几年对智能制造探索基础上推出的中国首个独创的、具备自主知识产权、把互联工厂模式产品化并可对外服务的工业互联网平台。依托COSMOPlat,海尔构建了一个社群经济下以用户为中心,面向大规模定制的新工业生态,完全和用户连接,并以用户体验和用户需求,驱动内部“智能制造”的迭代升级。
强调与用户连接,强调从产品为中心到以用户为中心,把用户需求、用户体验作为推动自身迭代升级的最大驱动力,是海尔智能制造的核心。
一方面,COSMOPlat通过在全流程节点的业务模式变革,输出可社会化复制的应用模块,帮助企业实现产品生产高精度下的高效率。如下图所示COSMOPlat平台。

COSMOPlat平台
另一方面,COSMOPlat可为企业智能制造转型升级提供软硬一体的大规模定制整体解决方案和增值服务。具体提供的服务有两种:软硬一体、虚实融合的智能制造解决方案,如新工厂建设、老工厂升级、企业管理等。另外则通过平台沉淀的数据,为企业提供基于大数据的增值服务,如预测性维护、全产业链的协同优化、资源共享集约及金融服务等。
有业内人士认为:从全球智能制造大背景来看,“海尔模式”与美、德模式有着本质区别。美国以研发能力强而著称,但制造工艺不及德国;德国制造优势突出,但互联网技术渗透程度略逊一筹。
相比之下,海尔COSMOPlat具备了全流程、全产业链的概念和能力,并通过高内聚的系统架构和物理化的系统模块,实践了大规模定制的业务。
一个不容忽视的事实是,将“机器换人”作为“制造”向“智造”转型唯一目的的企业,当下仍不在少数。而过于追求机器带来的高效率,常会因找不到用户,而走向从“产量”到“规模”,再到“价格战”的死循环。目前,国内企业存在的最大问题就是方向不清晰,包括手段、模式都很不清晰。COSMOPlat就是要为所有企业在探索智能制造转型中,提供一个落地的标准与指南,减少试错成本,缩小与先进国家在品牌塑造和创新能力上的差距。
4.“智造”基因融入传统工厂,实现互联定制
海尔对COSMOPlat的自信,更多源自该解决方案在体系内部的成功应用。其已按COSMOPlat思路构建了沈阳冰箱、郑州空调、佛山滚筒、胶州空调、青岛热水器、FPA电机、青岛模具,及中央空调八个互联工厂。
重要的是,互联工厂在此过程中,很好地充当了海尔推广COSMOPlat的“样板间”—海尔希望让每一个对制造升级充满期待的企业感知到,海尔互联工厂“样板间”完全可成为他们“未来工厂”的标配。
而当下最受热议的,当属位于青岛中德工业园区的海尔中央空调互联工厂。这里是全球中央空调行业最先进的制造基地:投资数亿元,占地面积8万多平方米,始建于2016年1月,边建边投产,如今年产能已达30万台,生产效率、库存周转率均提升300%。
走进车间,会发现这里更像一个整洁明亮的办公空间,工人并不多见,柔性生产线上,为数不少的橙黄色机械臂协同运转,井然有序。而恰恰是在这全然不像工业车间的厂区内,大型装备的自动化率竟高达70%以上。如下图所示。

海尔互联工厂生产线
比如,以往在炎热夏天,工人穿着厚厚的工服手工喷漆,汗流浃背。如今,这项工作完全由机器人取代,不仅改善了工作环境,还能解决手工喷漆不均匀问题。
又如,传统中央空调主机生产线均采用人工推动生产,效率低又浪费人力。而今磁悬浮总装线,在借鉴汽车行业动力板链地平线基础上,可根据节拍设定自动运转,做到了6种产品的总装混产,工程不良减少了30%,效率提升了50%。重要的是,该生产线属于用户订单驱动的柔性生产线,即用户的体验信息可上传至生产线相应工位,用户评价与员工薪酬直接关联。对员工而言,这既是压力也是动力。
中央空调互联工厂的“智造”基因,还体现在COSMOPlat智能云服务平台大数据分析上。该平台通过用户使用数据和设备数据分析,可为中央空调用户推送设备诊断、异常预警,以及节能运营等各种增值服务。
借助大数据分析,系统可实现自诊断和自反馈,原来中央空调都是坏了再修,现在通过大数据分析,可在故障发生前提前预测,实现用户零停机,在提升体验之余,还能帮用户节省备用机费用……由此传统买卖关系,就变成了终身用户关系。
除此之外,具备磁悬浮中央空调设备的100%用户定制,是中央空调互联工厂推广的一大亮点,也是与海尔此前7个互联工厂的根本不同。
5.建立共创共赢新模式
形象地说,依托COSMOPlat智能制造平台,海尔互联定制可让每个用户自己“制造”家电。但这背后的关键,仍然基于“人单合一”模式。如下图所示。

海尔“人单合一”模式
“人单合一”始自2005年,是海尔CEO张瑞敏提出并命名的一种全新商业模式。经过长达12年的探索,“人单合一”如今已进入2.0时代,有了新内涵,即建立一个互利共生的平台。
从实践上看,“人单合一”的新诉求,无不倒逼着海尔对组织颠覆、流程升级、机制创新等方面进行探索,最终自主研发了“人单合一”在制造业的落地载体—COSMOPlat;反之,COSMOPlat又为“人单合一”提供验证和支持,所有数据都会在COSMOPlat平台运营、管理。
以COSMOPlat为依托的海尔“智造”,并非简单的机器换人或自动化。最重要的,它让互联工厂超越了传统工厂的概念,以用户为中心,全流程资源并联形成了一个共创共赢的生态圈。而要支撑这个生态圈,必须从传统组织变成一个平台。
具体到整个供应链上,包括设计师、模块商(上游供应商)、互联工厂、车小微(负责物流配送)等各环节都要转型,由传统串联的部门组织,变成共同面向用户的一个个“小微”,中央空调互联工厂就是其中一个“小微”。
在中央空调互联工厂,有8条线体(生产线)、42个小“小微”。与海尔集团旗下一些“小微”财务和用人独立不同,这些生产车间处处涌现的小“小微”,只是单元机构,但也要单独算投入产出,并可利用海尔平台资源,如借助外力来改进工艺。
在海尔互联工厂,每个工人都会被予以一个身份—“创客”。每个创客,如果他的创新方案被采纳,则会被充分尊重,并可得到相应激励。如下图所示为海尔创客发明的“自动打包机”。

海尔创客发明的“自动打包机”
张瑞敏更是在视察中央空调互联工厂时,对该组织平台彰显的“人的价值”给予肯定。他说:“机器换人只是解决了效率问题,但把工人真正变成了创客,与平台各方共创用户价值,才是互联工厂的核心本质。在海尔有创新基因的土壤上,每位员工的创新积极性都得以充分发挥,员工个人价值提升后,为用户提供解决需求的能力也得到了相应增长……而最终的目标,就是在迈进物联网的同时,实现为用户定制美好生活解决方案的愿景。”