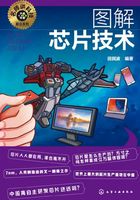
2.4 从单晶硅到晶圆
2.4.1 晶圆尺寸不断扩大
图1所示为由CZ法生长的φ300mm(12英寸)单晶硅棒,其质量可达350kg。
“硅圆片的大小为12英寸”,是指“其外径为12英寸”。通常,以英寸或毫米为单位的外径尺寸称呼硅圆片的大小。
硅圆片上制作IC时的有效部分为其表面积。因此,若外径尺寸变为1.2倍、1.3倍、……,相应制作芯片的有效面积则变为1.44倍、1.69倍、……,即按“外径平方成比例增加”。
伴随着IC的进步,硅圆片外径也连续不断地增加。但应指出的是,在集成电路制造中,随着硅圆片外径的变化,与其相关的所有设备也必须更新换代。
首先,制造硅圆片本身的生产设备需要更新。然后,为采用这种硅圆片来制造IC,其制造装置及工艺自不待言,生产线等也必须设立新的标准,进行改建更新,为此要耗费大量的人力和经费。
因此,今后相当一段时间内,仍然会是不同硅圆片产品同时存在。
为实现生产出更大外径的硅圆片,包括制造装置的厂家在内,对于制造厂家(生产硅圆片)和使用厂家(生产半导体IC)双方,都存在诸多问题和课题(图2)。
而且,在新一代大外径硅圆片上,要用最先进的技术制造更高集成度的复杂IC。因此,对硅圆片所要求的各种各样的尺寸、性能指标,比前一代更高、更复杂,会进一步增加难度。
尽管如此,与半导体相关的生产厂家对上述问题经过诸多因素的比较,对于硅圆片是否更新换代,总能适时地作出选择。其结果,过去硅圆片基本上按“每3.5年增加1英寸”的速度发展(图3)。
实际上,截至2009年,全世界可供应商用12英寸(φ300mm)晶圆的工厂已有上百家,且都为该领域的领头企业。但对于半导体IC厂家来说,硅圆片更新换代的负担很重,加之产品良率方面的考虑,目前对18英寸(φ450mm)硅圆片的大规模投产时间还不好预期。
本节重点
(1)为何晶圆尺寸增加的趋势并非像特征线宽减少那样明显?
(2)伴随晶圆大外径化,晶圆、IC厂商有哪些问题需要解决?
(3)调研国内晶圆十大厂商的产品及技术开发现状。

图1 12英寸(φ300mm)的单晶硅棒

图2 伴随硅圆片的大外径化有许多问题需要解决

图3 硅圆片大外径化的发展趋势
2.4.2 先要进行取向标志的加工
目前由直拉法制取的单晶硅棒,一般长度为2m,直径为8英寸(先进的为12英寸),质量为150kg。从硅棒中要切除不需要的部分,如剥皮和切除上、下两端头,并将其切分成若干个硅坯(图1)。
而后,按所要求的硅圆片直径,用磨削刀具研削硅坯外圆(图2)。当然,在拉制单晶时,应按硅圆片尺寸要求,保证硅棒外径足够大,并留有研磨外圆的尺寸裕度。
为了定出硅圆片面内的晶体学取向,并适应IC制造工程中在装置内装卸的需要,要在硅坯周边切出称为“取向平面(OF:Orientation Plat)”或“缺口(notch)”的标志(图3)。
取向标志的作用是,当硅圆片在装置内处理时,根据取向标志排列,可保证不同硅圆片间处理的均匀性,并且适应IC制造工程中硅圆片在装置内装卸的需求。过去,日本采用OF方式,美国采用V字形缺口方式,目前缺口方式有向统一方向发展的趋势。
本节重点
(1)介绍从硅单晶棒到晶圆的加工过程。
(2)晶坯为什么要进行取向标志的加工?
(3)一般采用何种取向标志?

图1 将硅棒切分成若干硅坯

图2 硅坯外圆的研削

图3 取向标志的加工
2.4.3 将硅坯切割成一片一片的硅圆片
接着,用黏合剂把硅坯固定在支持架上,将其切割成一片一片的硅圆片(切片),如图所示。在切片作业中,多采用贴附有金刚石颗粒的内圆刃切刀。但近年来,随着硅坯外径的变大,被称为“线刀(wire-saw)”的由钢琴丝与切削研磨液相组合的新的切片法也正在逐渐普及。
采用内圆刃刀片切片的特点是:①内圆刃刀片由高硬度不锈钢制作,张于环形刀架内侧,加一定张力固定;②适用8英寸以下的硅圆片的切片;③切片表面的平坦度良好;④切缝大约为0.6mm(刀片厚0.4mm,金刚石磨粒直径约0.1mm+a);⑤切片速度:8英寸硅圆片每片需6min,切割300片大约用30h;⑥对于大口径(300mm以上)硅坯,内圆刃刀片材料及制作都比较困难;⑦内圆刃刀片张力的均匀化等不好解决。
采用线刀切片的特点是:①将多根钢琴丝按一定间距平行固紧,沿钢琴丝滴下浆料(液)状金刚石颗粒研磨液;②可适用大口径(300mm以上)硅坯,8英寸硅圆片已有成熟的切片经验;③切片表面的平坦度比采用内圆刃刀片的情况略差;④切缝大约为0.3mm(钢琴丝直径0.2mm,金刚石颗粒直径+a大约0.1mm);⑤切片速度:8英寸硅圆片的标准时间为6h,可批量式切片;⑥钢琴丝及研磨液的运行费用相对于圆刃刀片法要高些。
根据以上对比可以看出,线刀切片的切缝小、可以多片同时切成,切片速度快,再加上切割大口径硅片的平面刃刀具的材料不易解决,因此,对于外径大于300mm的硅圆片,用线刀切割目前已成为标准切割方法。
切断后,用化学溶液溶解黏合剂,使硅圆片从支撑架上剥离,成为一片一片的硅圆片。
下一步是倒角(beveling)工序,要把硅圆片的侧面研磨成抛物线形状。这样做的目的,是为了在IC制造过程中装卸及加工硅圆片时,避免侧面棱角处破损(并产生后续制程中令人讨厌的颗粒污染),还可防止在热处理等制程中,由侧面部分导入晶体缺陷。
本节重点
(1)采用内圆刃刀片切片的特点。
(2)采用线刀切片的特点。
(3)防止在热处理等制程中,由侧面部分导入晶体缺陷。

将硅坯切割成一片一片的硅圆片
2.4.4 硅圆片有各种不同的类型
切好的硅圆片经倒角后,使用含有微细颗粒研磨剂的研磨液,进行机械研磨(lapping)。在对侧面磨削之后,将硅圆片置于转盘之上,对表面进行机械的、化学的研磨,使其变为闪闪发光的镜面状态。对于部分硅圆片来说,在经研磨、洗净后,还要放入扩散炉中,在氮气和氢气气氛中进行热处理。这样可以确保硅片表面附近成为无缺陷(DZ:Defect Zero)层。研磨好的硅圆片,经过各种严格检查,做最后洗净之后,装入特制的盒子出厂销售。
为了制作硅圆片基板,外延硅圆片也是典型方法之一。这种方法是在研磨完成之后或形成埋置扩散层后的硅圆片上,用气相沉积法形成硅单晶膜。这种气相生长称为“外延生长(epitaxial growth)”,是在反应容器(chamber)内通入硅烷(SiH4)及氢气(H2),一般将硅圆片加热到大约1500℃的高温,通过流动状态的SiH4与H2的气相反应,在硅基板表面按其晶体学方向连续地生长。
本节重点
(1)采用内圆刃刀片切片的特点。
(2)采用线刀切片的特点。
(3)防止在热处理等制程中,由侧面部分导入晶体缺陷。

从硅石变为硅圆片的过程