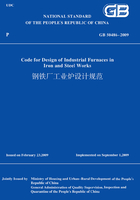
4.4 Stainless Strip Heat Treatment Line
4.4.1 Stainless strip heat treatment line could be divided into annealing-pickling line and bright annealing line.Annealing-pickling line could be equipped with horizontal furnace(including suspension type furnace and air-cushion type furnace)and vertical annealing furnace,and bright annealing line can be equipped with bright vertical annealing furnace.
4.4.2 Backup roll of suspension type furnace could be built in or out of furnace,but should be set in the new furnace.Suspension type furnace should basically consist of unfired preheating section,directly fired heating section and cooling section,and dryer section and heat recovery facilities moreover.There should be threading facilities inside the furnace.
4.4.3 Special sealing devices should be set up in charging and discharging opening of suspension type furnace.
4.4.4 It is proper to use ceramic fiber products as the main materials of furnace wall and roof lining and use coating with high radiation rate for internal surface of furnace liningand light refractory materials and insulators for furnace bottom lining.
4.4.5 The spacing of backup rollers at the same level,sag and tension of strip steel can be calculated according to the following formula.

where,L—Span(m);
f—Vertical distance between the suspension point and the lowest point of the strip(m);
T0—Horizontal tension of the lowest point(N);
T—Horizontal tension of the suspension point(N);
S—The length of the suspension cable(m);
q—Strip weight,uniform load(kN/m).
At the design temperature,permissible tension stress of stainless strip will be equal or less than 3.5N/mm2.
4.4.6 Design for cooling section of suspension type furnace shall conform to the following provisions.
1 One or more of cooling methods such as natural cooling in the air(air cooling),air blaster cooling,mist spray cooling,water spray cooling etc.,and reasonable design parameters like structure of cooling section,injected medium,injection speed and nozzles collocation etc.should be slected as per strip thickness and material quality.
2 Nozzles along width of wider strips can be divided into three groups as the left,the center and the right for control.Fume after heat recuperator can be used as spray media to cool down strips when temperature of strips entering cooling section is in the range of 600-700,then afterheat of strips will be taken away by coolers of recirculating cooling loop.
3 If the range of product size is large,cooling water should be distributed by flux.
4.4.7 The design of supporting rollers of suspension type furnace should conform to the following provisions.
1 If linear velocity of strip steel is low,it is suitable to apply ceramic fiber roller for high temperature section,and graphite roller or stainless roller for low temperature section.
2 The center distance between built-in rollers should be 10.0-20.0m in furnace direct fired section,and can be 5.0-6.0m in forced-convection preheating section or on condition that the sag of strips in cooling section is limited.The center distance between outdoor rollers in furnace direct fired section can be 20.0m.
3 Supporting rollers of preheating section and heating section should be mounted by pair in order to be able to change for each other quickly without furnace stop.Cooling section can be equipped with only one stainless roller.
4.4.8 Bright vertical annealing furnace mainly consists of entry sealing devices,heating section,radiation cooling section,convection cooling section and exit sealing devices,etc.
4.4.9 Top steering roll of upstriker vertical annealing furnace should be on the top of convection cooling section,and that of downstriker vertical annealing furnace should be on the top of heating section(in front of heating section).Each zone of vertical annealing furnace should be arranged converse"U"in shape.But the cooling section of vertical furnace in annealing-pickling line can be arranged horizontally in whcih strips will be transferred by air cushion.
4.4.10 Heating section of muffle bright vertical furnace can use gas or electric heater as power,but unmuffle bright vertical furnace can use electric heater only.
4.4.11 Gas burners should be distributed in tiers,and there should be two burners for one tier.Flame of burners which are staggered between tiers will run parallel with surface of strips.From entry to exit of the vertical furnace,50 percentage of heat loading should be distributed to 40 percentage of furnace boby,38 percentage of heat loading to the middle 40 percentage of the body,and 12 percentage of heat loading to the last 20 percentage of the body.Fume of each zone can be drafted individually.Electrical heating elements should also be allocated and controlled in zones and segments when furnace uses electric heaters.
4.4.12 The main material of furnace lining should be ceramic fiber products.A protective coat of stainless steel sheet of 0.5mm thickness or other high-density ceramic materials can be layered on the inner surface of furnace lining.Ceramic fiber layer should have corresponding anchors.
4.4.13 The entry and exit seal of bright vertical annealing furnace should be tight without any influence on exactness of strip tension regulating.
4.4.14 Muffle pipe can work at the temperature more than 1000℃for long term.It should be of suspension type and only fixed on the roof of furnace,and its wall thickness is decreasing from top to bottom.Its bottom can be equipped with counterweight to balance its weight.
It must be possible for muffle pipe to be installed and removed,so there should be suitable space around the furnace for its installation and hoisting.
4.4.15 The cooling rate of radiation cooling section should be adjustable.
4.4.16 Air blaster cooling should be adopted for convection cooling section which is of double spray or blast system.Mist spray to wash strips at strip entry.
Spray or blast system should consist of spraying or blasting cooler,circulating fan and water-cooled recuperator.For convection cooling section,spray or blasting flux of coolers should be adjustable in zones along strip width,and strip stabilization devices can be applied.
4.4.17 Diameter of top steering roll should be designed according to the maximum thickness of strips.
The roll should be flexible to swing at a certain angle at a horizontal level and threading devices can be mounted on its top.
4.4.18 It is indispensable to set tension adjusting device for vertical furnace,which can adjust tension according to strip thickness,strip width,furnace length and treatment temperature.Permissible tension stress for stainless strip should be controlled in the range of 2.0-3.5N/mm2 at design temperature.
4.4.19 Advanced automation control and detection system should be equipped for stainless strip heat treatment line,and explosion-proof measures will also be taken for the line.
4.4.20 Controlled atmosphere could be hydrogen or mixed gas of nitrogen and hydrogen.Its dew point should be lower than-50℃with the content of oxygen under 10×10-6.Gas injecting speed must be reduced greatly on condition that the strips thickness is less than 0.1mm.