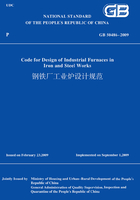
4.2 Cold Rolled Wide Strip Heat Treatment Production Line
4.2.1 Single stack tight coil hood-type annealing furnace can be used for annealing of cold rolled thin strip coils with big output fluctuations,many product varieties and big specification variation,width no less than 600mm,and thickness 0.2-3.5mm.
Design of single stack tight coil hood-type annealing furnace should comply with the following requirements:
1 Heat treatment steel type includes drawing steel,carbon structure steel,high strength steel of which strength is less than 590MPa,and maximum annealing temperature should be 750℃.
2 Steel coil dimension and shape requirements are given in Table 4.2.1-1.
Table 4.2.1-1 Steel coil dimension and shape requirements

3 Gas fuel should be choosen for heating supply of Hood-type annealing furnace,and electric power can be used in areas with rich electric power resources.Liquid fuel should not be used.Gas fuel specification should meet the provisions of Table 4.2.1-2.
Table 4.2.1-2 Hood-type annealing furnace gas fuel specification

4 In the hood-type annealing furnace,controlled atmosphere species can be determined according to the gas source condition.Controlled atmosphere species and hydrogen(nitrogen)specification should meet the provisions of Table 4.2.1-3 and Table 4.2.1-4.
Table 4.2.1-3 Controlled atmosphere species

Table 4.2.1-4 Hydrogen(nitrogen)specification

Note:The nitrogen must be continuously supplied,and emergency nitrogen supply system must be set up.
5 Cooling water for the furnace base seal cooling,process spray cooling or divert cooling must be used circularly.The emergency water supply system should be provided for furnace base seal cooling,with water consumption as 1-2t/h.
6 Furnace base quantity should be determined in accordance with the following provisions:
1)Yearly working hours can be considered as 8000h;
2)Charge stock quantity should be calculated by 2.0-2.6 times of the steel coil maximum diameter;
3)Steel coil of different annealing processes and inner diameter should not be mixed;
4)Number of heating hood and furnace base should be determined according to the furnace base occupation time and heating hood occupation time of various strips of varied specifications derived from product mix and heat treatment systems.
7 Specific fuel consumption of hood-type annealing furnace is related to annealing treatment variety,annealing temperature,strip width and furnace size and other factors,and can be controlled at 600-800MJ/t.
4.2.2 Major equipment and systems of hood-type annealing furnace should include furnace base,heating hood,inner hood,cooling hood,valve racks,middle convection plate,top convection plate,heat supply systems,exhaust systems,controlled atmosphere supply and exhaust system,furnace atmosphere circulation system,cooling water supply and drainage system,flow distribution or jet flow cooling system,power supply system,detection and automatic control systems,process control and management system.
There should be good interchangeability between furnace base of the same size and its heating hood,cooling hood,inner hood in the same workshop.
4.2.3 Furnace base should consist of supporting seat,baffle at the bottom made of bottom shell steel structure and heat-resistant steel,circulating fan,clamp device,furnace base seal cooling water tanks and furnace base thermal insulation material.Furnace base design should meet the following requirements:
1 The baffle at the bottom should be made from heat-resistant steel casting or steel structures;the furnace base flatness tolerance should be less than 0.5mm;furnace base centerline tolerance is±2.0mm.
2 Water cooled silicone rubber seal should be used between furnace base and inner hood,and manual compaction,pneumatic clamping or hydraulic clamping shall be adopted for clamping.
3 Clamping devices should be arranged evenly around the furnace base.Pneumatic clamping gas source working pressure should be greater than 0.6MPa,the hydraulic clamping working pressure should be 12-14MPa.
4 Circulating fan should be installed at the furnace base bottom center,and should consist of impeller and asynchronous two-speed or variable-frequency motor;bearings should be cooled by water cooled jacket,and lubricated by grease or oil mist;between the bearing and shaft,axis slip should be allowed;circulating fan working pressure should be 4.0-5.0kPa.
5 In the annealing shop with quite a number of hood-type furnaces,gas pipe connecting around the furnaces,combustion exhaust gas pipe connecting,electrical sockets,water supply and drainage pipe connecting,heating hood supporting seat,guide post and so on must be installed by the same installation die.
6 Top level of four support seats at a 90° angle against each other of the heat hood around furnace base must be consistent,with permissible tolerance less than 1.0mm.
7 Height difference of two guide posts at a 180° angle against another around furnace base,one high and one low,can be 200-300mm;guide post perpendicularity deviation should be less than 5.0mm.
8 Ceramic fibers should be filled between the steel structures in the furnace base shell.
9 In the hood-type furnaces plant,testing furnace base shall be provided for new technology test,research and development.
4.2.4 Cylindrical heating hood should consist of heating devices(burner),air-fuel ratio and temperature control system,combustion fan,air heat exchanger,exhaust pipe,lining,top ring,air and gas pipe and other components.Heating hood must be designed in accordance with the following provisions:
1 When gas fuel is to be adopted,burners design should meet the following requirements:
1)Burner centerline should be uniformly arranged on the direction of the heating hood imaginary circle tangent;
2)Each burner capacity should be small rather than big,flame length long rather than short,and the combustion air must be preheated;
3)Combustion fan should be installed on the heating hood,air should be supplied for each burner through preheater;
4)Ignition and flame monitoring devices should be set for burner;
5)Waste hydrogen combustion devices should be set for full hydrogen hood-type annealing furnace.
2 Natural smoke exhaust can be adopted for gas-fuel hood-type annealing furnace in workshop;centralized exhaust by smoke extractors and chimney will also do.Independent exhaust system should be adopted for controlled atmosphere exhaust.
3 Automatic joining or manual joining can be adopted for heating hood gas pipe connection,exhaust pipe connection,electrical power and control system connection.
4 Heating hood steel structure should be made from 5.0mm thickness welded steel plate;top ring position should be fixed after all the accessories of the heating hood was installed and located;however,top ring position must ensure outer hood balance.
5 When electrical energy is to be adopted,Ni-Cr resistance strip with service temperature of 950℃should be laid out on the inner wall of the heating hood lower part.A special shaped high alumina brick hanging should be adopted for electric heating element.
4.2.5 Hood-type annealing furnace inner hood should consist of a cylindrical barrel,roll forming dome and bottom flange.Inner hood design should meet the following requirements:
1 Inner hood barrel can be made of gas-tight welded 1Cr20Ni14Si2 heat-resisting steel plate,the bottom flange materials can be Q235-B.
2 Inner hood quantities should be consistent with the number of furnace base.
3 Inner hood can be horizontal corrugated cylinder or flat cylinder.
4 Inner hood structure lower part should be made from 6.0mm thickness plates,the upper part can be made from 5.0mm thickness plates;diameter tolerance should be
5 When continuous gas-tight welding is to be adopted,perpendicular weld joints of two ring plates must be staggered;run-through weld joints are not allowed.
6 Bottom flange should be made of 50.0mm thickness steel plate,and must be machined;bottom surface flatness tolerance should be 0.5mm;diameter tolerance should be
7 Between the inner hood and heating hood,cleaned dry quartz sand or annular ceramic fiber products should be used for seal.
8 Furnace top should be rolled or molded spherical dome.
4.2.6 Hood-type annealing furnace cooling hood should consist of the circular barrel,cooling fan,water cooling nozzle and other components.Cooling hood design should meet the following requirements:
1 Cooling hood quantity should be determined through the heat treatment process time.
2 Circular barrel should be made of 4.0-5.0mm heat-resistant steel plate or carbon steel plate;diameter tolerance should be
3 When 1 axial flow fan is to be adopted for cooling fan,it should be installed on the top of the cylinder,and cold air should be inhaled from the lower part;when more than two centrifugal fans are to used for cooling,they should be uniformly arranged.Water cooling nozzles should be installed on the top of the cylinder.
4.2.7 Middle convection plate must be provided between two layers of steel coil of annealing steel coil stack;a top convection plate should be placed on the top part;3-4 middle convection plates should be equipped for a furnace base.
Q345 should be adopted for convection plate material;the baffle must be made of a piece of plate;flatness tolerance should be less than 0.5mm.
4.2.8 Detection and control of the hood-type annealing furnace annealing process should be automatic;manual intervention can be implemented in the process.Automatic detection and control systems shall meet the following requirements:
1 In annealing process,furnace temperature,controlled atmosphere pressure,flow rate,dew point and oxygen content,medium(fuel gas and water)parameters such as temperature,pressure and flow rate,should be detected,controlled,indicated,recorded and alarmed.
2 After annealing process has been selected,the annealing cycle must be automatically controlled by the control system;there should be annealing process setting,output,records,statistics gathering and grandfather functions;between the computer and host computer the data exchange interface should be set.
3 Comprehensive automatic safety diagnosis and fault treatment functions should be provided for the system.
4 Fire and explosion protection monitoring and alarm systems should be set.
4.2.9 Final cooling platform quantity can be determined as 0.5-0.6 times of furnace base.Final cooling platform should include fan,muffler,backplane,middle convection plate and the top convection plate.Cooling platform can be set under the ground,and also can be set on the ground.Air fan air pressure should be 0.9-1.3kPa.
4.2.10 Vertical continuous annealing furnace can be used for cold rolled thin strip coil continuous annealing of which output is high,unit speed is high,strip width is not less than 600mm,and thickness do not exceed 2.5mm.Vertical continuous annealing furnace design should meet the following requirements:
1 Type of heat treatment should be strip continuous annealing.
2 Heat treatment steel type should be drawing steel,carbon structure steel and high strength steel.
3 Steel coil size should meet the provisions of Table 4.2.10.
Table 4.2.10 Steel coil size

Note:Maximum coil weight is 45t.
4 Heat treatment system should be established according to the heat treatment process curves.
5 Annealing furnace working temperature should be 920℃,strip maximum processing temperature should be 890℃.
6 Specific fuel consumption of continuous annealing furnace should be determined according to factors such as annealed material type,annealing temperature,hourly output,strip speed,etc.,with specific consumption fluctuating at 740-1300MJ/t for different types.
4.2.11 Vertical annealing furnace should consist of the inlet seal device,preheating section,radiant tube heating section,slow cooling section,fast cooling section,aging section,final cooling section,outlet seal device,water quenching device,wringer section,drying section and other main furnace section and strip transmission system.
Common cold-rolled plate and car sheet annealing speed should be 250-450m/min;tinplate annealing speed should be 500-880m/min;nitrogen and hydrogen mixture gas should be adopted for controlled atmosphere.
4.2.12 Inlet seal device should meet the requirement that it prevents the gas in the furnace spilling and prevents air outside the furnace entering the furnace;main facility should consist of the inlet seal box,a pair of seal rollers,seal roller switch cylinders,two seal baffle plate,nitrogen seal pipes etc.
4.2.13 In the preheating section,strip should be preheated by controlled atmosphere which was heated by flue gas discharged from heating section radiant tube through preheater;in preheating section main equipment should include controlled atmosphere spray tank,preheater,circulating fan and pipeline.
4.2.14 Design of radiant tube heating and soaking sections should meet the following requirements:
1 Strip should be brought into radiant tube heating section after preheating,and heated to the temperature required by the process;and should be kept in the soaking section for some time.
2 Heating section and soaking section should be two independent furnace chambers,gas-fired radiant tube can be adopted in both sections;however,in the soaking section,electric heating also can be adopted.Design of heating section or soaking section which is to be heated by gas-fired radiant tube should meet the following requirements:
1)"Pumping and airblast"style radiant tube and built-in air peheater should be adopted;W,U,P shape should be adopted for radiant tube shape;
2)Combustion exhaust gas should be drawn by exhaust blower,and discharged through the preheater,flue duct and chimney;
3)Spark ignition and flame monitoring device should be used for burner;
4)Along the strip stroke some temperature control section should be provided so as to control temperature based on annealing process requirement;
5)In the heating section,below the first few top rollers and above the first few bottom rollers the radiation-proof board should be set;
6)Top and bottom plate of the furnace shell should be provided with cover plate and threading holes should be set for service and threading;
7)When steel chimney is to be adopted,steel chimney can be laid out independently or between the adjacent factory building column lines.Protective measures should be taken nearby the chimney.Drain pipe should be set at the bottom of a chimney,and accumulated water should be discharged regularly.Lightning grounding device should be set for chimney.
4.2.15 Slow cooling section design should meet the following requirements:
1 Injection cooling device should be arranged on both sides of the Strip.
2 Injection cooling device should be made of heat-resistant steel,and nozzle form and structure should facilitate arrangement of gas blowing direction and uniform cooling of strip.
3 Fin-and-tube heat exchanger quantity and capacity should match the cooling device.
4 Circulating fan body should be made of heat-resistant steel,speed variable motor should be configured for the fan.
5 In the slow cooling section and top roller and bottom roller chambers,adjustable resistance bands or radiant tube heating should be set.
4.2.16 Design of fast cooling section of controlled atmosphere high-speed injection cooling should meet the following requirements:
1 Fast cooling section should consist of controlled atmosphere injection cooler,circulating fans,controlled atmosphere and water heat exchanger and other components.
2 Injection cooling device can be divided into several groups;injection tank and the nozzle made of heat-resistant steel should be evenly arranged along both sides of the strip;distance between nozzle and strip should be adjusted by variable-speed gear motor.Controlled atmosphere should be supplied for each group of injection tank and nozzle by separate circulating fan,heat exchanger and circulation pipeline,the nozzle should provide high-speed injection cooling evenly along the strip width.
3 Seal device should be set on inlet and outlet of fast cooling section;a controlled atmosphere exhaust fan should be set in top roller chamber.
4 Circulating fan should be driven by adjustable speed motor,wind pressure should be 10-15kPa,air flow can be determined according to the heat exchange capacity.
5 Controlled atmosphere and water heat exchanger can be made of aluminum finned heat-resisting steel tubes or materials with high heat transfer efficiency;heat exchange capacity should be determined according to output,strip specification,speed of operation,residence time in cooling section,the cooling rate and other data.
6 In fast cooling section inlet,outlet and between two groups of injection tanks,stabilizing rollers should be set.Stabilizing roller rotational line speed should be synchronized with the strip;it should be driven by gear motor.Each stabilizing roller should be driven by two cylinders.
7 Electric resistance band or radiant tube heating should be set for the channel before the inlet and after the outlet of the fast cooling section for heating purposes.
4.2.17 Aging section design should meet the following requirements:
1 When temperature of strip remains at a certain level or drops down slightly,microstructure and physical properties of strip should meet the stipulated requirements.
2 Aging section structures should meet the following provisions:
1)Aging section may consist of two independent furnace chambers;resistance band(or electric radiant tube)and injection cooling pipe can be set for each furnace chamber to adjust the furnace temperature and for startup;
2)When structure of two aging sections are similar,expansion compensators should be set between the two sections;
3)Heat-insulation lining in aging section inside and top should be made of ceramic fibre products fixed by heat-resistant steel anchor nail;light heat-insulation brick should be adopted for the bottom,and the inner surface should be protected by heat-resisting steel plate.
4.2.18 Final cooling section design should meet the following requirements:
1 In the final cooling section strip should be cooled from aged temperature to below 150℃.
2 Final cooling section should be made up of a number of controlled cooling sections;controlled cooling section should be made up of a stroke or two strokes,and independent controlled atmosphere circulatory system should be formed.Controlled atmosphere circulatory system should include circulating fan,bellow injection cooler,cooler and pipeline.Expansion compensator should be set between final cooling section and aged section.
4.2.19 Outlet seal device design should meet the following requirements:
1 Seal device should prevent the atmosphere in the furnace leaking and prevent air outside the furnace entering the furnace.
2 Main equipment should include two pairs of seal rollers.Each seal roller should be provided with two on/off cylinders,water jacket,N2 seal system and exhaust gas discharging system.
3 Seal roller should be made of Ni-Cr steel,exhaust blower and pipeline should be located between the two pairs of seal rollers.
4.2.20 Design of water quenching device should meet the following requirements:
1 Strip should be cooled from 150℃to 40-45℃with water quenching.
2 Main equipment should include demineralized water spray device,water quenching tank,sink roll,circulating water system,demineralized water and cooling water heat exchanger;mist exhaust fan should be provided at the top of spray device.
4.2.21 Wringer and drying device design should meet the following requirements:
1 Residual moisture on the surface of steel strip should be removed by wringer and drying device.
2 Main equipment should include two or three pairs of wringer rolls,drying facilities,air and superheated water(or steam)heat exchangers.
4.2.22 Different roller types should be adopted for strip transmission system depending on working environment and feature of furnace roller in different furnace sections.According to strip operation parameters detected by automatic control system,strip tension and deviation correcting in the furnace should be adjusted and controlled by computer.Strip transmission system design should meet the following requirements:
1 Centrifugal casting of heat resistant steel should be adopted for furnace roller,and spray treatment should be adopted for its surface.
2 Strip tension measuring devices should be provided in the related furnace section,and reliable lubrication system should be adopted for bearings.
3 Steering roll should be located at the top of the furnace chamber.Bearings,motors and gear boxes should be supported by furnace body steel structure.
4 Furnace roller materials should be determined in accordance with various furnace section operation temperature.
5 Roller surface length should be 200mm greater than the maximum strip width,roller diameter should be determined according to the variety of product,specification,furnace section and its functions.
6 Furnace roller should be driven by AC adjustable speed motor independently.
4.2.23 Furnace shell and steel structure design should meet the following requirements:
1 Furnace shell should be made of gas-tight weld steel;bellow expansion compensator should be set between various furnace sections;steel structure should be able to support the furnace body,platforms,ladders,handrails,and various pipelines.
2 Distance between furnace drive side and factory column should allow radiant tubes and furnace roller assembling and disassembling by the workshop crane;2000-2500N/m2 can be chosen for the platform load design.
4.2.24 Design of vertical annealing furnace automatic control systems should meet the following requirements:
1 Main items of measurement and adjustment should include gas,various water,electricity,hydrogen,nitrogen,steam,compressed air and other public medium flow,temperature,pressure and furnace atmosphere control adjustment.
2 Automatic control items should include furnace temperature detection and control of various section,radiant tube temperature detection and control,strip temperature detection and control,exhaust gas temperature measurement and control of exhaust system,adjustment and control of combustion,flame monitoring,cooling rate adjustment and control of the cooling system,flow and temperature control of water quenching system,wringer and drying system flow and temperature control.
3 Strip tension measurement,regulation and control.
4 Strip centering and deviation correct control.
5 Safety control system shall be provided with monitoring facilities preventing excessive high furnace temperature,radiant tube overheating,atmosphere detecting,fuel gas low pressure,flame extinguishing etc.
4.2.25 Top cover lifting machines,bottom cover mounting and dismantling machines,top rollers,bottom rollers,seal roller and stabilizing roll installation and removing machines,radiant tube installation and removing machines,threading machine and other auxiliary tools should be configured for vertical continuous annealing furnace.
4.2.26 Supply conditions of common medium T.O.P should meet the following requirements:
1 Fuel gas specifications of vertical continuous annealing furnace should refer to the specifications given in Table 4.2.1-2.
2 Controlled atmosphere specifications of vertical continuous annealing furnace should meet provisions given in Table 4.2.26-1 and Table 4.2.26-2.
Table 4.2.26-1 Hydrogen technology specification of vertical continuous annealing furnace

Table 4.2.26-2 Nitrogen technology specification of vertical continuous annealing furnace

3 Cooling water pressure should not be less than 0.4MPa,the total hardness should not be greater than 150mg/L(on the basis of calcium carbonate),pH value should be controlled at 7-8.