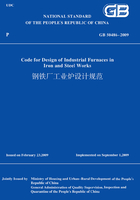
3.5 Thin Slab Continuous Casting and Rolling Furnace
3.5.1 Technology and structure design should meet the following requirements:
1 Through roller hearth furnace should be chosen for such furnace.
2 Production of continuous casting machine and rolling mill should be connected efficiently,and there should be sufficient buffer capacity with the furnace.
3 Buffer time for the thin slab in furnace should be more than 10 minutes.
4 Billet should swing backwards at low speed when buffering in the furnace.
5 Real-time tracking of billet position should be provided.
6 Billet shall enter the furnace continuously at casting speed and exit the furnace at the biting speed of the first mill stand.
7 The hourly output of the furnace should be equal to the hourly output of the continuous casting machine.
8 Steel structures should be designed on modular basis.
9 Movable type furnace roof should be designed.
10 Light structure with high temperature ceramic fiber modules should be designed for the furnace roof and the lining of the upper furnace wall,composite structure with castable refractory,light weight refractory brick and flame-retardant fibre board should be designed for the iron slag hopper and the lining of the lower part of furnace wall.
3.5.2 Design of heat supply system should meet the following requirements:
1 The system should consist of 2-3 subsystems,and independent combustion system and smoke extraction system should be arranged for every subsystem.
2 Top-heating should be set for combustion system.
3 Inferior high-velocity burner and pulse control should be chosen for combustion device.
4 Nominal specific consumption should be calculated and determined on the basis of casting speed,thickness and width of the slab.
3 The furnace can be divided into heating zone,transfer zone,ferry zone and soaking zone along the slab movement direction,with heat load at heating zone up to 50% of the total.
3.5.3 Design of furnace roller should meet the following requirements:
1 Non water cooled(dry roller)or water cooled roller(wet roller)should be chosen for design of roller structure in order to reduce the iron slag buildup on the furnace roller and improve the quality of slab.
2 Manually-operated C hook or mechanical carts can be adopted for roll changing.
3 Independent drive and variable frequency control should be chosen for the furnace roller,the range of the designed roller speed in furnace should be 2 to 90m/min.
3.5.4 Design of the major furnace mechanical equipment should meet the following requirements:
1 Lifting door should be adopted for thin slab continuous casting and rolling furnace,and electric control or start control can be adopted for furnace door motion.
2 Several scale hoppers should be designed at the furnace bottom.A set of start control scale door lined with refractory insulation material at the outlet of the hopper should be set.The scale in furnace should drop into waste box when the scale door is opened regularly.
3 There should be a roller repair workshop for thin slab continuous casting and rolling furnace.
3.5.5 Two-level computer autocontrol should be adopted for the automatic control system,the first-level control should include thermal instrument control and mechanical drive control,the second-level computer control should be furnace optimization control system.
3.5.6 Plane arrangement should meet the following requirements:
1 One furnace should be equipped for the production line of which annual output is about 1 million tons,two furnaces should be equipped for the production line of which annual output is about 2 million tons.
2 The furnaces can be translational ferry or rotating ferry if two furnaces were arranged in thin slab continuous casting and rolling plant.

Figure 3.5.6-1 Rotating ferry sketch
1-A furnace heating transfer zone;2-A furnace rotating ferry zone;3-A furnace soaking zone;4-B furnace heating transfer zone;5-B furnace rotating ferry zone

Figure 3.5.6-2 Translational ferry sketch
1-A furnace heating transfer zone;2-A furnace landscape orientation ferry zone;3-A furnace soaking zone;4-B furnace heating transfer zone;5-B furnace landscape orientation ferry zone