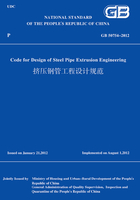
6 Equipments
6.1 Horizontal Extrusion Press
6.1.1 The horizontal pipe extrusion line shall be provided with full-line basic automation control.
6.1.2 Either hydraulic or mechanical straightening machine may be selected for long-billet straightening process.Straightening unit shall be combined with billet turning device.
6.1.3 Either multiple-length peeler or cut-to-length peeler can be selected for peeling process,and the peeler shall meet requirements as follows.
1 Machining sizes shall cover all diameters and lengths of raw materials.
2 The diameter tolerance and surface roughness after machining shall conform to extrusion requirements.
3 The surface after machining shall be free of any defect that may affect the extrusion product.
6.1.4 The band saw should be selected for billet cutting.However,the circular saw can be a choice as well.
6.1.5 Special machine tools which can perform drilling and borehole shall be provided for drilling process.
6.1.6 The CNC lathe should be used for end-face machining.
6.1.7 The continuous washing line should be selected for billet surface cleaning;and the billet drying unit shall be available after cleaning.
6.1.8 The rotary-hearth furnace plus induction furnace should be selected for billet reheating;and using induction furnace alone may also be an alternative for the same.The furnace equipment shall meet the following requirements.
1 The rotary-hearth furnace shall meet the temperature requirement of billet preheating for extrusion process.
2 Either mains-frequency induction furnace or variable-frequency induction furnace may be selected for inductive heating.
3 Induction furnace shall ensure that the billet reheating temperature can satisfy the expanding and extrusion processes.
4 The sizes of induction furnace shall conform to expanding and extruding dimension requirement.
6.1.9 The vertical expander for expanding process shall be selected according to the following requirements.
1 The expender shall be able to perform expanding.Meanwhile,piercing may be expected as an additional function of the expender.
2 The maximum expanding(piercing)capacity shall satisfy the need of pipe production.
3 The inside diameter of expanding container shall match the billet diameter.
4 There must be no any crack and depression on billet surface after expanding.
5 Electric stove shall be installed in expanding section for preheating tools and dies.
6.1.10 Hydraulic descaler shall be selected for billet surface descaling,and the descaling pressure shall not be lower than 12MPa.
6.1.11 The lubrication unit for applying glass powder on inside and outside surface of the billet shall be provided prior to expanding and extrusion and comply with the following requirements as well.
1 The lubrication table should be used for lubricating the billet outside surface with glass powder.
2 The automatic manipulator should be used for adding glass powder to lubricate the surface of hole inside the billet before expanding;and the manual mode may be selected as an option.
3 The manipulator for adding glass powder should be selected for lubricating the inside surface of the billet before extrusion.
6.1.12 The selection of extrusion press shall meet the following requirements.
1 The oil should be used as transmission media for extrusion press,and the water may be used as an alternative.
2 The maximum extrusion force shall meet the product extrusion requirement.
3 The inside diameter of extrusion container shall match the billet diameter.
4 The extrusion tools shall have a quick-change function.
5 The inner wall of extrusion container should be combined with automatic cleaning device.
6 The cooling unit shall be provided for mandrel bar.
7 Preheating and cooling devices shall be installed for extrusion container.
8 Preheating unit shall be provided for tools and dies.
6.1.13 The pipe extrusion press may incorporate the equipment which is able to extrude profiled bar and shaped pipe.
6.1.14 The safety guard must be installed along delivery roller table,and must be strong enough to prevent mandrel and pipe from rushing out of the guard in case of accident.
6.1.15 Quenching tank and collection unit shall be available in pipe cooling section;and the cooling bed or online spraying unit may be used as an alternative.
6.1.16 The roller-hearth furnace should be selected for heat treatment in extrusion shop;and the bogiehearth furnace and chamber furnace may be added as well.
6.1.17 The roller straightener shall be provided for straightening process;and the straightening press may be added as well.The stretcher straightener shall be installed in case of producing profile bars.
6.1.18 Equipment selection for sawing process shall conform to the following requirements.
1 The sawing equipment shall have cutting-to-length function.
2 The sawing equipment should be combined with deburring unit.
6.1.19 Abrasive belt grinder should be selected for pipe outside grinding and the wet-type grinding is preferable.
6.1.20 The pipe inside grinding equipment shall conform to the following requirements.
1 The grinding machine shall be able to perform full-length inside grinding;and the inner surface of pipe after grinding shall be free of any defect like scratch and depression.
2 The grinder shall be equipped with dedusting unit.Direct emission of dust generated during grinding is strictly prohibited.
6.1.21 Pickling equipment shall be installed to remove scales from inside and outside surface of steel pipes;and the shot blasting and pickling equipment may be provided simultaneously.The equipment shall conform to the requirements as follows.
1 The shot blasting equipment shall be equipped together with dedusting unit.
2 The acid-mist collection and treatment unit must be provided for pickling equipment.
3 The pickling equipment must be combined with collection and treatment facilities for acidcontained wastewater.
4 The waste-acid collection system must be provided for pickling equipment.
6.1.22 Ultrasonic flaw detector and eddy-current flaw detector shall be installed in non-destructive test(NDT)section;and other NDT equipment may be added if necessary.
6.1.23 Ultrasonic flaw detector shall have a function of thickness gauging.The NDT equipment shall be able to mark and record defects.