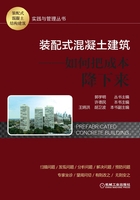
2.3 成本增量的解决思路
解决成本增量的思路主要有三条:一是把可避免、可压缩的成本增量减下来;二是对于不可避免不可压缩的成本增量,发挥和扩大其功能,让功能增量大于成本增量;三是通过技术、管理和市场手段落实可争取的成本减量。
2.3.1 可避免的成本增量
1.政策不适宜导致的成本增量
当前一些城市出现一刀切的政策,导致与当地的市场供应情况及项目或建筑情况不适应,产生了不必要的成本增量。
(1)量化指标与市场供应不匹配
有些地方政策过于激进,人为造成了供给侧紧缺。譬如合理运输半径150km范围内预制构件实际产能有100万m3,但要完成政策要求的装配式建筑指标需要200万m3。这种情况下一方面会造成供不应求、价格上涨,一方面需要从更远的地方耗费更多的运费采购构件,两种情况都会造成构件价格偏高。这种原因导致的成本增量自然不能被市场认可、客户不会买单。所以,在政策制定时一定要考虑当地现有实际产能及新增产能与市场的匹配性。
(2)量化指标与项目或建筑不适应。
有的地方政策太刚性,缺少灵活性,把不适合做装配式的项目或建筑也硬性要求做装配式。例如一个项目有两栋楼,一栋9层,一栋3层,那么9层的更适合,3层的相对就不适合做装配式。如果把装配式指标全放在这栋9层的建筑上,做略高一点的装配率,这个项目总的装配率能实现,也不会造成很多模具的浪费,那么就能取得较好的规模效益。而如果按照某些城市的现有政策,这两栋楼都要求达到装配率50%,这种情况下3层的建筑成本增量就会相对更高,这就是额外的成本增量。
2.标准缺位导致的成本增量
近年来,我国装配式建筑得到了集中爆发式的发展,而目前尚未建立起完整的工业化建筑标准体系,现行标准规范对工业化建筑发展支撑不足、关键技术标准缺位等问题突出,出现了技术标准跟不上装配式建筑的发展的问题,也造成了在标准缺位领域的大面积保守设计,导致了成本增量。
例如《装标》是现行主要标准,未对多层建筑、高层建筑进行明显区分,由于该标准主要是针对高层建筑而制定的,所以对于应用广泛的多层装配整体式剪力墙结构建筑而言要求过于严格,多层建筑的成本增量本身就相对高,加之标准缺位导致成本增量更高。解决这一标准空缺问题的《多层装配式混凝土结构技术规程》(T/CECS 604—2019)于2019年7月8日颁布,此规程的实施可以有效降低多层装配式结构建筑的成本增量。类似这类标准空缺的问题,只要填补空白就可直接避免再产生额外的成本增量。
3.由于甲方不进行事前策划分析而造成的成本增量
在传统建筑中,甲方从来不会认为如何建造会成为一个问题,更不会想到如何建造的问题会制约设计、销售、财务等环节。这一惯性思维在装配式建筑中遇到了问题,没有针对装配式建筑进行设计前的技术策划及方案比选,而是仍然按原来的工作套路,先设计后施工,有问题再修改。特别是在装配式建筑的设计过程中采取了用建筑方案直接进行设计而没有考虑装配性要求,导致了最终的设计不合理,发挥不出装配式建筑的优势,且产生了额外的成本增量。
4.由于装配式设计滞后而产生的成本增量
装配式建筑较传统建筑最大的区别在于装配式建筑是产品思维,而不像传统建筑设计那样是半成品。在设计上最大的区别在于时间上从各专业依次设计转变为全过程协同设计;在空间上最大的区别在于装配式建筑的设计是一个综合性的设计,集成度高,而不再是各专业的分别设计,设计中需要各专业前后考虑、密切协同、相互交圈。而如果沿用传统建筑的设计习惯,按现浇结构设计完成后再进行装配式的深化设计、二次设计,就会丧失对在规划、方案等高价值的设计前端的有效管理,规划设计中没有考虑装配式建筑的优势与劣势,方案设计中没有考虑装配式建筑的特性与要求,其结果就是用高成本买单,产生额外的成本增量。
5.由于设计精细化水平不高而产生的成本增量
装配式建筑较传统建筑在质量管理上的区别是精度高,传统混凝土结构的施工比较粗放,误差以厘米计,而装配式建筑的误差是毫米级。高精度的质量标准对应的是容错度极低的管理要求,首当其冲的就是设计精细化,不能粗放和随意,只有设计精细化了,生产的预制构件才能精细化,现场施工才能高精度完成。而精细化水平不高的设计将直接导致生产的预制构件不能满足现场施工要求,或者由于精度不够而降低现场施工效率,或者精细化水平差到出现钢筋或构件干涉碰撞、预留预埋遗漏或错位等而导致返工,这些都将导致额外的成本增量。
6.由于拆分设计中功能过剩而产生的成本增量
装配式混凝土建筑的高集成性决定了拆分设计除了需要考虑建筑设计、结构设计本身的要求以外,还需要考虑预制构件在生产、运输、施工等环节的要求,需要集成水、暖、电、通信、设备、装饰等各个专业的要求。而设计师在不了解生产、运输、施工等环节技术要求的情况下容易按保守的、更高的要求进行设计,例如由于对预制柱的生产方式不了解而加大了生产中脱模、吊装等环节的荷载,或者由于对现场施工措施的不了解或未确认而增加了额外的预埋件。这些超出实际需要的荷载和预留预埋都会产生额外的成本增量。
7.由于拆分设计预制构件大小不合理而产生的成本增量
装配式混凝土建筑的成本增量中有一项是起重机的成本增量。控制好起重机成本增量的主要措施是控制预制构件的单件重量,并据此选择经济的起重机布置方案和设备型号。单个构件过重过大,如果这个构件的位置正好在起重机的起重重量之外,起重机就要提高一个等级,就会为这一个构件增加起重机的台班费;单个构件过小,数量过多,导致吊装次数过多、效率低下,就会增加吊装工期,导致结构工期延长,增加起重机的台班量。这两种情况都会产生额外的成本增量。
8.预制构件厂家缩短摊销和折旧年限而产生的成本增量
土地成本摊销及固定资产折旧是预制构件成本的重要组成部分,预制构件工厂应该按照合理的使用年限进行土地成本摊销及固定资产折旧,一般合理的摊销和折旧年限为土地按50年、房屋建筑按20年、生产设备按10年、工具器具及运输设备按5年。而有的生产厂家为了尽快甚至短期内就收回投资而随意缩短摊销和折旧年限,大大提高了构件成本,在构件供不应求的地区,这种做法更为常见,导致了构件价格的虚高。这一情况也造成了成本增量。
9.预制构件工厂盲目追求“高大上”而产生的成本增量
自动化流水线是建筑工业化的特征,也是现阶段的最高水平。而我们现在还处于装配式建筑发展的初级阶段,标准体系尚未完善,设计标准化程度还较低,预制构件工厂的生产对象并非是标准化的预制构件,大多数是非标构件、异形构件。构件厂盲目追求自动化、高配置必然导致投资过大、设备利用率低,构件成本偏高,从而产生额外的成本增量。同时构件厂由于过多征用建设用地、厂房及办公楼等过分奢华也会产生额外的成本增量。
10.预制构件工厂总平面及工艺布置不合理而产生的成本增量
预制构件工厂合理的总平面及生产车间工艺布置既有利于降低建设投资,也有利于缩短厂内原材料、预制构件、能源的运输和输送距离,提高效率,降低成本。例如混凝土搅拌站紧连构件生产车间、构件生产车间外直接布置构件存放场地、钢筋绑扎工位靠近钢筋骨架入模工位,这些措施都有利于降低生产成本。但实际上很多构件厂由于迅速上马,选址匆忙,由于客观限制或主观原因或由外行设计造成构件厂的总平面及生产车间的工艺布置不合理,难以修改,因而产生了持续性的成本增量。
11.因预制构件质量问题而导致现场吊装怠工产生的成本增量
高质量的预制构件是高效率施工的前提条件,高效率施工是低成本的前提条件。由于装配式建筑对质量问题的容错度比传统建筑低,传统建筑中的粗放式质量管理的习惯极易放过预制构件生产质量出厂检查或进场验收检查,极易用抽查的方法而不是逐件检查的方式进行质量检查验收。而一旦有一个构件的质量出现问题(图2-12),导致安装不上,可能损失的就是整个楼层、整个建筑的正常进度,从而产生额外的成本增量。
12.现浇结构部分质量偏差、预留预埋不准确而产生的安装成本增量
高精度的预制构件要求现浇结构部分也必须是高精度,特别是从现浇层到装配层的转换层的结合面质量,包括混凝土标高及伸出钢筋质量等,这都直接决定了装配层的安装效率。如果转换层标高有偏差,或者预留钢筋位置、长度不准确(图2-13),那么预制构件的安装就会受到影响,甚至暂停,需要处理完问题后再进行下一道工序,从而造成安装时间延长,成本增加。
13.因总工期延长而增加的财务成本、管理成本
理论上,装配式建筑可以缩短建设工期,但由于装配式混凝土建筑兼有预制、现浇两种施工内容,较传统现浇混凝土建筑多出预制构件的设计、生产、安装工序,加之很多项目没有在地下室结构完工前完成安装所需预制构件的生产,或者没有通过外墙一体化施工来节约外装修施工时间,或者没有通过内装修穿插施工来节约总工期,导致装配式混凝土建筑的总工期反而被延长,从而产生了额外的财务成本和管理成本。

▲ 图2-12 夹芯保温外墙板因质量问题需要退场

▲ 图2-13 转换层伸出钢筋严重偏位
2.3.2 可压缩的成本增量
1.标准的审慎和保守等原因导致的成本增量
现有标准的个别规定过于审慎和保守,有些要求高于国外同类标准,譬如叠合楼板出筋问题、同一层内既有预制又有现浇抗侧力构件时现浇竖向构件内力放大问题、多层装配剪力墙结构位移角限值要求过严问题等。标准还偏重于强调结构系统,对四个系统的综合平衡考虑不足。标准的审慎和保守及考虑不周都不利于装配式混凝土建筑的成本降低。现行标准图也存在不利于效率提高、成本降低的地方。
2.叠合楼板较现浇板厚20mm而增加的成本
因常规设计的机电管线通常预埋在混凝土结构中,所以叠合楼板上面的后浇混凝土层需要加厚,导致叠合楼板的整体厚度超过原设计的现浇楼板厚度20mm左右,增加混凝土用量0.014~0.016m3/m2,增加钢筋用量0.42~0.48kg/m2;因此也增加了地上楼层结构荷载约0.35kN/m2(相当于33层的住宅要增加近0.7层的荷载),增加了钢筋混凝土用量,这都导致了成本的增加。如果实施管线分离,或者尽可能减少管线预埋在楼板中,就可以压缩部分成本增量。
3.现浇改预制而增加的钢筋及混凝土
目前的经验数据是单体建筑的预制率20%~40%,钢筋和混凝土含量增加10%~25%。《装配式混凝土建筑技术管理与成本控制》一书中分析了上海某18层剪力墙结构住宅案例(单体建筑预制率40%),装配式与传统现浇之间的结构构件的钢筋和混凝土用量差异达到15%,钢筋用量增加6~10kg/m2,混凝土用量增加0.025~0.035m3/m2。因此导致的成本增量约55~88元/m2。这部分成本增量除了规范原因以外也有设计是否前置、设计是否熟悉预制构件生产施工全过程的原因,随着设计的成熟和精细化,可以压缩部分成本增量。
4.因预制而增加的连接成本(连接件、结合面)
可靠的连接是装配式结构安全最基本的保障,也是建筑防水保温的关键。结构连接包括套筒灌浆连接、浆锚搭接连接、后浇混凝土连接、预制构件的粗糙面和键槽构造、螺栓连接、焊接连接等;建筑连接包括外墙接缝。连接工艺、连接材料都会带来成本增量,尤其是连接材料在当前技术标准较高、供应商较少、价格较高的情况下。但随着技术研发和市场成熟,就可以压缩部分成本增量。例如《钢筋灌浆套筒连接技术应用规程》JGJ355正在进行修订,修订后有可能使生产材料范围扩大、生产企业条件放宽,从而有更多企业生产和供应,提供给市场质量更优和价格更经济的连接件。
5.部分材料因进口或垄断而增加的成本
灌浆套筒及灌浆料在国产化前,完全靠进口,价格高昂,现在国内有了标准、有了专利,实现了国产化,灌浆套筒及灌浆料价格开始大幅降低,灌浆连接的成本增量也得以大幅压缩。
目前夹芯保温墙板金属拉结件、外墙接缝防水布等依然需要进口。非金属拉结件已经实现国产化(例如南京斯贝尔FRP拉结件),成本大幅降低,而金属拉结件仍靠进口德国哈芬等公司的产品(图2-14),成本仍较高;外墙接缝防水布仅西卡等公司有供应,价格较高。随着国内企业技术研发的不断深入,因材料进口原因而导致的成本增量将进一步压缩。

▲ 图2-14 德国哈芬金属拉结件
6.标准化程度低而增加的人工成本
装配式建筑的优势之一就是预制构件通过规模化和自动化生产,从而减少人工消耗量,降低人工成本。标准化设计是前提条件,我国现阶段的标准化程度还较低,即使配备了自动化生产线也只能生产并不标准的预制构件,导致生产效率低下,构件生产环节的人工消耗量并未得到实质减少,行业平均的每立方米构件的人工消耗量在1~1.5工日左右(美国0.25~0.3工日),人工成本并不比现浇混凝土低。这部分成本增量随着标准化的普及和提高将会被逐渐压缩。
7.标准化程度低而增加的模具成本
模具周转次数越多,模具的摊销成本越低,而模具的周转次数由标准化程度决定。目前我国的标准化程度较低,不同层级的标准没有形成合力,重结构轻建筑,国家层级的标准化体系尚在建立和完善中,区域级标准化正在逐步构建中,企业级标准化受产品个性化制约进展缓慢,除个别大型房地产企业的标准化体系应用较为成熟外,大多数企业的标准化没有建立或者在项目层级、构件层级等低层级应用上,钢模具周转次数太低,大多数项目在40~80次之间,远没有达到钢模具最起码的200次周转次数。随着社会和企业对标准化的重视程度日益增强和解决标准化与个性化矛盾的技术能力的增强,标准化程度逐渐在提升,模具周转次数将逐渐增加,模具成本也会逐渐压缩。
8.模具厂产能不足而增加的成本
在装配式建筑发展较快的地区,预制构件工厂的数量在不断地增加,且构件厂都在满负荷生产,所以需要模具量较大,许多模具厂都出现产能不足、供不应求的情况,导致模具价格持续上涨,目前最高已达到1.5万元/t,而在供需相对平衡的地区的模具价格在1~1.3万元/t左右。随着模具市场的不断完善和模具周转次数的增加,因模具价格偏高导致的成本增量将得到压缩。
9.因人才结构和人才数量不足而增加的成本
我国现阶段无论是甲方、设计、生产,还是施工管理等各个环节都存在人才结构不合理、人才数量不足的问题,关键人才严重短缺、国际人才稀缺,人才问题严重制约了装配式建筑的发展,学习成本、犯错成本,是装配式成本增量的很大因素之一。甲方人才缺乏,会导致前期策划重视不够或质量不高;设计人才缺乏,会使标准化设计能力、集成管理能力不足,能兼顾生产、施工、成本的设计并不多见;生产人才缺乏,加之部分地区预制构件供不应求的现状,造成构件的生产质量不精细、成本控制不力;施工管理人才缺乏,导致关键节点的施工质量精度与效率不高,甚至不达标。这些情况都造成了成本的额外增加,只有扭转重硬件轻软实力,只用人不培训的作法,这部分成本增量才能得到有效遏制并消减。
10.因预制构件工厂产能率低而增加的成本
预制构件成本中固定成本占有一定的比例,如果实际产能低于设计产能,固定成本的占比就高,就会造成构件成本的增加。产能率低主要由两种原因造成,一是任务不饱满;二是任务饱满但生产效率低。例如上海的预制构件工厂任务普遍处于饱满状态,但2018年的统计数据显示上海本地构件厂的实际产能率仅为69%,外地进沪构件厂的产能率更低,平均为55%。产能率低导致的成本增量随着产业布局优化和标准化程度的提高将逐渐得到压缩。
11.预制构件工厂生产不均衡而产生的成本增量
预制构件的工厂化生产对计划性、连续性要求较高,一旦出现计划调整或产能忽高忽低的情况就会导致生产不均衡,生产效率降低,生产成本增加。而我国现阶段的预制构件工厂绝大多数是订单式、被动式生产,生产预制构件的种类、数量及时间几乎完全受制于市场需求,不是主动性生产,计划性和均衡性无法得到保障。随着国家层级标准体系的建立、完善,这一局面将逐渐得到改善,成本增量也将逐渐得到压缩。
12.预制构件多用蒸汽养护而增加的养护成本
预制构件一般采用蒸汽养护以提高早期强度、缩短养护时间、实现快速脱模、提高生产效率。但蒸汽养护较自然养护成本增量大,如果设施缺陷及管理不善成本增量会更高。如固定模台没有自动温控系统,养护过程管理不到位甚至失控;养护窑没有进行有效分仓,保温效果不好等。随着养护设施的不断完善,温控系统的普及和太阳能等自然能源的利用,养护成本增量也将会得到有效地压缩。
13.因预制构件存放不当而产生的成本增量
因预制构件存放不当而产生的成本增量主要包括两个方面:存放随意及混乱,如叠合楼板不同规格混叠存放导致损坏而产生的成本增量;预制构件存放时间过长会造成大量的资金占用、场地占用等成本增量。
通过精细化及信息化的管理可以规范存放作业,通过周密的计划管理可以减少存放时间,通过优化存放方式可以减少存放场地占用。因存放不当产生的成本增量可以通过改善管理、升级设施等得到压缩。
14.运输效率低、装车辆不足而增加的运输成本
现阶段我国的预制构件运输体系不完善,运输设备也不先进(图2-15),预制构件工厂、运输单位、施工单位协同不够,构件标准化程度低,装车量不足,运输过程受限较多等,这些都造成了运输效率低下,运输成本偏高。随着运输体系的完善、先进专用运输车辆的使用、标准化程度的提高等,运输效率低、装车量不足导致的成本增量是能够得到压缩的。
15.预制构件工厂分布不均而增加的运输成本
现阶段我国预制构件的生产企业处于盲目生长期,缺乏统一的产能布局规划,加之各地区的市场准入制度的限制,造成部分地区产能过剩,部分地方又产能不足。这种不均衡的情况,导致预制构件运输距离难以从经济性方面进行考量,实际运距往往大大超过合理运距,例如上海的构件供不应求,需要从周边省市购买,特别是双T板这类可供应企业稀少的构件,造成运输成本增量较大。随着构件厂的统筹合理布局,这种成本增量也可以逐步得到压缩。
16.预制构件损坏造成的修补成本
由于管理、设备工具、模具、人员等诸多方面原因,预制构件从生产到安装全过程中都有可能出现质量缺陷,存放、运输不当也会造成构件出现质量缺陷,出现质量缺陷的构件需要修补,无形中又增加了修补成本(图2-16)。构件质量缺陷问题在装配式建筑的发展初期尤其突出,产生的成本增量较多,随着管理的完善、生产工艺及设备工器具的成熟、工人操作水平的提高,这一部分成本增量将会逐渐得到压缩。

▲ 图2-15 目前常用的运输车辆

▲ 图2-16 预制阳台正在由4个工人进行修补
17.招标竞争性水平不高而增加的成本
现阶段,装配式建筑积极推进且预制率要求较高的城市,普遍存在预制构件供不应求的情况。在这种情况下市场竞争机制近乎失效,导致构件价格居高不下,出现了装配式建筑占新建建筑比例越高、预制率或装配率越高,构件价格反而越高的不正常现象。随着当地构件产能和生产效率的提高,市场竞争应逐步回归正常,成本增量会得到压缩。
18.因预制而增加的起重机成本
由于预制构件较重(单件重量1~5t),一般情况下施工现场需要比传统现浇结构配备更大规格的塔式起重机。塔式起重机成本主要由起重机规格和使用时间决定,起重机的规格是通过拆分设计与施工的协调来综合选择,或者通过个别构件使用轮式起重机的方法配合完成。而使用时间主要由结构施工效率决定。在预制率30%的情况下,大多数住宅项目的单层结构工期在5~7d,比传统现浇结构反而多出1~3d。这一部分主要是由于施工不熟练、效率不高导致的成本增量,具有一定的压缩空间。
19.因施工现场增设存放场地而增加的成本
目前我国的装配式混凝土建筑施工还不能完全实现直接吊装,所以施工现场需要设置预制构件存放场地,存放场地需要硬化,构件存放需要使用存放架及垫木、垫方等,如果存放场地布置在地下室上面,地下室顶板还需要加固,还要设专人对存放场地进行管理,以上都造成了成本的增加。所以应尽可能采取直接吊装,以及通过施工单位与预制构件工厂密切协同来减少现场构件的存放量,就可以压缩施工现场的存放成本。
2.3.3 不可避免和不可压缩的成本增量
1.与装配式相关的管理成本
装配式建筑较传统现浇建筑更复杂,集成度更高,在管理上多出了技术策划环节,在设计工作中多出了预制构件拆分设计、构件设计、连接节点设计、模具设计等工作内容,这些管理工作的完成质量和精细化程度对降低成本增量非常关键。加之目前甲方管理团队中具备装配式建筑经验的专业人士普遍相对缺乏,在现阶段多采取引进咨询顾问的方式补短板。这一项成本增量会长期存在,但压缩空间不大,也不建议过度压缩。
2.为满足装配式规范或适合装配式进行优化设计需要而增加的成本
为适合装配式生产和施工特点,在结构设计中对多规格的构件进行合理归并,或者对多规格的钢筋进行归并等措施来减少模具种类,在节约模具成本的同时会增加结构钢筋和混凝土的用量;以及在柱梁结构中将框架梁梁高垂直方向高差调整到100mm以上,从而使截面变高,或者为控制梁负筋不超过三排(120mm厚的板高范围内现浇叠合层,最多只能排布两排负筋),梁需要加宽或加高,这些为适应预制构件在现场的安装也使结构钢筋和混凝土的用量有所增加。
3.因采用外墙保温装饰一体化等集成设计而增加的成本
采用PCF板、夹芯保温板一体化工艺会增加外叶板、拉结件、增加生产人工等成本,以及由于额外增加了外叶板导致结构荷载增加的成本,这部分成本是生产工艺本身造成的,从生产工艺和材料使用角度而言成本压缩空间不大。类似情况还有石材反打工艺增加的卡勾连接件等。
4.预制构件在生产、运输、施工环节因工艺需要增加的成本
预制构件由于生产、运输和施工环节脱模、吊装、支撑、临时固定、设备管线安装等而增加的预埋件、包装、装卸等客观上增加的成本,一般情况也是不可压缩的成本。
2.3.4 可争取的成本减量
1.模具费
充分发挥工厂化、规模化生产的优势可以大幅降低模具等摊销类的成本。如图2-17所示,某项目预制率30%,钢模具周转次数超过30次以后可以获得模具上的减量成本,周转80次时可以获得40元/m2(地上建筑面积)的减量成本,周转达到200次时最多可降低成本约52元/m2(地上建筑面积)。国内的保障房、安居房、廉租房项目的模具周转次数平均都在100次以上,部分标准化水平高、应用成熟的房地产企业内部的模具周转次数也在100次左右,已开始获得工厂化生产的成本优势。

▲ 图2-17 某项目模具周转次数与成本增量的关系
2.内脚手架费
理论上使用叠合楼板后可以采用独立支撑体系(图2-18),取消满堂红脚手架,从而降低成本。但在实际工程中由于叠合楼板采用双向板较多,普遍有后浇带,加上管理经验不足、对安全性不放心而仍在使用满堂红脚手架。这一问题解决后可以为装配式的成本管理加分。
3.外脚手架费
外脚手架的情况与内脚手架类似,外墙预制可以免外架,但大多数项目出于技术应用不熟练,从确保安全的考虑下仍沿用传统外架方案。个别示范项目免外架后降低了成本,装配式建筑的综合优势得到突显(图2-19)。

▲ 图2-18 叠合楼板采用独立支撑体系
4.找平层抹灰费
由于预制构件的高精度,理论上是可以不用再做找平层而可以直接进行腻子层施工(图2-20)。但由于实际情况是预制与现浇并存且有连接面,预制剪力墙与轻质隔墙连接处不平或有厚度差等原因,造成多数情况下的找平层抹灰并没有取消,只是厚度变薄。这一部分成本可以通过设计、生产、施工的协同和工艺改进而节省下来,为装配式混凝土建筑的成本减量加分。

▲ 图2-19 上海某装配式项目的外挂架施工现场

▲ 图2-20 高精度的预制构件与现浇混凝土、高精砌体的无高差连接
[1] 《装配式混凝土建筑技术标准》GB/T 51231—2016的简称,本书余同。