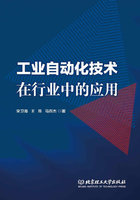
第2章 基于PLC的自动控制系统
2.1 PLC简介
PLC是一种为工业环境中的应用而设计的工业控制装置。它结合了计算机技术、自动化技术和通信技术,具有与计算机相似的结构,是一种工业通用计算机。为适应各种较为恶劣的工业环境,PLC具有很强的抗干扰能力。PLC和一般微机控制系统的不同之处在于,PLC必须经过用户二次开发编程才能使用。20世纪60年代,生产过程和生产设备主要采用继电器控制系统。继电器控制系统简单实用,但存在着明显的缺点:控制设备体积大、速度慢、可靠性低;它靠硬连接逻辑构成系统,一旦动作顺序或生产过程发生变化,就必须重新设计、布线、组装和调试,通用性和灵活性较差。1969年,美国数字公司根据通用汽车招标的要求,在世界范围内开发了第一个PLC,并成功地应用于通用公司汽车生产线。初期的PLC仅具有逻辑控制、定时、计数等功能,仅用于代替继电器控制。随着计算机技术的飞速发展,PLC以通用微处理器为核心,新增了功能操作、高速计数、中断和PID控制等功能,可以与上位机通信,实现远程控制,称为可编程序控制器PC。为了避免与个人计算机(Personal Computer, PC)混淆,人们仍习惯于将可编程序控制器简称为PLC。经过几十年的发展,PLC已经成为自动化技术(PLC、机器人和CAD/CAM)的三大支柱之一。1982年11月,国际电工委员会(International Electrotechnical Commission, IEC)制定了PLC的标准,在1987年2月颁布的第三稿中,对PLC的定义如下:可编程序控制器是一种数字运算操作的电子系统,专为在工业环境下应用而设计,它采用可编程序的存储器,用来在其内部存储执行逻辑运算、顺序控制、定时、计数和算术运算等操作命令,并通过数字式或模拟式的输入和输出控制各种类型的机械或生产过程。可编程序控制器及其有关的设备都应按照易于与工业控制系统连成一个整体,易于扩充功能的原则设计。
2.1.1 PLC的特点
1.结构简单,应用灵活
目前,PLC已有一系列大、中、小规模产品,并已标准化、系列化、模块化,配备有各种输入输出信号模块、通信模块和一些特殊功能模块。对于不同的控制对象,用户可以灵活方便地配置系统,形成不同的功能和不同规模的控制系统。当生产工艺要求发生变化时,不需要重新连接。通过编写应用软件可以实现新工艺要求的控制功能。
2.编程方便,易于使用
PLC采用的主要编程语言——梯形图与继电器控制电路有很多相似之处,程序图像直观,指令容易学习,编程步骤和方法易于理解和掌握,不需要特殊的计算机知识。有一定的电气和电气控制技术知识的人员都可以在短时间内学会。
3.功能完善,适用性强
PLC具有强大的数字和模拟数据处理功能,如逻辑运算、算术运算、特殊功能计算等。PLC具有常用的控制功能,如PID闭环控制、中断控制等。PLC可扩展特殊功能,如高速计数、电子凸轮控制、伺服电动机定位、多轴运动插补控制等。PLC可以组成各种工业网络,实现数据传输、HMI监控等功能。
4.可靠性高,抗干扰能力强
虽然微型计算机具有很强的功能,但在工业领域中抗干扰能力和抗电磁干扰能力都很差。功率波动、机械振动、温度和湿度变化都会使普通微型计算机不能正常工作,而PLC是专门为工业环境应用而设计的。在硬件方面,PLC采用了严格的生产工艺,内部电路采用了先进的抗干扰技术,对易受干扰的部件采用电磁屏蔽,I/O端口采用光电隔离。因此,PLC对电磁干扰、高温、低温、功率波动有较强的抗干扰能力。在软件方面,PLC利用故障检测、诊断、信息保护和恢复等手段,一旦出现异常,CPU立即采取有效措施,防止故障扩大,从而大大提高了PLC的可靠性。
2.1.2 PLC的应用
PLC由于其自身的特点和优势,已被广泛应用于工业控制领域,包括机械、冶金、化工、电力、交通、建筑等领域。PLC的主要应用领域包括以下几个方面:
1.逻辑控制
逻辑控制是PLC最基本的应用。它可以取代传统的继电器控制装置,如机床电气控制、各种电动机控制等。它可以实现组合逻辑控制、定时控制和顺序逻辑控制等功能。PLC的逻辑控制功能不仅可用于单机控制,还可用于多机群控制和自动生产线控制。
2.运动控制
PLC采用一个特殊的运动控制模块来控制直线运动或图形运动的位置、速度和加速度,实现单轴、双轴和多轴联动控制。PLC的运动控制功能可应用于金属切削机床、机器人、电动机等各种机械中,方便地实现机械设备的自动控制。
3.闭环过程控制
闭环过程控制是指对温度、压力、流量等连续变化的模拟量的闭环控制,PLC通过其模拟量I/O模块及数据处理和数据运算等功能,实现对模拟量的闭环控制。
4.工业网络通信
PLC的通信包括主机与远程I/O之间的通信,多PLC之间的通信及PLC与计算机、HMI设备、转换器、数控设备等其他智能设备之间的通信。PLC与其他智能控制装置一起可构成分散式控制系统DCS。