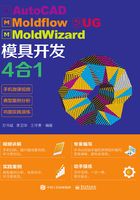
2.3 初步分析
本案例希望通过“BEM冷却+填充+保压+翘曲”分析,改善制品的质量。以Moldflow最佳浇口位置区域分析结果为基础,展开基本分析。
技术要点
BEM(全称“边界元法”)冷却分析将计算稳定状态或整个成型周期的平均温度。至少需要为此分析准备成型零件和冷却管道的模型。使用这种方法,很容易修改冷却管道的位置,以查看冷却管道位置的影响。创建镶件来代表由不同材料(通常采用具有较高热传导率的材料)制成的工具区域。
2.3.1 工艺设置与分析过程
① 选择分析序列。在【成型工艺设置】面板中单击【分析序列】按钮,弹出【选择分析序列】对话框。从中选择“冷却+填充+保压+翘曲”,再单击【确定】按钮,如图2-43所示。
② 初步分析时工艺设置参数尽量采用默认设置。由于继承了前面分析的结果,所以无须重新选择材料。单击【工艺设置】按钮,弹出【工艺设置向导】对话框。设置第1页,如图2-44所示。

图2-43 选择分析序列

图2-44 设置第1页
③ 单击【下一步】按钮进入第2页。然后设置如图2-45所示的参数。
④ 单击【下一步】按钮进入第3页。在第3页中勾选【考虑模具热膨胀】和【分离翘曲原因】复选框。最后单击【完成】按钮,如图2-46所示。
⑤ 当所有应该设置的参数都完成后,单击【开始分析】按钮,Moldflow启动分析。可以单击【作业管理器】按钮
,弹出【作业管理器】对话框以查看分析进程,如图2-47所示。

图2-45 设置第2页

图2-46 设置第3页

图2-47 查看分析进程
2.3.2 分析结果解读
经过较长时间的耐心等待之后,完成了“冷却+填充+保压+翘曲”分析。下面解读分析结果。
在方案任务窗格中可以查看分析的结果,本例有流动、冷却和翘曲3个结果,如图2-48所示。
1.流动分析
为了简化分析的时间,下面将重要的分析结果一一列出。

图2-48 分析结果列表
(1)充填时间。
如图2-49所示,按Moldflow常规的设置,所得出的充填时间为0.6829s,充填时间较短。从充填效果看,熔体流动性较为一般,很明显制件的头部端比尾部端充填得较慢一些。

图2-49 充填时间
(2)流动前沿温度。
流动前沿温度结果由充填分析生成,显示的是流动前沿到达位于塑料横截面中心的指定点时聚合物的温度。
图2-50表示的是充填过程中流动波前温度的分布,产品中大部分区域波前温度较为平衡,在223.2℃~231.7℃之间。但是流动性好的制件,波前温度差应该在2℃~5℃之间较为合理。本制件有约8℃的落差,说明存在因充填时间较短而产生的迟滞区域。
技术要点
如果零件薄壁区域中的流动前沿温度过低,则迟滞可能导致短射。在流动前沿温度上升数摄氏度的区域中,可能出现材料降解和表面缺陷。

图2-50 流动前沿温度
(3)体积收缩率。
体积收缩率是指从保压阶段结束到零件冷却至环境参考温度(默认值为25°C/77°F)时局部密度的百分比增量。体积收缩率主要用来检查制件中是否存在缩痕缺陷。
从本例制件分析的体积收缩率结果来看,体积收缩率最高达到了6.284%(0.06284),最低为0.1932%,体积收缩不均匀,产生缩痕缺陷。再看图2-51中的收缩率较为严重的区域是在充填末端,而好的制件其体积收缩率应该是很均衡的。

图2-51 体积收缩率
(4)气穴。
气穴一般产生在流动前沿与型腔壁之间,因形成旋涡并挤压便会产生气穴(常说的“气泡”),通常的结果是在零件表面形成小孔或瑕疵。在极端情况下,这种挤压将使温度升高到引起塑料降解或燃烧的水平。
不管制件的流动性有多么好,总会在充填末端产生气穴。本例制件的气穴效果如图2-52所示,总的来看,气穴产生在孔、倒扣位置区域,这些位置通常会设计顶杆及斜顶等顶出机构,借助于顶杆间隙,排气就容易解决。所以气穴不会对制件带来不良影响。

图2-52 气穴
(5)熔接线。
熔接线表达了两个流动前沿相遇时合流的角度。熔接线的显示位置可以标识结构弱点和(或)表面瑕疵。
从如图2-53所示的熔接线分布图可以看出,熔接线主要集中于孔、倒扣位置,数量较少。可以适当加大熔体温度、注射速度或保压压力,以便更好地解决熔接线的问题。
技术要点
如果熔接线集中出现在产品中心或筋、肋较少的受力区域,极易造成产品断裂。

图2-53 熔接线
2.冷却分析
在冷却分析结果中,以回路冷却液温度、产品最高温度、产品冷却时间3个主要方面来进行介绍。
(1)达到顶出温度的时间,零件。
如图2-54所示为“达到顶出温度的时间,零件”的冷却过程。这4个图表示的是产品的冷却凝固过程,蓝色区域表示最先凝固的区域,一般最薄处最先凝固,最厚处最后凝固。从图中可看出,较厚区域周围先行凝固而切断了保压回路,致使较厚区域得不到有效保压。

图2-54 冷却过程
(2)回路冷却液温度。
如图2-55所示,冷却介质最低温度与最高温度之差仅约为0.33℃,总的来说冷却系统是接近于恒温的。而最高温度与室温也差不多,也就是说整个冷却系统设计还是成功的。

图2-55 回路冷却液温度
(3)最高温度,零件。
如图2-56所示,制品的最高温度为43.17℃,最低温度为30.37℃,温差较大,冷却不均匀,易产生翘曲。这需要对冷却管道与制件间的距离,或者管道直径等进行调整,直至符合设计要求为止。

图2-56 最高温度,零件
(4)温度,零件。
查看“温度,零件”结果可找出局部的热点或冷点,以及确定它们是否会影响周期时间和零件翘曲。如果有热点或冷点,则可能需要调整冷却管道。零件整个顶面或底面与目标模具之间的温差不应超过±10°C。
如图2-57所示,零件某个点的最高温度为45℃,最低温度为27.01℃,温差超过正常值(10°C)18°C左右,说明冷却效果不理想,需要改善冷却系统设计。

图2-57 温度,零件
3.翘曲分析
翘曲是塑件未按照设计的形状成型,而发生表面的扭曲,塑件翘曲归因于成型塑件的不均匀收缩。假如整个塑件有均匀的收缩率,塑件变形就不会翘曲,而仅仅会缩小尺寸;然而,由于分子链/纤维配向性、模具冷却、塑件设计、模具设计及成型条件等诸多因素的交互影响,要能达到低收缩或均匀收缩是一件非常复杂的工作。
如图2-58所示为翘曲总变形。总的来说,产品的翘曲在3个方向都有,尤其在X方向上的翘曲量最大,总的翘曲量为0.4566mm。

图2-58 翘曲总变形
技术要点
要想将翘曲变形的比例因子放大,可以在分析结果中选中某一变形,然后选择右键快捷菜单【属性】命令,在打开的【图形属性】对话框的【变形】选项卡中设置“比例因子值”即可,如图2-59所示。

图2-59 设置比例因子
(1)变形,冷却不均:变形。
如图2-60所示为导致翘曲的冷却不均因素的图像。可以看出冷却因素对翘曲的影响是比较小的,3个方向上都有少量的变形。

图2-60 冷却不均因素的翘曲变形
(2)变形,收缩不均:变形。
如图2-61所示为导致翘曲的收缩不均因素的图像,从图中可以看出,收缩不均因素对翘曲变形影响较大,是导致翘曲变形的主要因素。

图2-61 收缩不均因素的翘曲变形
知识链接
收缩与残留应力
塑料射出成型本身就会发生收缩,因为从制程温度降到室温,会造成聚合物的密度变化,造成收缩。整个塑件和剖面的收缩差异会造成内部残留应力,其效应与外力完全相同。在射出成型时,假如残留应力高于塑件结构的强度,塑件就会于脱模后翘曲,或是受外力而产生破裂。残留应力(residual stress)是塑件成型时,熔融料流动所引发(flow-induced)或者热效应所引发(thermal-induced)的,而且冻结在塑件内的应力。假如残留应力高于塑件的结构强度,塑件可能在射出时翘曲,或者稍后承受负荷而破裂。残留应力是塑件收缩和翘曲的主因,而减少充填模穴造成之剪应力的良好成型条件与设计,可以降低熔胶流动所引发的残留应力。同样地,充足的保压和均匀的冷却可以降低热效应引发的残留应力。对于添加纤维的材料而言,提升均匀机械性质的成型条件可以降低热效应所引发的残留应力。
(3)导致翘曲的取向因素。
如图2-62所示为导致翘曲的取向因素的图像,从图中可以看出,取向因素并没有导致翘曲产生。

图2-62 取向因素的翘曲变形
4.制品缺陷
从初次的按Moldflow理论值进行的分析结果可以得出如下结论:
(1)流动前沿温度温差大,冷却效果不太理想,有迟滞现象。
(2)制件产生了较为严重的体积收缩。
(3)翘曲变形量较大,其中收缩不均因素为主要因素。
技术要点
塑件产生过量收缩的原因包括射出压力太低、保压时间不足或冷却时间不足、熔融料温度太高、模具温度太高、保压压力太低等。
5.解决方案
针对初步分析中提出的缺陷问题,为优化分析给出合理建议:
● 改善冷却效果,即改变冷却管道管径、冷却回路与制件之间的间距。
● 通过设置工艺参数,调整注射压力、注射时间、冷却时间、模具温度、熔体温度、保压压力等值。