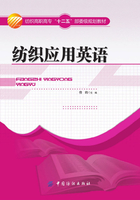
Task 1 To describe the cotton ring spinning process描述棉纺环锭纺工艺
General information Cotton spinning棉纺
Ring spinning is a traditional common processing method,because it exhibits significant advantages in comparison with the new spinning processes.Most cotton yarn is still processed in this way.Ring spinning frame will continue to be the most widely used form of spinning machine in the near future.
Cotton spinning is essentially a discontinuous process in which the short raw fiber goes through a series of machines that transform it into a continuous strand of yarn.The major production stages of ring spinning are opening,blending,carding,drawing,roving,and spinning,which includes twisting and winding.The spinning process can be summarized as Fig.2.1.

Fig.2.1 Ring spinning process for cotton yarn
Blending,Opening,and Cleaning
Blending(Fig.2.2)and opening(Fig.2.3),which separate or break up bales of fibers,are carried out in enclosed machinery to reduce the dust level in the plant.Fiber from the specified bales is fed into a hopper,where the processes of separating the mass of fibers into tufts and removing trash are begun.Because man-made fibers are more uniform and contain less trash than natural fibers,they require less processing.Dirt and impurities which are heavier than the fibers and are not entangled in them are separated from the fibers by mechanical forces and air.The fibers are now in a loose,fluffy mass that may be conveyed with forced air through a chute directly to a card,or to a picker and then a card.Where pickers are used,the fibers are further opened,blended,and cleaned with a system of rollers,conveyors,and forced air.They are then transported to a collecting cylinder that forms a thin layer or batt of fibers.The fiber batt is rolled up,much like a very large roll of absorbent cotton,to form a picker lap.The lap is then transported to the card for further processing.Carding

Fig.2.2 Blending

Fig.2.3 Opening
The fibers after blending and opening are delivered to the card in the form of a picker lap or from a chute-fed hopper.They are randomly arranged and may contain trash and short fibers that are not suitable for further processing.A card consists of a large rotating cylinder covered with wire pins or teeth and a series of flats(interlaced rectangular boards).The flats form an endless belt that rotates above the card cylinder.The cylinder and the flats rotate in the same direction but at different speeds,to tease the fibers into a thin,filmy web.In the process,short fibers and trash are removed and deposited on the flats.The fibers,which remain on the card cylinder,are partially aligned,so their longitudinal axes are somewhat parallel to each other and the length of the card web.The thin web is pulled off the cylinder and gathered into a soft mass,which is pulled through a cone-shaped condenser,or trumpet,to produce a ropelike strand called a sliver.A cotton card sliver has no twist and only a little strength,provided by the entangling of fibers.The strength is adequate to allow the sliver to be doffed(removed)into a can or placed on a conveyor for transfer to the next processing step,which is drawing or drafting.Carding process is shown as Fig.2.4.

Fig.2.4 Carding
Drawing
A drawing frame(Fig.2.5)uses a series of rollers which are arranged in pairs and rotating at different speeds,to draw out or draft sliver.At the first drawing frame,several card slivers(usually eight)are combined to further blend the fibers.The slivers are pulled from the back of the machine through a series of pairs of rollers.The back pair of rollers is rotating at a lower speed than the pair at the front of the frame.Because the sliver is being taken up at a faster speed than it is being delivered,the sliver becomes thinner as it is drawn out,or drafted.Both card sliver,which has been drafted once,and comber sliver must go through finisher drawing to receive further blending and alignment.In some cases,a second finisher drawing occurs.The drafting through a series of rollers is the same in all the processes.For fine count yarns,a higher draft producing a lighter weight sliver is possible.After drafting,the fibers are in their most parallel alignment.The strand is not twisted,although some twisting may occur as the sliver is doffed into the sliver can.

Fig.2.5 Drawing
At this point,ring-spun yarns go through a roving process;other short-staple yarns are spun directly from drawn sliver.
Combing
For high quality yarns of superior evenness,smoothness,fineness,and strength,fibers are combed as well as carded.A common procedure is to combine 48 slivers from breaker drawing to form a lap for the comber.The 30 pound laps are moved to the comber,where fine metal wires clean out the remaining short fibers and other impurities.The combed fiber is condensed into a comber sliver.
Combing(Fig.2.6)is a key process that makes the difference between an ordinary yarn and a quality yarn.It enables the ultimate yarn to be smoother,finer,stronger,and more uniform than other spinning system.

Fig.2.6 Combing
Roving
Sliver cans from finisher drawing are dotted and moved to the roving frame,where the sliver is drafted to about one-eighth of its original diameter by three pairs of rollers rotating at different speeds.The first set moves at a relatively slow speed,the middle set at an intermediate speed,and the final set a speed about 10 times the speed of the first.This drafts the fibers out,reduces the diameter of the strand,and imparts some additional parallel alignment to the fibers.The new strand,called a roving,is wound onto a bobbin(Fig.2.7).The winding process produces a small amount of twist,which imparts some added strength to the strand.The bobbins are doffed and transferred to the spinning area.

Fig.2.7 Roving
Spinning
Spinning is the final process in production of single yarn.The roving is drafted to the desired diameter,and the desired amount of twist is added.The method of drafting used in spinning is the same as that used in drawing and roving.The twist is imparted by the movement of the fiber strand around the bobbin and by the speed of rotation of the spindle holding the bobbin.The fiber strand is pulled from the drafting elements;fed through a U-shaped guide called a traveler,which moves freely around the bobbin spindle on a circular track or ring;and wrapped around the bobbin.The process is called ring spinning because the twist in the yarn is produced as the traveler moves around the ring.

Fig.2.8 Principle of ring spinning
Spinning process is shown as Fig.2.8.
New Words and Expressions
ring spinning 环锭纺
strand 须条
stages 工序
opening 开清
blending 混合
card 梳理,梳理机
drawing 并条,牵伸
roving 粗纱
twist 加捻,捻度
wind 卷绕
bales 棉包
dust level 含尘量
hopper 棉箱
tufts 纤维束
remove 除去
trash 杂质
man-made fiber 人造纤维,化学纤维
uniform 均匀
natural fiber 天然纤维
picker 清棉机
cylinder 锡林
layer 层
batt 纤维层
roller 罗拉
picker lap 棉卷
chute-fed hopper 喂棉箱
wire pins 金属针布
flat 盖板
tease 撕扯
align 平行排列
sliver 条子
card sliver 生条
can 条筒
drafting 牵伸
drawing frame 并条机
comber sliver 精梳条
fine-count yarns 细支纱
lighter-weight 轻定量
sliver can 条筒
combing 精梳
evenness 均匀度
fineness 细度
condense 凝聚
doff 落纱
roving frame 粗纱机
bobbin 筒管
spindle 锭子
drafting elements 牵伸装置
U-shaped guide U形导纱钩
traveler 钢丝圈
wrap 卷绕,缠绕
Notes
1.The fibers,which remain on the card cylinder,are partially aligned,so their longitudinal axes are somewhat parallel to each other and the length of the card web.
在梳棉机锡林上的纤维部分伸直,因此,纤维轴向相互之间以及纤维与棉网之间基本上平行。
2.A drawing frame uses a series of rollers,which are arranged in pairs and rotating at different speeds,to draw out or draft sliver.
每台并条机使用一系列罗拉,这些成对的罗拉以不同的速度对条子进行牵伸。
3.Sliver cans from finisher drawing are dotted and moved to the roving frame,where the sliver is drafted to about one-eighth of its original diameter by three pairs of rollers rotating at different speeds.
从末道并条机落下来的条筒运送至粗纱机,在粗纱机上,熟条经过不同速度的三对罗拉牵伸,变成了粗细大约为原来直径的八分之一的粗纱。
Exercises
1.What are the basic cotton spinning processes?
2.What are the differences between carded and combed yarns?