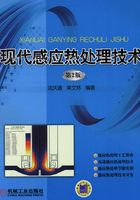
3.1 电流频率的选择
1.电流透入深度
感应表面淬火的机理是利用电流的趋肤效应。感应加热时,从工件表面电流最大值处(I0)测到I0/e(e为自然对数的底,可取2.7)处的深度,称为电流透入深度d,如图3-1所示。
电流透入深度d(mm)计算式如下:
式中 μ——材料的磁导率,当钢加热到居里点温度以上时,μ=1(相对磁导率);
ρ——材料电阻率(Ω·cm);
f——电流频率(Hz)。
图3-1 表面加热时电流沿深度的变化
钢在800℃时,当μ=1,ρ=111×10-6Ω·cm时,电流透入深度与频率的关系见表3-1。
表3-1 钢在800℃时电流透入深度与频率的关系
2.电流频率选择的原则
1)电流频率选择的首要原则是透入式加热。钢在感应淬火加热时,当电源频率确定了,电流透入深度d也确定了,即涡流深度在一定值范围。实际上由于工件硬化层深度Ds有不同要求,因此在一定电流深度情况下,会出现两种加热状态:一种是电流透入深度d大于硬化层深度Ds,称为透入式加热;另一种是电流透入深度小于硬化层深度,称为热传导加热。
例如:一工件要求Ds=3~5mm,如果将此工件置于中频3kHz电流下加热,d=9.27mm Ds=3~5mm,d>Ds,是透入式加热;如果将此工件置于高频200kHz电流下加热,则d=1.14mm,此时d<Ds,由于涡流深度小于硬化层深度,因此要达到3~5mm的硬化层,必须靠热传导。两种加热状态的比较见图3-2和表3-2。
图3-2 透入式加热与热传导加热的比较
1—热传导加热(t=10s,ΔT=65℃,η=9%
2—透入式加热(t=4s,ΔT=65℃,η=21%
表3-2 透入式与热传导加热法对比
从两种加热法对比中得知,在大量生产条件下,无论从节能、劳动生产率表面过热度等几个方面比较,应选择透入式加热法,也称深层加热。其定义是工件热状态下的电流深度,大于工件要求的硬化层深度,即d>Ds。有资料总结为下式:0.33<Ds/d<1。最佳频率时,Ds/d=0.5。
2)电流频率选择的第二原则是感应器电效率要高。感应器的电效率取决于零件直径(厚度)与热状态下电流透入深度的比值,此值又称电尺寸。图3-3所示为加热时电尺寸对圆钢与扁钢电效率的影响。当 时,η感≈80%;当
时,η感≈70%
图3-3 加热时电尺寸对圆钢与扁钢电效率的影响
注:材料为中碳钢,温度为900℃,感应器为螺管式,内径=1.3D
生产实践中,一般将工件直径与热状态下电流透入深度之比设为4∶1。图3-4所示为不同直径圆钢棒的临界频率,即D/d应大于4。
图3-4 不同直径圆钢棒的临界频率
有资料总结感应器的电效率计算公式如下
式中 PW、P1——工件及感应器损耗功率;
Ci、CW——工件及感应器截面周边长度;
ρ1——感应器材料电阻率;
μr——钢的相对磁导率;
K1——感应器空间系数,对多匝线圈,此值为0.6~0.85,单匝线圈此值为1.0;
K2——修正系数,随工件与线圈耦合情况而变,一般在0.4~0.9对长线圈此值接近1;
Ki——线圈导体损耗系数,取决于导体管子壁厚;
K——转换系数,取决于工件外形及截面相对尺寸。
对于1~2匝轴向磁力线感应器与圆柱形钢件耦合条件下,钢件直径又大于6~8倍电流透入深度时,其近似计算公式如下:
式中 D1——感应器内径,最大不超过工件D2的20%;
D2——钢件外径;
ρ1——铜的电阻率;
ρ2——钢的电阻率;
μr——钢的相对磁导率,此值为5~10(因为在居里点前,耗能占一大部分)。
计算及试验得出,感应器的电效率η感一般为80%~85%。
3)电流频率选择的第三原则是电流频率不能太低。电流频率过低时,即热状态下电流透入深度与硬化层深度之比值太大时,必然要使用极高的功率密度此时,感应器上的载流密度极高(有些公司规定此值不大于1200A/mm2),即使在极良好的水流冷却下,感应器仍容易损坏。因此,一般规定Ds≥0.25d,这样就规定了电流频率选择的下限。
4)电流频率的选择还与噪声、振荡系统功率因数、电磁作用力有关。当电流频率增高时,在相同功率情况下,感应器上的电磁作用力、振动及噪声级下降;当电流频率增高时,系统的功率因数降低。
3.实用的电流频率选取图表
对不同硬化层深度与不同直径零件的电流频率选择原则,主要有以下两条①工件直径最好是热状态下电流透入深度的4倍以上,此时感应器电效率高②热状态下的电流透入深度最好是工件硬化层深度的2倍左右,此时为透入式加热,热效率高。不同硬化层深度所需的电流频率见表3-3
表3-3 不同硬化层深度所需的电流频率
注:“1”表示高效率;“2”表示较低效率;“3”表示不适合
(1)齿轮单频加热时频率的选择 一种频率加热齿轮时,要获得仿齿廓的淬硬层时,必须保证两个条件:
一个条件是合适的电流频率,轮齿的模数m越小,要求电流频率越高。其机理是涡流在齿上会形成局部涡流环,小模数齿的齿厚薄,如果电流频率低涡流深度深,会互相抵消,此时涡流会转而进入齿沟部分,只加热齿沟。最佳电流频率的选择公式如下:
f=K/m2
式中,K=350~600,取决于淬硬层深度与钢材。
另一个条件是合适的功率密度,即在一定加热速度下的加热时间。表3-4是单频加热时不同模数齿轮与电流频率、功率密度的对应关系。
表3-4 单频加热时不同模数齿轮与电流频率、功率密度的对应关系
(2)凸轮加热时特殊的频率计算公式 凸轮加热时,当电流频率低于最佳频率时,桃尖温度加热不足;反之,当电流频率高于最佳频率时,桃尖温度过高。下式可作为凸轮电流频率选择的参考公式:
式中 f——电流频率(Hz);
r——桃尖半径(mm)。
(3)圆钢透热时推荐的电流频率 圆钢透热时推荐的电流频率见表3-5
表3-5 圆钢透热时推荐的电流频率