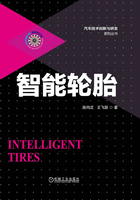
3.4 轮胎阻抗传感器
集成MEMS传感器不但可以安装在轮胎气门嘴部位进行轮胎状态的测量,而且可以嵌入在轮胎胎面内部进行轮胎状态的测量,但是,集成MEMS传感器的刚度与橡胶差别比较大,当嵌入轮胎胎面内部测量轮胎的应变时,容易破坏轮胎的应变和变形,另外,在轮胎旋转过程中,传感器容易脱落,因此,利用这种传感器直接嵌入轮胎胎面进行轮胎状态的测量存在一定的困难。
轮胎阻抗传感器是利用轮胎材料的阻抗特性进行轮胎应变特性的测量,包括轮胎电容阻抗传感器[18]、轮胎电容电阻阻抗传感器[19][20]、柔性环氧树脂电容阻抗传感器[21]、橡胶基电容阻抗传感器[22]。
由于与柔性环氧树脂材料相比,橡胶基材料具有更优越的性能,两者在原理和制作方式方面都具有相似性,因此,本部分主要阐述轮胎电容阻抗传感器、轮胎电容电阻阻抗传感器和橡胶基电容阻抗传感器,下面分类阐述其原理、结构和实验测试结果。
3.4.1 轮胎电容阻抗传感器
轮胎电容阻抗传感器利用轮胎的电容阻抗特性进行轮胎应变特性的测量,文献[18] 设计了一种轮胎电容阻抗传感器,分析了其测量原理和温度补偿原理,并通过实验测试验证了这种传感器的有效性。下面进行具体分析。
3.4.1.1 测量原理
轮胎主要由橡胶、钢丝和有机纤维组成,具体结构如图3.5所示。相邻的不同钢丝之间可以看作一个电容器,其中钢丝为导电材料,钢丝之间的橡胶为绝缘材料,如图3.6所示。

图3.5 典型子午线轮胎结构[18]

图3.6 轮胎钢丝层的电容模型[18]
钢丝作为电极,假定它的半径为a,单位长度的电荷量分别为q和-q,它们之间的距离为d,橡胶为介电材料,介电常数为ε,根据高斯定律,通过相邻钢丝中心线,距离钢丝为r处的电场Er可以表达为[18]:

相邻钢丝之间的电压为[18]:

单位长度的电容为[18]:

轮胎在外力作用下会引起胎体橡胶层的变形,橡胶层将变形传递到钢丝层,引起钢丝层的变形,钢丝层的变形会引起相邻钢丝之间距离d的变化,在钢丝层伸长时d变长,根据式(3.3),电容量变小,相反,钢丝层收缩时d变短,根据式(3.3),电容量变大,因此,轮胎胎体的变形可以引起轮胎电容量的变化,利用轮胎电容量的变化可以反映轮胎应力或变形的大小。
根据前面的分析,轮胎应变量的变化可以转化为轮胎电容量的变化,但是电容量无法实现无线传输,在利用轮胎电容阻抗传感器进行轮胎应变测量时,需要将测量值无线传输出来,因此,需要将轮胎的电容量变化转化为可以无线传输的量。通常的做法是利用匹配电阻与电容构成RC振荡电路,利用振荡频率的变化反映电容的变化,典型的RC振荡电路如图3.7所示。

图3.7 典型的RC振荡电路[18]
该典型的RC振荡电路在电阻和电容固定时,发送振荡电磁波,频率为[18]:

根据式(3.4),当电阻固定为RS=5kΩ,电容下降时,振荡频率增加;电容增加时,振荡频率下降。利用振荡频率的变化就可以反映轮胎电容量的变化。另外,电容量的变化可以反映轮胎应变量的变化,因此,利用振荡频率的变化就可以反映轮胎应变量的变化。
3.4.1.2 温度补偿方法
在实际的测量过程中,轮胎的长时间运动会引起胎内温度的升高,轮胎温度的升高会引起RC振荡器电路特性的变化,从而引起振荡频率的改变。如图3.8所示,横轴为利用嵌入在轮胎内的热电偶测量的温度,纵轴为振荡频率的变化率ft/f40,ft为温度为t℃时的振荡频率,f40为温度为40℃时的振荡频率,由图3.8可以看出,振荡频率随轮胎温度的升高而下降,因此需要进行RC振荡器的温度补偿。
RC振荡器振荡频率的变化是由于温度变化引起电阻阻抗的变化造成的,为了补偿温度变化的影响,可以为原来的电阻RS串联一个随温度升高而电阻下降的电阻。NTC热敏电阻是一种阻值随温度的升高而下降的电阻,可以满足补偿要求,它的阻值温度特性如图3.9所示。
利用NTC热敏电阻进行温度补偿的RC振荡器的典型电路如图3.10所示,此时的振荡频率为[18]:

图3.8 RC振荡电路振荡频率的温度特性[18]


图3.9 NTC热敏电阻的阻值温度特性[18]

图3.10 利用NTC热敏电阻进行温度补偿的RC振荡器电路[18]
利用NTC热敏电阻进行温度补偿的RC振荡器的振荡频率的理论和测试结果如图3.11所示,由图可以看出,利用NTC热敏电阻进行温度补偿后的频率变化率下降,理论和测试结果比较接近,因此利用NTC热敏电阻进行RC振荡器的温度补偿是有效的。
3.4.1.3 测试结果
为了对理论研究的正确性进行验证,下面进行轮胎电容阻抗传感器的静态和动态实验测试研究。
首先利用轮胎胎体的矩形切片进行静态的拉伸实验,切片结构如图3.12所示。切片的长、宽、厚分别为250mm,30mm和5mm,钢丝的直径为1.0mm,钢丝间距为2.5mm,钢丝电极在没有施加应力时的距离为70mm。
实验时,加载速度为1.0mm/min,当拉伸长度达到3mm的距离后,进行去载。利用LCR测试仪测量在加载和去载过程中轮胎电容量的变化,充电电流频率为100kHz,测量的电容量变化结果如图3.13所示,横轴为利用应变计测量的应变,纵轴为电容量的变化。由图可以看出,当拉伸负载增加时,轮胎电容量从12pF下降到8pF,由于拉伸负载的增加扩大了钢丝之间的距离,根据式(3.3)可知,轮胎电容量下降。

图3.11 利用NTC热敏电阻进行温度补偿的理论与测试结果[18]

图3.12 测试轮胎切片结构[18]
为了研究初始距离对轮胎电容量变化的影响,分别对初始电极之间距离为20mm、46mm和70mm时的电容量变化进行测量,测量结果如图3.14所示。由图可以看出,轮胎电容量的变化随初始距离的增加而增加,因此可以采用较大的初始电极距离来提高测量的精度和灵敏度。

图3.13 轮胎加载和去载过程中测量的轮胎电容量变化[18]

图3.14 当初始距离分别为20mm、46mm和70mm时测量的轮胎电容量变化[18]
轮胎电容阻抗的变化需要通过RC振荡器转换为振荡频率的变化,通过无线发射器发射出去,然后通过无线接收器接收,根据接收信号,测量信号频率的变化,根据频率的变化获得轮胎应变量的大小。轮胎应变量测试系统的原理如图3.15所示,轮胎与RC振荡器相连,RC振荡器将轮胎变形引起的电容量变化转化为振荡频率的变化,变化的频率通过振荡电路无线发射出去,无线接收器接收RC振荡器发送的振荡信号,并送给PIC频率计数器,PIC频率计数器对振荡信号的频率进行计数,并将计数结果传送到PC机,PC机根据频率与电容量变化的关系以及电容量变化与轮胎应变量变化之间的关系,最终得到轮胎应变量的变化。

图3.15 利用RC振荡器的轮胎应变量测试系统原理图[18]
利用图3.15的测试系统测量轮胎胎体切片在静态加载和去载过程的应变量,测试结果如图3.16所示,横轴为应变量,纵轴为测量的振荡频率变化率Δf/f,频率变化率为频率变化量与不加载情况下的频率的比率。由图可以看出,应变量和频率变化率之间为近似线性的关系,并且随着应变量增加,频率变化率增加,这与式(3.3)和式(3.5)的理论描述的应变与频率之间的关系一致,应变量增加,电极之间的距离增加,轮胎电容量下降,从而振荡频率增加。

图3.16 加载和去载过程中的频率变化率和应变量之间的测量关系[18]
在轮胎切片实验的基础上,下面利用由经过NTC热敏电阻温度补偿的RC振荡器构成的轮胎电容阻抗传感器进行轮胎应力的静态和动态测试实验,测试轮胎的胎宽为175mm,扁平率为70%,直径为355.6mm,轮子的最大速度为180km/h,轮胎压力为200kPa。
静态压缩实验测量的频率与应变之间的关系如图3.17所示,横轴为应变量,纵轴为振荡电路的测量频率,由图可以看出它们之间近似为线性关系。
另外,进行了轮胎的动态旋转测试实验,轮胎在旋转过程中,在接触路面之前先压缩,接触路面后开始拉伸,离开路面后又进行压缩,该过程可以用图3.18形象地表示。动态测试的结果如图3.19所示,横轴为时间,纵轴为测量频率和应变,频率与应变的变化趋势基本一致,因此,它们之间为近似线性关系,利用频率的变化可以反映轮胎应变或轮胎压力的变化。

图3.17 静态压缩实验测量的频率与应变量之间的关系[18]

图3.18 轮胎与路面接触过程的变形[18]

图3.19 动态旋转测试过程的测量频率和应变量变化[18]
3.4.2 轮胎电容电阻阻抗传感器
由于轮胎的橡胶内含有炭黑,炭黑为导电材料,因此,轮胎的橡胶不完全为介电材料,还具有一定的导电性,轮胎胎体钢丝层的相邻钢丝之间存在电容和电阻阻抗[19][20]。通过研究轮胎的电容和电阻阻抗特性,可以设计轮胎电容电阻阻抗传感器。文献[19]设计了一种轮胎电容电阻阻抗传感器,通过理论分析和实验测试的方法,建立了轮胎电容电阻阻抗与轮胎应变量之间的关系,下面进行具体阐述。
3.4.2.1 测量原理
在轮胎的钢丝层,钢丝是导电材料,橡胶为介电材料和电阻材料,临近的钢丝可以简化为图3.20所示的原理图。在图中,相邻的两条钢丝作为两个电极,钢丝之间为橡胶,橡胶为介电材料,可以等效为电容,同时橡胶内存在炭黑,炭黑为电阻材料,可以等效为电阻,因此,轮胎钢丝层相邻钢丝之间的部分可以等效为电容和电阻并联的电路结构。

图3.20 子午线轮胎钢丝层的电阻电容并联模型[19]
在图3.20中,电容C仍然可以用式(3.3)求解,电阻R求解如下[19]:

式中,ρ为橡胶的电阻率。
轮胎变形引起钢丝层的变化,由式(3.3)和式(3.6)可以看出,当钢丝层伸长时,两条钢丝之间距离d增大,电容C降低,电阻R增大;当钢丝层压缩时,两条钢丝之间的距离d减小,电容C增大,电阻R减小,因此,轮胎的变形引起电容和电阻的变化,根据电阻和电容变化可以获取轮胎应变量的大小。
由于电容和电阻不能直接测量,因此,需要将电容和电阻的变化转换为频率的变化。文献[19]利用电感线圈L和轮胎电阻R与电容C组成谐振电路,将电容和电阻变化转换为频率信号的变化,通过测量频率信号的频谱特征,获取电阻和电容变化的信息。系统测量的原理如图3.21所示,首先利用外部发射器发射白噪声频率信号,然后轮胎电容电阻阻抗和电感线圈组成的谐振电路通过天线接收白噪声频率信号,发生振荡,该振荡信号通过天线发射出去,外部的接收器通过天线接收振荡电路发射的信号。轮胎电容和电阻变化影响振荡信号的特征,根据接收信号的频谱特征分析,可以建立信号频谱与电容和电阻的联系,根据信号频谱与电容和电阻的联系以及电容和电阻与轮胎应变量的联系,可以利用接收信号的频谱得到轮胎的应变量变化信息。

图3.21 轮胎电容电阻阻抗传感器无源无线测量的原理图[19]
在图3.21所示的LRC并联谐振电路中,谐振电路电抗为:

在LRC谐振电路发生谐振时,电抗最小,即式(3.7)的虚部为零,从而可以求解得到谐振频率ft如下:

当电感线圈的电感L恒定时,利用谐振频率ft可以反映轮胎电容阻抗的变化。
当谐振发生时,谐振电抗Y0可以简化为:

在谐振时的峰值功率谱Pp可以表达为:

式中,I为LRC并联电路的总电流。由式(3.10)可以看出,轮胎电阻阻抗与谐振时的峰值功率谱有关,因此,利用峰值功率谱可以反映轮胎电阻阻抗的变化。
另外,振荡频率信号的特征还可以用品质因数描述,品质因数反映谐振频率的尖锐程度。对于LRC谐振电路,品质因数Q可以用下式表示:

利用品质因数Q可以同时反映轮胎电容和电阻阻抗的变化。
由式(3.8)可以看出,谐振频率反映轮胎电容阻抗的变化,由式(3.10)可以看出,峰值功率谱反映轮胎电阻阻抗的变化,由式(3.11)可以看出,品质因数反映轮胎电容和电阻阻抗的变化。另外,轮胎胎体的应变引起轮胎钢丝层相邻钢丝之间距离的变化,从而轮胎的电容和电阻阻抗发生变化,因此,通过谐振频率、峰值功率谱和品质因数可以反映轮胎应变量的变化。为了充分利用测量信号频率特征,更准确地获得轮胎的应变量变化信息,可以综合谐振频率ft、峰值功率谱Pp和品质因数Q信息,建立轮胎应变量y的表达式如下[19]:

式(3.12)的具体表达式可以通过实验测试的方法建立,根据建立的关系就可以利用轮胎电容电阻传感器测量轮胎应变量变化的大小。
3.4.2.2 测试结果
为了对理论分析的结果进行实验验证,将轮胎胎体部分的钢丝层的相邻钢丝作为电极,进行轮胎电容和电阻阻抗的测量,在加载和去载过程中,测量得到的轮胎电容和电阻变化如图3.22所示。

图3.22 加载和去载过程测量得到的轮胎电容和电阻阻抗随应变的变化关系[19]
由图3.22可以看出,当轮胎加载或去载引起变形后,轮胎的电容和电阻都发生相应的变化,并且加载和去载过程存在滞后,即在加载过程的轮胎应变和去载过程的轮胎应变引起的电容和电阻变化不同。
测量得到的电容和电阻的变化,可以通过LRC谐振电路转换为频率的变化。根据式(3.8)、式(3.10)和式(3.11)可以得到轮胎在加载和去载过程的谐振频率变化、峰值功率谱变化和品质因数的变化过程,如图3.23所示。由图可以看出,轮胎在加载和去载过程的变形引起的电容和电阻变化,可以通过谐振频率、峰值功率谱和品质因数的变化来反映,通过测量谐振频率的变化、峰值功率谱的变化或品质因数的变化,可以得到轮胎应变量的变化情况。
利用式(3.8)、式(3.10)和式(3.11)求解的结果为理想情况的变化,为了验证公式的正确性,下面进行具体的实验测试研究。

图3.23 通过式(3.8)、式(3.10)和式(3.11)计算得到的Δft/ft0、ΔPp/Pp0和ΔQ/Q0[19]
实验测试得到轮胎加载和去载过程引起的谐振频率变化曲线,如图3.24所示。

图3.24 轮胎加载和去载过程测量得到的谐振频率随应变量的变化关系[19]
由图可以看出,谐振频率的变化并不随着轮胎应变量的变化发生单调线性变化,因此,难以仅利用谐振频率的变化进行轮胎应变量的估计,需要结合其他信号频率特征进行轮胎应变量的估计。

图3.25 轮胎加载和去载过程测量得到的峰值功率谱随应变量的变化关系[19]
实验测试得到轮胎加载和去载过程引起的峰值功率谱变化曲线,如图3.25所示。
由图可以看出,无论加载过程还是去载过程,随着轮胎应变量的增加,峰值功率谱都单调增加,两者之间存在明显的线性关系。
实验测试得到轮胎加载和去载过程引起的品质因数变化曲线,如图3.26所示。

图3.26 轮胎加载和去载过程测量得到的谐振器品质因数随应变量的变化关系[19]
由图可以看出,无论加载过程还是去载过程,随着轮胎应变量的增加,品质因数基本单调增加,两者之间存在一定的线性关系。
由图3.24~图3.26可以看出,实验测试的结果与图3.23通过公式求解的结果基本一致,说明轮胎的应变量变化与谐振频率、峰值功率谱和品质因数之间存在密切的联系,通过实验测试建立它们之间的回归关系,从而可以利用轮胎电容电阻阻抗传感器进行轮胎应变量的测量。

图3.27 估计得到的轮胎应变量与测量得到的轮胎应变量比较[19]
图3.27给出了实验测试的应变量与轮胎电容电阻阻抗传感器得到的应变量的对照,从图中可以看出,两者具有很好的一致性,因此,利用轮胎电容电阻传感器进行轮胎应变量的测量方法是可行的,通过对轮胎应变量的测量可以获得轮胎的压力变化。
3.4.3 橡胶基电容阻抗传感器
对于轮胎电容阻抗传感器或电容电阻阻抗传感器,需要利用外部的调谐电路将阻抗变化转换为频率信号变化,从而实现测量信息的无线传输。轮胎阻抗是轮胎内部钢丝层相邻钢丝之间的阻抗,调谐电路需要与钢丝相连实现无线传输,因此,目前的轮胎制造过程需要改变,这将需要大量的投资和成本,影响比较大。另外,调谐电路的电子元件需要承受轮胎生产过程的高温等恶劣环境,对电子元件的性能要求将非常高,从而需要的成本也会随之增加,这将不利于这种传感器的推广应用。
此外,轮胎阻抗传感器利用轮胎的应变量的变化与轮胎电容和电阻阻抗变化之间的关系进行轮胎应力的测量,但是由于轮胎结构的复杂性使得加载与去载过程引起的变形路径不同,轮胎的黏弹性引起轮胎的变形与应力之间存在滞后,因此,实际测量的应力与电容和电阻阻抗变化之间存在一定的滞后,应力对应的电容或电阻阻抗变化不唯一,难以根据测量得到的电容或电阻阻抗变化获得准确的轮胎应力变化信息。
为了解决这些问题,文献[21]利用柔性环氧树脂材料作为基底制作电容传感器,粘贴在轮胎胎侧进行应力的测量。由于柔性环氧树脂材料与轮胎材料之间存在一定的差异,文献[22]采用性能更好的橡胶作为基底材料,通过光刻技术制作电容传感器,将传感器粘贴在轮胎胎侧部位,进行轮胎应力的测量。下面具体阐述橡胶基电容阻抗传感器的原理和实验测试结果。
3.4.3.1 测量原理
橡胶材料的弹性、刚度、泊松比、热膨胀系数以及其他力学参数都与轮胎材料相同,因此,利用橡胶作为基底材料,通过光刻技术可以制作如图3.28所示的电容阻抗传感器。

图3.28 橡胶基电容阻抗传感器原理解释[22]
这种传感器可以直接粘贴在轮胎胎侧进行轮胎应力的测量,并且,在测量过程中,传感器对轮胎的变形影响很小。轮胎的应力变化引起应变量的变化,轮胎应变量的变化可以转换为电容的变化,电容的变化很容易通过谐振电路转换为频率信号实现无线传输,下面主要分析应变量变化与电容变化之间的关系。
如图3.28所示,通过光刻技术制作的叉指电容可以获得更大的初始电容,从而可以更灵敏地测量轮胎应变量的变化。应变量的测量垂直于叉指电极的方向,它利用叉指之间的间隙距离的变化进行应变量的测量。传感器粘贴在轮胎胎侧表面上的区域,为叉指电容器的叉指电极所在的区域,侧面的电极不受应力的作用,因此,初始电容C0由初始叉指电容Cs0和寄生电容Cp组成,可以用下式表示[22]:

式中,p为介电常数;a为叉指电极的搭接长度;g为叉指之间的间隙;h为介电材料的厚度,n为叉指电极的对数。具体如图3.29所示。
当叉指电容器在纵向方向受到ε的拉伸应变作用时,叉指之间的距离变为g(1 +ε),假定泊松效应影响系数为υ,叉指电极的搭接长度变为a(1-υε),因此,在应变作用下的叉指电容器的实际电容可以表达为[22]:

由于寄生电容Cp在电极和连接线之间,一般为常数,与施加的应力大小无关,可以采用初始电容Cs0和比例α表示[22]:

图3.29 叉指电极的结构[22]

叉指电容器电容的变化率可以表示为[22]:

根据式(3.16),可以求解得到传感器的灵敏度GF,即电容变化率与应变的比例,如下式所示:

如果施加的应力ε≪1,灵敏度GF可以简化为:

由于寄生电容与初始电容的比例α与传感器的结构有关,为固定值,泊松效应对橡胶材料应变的影响系数υ与橡胶材料有关,因此,当传感器结构和材料确定之后,灵敏度GF为常数,可以用电容变化反映应变量的变化,从而,利用该橡胶基电容阻抗传感器可以实现轮胎应变量的测量。
灵敏度GF越大,测量精度就越高,因此,如何增加灵敏度就显得非常重要了。由式(3.18)可以看出,当寄生电容与初始电容的比例α越小,泊松效应影响系数υ越大时,灵敏度就越高。假定寄生电容与初始电容的比例α为0.6,GFRP(GlassFiberReinforced Plastic)材料的泊松效应影响系数υ为0.1,其灵敏度GF为-0.69,橡胶的泊松效应影响系数υ为0.47,其灵敏度GF为-0.92,因此,橡胶基底传感器的灵敏度更高[22]。
另外,由于橡胶的性能很容易受到温度的影响,因此,在进行电容测量的过程中,还需要考虑温度的补偿,从而减小温度对测量结果的影响。
3.4.3.2 测试结果
为了对理论分析的结果进行实验验证,通过光刻技术在橡胶基表面制作叉指电容器,设计橡胶基电容阻抗传感器,然后将传感器粘贴在轮胎胎侧表面,通过对轮胎加载和去载,测试轮胎应变量变化与传感器电容阻抗变化之间的关系。
实验测试的装置图如图3.30所示,传感器粘贴在轮胎的胎壁上,在轮胎表面施加载荷,通过LRC测量仪器进行电容变化的测量。

图3.30 对粘贴在子午线轮胎(175/70 R14)内表面的传感器的电容变化进行测量的装置[22]
测试轮胎在加载和去载过程橡胶基叉指电容器的变化如图3.31所示,由图可以看出,随着应变量的增加,叉指电极之间的距离增大,因此,电容减小。测试加载和去载过程的电容变化如图3.32所示。

图3.31 橡胶基电容阻抗传感器在应变从0%增加到13.3%时的变形照片[22]

图3.32 橡胶基电容阻抗传感器在加载和去载过程的电容变化率[22]
由图3.32可以看出,随着加载或去载过程的应变量增加,电容变化率逐渐下降,灵敏度GF为-3.95,另外,加载和去载过程的差别很小,电容变化与应变量变化之间存在线性变化关系,因此,橡胶基电容阻抗传感器可以测量轮胎应变量的变化。
3.4.4 轮胎阻抗传感器优缺点分析
通过对轮胎阻抗传感器的理论和实验测试结果的分析,可以看出,这种新型的传感器具有下面的优点。
(1)传感器的成本比较低
轮胎阻抗传感器制作过程非常简单,轮胎电容阻抗传感器和轮胎电容电阻阻抗传感器直接利用轮胎作为传感器,橡胶基电容阻抗传感器利用光刻技术在橡胶表面制作叉指电容器完成传感器的制作,这些过程都非常简单,需要的材料也非常便宜,因此,传感器的制作成本很低。
(2)传感器对轮胎应变影响很小
传感器的刚度与轮胎的刚度差别很小,在轮胎受到应力作用时,传感器可以直接感受轮胎应力的变化,不改变轮胎的刚度和变形,因此,传感器可以更准确地测量轮胎的应力和应变的变化。
(3)传感器对轮胎动态过程影响小
轮胎阻抗传感器通过轮胎阻抗和外接谐振器电路实现轮胎应力的测量,传感器的结构非常简单,利用集成技术可以将传感器做得很小,因此,传感器可以安装在胎面或嵌入在轮胎内,在轮胎旋转过程中,对轮胎动态过程的影响很小,并且,不容易在轮胎长期旋转过程中,造成传感器与轮胎橡胶的脱离。
但是,轮胎阻抗传感器需要进行专门的设计和制作,还存在下面的局限性。
(1)传感器需要电源供电
轮胎阻抗传感器需要通过振荡电路将阻抗变化转换为频率信号的变化,从而实现无线传输,但是,振荡电路需要供电电源,目前的轮胎阻抗传感器还没有考虑如何通过无源方式进行测量信号的传输。
(2)传感器应用过程复杂
轮胎电容阻抗传感器和轮胎电容电阻阻抗传感器利用轮胎钢丝层的相邻钢丝与橡胶组成传感器,这需要在轮胎生产过程中进行专门的设计与制作,需要改变轮胎的生产流程,需要得到轮胎生产厂商的协助与支持,涉及的过程比较复杂,另外,还需要考虑轮胎生产过程的高温环境对传感器的影响,因此,这种传感器实际应用过程会比较复杂。
(3)测量信号需要进行温度补偿
轮胎阻抗传感器测量的阻抗变化会受到温度变化的影响,特别是在轮胎旋转过程中,轮胎温度不断上升,测量的阻抗会发生变化。如果不进行温度补偿,难以正确测量轮胎的应力变化,但是,温度补偿电路增加了传感器设计的复杂性。