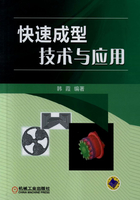
第四节 熔丝堆积(FDM)成型技术
熔丝堆积(Fused Deposition Modeling,FDM)成型技术也称为熔融沉积制造、熔融挤出成型技术。FDM技术是利用热塑性材料的热熔性、粘结性等特点,在计算机控制下,进行层层堆积叠加,最终形成所需产品或模型。FDM技术的最大特点是不依靠激光成型能源,而是将成型材料熔融后堆积成三维实体模型的工艺方法。该技术最初由美国Stratasys公司在20世纪90年代初首次推出,并在1999年开发出水溶性支撑材料,后被广泛应用于RP的各行业中。
由于FDM快速成型技术不使用激光,因此设备使用、维护都简单,成本也较低。用蜡成型的零件模型,可以直接用于熔模铸造。用ABS丝制造的模型因其具有较高强度,在产品设计、测试、评估等方面得到了应用。近年来,PPSF、PC、PC/ABS等强度较高的成型材料开发成功,使得该工艺可直接加工制造出功能性零件或产品。由于FDM技术具有以上这些显著优点,因此发展极为迅速,目前的FDM系统在全球快速成型系统中的份额占30%左右。
由于FDM技术用丝状材料,是依靠熔融状态下在工作空间中一层层堆积而成,因此在构建模型时也需要设计必要的支撑结构。Stratasys公司随机附有支撑结构的生成软件,而且现在能采用水溶性丝材作为支撑结构的材料,待模型制件加工制作完成后,只要经过简单的水洗处理,就能方便地剥离支撑结构,从而大大简化了FDM技术的后处理过程,并且大大提高了模型的表面精度和表面质量。图2-30所示为FDM Titan型快速成型机的外观和工作原理示意图。
图2-30 FDM Titan型快速成型机的外观和工作原理示意图
1—电动机 2—原材料 3—原型 4—工作台 5—支撑
6—喷嘴 7—原型制件 8—支撑结构 9—原丝材
一、FDM技术原理及系统组成
(一)FDM技术原理
FDM技术用材料一般为热塑性材料,如ABS、蜡、PC、尼龙等都以丝状供料。丝状的成型材料和支撑材料都由供丝机构送至各自相对应的喷丝头,然后在喷丝头中被加热至熔融状态;此时,加热喷头在计算机的控制下,按照事先设定的截面轮廓信息做X-Y平面运动;与此同时,经喷头挤出的熔体均匀地铺撒在每一层的截面上。此时喷头喷出的熔体迅速固化,并与上一层截面相粘结。每一个层片都是在上一层上进行堆积而成,同时上一层对当前层又起到定位和支撑的作用。
随着层的高度增加,层片轮廓面积和形状都会发生一些变化,当形状有较大的变化时,上层轮廓就不能给当前层提供足够的定位与支撑作用,这就需要设计一些辅助结构(即“支撑”结构),这些支撑结构能对后续层提供必要的定位和支撑,保证成型过程的顺利实现。这样,成型材料和支撑材料就被有选择性地铺覆在工作台上,快速冷却后就形成一层层截面轮廓。当一层成型完成后,工作台就会下降事先设定好的一截面层的高度,然后喷头再进行下一层的铺覆,如此循环,最终形成三维实体产品或模型。具体的FDM原理如图2-31所示。
图2-31 FDM原理示意图
a)FDM原理图 b)原型制件与支撑
1—喷头 2—原丝 3—喷头 4—成型工件
(二)FDM系统组成
以清华大学研制出的MEM-250为例,FDM系统主要由机械系统、软件系统、供料系统三部分组成。
1.机械系统 MEM-250机械系统由运动部分、喷头装置、成型室、材料室和控制室等单元组成。机械系统采用模块化设计,各个单元之间相互独立。例如,运动部分完成扫描和升降动作,整套设备的运动精度由运动单元的精度所决定,与其他单元无关。因此,每个单元可以根据自身功能的需求采用不同的设计。此外,运动部分和喷头装置的精度要求较高。
机械系统的关键部件是喷头装置,现以上海富力奇公司研制出的TSJ系列快速成型设备为例介绍喷头的结构。如图2-32所示,沿R方向旋转的同一步进电动机驱动喷头内的螺杆与送丝机构,当计算机发出指令后,电动机驱动螺杆的同时,又通过同步齿形带传动,送料辊将ABS丝等丝束送入成型头。在喷头装置中,丝束被电热棒加热呈熔融状态,并在螺杆的推动下通过铜质喷嘴挤出,按照计算机给定的模型轮廓路径铺覆在工作台上。
2.软件系统 FDM工艺软件系统包括信息处理和几何建模两部分。信息处理部分包括STL文件的处理、工艺处理、图形显示等模块,分别完成STL数据的检验与修复、层片文件的设置与生成、填充线的计算、对成型机的控制等工作。其中,工艺处理部分是根据STL数据文件,判断在产品的成型过程中是否需要设置支撑和进行支撑结构的设计以及对STL数据的分层处理,然后再根据每一层填充路径的设计与计算,以CLI格式输出,并产生分层CLI文件。
几何建模部分是由设计师使用三维CAD建模软件(如Pro-E、AutoCAD、SolidWorks等)构造出产品的三维数据模型,或利用三维扫描测量设备获取的产品的三维点云数据资料,重构出产品的三维数据模型,最后以STL文件的格式输出产品的数据模型。
3.供料系统 MEM-250制造系统要求FDM的成型材料及支撑材料为直径2mm的丝束,而且丝束具有较低的收缩率和一定的强度、硬度以及柔韧性。一般的塑料、蜡等热塑性材料都可以使用。目前研制较成功的丝束有蜡丝和ABS丝。
图2-32 TSJ系列快速成型系统喷头结构示意图
1—电动机 2—螺杆成型头 3—喷嘴
4—工作台 5—电热棒
6—送料辊 7—原丝材
8—齿形带传动 9—送丝机构
将ABS等丝束材料缠绕在供料辊上,电动机驱动辊子旋转,辊子和丝束之间的摩擦力能使丝束向喷头的出口送进。喷头的前端部位装有电阻丝加热器,在其作用下,丝束被加热和熔融,然后流经喷嘴后铺覆至工作台上,冷却后就形成一层层的轮廓界面。由于受到喷嘴结构较小的限制,加热器的功率不大,FDM所选用的丝束一般为熔融温度不太高的热塑性塑料或蜡。丝束熔融沉积的层厚随喷头的运动速度、喷嘴的直径而变化,通常铺覆的层厚为0.15~0.25mm。
FDM快速成型技术在制作模型制件的同时需要制作支撑结构。因此,为了节省材料成本和提高沉积的效率,可以设计出多个喷头。如图2-33所示,该FDM设备采用了双喷头装置,其中一个喷头用于制作模型制件,另一个喷头用于制作支撑材料。一般来说,用于制作模型制件的材料精细且成本较高,同时制作效率也较低;而用于制作支撑的材料较粗且成本较低,因此制作的效率也较高。双喷头的优点除了考虑到制作效率和成本以外,还可以灵活地、自己随意地进行选择一些特殊的支撑结构,以使得成型制件的外形更加完美。此外,还可以采用最近刚研制出的水溶性支撑材料,以便后处理过程中支撑材料可被简便、快捷地去除。
图2-33 FDM双喷头的工艺原理
1—喷嘴 2—原型制件 3—原丝材
二、FDM工艺过程
如图2-34所示,FDM的工艺过程大致可归纳成以下6步:
图2-34 FDM基本工艺过程
(1)读取产品的三维数据文件(目前常用的一般为∗.stl文件),并检查数据是否有问题,若有问题需修正数据。
(2)确定产品的成型区域、成型方向及摆放位置。
(3)设定成型参数,对产品的三维数据按确定的分层厚度进行分层处理,同时建立分层数据文件,目前一般为∗.cli文件。
(4)建立成型所需的支撑结构,同时检查支撑结构摆放的位置是否合理。
(5)生成加工路径,输出∗.cli等加工文件。
(6)自动成型加工。
如图2-35所示,以一按钮的快速制作过程为例,展示FDM具体的整个工艺过程。
图2-35 按钮FDM模型的加工制作过程
a)载入三维模型 b)模型的分层处理及支撑的设置 c)打印模型
d)喷头沿零件截面轮廓和填充轨迹运动 e)按钮FDM模型制件
三、FDM技术及模型制件精度的影响因素
(一)材料性能及影响因素
FDM材料的性能将直接影响模型的成型过程及成型精度。FDM材料在加工工艺过程中要经历固体—熔体—固体的两次相变过程,因此在冷却成固体的过程中,材料会发生收缩,产生应力变形,这将直接影响成型制件的精度。例如,ABS丝束在FDM的工艺过程中主要产生以下两种收缩:热收缩、分子取向的收缩。热收缩即材料固有的热膨胀率而产生的体积收缩,它是ABS丝束产生收缩的最主要原因。成型过程中,熔融状态下的ABS丝束在纵向上被拉长,又在冷却中产生收缩,而分子的取向作用会使ABS丝在纵向的收缩率大于横向的收缩率。
为了提高模型制件的成型精度,应减小FDM丝束的收缩率。目前有关单位正在研究通过改进材料的配方来实现较小的收缩率。在当前的数据处理软件中,可以采用在设计时就考虑收缩量,提前进行尺寸的补偿,即在X、Y、Z三个方向使用“收缩补偿因子”,针对不同的零件形状、结构特征,根据经验值来设定不同的“收缩补偿因子”(通过这种方法设计出的零件成型的实际尺寸稍大于CAD模型的尺寸);然后当其冷却成型时,模型制件的尺寸就会按照预定的收缩量收缩到CAD模型的实际尺寸。
(二)喷头温度的恰当设定及影响因素
喷头温度决定了FDM材料的丝材流量、挤出丝宽度、粘结性能及堆积性能等。若喷头温度太低,材料黏度就会加大,则丝束的挤出速度变慢;若丝束流动太慢,则有时会造成喷嘴堵塞,同时丝束的层与层之间的粘结强度也会相应降低,有时甚至还会引起层与层之间的相互剥离。
此外,若喷头温度太高,材料趋于液态,黏性系数变小,流动性增强,则可能会造成挤出速度过快,无法形成可精确控制的丝束,在加工制作时可能会出现前一层的材料还未冷却成型,后一层材料就铺覆在前一层的上面,使得前一层材料可能会出现坍塌现象。因此,喷头温度的设定非常重要,应根据每种丝束的性质在一定范围内进行恰当选择,以保证挤出的丝束呈正常的熔融流动状态。
(三)挤出速度的合理选择与影响因素
挤出速度是指喷头内熔融状态的丝束从喷嘴挤出时的速度。在单位时间内,挤出的丝束体积与挤出速度成正比。若挤出速度增大,挤出丝的截面宽度就会逐渐增加,当挤出速度增大到一定值时,挤出的丝束就会黏附于喷嘴外圆锥面,形成“挤出涨大”现象,而在此情况下就不能正常地进行FDM成型工艺的加工。
(四)分层厚度的合理选择
分层厚度是指模型在成型过程中每一层切片截面的厚度,由此也会造成模型成型后的实体表面出现台阶现象,这将直接影响成型后模型的尺寸精度、表面粗糙度。对FDM快速成型工艺,由于分层厚度的存在,就不可避免台阶现象。通常情况下,分层厚度的数值越小,模型表面产生的台阶的高度就越小,表面质量就越高,但所需的分层处理和成型时间就会相应延长,从而降低加工效率。反之,分层厚度的数值越大,模型表面产生的台阶的高度也就越大,表面质量就会越差,但加工效率相对较高。此外,为了提高模型制件的成型精度,可在模型制件加工完毕后进行一些后处理工序,如打磨、抛光等后处理。
(五)扫描方式的合理选择
FDM成型方法中的扫描方式有多种,如回转扫描、偏置扫描、螺旋扫描等。回转扫描指的是按X、Y轴方向进行扫描与回转,回转扫描的特点是路径生成简单,但轮廓精度较差。偏置扫描指的是按模型的轮廓形状逐层向内偏置进行扫描,偏置扫描的特点是成型的轮廓尺寸精度容易保证。螺旋扫描指的是扫描路径从模型的几何中心向外依次扩展。
通常情况下,可以采用复合扫描方式,即模型的外部轮廓用偏置扫描,模型的内部区域填充用回转扫描,这样既可以提高表面精度,又可以简化整个扫描过程,也提高了扫描的效率。
四、FDM成型工艺的应用举例
目前,FDM工艺与技术已被广泛地应用于航空航天、家电、通信、电子、汽车、医学、机械、建筑、玩具等领域的产品开发与设计过程,如产品外观的评估、方案的选择、装配的检查、功能的测试、用户看样订货、塑料件开模前校验设计、少量产品的制造等,传统方法需几个星期、甚至几个月才能制造出来的复杂产品原型,用FDM成型工艺,无需任何刀具和模具,几个小时或一至两天即可完成。
(一)日本丰田公司的具体应用
日本丰田公司借助FDM技术制作轿车部分零部件的模具或母模,如右侧镜支架和四个门把手的母模,使得2000 Avalon车型的制造成本显著降低,四个门把手的模具成本降低了30万美元,右侧镜支架模具成本降低了20万美元。
FDM在快速模具制作中用途相当广泛。最常用的方法是利用FDM制作出的快速原型来制造硅橡胶模具。例如,汽车电动窗和尾灯等的控制开关就可采用这种方法进行制造,或通过打磨过的FDM母模制得透明的氨基甲酸乙酯材料的尾灯玻璃,它与用铸造法或注射法制作的零件几乎没有任何差别。FDM工艺为整个新式2000 Avalon车型的改进设计制造所节约的资金超过200万美元。
(二)福特公司的应用
福特公司常年需要制造部件的衬板,以往每种衬板改型要花费千万美元和12周时间制作必需的模具。现在新衬板部件的蜡靠模采用FDM制作,制作周期仅3天。采用FDM工艺后,福特汽车公司大大缩短了衬板的制作周期,而且显著降低了制作成本。如今,仅花5周时间和原来一半的成本,所制作的模具每月可生产30000套衬板。
(三)美国快速成型制造公司的应用
美国Rapid Models与Prototypes公司采用FDM技术为一生产厂商制作了玩具水枪模型,如图2-36所示。借助FDM技术,通过将该玩具水枪多个零件一体制作模型,从而减少了传统制作模型的部件数量,同时也避免了焊接与螺纹连接等组装环节,大大缩短了该模型的制作时间。
图2-36 采用FDM技术制作玩具水枪
a)原型制件 b)产品的三维建模
(四)Mizunos公司的应用
1997年1月,Mizunos美国公司开发一套新的高尔夫球杆,若采用传统的方法,一般需要13个月左右的时间才能完成,可借助FDM成型工艺,新的高尔夫球杆整个开发周期在7个月内就全部完成了,缩短了40%的时间。其具体流程是,在设计出新高尔夫球头后,迅速按照反馈意见进行修改,因而加快了模型造型阶段的设计验证;最后以制造出的ABS原型制件作为加工的基准,再在CNC机床上进行钢制母模的加工与制作。显然,FDM成型工艺与相关技术已成为Mizunos美国公司在新产品研发过程中的重要组成部分。
(五)韩国现代汽车公司的应用
近几年,韩国现代汽车公司借助FDM快速成型系统进行检验设计、空气动力评估等功能测试,并在Spectra车型设计上得到了较为成功的应用。目前,现代汽车公司计划再安装第二套先进的FDM快速成型系统。图2-37所示为韩国现代汽车公司采用FDM技术制作的汽车仪表盘。
图2-37 韩国现代汽车公司采用FDM技术制作的汽车仪表盘
除了上述各大公司的具体应用外,FDM技术在其他领域的应用也是十分广泛的,尤其是在工业产品等方面的应用相当普及。图2-38~图2-42所示分别为采用FDM技术制作的彩色原型制件、龙图腾艺术品、健身球、侗族鞋及满族鞋等模型。
图2-38 FDM彩色原型制件
图2-39 FDM龙图腾艺术品
图2-40 FDM健身球
图2-41 FDM满族鞋
图2-42 FDM侗族鞋
五、FDM技术的特点及研究现状
(一)FDM技术具有的显著优点
1.成型材料广泛 FDM技术所用材料多种多样,主要有ABS、石蜡、人造橡胶、铸蜡和聚酯热塑性塑料等低熔点材料,以及低熔点金属、陶瓷等的丝材,可用于直接制作金属或其他材料的模型制件或用ABS塑料、蜡、尼龙等制造零部件。ABS塑料制件的翘曲变形小,采用石蜡制得的石蜡原型能直接制造精铸蜡模(可用于熔模铸造工艺生产金属件)。此外,原材料丝材基本上是以盘卷的形式提供,便于搬运和快速更换。
2.成本相对较低 由于FDM技术用熔融加热装置代替了激光器,因此与使用激光器的快速成型工艺方法相比,其制作费用大大减低。此外,原材料的利用率较高且无污染(成型过程中无化学反应),使得其成型成本大大降低。
3.后处理简单 支撑结构容易剥离,特别是模型制件的翘曲变形较小,原型经简单的支撑剥离后即可使用。目前出现的水溶性支撑材料使得支撑结构更易剥离。
此外,FDM技术还有以下优点:用石蜡成型的原型制件可以直接用于熔模铸造;能成型任意复杂外形曲面的模型制件,常常用于成型具有很复杂的内腔结构的零件;可直接制作出彩色的模型制件。ABS材料由于具有较好的化学稳定性,能采用γ射线进行消毒,因此特别适合用于制作医用模型。
(二)FDM技术存在的缺点
(1)只适合制作中、小型模型制件。
(2)成型件的表面有较明显的一层层条纹。
(3)纵向方向的强度比较弱。由于丝材是在熔融状态下一层层铺覆的,截面轮廓层之间的粘结力有限,因此原型制件的垂直方向的强度较弱。
(4)成型速度较慢。FDM工艺需设计、制作支撑结构,并且需对整个轮廓截面进行扫描和铺覆,因此成型时间较长。为尽量避免这一缺点,可采用双喷头同时铺覆或增加原型制件层厚等方法,来提高成型速度和成型效率。
(三)FDM的研究现状
材料性能的研究一直是FDM技术的主要研究重点。近年来研制出的PC、PC/ABS、PPSF等材料的强度已经接近或超过了普通注射件,能在某些特定场合进行试用、维修、暂时替换等。近年来,许多公司都在进行金属材料的研究工作,这也是当今快速原型领域的一个研究热点。
图2-43 气压式FDM系统示意图
1—压缩气体 2—压力控制管道 3—材料及加热装置 4—成型制件 5—工作台
目前,为了增加FDM所用材料的多样化和复合化,改进原有的容易出现问题且需经常更换的送丝机构,以及提高FDM的成型精度等,出现了气压式FDM工艺,其成型系统示意图如图2-43所示。它与传统的FDM工艺最大的不同点在于,其借助空气压缩机提供的压力将具有一定温度的低黏性材料(可以根据需要进行多种材料的组合)由喷头挤出,并逐层扫描堆积成型。此工艺与传统的FDM工艺相比,具有设备成本低、材料广泛且无污染等优点。但由于其喷嘴孔径较小,对材料的含杂质率有一定的要求,因此还有待于进一步改进与完善。
FDM技术与其他几种常见的快速成型技术的比较见表2-3。
表2-3 FDM技术与其他几种常见的快速成型技术的比较