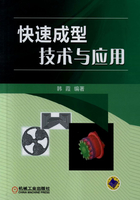
第一节 快速成型技术的分类
一、快速成型的基本原理及工艺技术
RP技术是一种基于离散和堆积原理的崭新的快速制造技术。它将零件的三维CAD实体模型按一定方式进行离散,将其转变成为可加工的离散面、离散线和离散点,然后采用多种物理或化学方式,将这些离散面、线段和点进行逐层堆积,最终形成零件的实体模型。它与从毛坯上去除多余材料的切削加工方法完全不同,也与借助模具锻造、冲压、铸造和注射等成型技术有异,是一种自由成型之逐层制造技术。
(一)自由成型之逐层制造
采用RP成型技术时,产品或模型的具体成型过程是:首先采用相关的计算机绘图软件设计出三维CAD模型,然后经过相关的格式转换,再对零件进行分层切片,得到各层截面的二维轮廓形状;再按照这些二维的轮廓形状,采用激光束选择性地固化一层一层的液态光敏树脂,或者切割一层一层的特制纸或金属薄材,或者烧结一层一层的粉末材料,或者用喷射源选择性地喷射一层一层的粘结剂或热熔性材料,以形成每一层呈二维的平面轮廓形状;最终再一层层叠加,形成三维实体产品或模型。
由此可见,RP技术的成型过程是属于“材料增长”的方法,即用事先设置好的一层一层“薄片毛坯”逐步叠加形成具有复杂外形的三维实体零件。由于它的制作原理是将复杂的三维实体分解成二维轮廓的逐层叠加,所以有时也称之为“叠层制造”技术。其成型的基本原理如图2-1所示。
图2-1 RP技术的基本原理
a)CAD模型 b)STL格式 c)分层切片 d)叠层过程
1—成型能源 2—升降台
(二)三维CAD模型之逐层制造
1.三维实体模型的近似处理 产品零件上往往有一些不规则的、复杂的自由曲面,在制作快速原型前必须对其进行一定的近似处理,才有可能获取比较准确的截面轮廓。在RP技术中,最常见的近似处理方法是用一系列的小三角形面片来逼近零件的自由曲面。其中,每一个三角形面片可以用三个顶点的坐标和一个法线矢量来描述,即STL格式文件。三角形的大小可以根据设计及用户需要进行设定,从而得到不同的曲面近似精度。目前大多数三维CAD软件都有输出STL文件的转换接口,若有时输出的三角形会有少量错误,则还需进行局部的编辑与修改。
2.三维实体模型的切片处理 RP的成型过程是按照截面轮廓来进行逐层加工的。加工前,须在三维实体上沿着成型的高度方向,每隔一定的间隔进行一次切片处理,以获取此层的截面轮廓。间隔的大小可根据待成型件的精度进行确定,间隔越小,精度越高,但成型时间也相应延长。目前间隔选取的范围一般为0.05~0.50mm,最常用的是0.1mm左右。在此取值下,能得到较光滑的成型曲面。各种RP快速成型系统都带有分层切片处理软件,能自动提取出三维CAD模型的截面轮廓。图2-2所示为对摩托车气缸盖的三维实体模型进行分层切片后得到的某一层截面轮廓。
3.截面轮廓的加工 在RP数控系统的控制下,快速成型设备中的激光头或喷头按照分层切片处理后的截面轮廓在二维平面内做轨迹运动,进行切割纸、固化液态树脂、烧结粉末材料或喷射粘结剂和热熔材料等,从而获得具有一定厚度的、一层层的截面轮廓。
图2-2 摩托车气缸盖的CAD模型及其某一层截面的轮廓
a)气缸盖 b)某一层截面的轮廓
4.截面轮廓的叠合 每层截面轮廓成型之后,RP设备就将下一层材料送至已成型的最后加工的一层轮廓表面上,再进行新一层截面轮廓的成型,并将一层层的截面轮廓逐步叠合在一起,最终形成三维的产品或模型。
(三)快速成型的前处理
1.三维CAD模型的几种表达方法
(1)构造型立体几何表达法。该方法采用布尔运算法则将一些简单的三维几何基元(如立方体、圆柱体、环、锥体等)加以组合,然后转化成复杂的三维实体。此方法的优点是易于控制存储的信息量,所得到的实体较真实有效,并且能方便地对其外形进行修改。此方法的缺点是,由于产生和修改实体的算法有限,因此构成图形的计算量很大,比较费时。
(2)边界表达法。该方法是根据顶点、边和面构成的表面来精确地描述三维实体的一种方法。此方法的优点是能快速地绘制出立体或线框模型。缺点是由于它的数据是以表格形式出现的,空间占用量大,修改设计不如构造型立体几何表达法简单,且所得到的实体不一定真实有效,有可能会出现错误的孔洞和部分特征颠倒现象,描述缺乏唯一性。
(3)参量表达法。对于一些产品模型的自由曲面难以用传统几何元素来进行描述的,可用参量表达法。该方法是借助参量化样条、贝塞尔曲线以及B样条来描述其自由曲面的。它的每一个X、Y、Z坐标都呈参量化形式。各种参量表达格式的差别在于对曲线的控制能力(即局部修改曲线而不影响临近特征的能力)以及建立几何体模型的能力,其中较好的一种为非有理B样条法(NURBS)。它既能表达出复杂的自由曲面,允许局部修改曲率,又能准确地描述几何特征。
(4)单元表达法。此方法来源于分析软件。在这些分析软件中,要求将三维实体表面离散成特定的单元形式。典型的单元形式有三角形、正方形或多边形等。在RP技术中采用的三角形近似,如将三维CAD实体模型转化成STL格式文件,就是一种单元表达法的应用形式。
2.RP技术中常用的文件格式
(1)STL(Stereo Lithography)格式。STL格式始于美国3D System公司生产的SLA快速成型系统,目前它已成为快速成型系统中最常见的一种文件格式。它是将曲面的三维CAD模型近似成一个个小三角形平面的组合,如图2-3所示。
图2-3 STL文件的三角形面片格式
a)曲面模型 b)小三角形面片组成的模型
一般情况下,STL文件有ASCII码和二进制码两种输出形式。二进制码输出形式所占用的文件空间比ASCII码输出形式的占用空间小得多,一般只是ASCII码的1/6。但是ASCII码输出形式的最大优点是可以阅读,并能进行直观地检查。
(2)IGES(International Graphics Exchange Standard)格式。IGES是目前大多数CAD系统采用的一种图形转换标准,可用于支持多种不同文件格式间的转化。
(3)HPGL(HP Graphics Language)格式。HPGL是美国惠普公司开发的用来控制自动绘图机的一种语言格式,目前它已被广泛地接受与应用。这种表达格式的基本组成结构是描述图形的矢量,用X和Y的坐标值来表示矢量的起点与终点以及绘图笔相应的抬起和放下等动作。现在一些与绘图原理有关的RP系统(如三维打印)就是采用HPGL来驱动喷头进行工作的。
(4)STEP(Standard for the Exchange of Product)格式。STEP是国际标准化组织提出的一种产品数据交换标准。目前,典型的CAD系统都可以输出STEP的格式文件。有些快速成型技术的研究人员正在研究借助STEP格式而不经过STL格式的转化,就可直接对三维实体模型进行分层和切片处理,从而有效地提高快速成型的精度。
(四)快速成型方向的选择
由于RP技术的基本原理是将复杂的三维实体分解成二维轮廓,然后再一层层地叠加,因此将各种格式的文件所表达出来的三维模型进行旋转,再进行切片可获得不同的模型成型方向。成型方向对工件的品质、材料消耗和模型的制作时间等方面都有很大的影响。
1.对工件品质的影响 一般情况下,大多数RP技术都较难控制Z轴方向界曝光功率及较大的穿透深度和较低的黏度等。功能测试型对成型材料成型后的强度、刚度、耐热性、耐蚀性等也有一定要求,若用于可装配测试,则对于材料成型的精度有更高的要求。模具型要求成型材料能适应具体模具制造的要求,如消失模铸造用原型材料要求材料成型后易于去除废弃的材料。RP技术常用的成型材料种类见表2-1。
表2-1 RP技术常用的成型材料种类
二、快速成型的基本工艺步骤
快速成型的过程一般都包含CAD模型的建立、前处理、原型制作和后处理四个步骤。其工艺流程如图2-4所示。
图2-4 RP的基本工艺流程
(一)产品三维CAD实体模型的创建
RP系统是由三维CAD数据模型直接驱动,因此首先要构建出产品的三维CAD数据模型。三维CAD数据模型可以利用计算机的三维辅助设计软件(Pro/E,I-DEAS,Solidworks,UG等)直接构建;也可以将已有产品的三维实体进行激光扫描、CT断层扫描等逆向工程的技术操作,以获取三维的点云数据,然后利用逆向工程的相关软件方法构造出产品的三维数据模型。目前,快速成型软件所接受的数据文件一般为STL格式,所以必须先对产品的三维数据模型进行近似处理,用一系列的小三角形平面去逼近原来的实体模型。目前一般的三维CAD软件都带有转换和输出STL格式文件的功能。
(二)快速成型的前处理
首先根据被加工模型的三维特征选择合适的成型方向,在模型的成型高度方向上用一系列一定且相同间隔的平面去切割模型,以便提取出截面的轮廓信息。间隔一般设定在0.05~0.5mm之间,目前最小分层厚度可达到0.016mm。间隔越小,模型的成型精度越高,但相应的模型的成型时间也越长,效率也越低;反之,则成型精度降低,但效率有所提高。
(三)快速加工与成型过程
在计算机控制下,根据切片处理的截面轮廓,相应的RP设备的成型头(激光头或喷头)就会按照各截面轮廓的信息做二维的扫描运动,在工作台上一层一层地进行材料的堆积工作,同时将各层进行粘结,最终得到三维产品或模型。
(四)模型制件的后处理
从RP系统里取出模型成型件,进行一些模型的后处理工作,如进行剥离、后固化、修补、打磨、抛光及涂挂等后处理工艺,其目的是降低产品或模型的表面粗糙度值,提高其强度。
三、快速成型设备的组成与分类
快速成型技术的基本原理是逐层叠加制造。快速成型设备是在X-Y平面内通过二维扫描形成原型制件的截面轮廓形状,而在Z坐标上做间断的层厚位移,最终形成三维的产品或模型。因此,目前一般的快速成型设备主要由扫描路径、RP运动机构、能源设备、材料供给和控制系统四大部分组成。
(一)扫描路径
扫描路径是指模型成型一个截面轮廓时的运动路径,共有两种路径:一种是栅格路径,由一系列连续的或者是间断的直线形成一个个轮廓截面;另一种路径是先沿截面轮廓线进行矢量运动,而后形成一圈圈截面外轮廓线,外轮廓线的内部可以用矢量路径或栅格路径加以填充。
这两种路径的主要差别在于模型成型的精度和速度。栅格路径是仅仅沿着一个坐标运动,所以其速度较快,由于其轮廓线是由三角形近似得到的,因此会产生离散误差。矢量路径则避免了这种误差,但需进行二维的插补,扫描速度较慢,其优点是轮廓精度较高。
(二)RP运动机构
RP运动机构是指得到三维几何实体制件的运动执行机构。常用的运动执行机构有两种:一种是X、Y、Z三个坐标轴的运动均由机械传动实现;另一种由电流偏转镜的转动形成原型件的二维轮廓截面,再由机械传动的垂直位移使轮廓截面相互叠加。
快速成型机的控制系统只有接受三维CAD实体模型后,才能进行数据格式转换和分层切片处理。因此,必须先在计算机上用CAD软件建立产品的三维实体模型;或将已有产品的二维工程图样转换成三维CAD数据模型;或采用逆向工程用扫描机对已有的零件实样进行扫描,得到三维CAD数据模型。然后再对三维CAD数据模型进行处理。
目前,根据快速成型设备的运动机构和成型的扫描路径特征,可将典型的快速成型设备分为以下几类,见表2-2。
表2-2 几种典型的快速成型设备
①MJM:Multi-Jet Molding(多喷嘴成型)。
四、快速成型技术的分类
RP技术结合了当代众多的高新技术内容,如计算机辅助设计与制造、数控加工技术、激光加工技术以及材料技术等,同时随着众多技术的不断更新而快速向前发展。RP技术自1986年出现至今,已经有三十多种不同的加工方法,而且许多新的加工与制造方法仍在继续涌现。
目前,按照RP技术使用的能源进行分类,可以将RP技术分为激光加工和非激光加工两大类。成型材料按照形态可以分为液态、薄材、丝材、金属和非金属粉末五种。其中,目前得到较为广泛应用的有以下五种快速成型技术:液态光敏树脂选择性固化(Stereo Lithography Apparatus,SLA)、薄型材料选择性切割(Lami-nated Object Manufacturing,LOM)、丝状材料选择性熔融堆积(Fused Deposition Modeling,FDM)、粉末材料选择性激光烧结(Selected Laser Sintering,SLS)、喷墨三维打印成型(Three Dimensions Printing,3DP)。
(一)按RP加工制造所使用的材料的状态、性能及特征分类
1.液态聚合与固化技术 原材料呈液态,利用光能、热能等使特殊的液态聚合物固化形成所需的形状。
2.烧结与粘结技术 原材料为固态粉末,通过激光烧结或用粘结剂把材料粉末粘结在一起,以形成所需形状。
3.丝材、线材熔化粘结技术 原材料为丝材或线材,通过升温熔融,并按指定的路线层层堆积出所需的三维实体。
4.板材层合技术 原材料是固态板材或膜,通过粘结将各片薄层板粘结在一起,或利用塑料膜的光聚合作用将各层膜片粘结起来。
(二)按RP加工制造原理分类
1.光固化成型(Stereo Lithography Apparatus,SLA)技术 以光敏树脂为原料,在计算机控制下,紫外激光束按各分层截面轮廓的轨迹进行逐点扫描,被扫描区内的树脂薄层产生光聚合反应后固化,形成制件的一个薄层截面。当一层固化完毕后,工作台向下移动一个层厚,在刚刚固化的树脂表面又铺上一层新的光敏树脂,以便进行循环扫描和固化。新固化后的一层牢固地粘结在前一层上,如此重复,层层堆积,最终形成整个产品原型。
2.分层实体制造(Laminated Object Manufacturing,LOM)技术 采用激光器和加热辊,按照二维分层模型所获得的数据,将单面涂有热熔胶的纸、塑料带、金属带等切割成产品模型的内外轮廓,同时加热含有热熔胶的纸等材料,使得刚刚切好的一层和下面的已切割层粘结在一起。如此循环,逐层反复地切割与粘合,最终叠加成整个产品原型。
3.熔融沉积制造(Fused Deposition Modeling,FDM)技术 采用热熔喷头装置,使得熔融状态的ABS丝按模型分层数据控制的路径从喷头挤出,并在指定的位置沉积和凝固成型,经过逐层沉积和凝固,最终形成整个产品原型。
4.选择性激光烧结(Selected Laser Sintering,SLS)技术 采用激光束,按照计算机输出的产品模型的分层轮廓及指定路径,在选择区域内扫描和熔融工作台上已均匀铺层的材料粉末,处于扫描区域内的粉末被激光束熔融后形成一层烧结层。逐层烧结后,再去掉多余的粉末即可获得产品模型。
5.三维打印(Three Dimensions Printing,3DP)技术 三维打印原理与喷墨打印机的原理近似,首先在工作仓中均匀地铺粉,再用喷头按指定路径将液态的粘结剂喷涂在粉层上的指定区域,待粘结剂固化后,除去多余的粉尘材料,即可得到所需的产品原型。此技术也可以直接逐层喷涂陶瓷或其他材料的粉浆,固化后得到所需的产品原型。