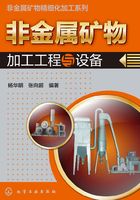
2.4.4 湿法超微细分级工艺设计与设备选型
湿法精细分级设备主要是卧式螺旋卸料沉降离心机和小直径水力旋流器组。
2.4.4.1 卧式螺旋卸料沉降离心机
卧式螺旋卸料沉降离心机生产能力可从两种途径进行计算,即按溢流或悬浮液计算和按沉渣(或沉淀物)计算。
(1)按溢流或悬浮液计算 如图2-49所示。

图2-49 螺旋卸料沉降离心机柱锥形转鼓结构参数
对于柱锥形转鼓,按∑理论有:
(2-6)
式中,Q为螺旋卸料沉降离心机按溢流或悬浮液计算的生产能力,m3/s;v0为临界直径粒子的重力沉降速度,m/s;w为转鼓回转角速度,s-1;r2为转鼓半径,m;g为重力加速度,m/s2;Fr为离心分离因素,Fr=w2r2/g;D为转鼓直径,D=2R2,m;π为圆周率;L为沉降区长度,m;λ为系数,λ=h/r2;A为随半径变化的沉降面积的修正面积,m2;∑为当量沉降面积,又称离心机的生产能力指数,m2。
对于柱锥形转鼓:
(2-7)
式中,L1为螺旋离心机柱形部分的长度;L2见图2-49。
但是,按∑理论计算的生产能力比实际的大,因此,在使用上述公式计算时要加以修正,即:
Q=ξv0∑ (2-8)
对于螺旋卸料沉降离心机,建议取:
(2-9)
式中,Δρ为固液相密度差,Δρ=ρ1-ρ2;ρ2为固相密度,kg/m3;ρ1为液相密度,kg/m3;de为粒子当量直径,m;L为沉降区长度,m。
对于高速螺旋沉降离心机,建议取:
ξ=1.06Re-0.074Fr0.178 (2-10)
式中,Re为雷诺数,Re=Q/(2h+b)ν;Fr为弗劳德数,;h为液层深度,m;b为螺旋流道宽度,m;ν为液体运动黏度,ν=u/ρ1,m2/s;rm为液层平均半径,rm=1/2(r1+r2),m;ω为转鼓回转角速度,s-1;
给料中,能被螺旋沉降离心机全部分离的最小粒子直接成为临界粒子直径dc,临界粒子直径dc按下式计算。
(2-11)
式中,k=Δρg/18μ;Δρ=ρ1-ρ2;g为重力加速度;μ为悬浮液黏度。
(2)按沉渣(或沉淀物)计算 设沉渣以条状沿螺旋叶面自大端被输向小端出渣口,沉渣条的截面形状及沉渣塔桥状况如图2-50所示。

图2-50 沉渣条的界面形状及沉渣搭桥状况
沉渣条沿螺旋叶面的滑动速度为:
(2-12)
螺旋的输渣能力G为:
(2-13)
式中,Ep为螺旋的输渣效率,Ep=tanδ1/(tanβ+tanδ1);Δω为螺旋与转鼓的角速度差,s-1;r为回转半径,m;s为螺旋螺距,m;A为沉渣条的截面积,m2;ns为螺旋的台数,台;γ0为湿渣的容重,kg/m3;δ1为沉渣沿鼓壁滑动方向与垂直于转鼓轴线的径向平面间的夹角,(°);β为螺旋叶片的升角,(°)。
根据沉渣的搭桥状况确定:当螺旋母线垂直于转鼓母线,即螺旋叶片母线与垂直于转鼓轴线的径向平面间的夹角β=α,沉渣有以下两种搭桥的可能性。
两螺旋叶片之间先搭桥:
(2-14)
式中,φ为沉渣条自由表面与转鼓轴线间的夹角,(°)。
转鼓与螺旋内筒之间先搭桥:
(2-15)
当螺旋母线垂直于转鼓轴线,即β=0°时[图2-50(b)],沉渣有以下两种搭桥的可能性。
两螺旋叶片之间搭桥:
(2-16)
转鼓与螺旋内筒之间先搭桥:
(2-17)
螺旋沉降离心机的技术参数包括以下几个。
①结构方面的参数 转鼓内直径D、转鼓总长度L、转鼓半锥角α、转鼓溢流口处直径D1、螺旋的螺距s或升角β、螺旋母线与垂直于转轴的截面的夹角θ。
②操作方面的参数 转鼓的转速n或角速度ω、转鼓与螺旋的转速差Δn。
选择与确定合理的技术参数是设计螺旋沉降离心机的首要任务。选择这些技术参数的依据是:悬浮液的特性(如固液相密度、固相浓度、粒度分布、液相黏度等)、处理量Q、分离效率Ex、沉渣产量G、渣含湿量W0、输渣功率N、输渣效率Ep、螺旋所受转矩M和轴向力F0、转鼓和螺旋的相对磨损程度T等。在诸多参数和因素中,必须首先解决参数的确定。
③主要参数D、L、n、F的选择 转鼓直径D的确定要考虑离心机系列型号的标准尺寸、单机生产能力和物料性质。转鼓直径是确定系列型号的主要尺寸数据。系列中转鼓直径的数值是从优先数系中,选取几何级数公比i=(2)1/3=1.26来确定的。在L/D一定的情况下,沉降离心机的生产能力大致与D3成比例,系列中的转鼓直径D按上述公比值来分级,说明逐级生产能力约提高一倍。国外螺旋沉降离心机系列中,一般最小型号为实验室用机型,D=160mm。据此,按公比i=1.26计算后,直径系列应为160mm、200mm、250mm、320mm、400mm、500mm、640mm、800mm、1000mm。考虑到小尺寸机型较多且尺寸相近,经合理调整后,我国所制定系列直径为200mm、350mm、450mm、600mm、800mm、1000mm。处理不同性质的物料时,单机生产能力的变化是很大的,表2-5仅供选择时做初步参考用,最后确定尚需做进一步的计算。在有条件的情况下,最好用相同物料进行试验,取得数据后再进行设计。转鼓直径的选择还要考虑物料性质,对于难分离或难分级的物料,分离因素要求较高时,限于转鼓材料强度,必须选用较小的直径。
表2-5 螺旋沉降离心机的生产能力范围

转鼓的长度L一般是按L/D值来确定的,对于易分离物料,L/D=1~2;对于难分离物料,L/D=3~4;制造较难,成本较高,目前较少采用。
选择转鼓转速n或分离因素Fr时应考虑生产能力、分离或分级要求、转鼓强度和功率消耗、转鼓的最高允许转速等。鼓壁所受的应力与转速或圆周线速度的二次方成比例。对于一定的材料而言,允许的最大圆周线速度有一定的限度,例如一般常用的1Cr18Ni9Ti不锈钢,允许的最大圆周线速度为70~75m/s,这种材料制成的各种转鼓直径的最大允许转速和最大分离因素见表2-6。如需提高分离因素时,应采用较高强度的材料。
表2-6 各种转鼓直径的最大允许转速和最大分离因素

分离因素的大小主要取决于料浆中固相粒子的分离难易程度。对于密度小、粒度细的难分离物料,即粒子的重力沉降速度小的物料,一般选用较高的分离因素。工业用螺旋沉降离心机宜用于分离固相粒子的重力沉降速度v0≥1×10-6m/s的悬浮液或料浆。表2-7可供选择时参考。
表2-7 分离因素的选择范围

此外,功率消耗随分离因素的提高而增大,同时也增大了转鼓和螺旋的磨损程度,对其寿命及操作成本均不利,因此在满足生产量和分离要求的前提下,尽量采用低的分离因素。对于难分离的物料,当处理量较大时,一般选用小直径(D≤600mm)、高分离因素(Fr≥3000)的机型。根据处理量选择机型时,还必须考虑选用的台数。
④沉降区参数的选择 沉降区参数包括沉降区长度LQ、液层深度h、转鼓半锥角α、转鼓与螺旋的转速差Δn。这些参数对离心机的悬浮液或料浆处理能力和分离效率是有影响的。
螺旋沉降离心机的转鼓绝大多数是锥状和柱锥状的。当转鼓直径D、总长度L及出渣口直径D3一定时,沉降区长度受液层深度h(或k0值)和a值变化的影响,如图2-51所示,当L、r2、r3不变,将实线所示的a、h改为虚线所示尺寸时,可看出沉降区长度的变化是很大的。因而h值(即k0值)和α角值的选择对悬浮液或料浆的处理能力有影响。现在按其理论公式来分析。

图2-51 a、h值对沉降区长度的影响
柱锥状转鼓生产能力的计算式见式(2-18)。
(2-18)
式中,L1为柱筒段沉降区长度,m;L2为锥筒段沉降区长度,m,如图2-51所示,其余符号同前。
当转鼓直径D(D=2r2)、总长度L、锥段小端出渣口D3(D=2r3)一定时,L1和L2受α和k0值得影响。从图2-52可知:
(2-19)

图2-52 柱锥状转鼓k6值与α、k0的关系
其中,k3=r3/r2,一般常用值k3=0.6~0.7。
(2-20)
将式(2-19)和式(2-20)代入式(2-18),并取k3=0.65,而λ=1-k0,于是可得:
(2-21)
其中:
(2-22)
当L、D、D3一定时,Q随α和k0变化的情况如图2-52所示。
图2-52中k6值是按L/D=2计算的。从图2-52中可看出:α=6°,即半锥角较小时,锥筒段沉降区长度L2相对较长,锥段的影响较突出,故k6值随k0值的增大而减小;α值超过10°以后,柱筒段影响较突出,k6值随k0值的增加而增大。一般工业用沉降离心机的k6值在0.7~0.9范围内选取。α值的选取还要考虑脱水区的一些影响因素。
⑤有关脱水区参数的选择 与脱水区操作状态有关的参数是α、β(或螺距s)、θ、LG、Δn。这些参数与螺旋转矩M、轴向力F0、输渣效率Ep、渣停留时间t、转鼓与螺旋的相对磨损程度T等的关系分述如下。
一般工业用螺旋沉降离心机,除特殊情况外,绝大多数机型均选用螺旋叶片母线垂直于转鼓母线,即θ=α的结构。因此,以下讨论内容,除注明外,均属θ=α的结构。
转矩M和功率N的计算式为:
(2-23)
(2-24)
KM=f1cosδ1(cotδ1+cotβ)(2-25)
式中,Frm为脱水区的平均分离因素,Frm=ω2rm/g,r=1/2(r1+r3);LG为脱水区的轴向长度,m;G为湿沉渣生产能力,kg/s;Δω为转鼓与螺旋的角速度差,s-1;β为螺旋叶片的升角,(°);δ1为沉渣沿鼓壁滑动方向与垂直于转鼓轴线的径向平面间的夹角,(°);f1为沉渣与鼓壁和螺旋叶面之间的摩擦系数。
从式(2-23)~式(2-25)可看出M与Δω成反比,N与Δω无关。在G、ω、LG一定的情况下,KM值的大小确定了功率消耗的大小,KM值随f1值的增大而增大,f1值的升高可使输渣功率成倍增加。
当转鼓的总长度L已确定不变时,则脱水区长度LG将随α和k0而变化,转矩M和输渣功率N也将随之变动。计算输渣功率的式(2-24)中除KM外,Frm和LG也随α和k0而变。
(2-26)
式中,;k0=r1/r2;k3=r3/r2,一般常用值k3=0.6~0.7;α为转鼓锥筒段的半锥角,(°)。
当θ=α时,F0的计算式为:
(2-27)
式中,KF=cosαcosβ[f1sin(δ1+β)+tanαcosβ](cotδ1+cotβ)。
当转鼓总长度L一定时,脱水区长度LG将随α和k0而变,F0也随之改变。此时,F0的计算式改为:
(2-28)
式中,Fr=ω2r2/g;;k1=r1/r2;k3=r3/r2,一般取k3=0.65。
磨损性按下式估计:
T=KTGFrmLG (2-29)
对于转鼓:
(2-30)
对于螺旋:
(2-31)
上式只用来估计相对磨损性,并非计算磨损的绝对值。转鼓与螺旋的磨损程度,主要取决于物料性质及转鼓与螺旋所用的材料。但对于同样的物料和材料,如参数选择得当,可相对减轻一些磨损,提高使用寿命。在处理量G、分离因素Frm和脱水区长度LG一定时,可用KT值的大小来评价相对磨损性。一般工业离心机在常用的β值范围内,螺旋的磨损程度较转鼓严重得多。
沉渣输送效率EP与沉渣滑动方向角δ1值的大小有关,而δ1与f1、f2、α、β有关。输渣效率EP为:
(2-32)
在θ=α、δ1=0°的情况下:
(2-33)
式中,λ1、λ2分别为沉渣与鼓壁和螺旋叶片之间的摩擦角,λ1=tan-1f1,λ2=tan-1f2。
EP和δ1随α、β值的增大而下降,沉渣与鼓壁的摩擦系数f1值减小时,EP和δ1明显下降,沉渣输送条件很快恶化,当f1=0.1、f2=0.3、β=13°时,会出现EP=0而停止输渣的现象。对于细滑物料,如高岭土等黏土矿物,为了保证输渣顺畅,最好选取较小的α和β值。一般情况下,为保证正常操作,EP值的选择不宜低于85%,δ1值至少要大于45°,最好能达到EP>90%,δ1>55°,如采用较大的α角时,必须选用较小的β值,但β值小于4°时,螺旋受力和磨损情况将恶化。因此,在设计时应根据具体情况而定。
停留时间的计算公式如下。
(2-34)
其中
(2-35)
式中,Δω为螺旋与转鼓的角速度差,Δω=(π/30)Δn;Δn为螺旋与转鼓的转速差,r/min。
当转鼓的D和L确定后,t值取决于δ1、α、β和k0,而δ1又与f1、f2和β有关。为了便于分析,将上式改写为:
(2-36)
tΔn值随α、β值的增加和k0值的下降而减小。为保证有一定的停留时间,Δn必须随α、β值和液层深度h值的增大而减小。沉渣脱水所需时间,一般不宜少于5s,最好能达到8s,但Δn值太小时,螺旋转矩M值将增大,差速器负荷增加,工作条件将恶化。
综上所述,影响技术参数选择的因素较多,各个因素对参数的要求有许多是互相矛盾的,见表2-8。在选择各参数时,必须抓住具体任务中的主要矛盾。
表2-8 各种因素对参数的要求

2.4.4.2 水力旋流器
用于超细粉体精细分级的水力旋流器一般是直径小于75mm、锥角≤10°的小直径和小锥角水力旋流器。水力旋流器的结构参数与工艺参数之间相互影响,关系密切,现在虽有多种计算公式,但均是在不同的结构参数及工艺条件下使用的经验公式,使用时有程度不同的误差。
(1)水力旋流器处理量的计算 按给料体积计算水力旋流器处理量的经验公式为:
(2-37)
(2-38)
(2-39)
(2-40)
p0=p+0.04Hpρa (2-41)
式中,V为按给料体积计算的水力旋流器处理量,m3/h;ka为水力旋流器的圆锥角修正系数;α为水力旋流器的圆锥角,(°);KD为水力旋流器的直径修正系数;D为水力旋流器的直径,cm;dn为给料口当量直径,cm;b为给料口宽度,cm;h为给料口高度,cm;dc为溢流口直径,cm;p0为入口处料浆的工作计示压力,MPa;对于直径大于50cm的水力旋流器,入口处料浆的工作计示压力应考虑水力旋流器的高度;p为水力旋流器入口处料浆的工作计示压力,MPa;Hp为水力旋流器的高度,m;ρa为料浆密度,t/m3。
(2)水力旋流器分离粒度的计算 水力旋流器的分离粒度有不同的定义,因而分离粒度的计算就有各种不同的方法,使用较多的计算方法是按溢流中d97粒度或最大粒度计算的分离粒度,或按d50粒度计算的分离粒度。
①按溢流中d97计算的分离粒度其计算式如下。
(2-42)
式中,D为水力旋流器的直径,cm;βu为给料中固体含量,%;D0为沉砂口直径,cm;ρ、ρ0为料浆中固体物料和水的密度,t/m3;dc、p0、kD同前。
②按d50粒度计算的分离粒度 在浆料给入水力旋流器内进行分级的过程中,必有某粒级物料对进入沉砂和溢流具有相同的可能性,即该粒级物料进入沉砂和溢流的概率或回收率(占给料中该粒级物料质量分数)均为50%。因此,定义在水力旋流器分级过程中物料进入沉砂和溢流具有相同的可能性的某粒级d50粒级。
克雷布斯(Krebs)公司用标准水力旋流器试验求d50(c)(校正d50粒度),其计算式如下。
(2-43)
式中,d50(c)为校正d50粒度,μm;D为水力旋流器的内径,cm;cV为水力旋流器给矿体积浓度,%;p为水力旋流器的给矿压力,kPa;ρ为物料密度,t/m3。
在研磨分级回路中旋流器的溢流粒度均用某一特定粒度dT的百分含量表示,其与d50(c)之间的关系见表2-9。
表2-9 水力旋流器溢流粒度dT与d50(c)之间的关系

(3)水力旋流器沉砂口直径的计算 沉砂口直径的计算式为:
(2-44)
式中,D0为旋流器沉砂口直径,cm;ρ为物料密度,t/m3;cW为沉砂质量浓度,%;U为沉砂量,t/h。
(4)水力旋流器台数的计算 计算步骤如下。
①根据分离粒度用式(2-39)计算水力旋流器直径D并查出dc、dn、a等参数。
②用式(2-37)计算水力旋流器的处理能力V。
③计算所需台数n。
(2-45)
式中,n为所需水力旋流器的台数,台;Vn为设计处理浆料量,m3/h;V为该水力旋流器的单台处理能力,m3/h。