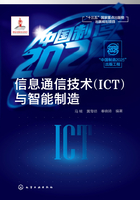
1.3.3 智能制造面临的挑战
随着智能制造系统的逐渐发展和应用,其所面临的挑战也应运而生,主要体现在以下几方面。
(1)异构异质系统的融合
智能制造系统利用信息物理系统(CPS)实现价值链水平集成化和网络化。当前存在的问题是传统工业自动化系统中不同技术的发展相对分散,虽然某些既定标准已被用于各种技术学科、专业协会和工作组,但是这些标准之间缺乏协调。目前,不同工业互联网络之间存在着严重的异构问题,导致资源难以得到有效利用。异构性是指不同类型网络之间的(如互联网、传感器网络、RFID、工业以太网等)高质量互联互通问题。异质性是指不同公司生产的硬件设备与不同功能之间互不兼容的问题。这需要从传感器、数据卡开始,从数据采集点到整个网络、云平台、数据中心、全连接,统一架构以及标准化接口。这需要一套新的国际技术标准来实现大规模嵌入式设备之间的互连并连接到虚拟世界。
解决异构异质系统融合的关键在于标准化的形成。这需要从不同层面积极推动智能制造的各国政府、不同领域的产业技术创新组织、跨国公司和广泛的中小企业共同参与,将已有的标准(如在自动化领域的工业通信、工程、建模、IT安全、设备集成和数字化工厂等的标准)纳入全新的全球参考体系中。这项工作具有高度的复杂性,是智能制造发展面临的一大挑战。
(2)复杂大系统管理
在现代管理中,为了降低管理的成本或开销,我们通常可以建立模型来模拟解决实际存在的或者假想的管理问题。比如产品、制造资源或整个制造系统,又如不同企业和组织之间的业务流程等管理方面的问题。
在智能制造时代,基于模型模拟使用标准的方式来配置和优化生产资源和制造工艺对于企业是一个重大挑战。主要原因在于智能制造系统变得越来越复杂,由于功能增加、产品用户特定需求多样化、交付要求频繁变化、不同技术学科和组织的交叉融合,以及不同公司之间合作形式变化迅速,很难开发一套稳定且具有极强适应性的管理模型。另外,开发新的管理系统模型的成本也较高。智能制造系统在建立初期阶段就需要建立明确的管理模型,这一阶段需要较高的资金支出。在高产量行业(如汽车行业)或有严格安全标准的行业(如航空电子行业),公司更有可能接受较高的初期投入。
(3)高质量高容量网络基础设施
由于智能制造系统对于数据传输的时延、数据交互的可靠性、服务质量的多样化都有着极高的要求,因此大容量、可扩展、低时延的高质量数据交换网络技术与基础设施是实现智能制造的基础。随着制造业信息化程度越来越高,工业生产相关的数据正呈现出爆发式的增长态势。各种设备和仪器产生的海量数据也增加了对信息处理的要求。高运行可靠性、数据链路可用性以及时延保证和稳定连接是智能制造的关键,因为它们直接影响应用程序的性能。
高质量高容量网络技术开发和基础设施建设是智能制造面临的又一个挑战。这种挑战主要表现在几个方面:一是工业领域宽带的基础架构过去并不是面向大数据的,大量机器与机器、设备与设备等数据的收集、传输、交互等,对工业领域宽带基础架构提出了更大的挑战。二是要实现基于数据驱动的端到端全生命周期,需要更大范围、更大维度的信息交流,对于异构异质网络的信息交流是一大挑战。三是网络的复杂性和成本控制的挑战。智能制造网络不仅需要高速、带宽、简单、可扩展、安全,还需要低成本,不明显增加现有制造产品和服务的开销。网络需要绑定可靠的SLA(服务水平协议);支持数据链路调试/跟踪,尤其是提供相关的技术援助;提供广泛可用/有保证的通信容量(固定/可靠的带宽);广泛使用的嵌入式SIM卡;所有移动网络运营商之间的短信传递状态通知;标准化的应用程序编程接口(APIs)的配置,涵盖所有供应商(SIM卡激活/停用);移动服务合约的成本控制;负担得起的数据全球漫游通信费用等。
(4)数据传递通道与实时交互
多节点交互、监控和控制,以及跨行业、跨域、跨产品和其他多场景需求,需要建立新的、系统的、统一的协议标准。除了整体架构和基本物联网外,至少同行业(领域)开始细化并建立统一的标准。此外,当前的网络资源显然不能支持智能制造的实际要求,无论是来自带宽(实时数据容量)、时延还是网络速度等要求。将智能制造和未来5G网络结合,是解决这一问题的前景方向。
(5)数据模型的多场景创建与打通
未来,智能制造系统中涉及的数据采集、存储、分配,模型设计,规则创建与利用等各环节,都与连接、控制和自动化密切相关。这意味着生产制造过程中将产生大量的数据,而如何利用好数据进行多场景的建模与仿真是实现智能制造的基础。因此,不同场景、不同模式下的数据模型建立与打通是智能制造面临的一大挑战。
(6)系统安全
智能制造系统涉及高度网络化的系统结构,涉及大量人员、IT系统、自动化组件和机器信息等元素。这意味着更多的人参与了整个价值链。开放性的网络环境和潜在的第三方访问意味着智能制造系统将面临一系列新的安全问题。因此在智能制造中,必须考虑到信息安全措施(加密程序或认证程序)对生产安全性的影响(时间关键功能、资源可用性)。
智能制造安全性的挑战主要表现在两个方面。首先,现有的工厂需要升级网络安保技术和措施,以满足新安全需求的挑战。但是,传统的机械装备寿命较长,原有的很多设备并不具备可靠的网络连接功能,升级改造非常困难。同时,企业内部生产系统与某些外部的陈旧基础设施很难联网,安全性的保障也很困难。其次,要为新的工厂和机器制定解决方案的挑战。企业界目前缺乏完全标准化的操作平台,以实施足够的安保解决方案。满足信息物理系统(CPS)安全的技术和标准化平台开发本身也充满挑战。