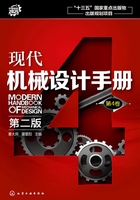
第4章 液力偶合器
4.1 液力偶合器的工作原理
液力偶合器是一种应用面很广的通用传动元件。它置于动力机与工作机之间传递动力,其作用有似于离心式水泵与水轮机的组合。虽然它连接在动力机与工作机两轴之间,但与联轴器明显不同,它所具有的改善启动性能、过载保护、无级调速等方面液力偶合器的特性,是各类联轴器所不具备的。
典型的液力偶合器结构(图19-4-1)由对称布置的泵轮、涡轮、输入轴、输出轴、外壳以及安全保护装置等构成。外壳与泵轮固定连接,其作用是防止工作液体外溢。输入轴(与泵轮固定连接)与输出轴(与涡轮固定连接)分别与动力机和工作机相连接。泵轮与涡轮均为具有径向平面直叶片的叶轮,由泵轮和涡轮具有叶片的凹腔部分所形成的圆球状空腔称为工作腔,供工作液体在其中循环流动,传递动力进行工作。工作腔(亦称循环圆)的最大直径称为有效直径,是液力偶合器的特征尺寸——规格大小的标志尺寸。

图19-4-1 液力偶合器结构示意
1—输入轴;2—输出轴;3—转动外壳;4—叶片;B—泵轮;T—涡轮
在液力偶合器被动力机带动旋转时,填充在液力偶合器工作腔内的工作液体,受泵轮的搅动,既随泵轮做圆周(牵连)运动,同时又对泵轮做相对运动。液体质点相对于叶轮的运动状态由叶轮和叶片形状决定。由于叶片为径向平面直叶片,按照叶片数目无穷多、厚度无限薄的假设,液体质点只能沿着叶片表面与工作腔外环表面所构成的流道内流动。由于旋转的离心力作用,液体质点从泵轮半径较小的流道进口处被加速并被抛向半径较大的流道出口处,从而液体质点的动量矩(mvuR)增大,即泵轮从动力机吸收机械能(力矩T和转速n)并转化成液体能 。在泵轮出口处液流以较高的速度和压强冲向涡轮叶片,并沿着叶片表面与工作腔外环所构成的流道做向心流动。液流对涡轮叶片的冲击减低了自身速度和压强,使液体质点的动量矩降低,释放的液体能推动涡轮(即工作机)旋转做功(涡轮将液体能转化成机械能)。当液流的液体能释放减少后,由涡轮流出而进入泵轮,再开始下一个能量转化的循环流动,如此周而复始不断循环。
在能量转化的过程中,必然伴随能量损耗,造成液体发热,同时使涡轮转速nT低于泵轮转速nB,形成必然存在的转速差(nB-nT)。
在液力偶合器运转过程中,由于泵轮转速始终高于涡轮转速,泵轮出口处压强高于涡轮进口处压强,因而液流能冲入涡轮进行循环流动,且使涡轮与泵轮同方向运转。
泵轮与涡轮转速差越大,则上述压差也越大,由于循环流量(单位时间内流过循环流道某一过流断面的液体的体积)与此压差平方根成正比,因此循环流量也越大(即循环流速增高)。当涡轮转速为零而泵轮转速不等于零时,循环流量最大,叶轮力矩也最大,此时为零速工况。当涡轮与泵轮转速相等时,压差为零,液流停止流动,循环流量为零,此时叶轮力矩等于零,为零矩工况。
液流与叶轮相互作用的力矩遵循如下的力矩方程,即
(19-4-1)
式中 Q——工作腔内液体的循环流量,m3/s;
R1,R2——叶轮液流进、出口半径,m;
vu1,vu2——叶轮进、出口处液流绝对速度的圆周分速度,m/s;
ρ——工作液体密度,kg/m3。
从式(19-4-1)中可见,叶轮力矩T取决于Q、vu、R等参数,而Q、vu、R又取决于泵轮转速、转速差和工作腔充液量。故液力偶合器传递力矩(或功率)的能力与泵轮转速和泵轮与涡轮的转速差(或转速比)大小有关,同时也与工作腔充液量大小有关,在相同情况下工作腔充液量越大,其传递力矩(或转速)的能力也越大,反之亦然。因而调节工作腔充液量(充满度),就可改变其传输力矩和转速。从这一特性出发,采用不同的结构措施,即可构成不同类型的液力偶合器。例如设置辅助腔(用来调节工作腔充满度的空腔),在液力偶合器力矩过载时靠液流的动压或静压使工作腔中工作液体自动地倾泻入辅助腔,减少工作腔充满度,限制输出力矩的提高,从而构成限矩型液力偶合器。在工作腔以外设置导管(导流管,亦称勺管)和导管腔(供导管导出工作液体的辅助腔),依靠调节装置改变导管开度(导管口端部与旋转外壳间距的百分率值)来人为地改变工作腔中的充满度(或充液量),从而实现对输出转速的调节,按此原理构成了调速型液力偶合器。
充液量的相对值以充液率(qc)表示
(19-4-2)
式中 q0——液力偶合器腔体总容积;
q——腔体中实际充液体积。
充液率直接影响液力偶合器的工作特性,它是液力偶合器应用中的重要参数。
对于限矩型液力偶合器,工作腔的瞬时充满度随载荷而自动变化。对于调速型液力偶合器工作腔充满度与导管开度之间有对应关系,需外部加以调控。由于调速型液力偶合器工作腔充满度在运行中难以测定,通常以导管开度(0%~100%)来代表工作腔充满度(或充液率)。
各类液力偶合器工作液体均为6号或8号(原YLA-N32或YLA-N46)液力传动油以及HU-20汽轮机油,见表19-1-7。水介质液力偶合器应用清水或水基难燃液,见表19-1-8。
4.2 液力偶合器特性
4.2.1 液力偶合器的特性参数
表19-4-1 液力偶合器的特性参数

4.2.2 液力偶合器特性曲线
表19-4-2 液力偶合器特性曲线


4.2.3 影响液力偶合器特性的主要因素
表19-4-3 影响液力偶合器特性的主要因素



4.3 液力偶合器分类、结构及发展
4.3.1 液力偶合器形式和基本参数(GB/T 5837—2008)
4.3.1.1 形式和类别
(1)形式

(2)类别




可同步液力偶合器和液力变矩偶合器不分类。
(3)型号

表19-4-4 液力偶合器形式与代号

表19-4-5 普通型液力偶合器类别与代号

表19-4-6 限矩型液力偶合器类别与代号

注:按传动结构特征分类、按工作腔数量分类、按安装形式分类必须在型号中表示,其他为可选项,根据需要表示。
表19-4-7 调速型液力偶合器类别与代号

表19-4-8 液力偶合器传动装置类别与代号

表19-4-9 液力减速器类别与代号

(4)标记示例
①循环圆有效直径560mm、复合泄液式、带制动轮的水介质限矩型液力偶合器,表示为:
液力偶合器 YOXFZ560S GB/T 5837
②循环圆有效直径560mm、出口调节式、伸缩导管调节式、水平剖分式、泵轮最高转速为3000r/min的调速液力偶合器,表示为:
液力偶合器 YOTCP560/3000 GB/T 5837
③循环圆有效直径560mm、前置齿轮式、增速型液力偶合器传动装置,表示为:
液力偶合器传动装置 YOCQZ560 GB/T 5837
4.3.1.2 基本参数
1)循环圆有效直径
2)基本性能参数 在雷诺数Re≥5×106条件下,液力偶合器的基本性能参数应符合表19-4-11与表19-4-12的规定。
表19-4-10 液力偶合器循环圆有效直径系列 mm

注:括弧中数值不推荐选用。
表19-4-11 普通型与限矩型液力偶合器的基本性能参数

注:1. qv为充液率,液力元件的工作液体体积与腔体容积之比。
2.液力偶合器使用介质为油介质。
表19-4-12 其他几种液力偶合器的基本性能参数

注:液力偶合器使用介质为油介质。
4.3.2 液力偶合器部分充液时的特性
普通型与限矩型液力偶合器均需在投运前充入与传递功率相应量的工作液体,故国外称此两类为常充型(constant filling)液力偶合器。按传递功率值,充液率可在40%~80%范围内选定。这是由于充液率小于40%时未发挥出其传递功率能力而不经济;而充液率大于80%时,则因工作腔内缺乏供液流流态变化的足够空间而影响液力偶合器特性。如果腔内全充满液体,则不但特性变坏,更因液体受热膨胀会引起密封失效或液力偶合器壳体爆裂。试验表明,在部分充液情况下,运转在不同工况会出现两种基本流动形式,即小环流和大环流。
小环流如图19-4-2(a)所示,在转速差较小(高转速比工况)时,液体在工作腔内循环流动速度较低,在涡轮内做向心运动的液体在涡轮旋转离心力作用下,在尚未到达工作腔的内缘部位,由于液体质点的向心力与离心力相等而失去向心运动动力,在其后液流推动下而改向进入泵轮,由泵轮得到液体能后又继续进入涡轮释放液体能,如此反复循环。在循环流动液体中的向心与离心流动流束之间有一小小的封闭的分界面,界面内为存留空气的空腔。随着转速差的升高,涡轮旋转离心力减弱,而液流在涡轮内的向心流动逐步加强。当转速差达到某值以后,小环流突然转变为大环流[图19-4-2(b)]。大环流液流沿工作腔外环流动,在中心形成较大的充满空气的气腔。由小环流转变为大环流时,泵轮中液流平均流线的入口半径rB1减小了,因而传递力矩增大[式(19-4-1)],这时会产生力矩的突然升高,影响运转的平稳性,故应避免其产生。办法有二:一是在涡轮中心部位增设挡板,防止小环流向大环流的突变,缩小两者差距,即可避免液力偶合器输出转速的不稳定,又可起到限制力矩突然升高的作用;二是使涡轮诸叶片与其背壳构成的流动出口半径不相等,使它们按某种规律相配比,变小环流向大环流的突变为渐变,使力矩和转速均能平缓的变化。

图19-4-2 液力偶合器液流流动形式
大、小环流的转换是在某一转差率下发生的,称该转差率为临界转差率。充液率不同,临界转差率也不同,通常充液率越大,则临界转差率越小。
通常小环流发生在额定工况下,在运转中一旦超载,小环流立即变为大环流,限矩型液力偶合器正是利用大环流使工作腔向辅助腔泄液,从而限制低转速比时力矩的上升。
4.3.3 普通型液力偶合器
普通型液力偶合器(图19-4-3)只有泵轮2、涡轮3、外壳1以及主轴等基本构件,除工作腔外无任何限矩(如辅助腔或挡板)、调速等结构措施。腔体有效容积大,传动效率高。其零速力矩可达额定力矩的6~7倍,甚至有时达20倍。因此过载系数大,过载保护性能很差。多用于不需要过载保护与调速的传动系统中,起隔离扭振和减缓冲击作用。如外配辅助系统可作为液体离合器用于舰船和绕线机等传动系统中。图19-4-3为带有带轮的普通型液力偶合器。这种结构的液力偶合器多用于小功率传动。泵轮2和涡轮3通过中空的泵轮轴支承在电动机轴上,通过键和定位螺栓使液力偶合器与电动机轴固定连接。带轮1通过外壳与涡轮3固定连接,液力偶合器通过V带轮将动力传给工作机。带有带轮的液力偶合器既能简化传动系统的连接,又使动力机和工作机可平行布置(即平行传动),扩大了液力偶合器的应用领域。在中小规格的搅拌机、长床身的机床中,这种平行传动较为常见。

图19-4-3 普通型液力偶合器
1—外壳及带轮;2—泵轮;3—涡轮
由于普通型液力偶合器的泵轮、涡轮形状对称,使其正向传动(动力从泵轮传至涡轮)与反向传动性能相同,可允许泵轮与涡轮(或动力机与工作机)互易其位。
图19-4-4为快放阀式普通型液力偶合器,可传递较大的功率,有供油系统使之可作为液体离合器使用。主动轴1和从动轴5的支点均在两侧,两叶轮均呈悬臂布置,这种结构称悬臂式结构。优点是结构比较简单,零件制造精度要求不高,允许泵轮、涡轮之间有较大径向、轴向尺寸偏差和角度偏差,主、从动轴同轴度要求低,拆装调整容易。缺点是轴向尺寸大,轴向力不能平衡,易产生较大的振动等。在正常工作时供油系统连续向工作腔供油,当需工作机快速停止时,在停止供油的同时,快放阀3开启,工作腔中油液迅速排空,切断主动轴与从动轴的动力联系,满足快速停止的需要。
4.3.4 限矩型液力偶合器
普通型液力偶合器由于过载系数大,使其在许多设备上无法应用。为了有效地保护动力机(及工作机)不过载,要求液力偶合器在任何工况下的力矩均不得大于动力机的最大力矩。因此必须采取结构措施来限制低转速比时力矩的升高。常采用的结构措施有设置辅助腔、采用多角形工作腔和在泵轮与涡轮之间加设挡板等。其中应用最多的是设置辅助腔,依靠超载时减少工作腔液体充满度来限制力矩的升高,此方式在限矩时能量损失较少。在泵轮与涡轮之间加设挡板限矩时能量损耗较大,常作为辅助限矩方式与辅助腔相配合来应用。
常见的限矩型液力偶合器有静压泄液式、动压泄液式和复合泄液式三种基本结构。在此基础上又有派生形式出现,诸如动压泄液式限矩型液力偶合器有派生形式:阀控延充式、闭锁式、堵转阻尼式、加长后辅腔及侧辅腔式、水介质液力偶合器、液力变矩偶合器及无滑差静液力机械偶合器等。

图19-4-4 快放阀式普通型液力偶合器
1—主动轴;2—泵轮;3—快放阀;4—涡轮;5—从动轴
限矩型液力偶合器在恒定充液率下依靠各种不同结构措施在运行中改变工作腔中液体环流状态或充满度来限制力矩的升高。限矩型液力偶合器的限矩原理见表19-4-13。
表19-4-13 限矩型液力偶合器的限矩原理


4.3.4.1 静压泄液式限矩型液力偶合器
图19-4-5为静压泄液式限矩型液力偶合器结构,利用侧辅腔与工作腔中液体的静压力平衡关系来调节充满度。侧辅腔设在涡轮与旋转外壳之间,有较大的容积。涡轮出口处设有阻流板。侧辅腔中的液体大致以泵轮和涡轮的平均转速旋转,以其旋转的离心力形成的静压力来达到与工作腔中的液体压力相平衡。在额定工况因涡轮转速与泵轮转速相接近,故侧辅腔液体旋转速度高、离心力大,存液较少。超载时涡轮转速低,侧辅腔中液体转速亦低,使其离心力小,则静压头小而使工作腔部分液体流入侧辅腔,降低了工作腔液体充满度,而起到限制力矩升高的作用。由于此时涡轮转速较低,工作腔内液体趋于大环流运动,受涡轮出口处阻流板的作用迫使液体外移作小环流运动,使力矩不再增加,也起到了部分限矩作用。

图19-4-5 静压泄液式限矩型液力偶合器结构
静压泄液式液力偶合器的特点是:结构比较简单,载荷突变时动态反应不灵敏,过载系数偏大,通常Tg=2.5~3。多应用在汽车、叉车、破碎机、塔式起重机等过载不频繁的传动中。
4.3.4.2 动压泄液式限矩型液力偶合器
表19-4-14 动压泄液式限矩型液力偶合器












4.3.4.3 复合泄液式限矩型液力偶合器
复合泄液式液力偶合器特点是既有动压泄液,又有静压泄液,故称复合泄液式。图19-4-6所示为复合泄液式液力偶合器结构。在腔内左右两侧各有两支骨架式橡胶油封,为油介质与水介质均可应用的腔型结构。此种液力偶合器有三大特点:液力偶合器固连与承重在电动机轴上;可带制动轮,并与原轮毂轴向尺寸相同;水介质、油介质均可应用。

图19-4-6 复合泄液式液力偶合器B—泵轮;T—涡轮
此种液力偶合器输入轴与动力机刚性连接并由其承受液力偶合器的重量,输出端以半联轴器方式与减速器输入轴或制动轮弹性连接。由于不承受液力偶合器的重量,而减免了减速器输入轴承受交变应力而有疲劳断裂、断轴的隐患。
图19-4-7为此种液力偶合器工作腔内液体的环流状态与泄液。小环流与动压泄液式基本相同,大环流时从连通孔A和工作腔外缘间隙D处同时泄液。前者为动压泄液,后者为静压泄液。因超载而引起动压、静压同时泄液,从而降低了工作腔液体充满度,使传递力矩下降,因而可有效地限制超载力矩的升高。当载荷下降,泵轮与涡轮转差率降低,循环流速与工作腔压强均下降,则超载时泄入侧辅腔中液体沿间隙D或连通孔A徐徐流回工作腔,逐步恢复稳态工况。此即复合泄液式限矩的工作原理。

图19-4-7 工作腔液体的循环流态与泄液
其特点是内轮驱动,泵轮在壳体内,在泵轮外侧设有侧辅腔(其外缘与中心部位均与工作腔连通),在超载(大环流)时中心部位为动压、外缘部位为静压同时向侧辅腔泄液。故既有动压泄液式动态反应灵敏的特点,同时又具有静压泄液式结构简单的优点。
复合泄液式(YOXF)液力偶合器只有泵轮、涡轮、外壳三个盘形件。以输入轴套孔和螺栓定位并固接在电动机轴上,由电动机轴承受液力偶合器重量。减少了减速器轴的承重,避免断轴延长减速器使用寿命。特别是对直交轴型减速器更为有利。液力偶合器输出端可按需要制成单一的轮毂或带有制动轮的轮毂,而且具有同一轴向尺寸。这样大大便利了制动器的布置,简化了结构。如此可使带式输送机的驱动装置大为简化,可使电动机—液力偶合器—制动器—减速器成直列式布置,构成驱动单元,便于带式输送机的驱动装置与支架实现三支点浮动支承,从结构上带来一系列优点。
图19-4-8为装有复合泄液式液力偶合器的驱动单元三支点浮动支承结构。液力偶合器2固连在电动机轴上,由电动机轴承担其重量。其输出端经弹性联轴器与减速器4的输入轴相连接,其输出端的制动轮由机械制动器3包围。电动机、制动器和直交轴减速器安装在同一底座5上。底座5下面铰链支座通过推拉杆6与设备机架的铰链支座相连,推拉杆长度可按需要调节。液力驱动单元作为整体(驱动头)以其输出轴孔套装在驱动滚筒轴上,形成两个支点加上推拉杆的支点,而成三支点支承。又由于推拉杆长度可调节,可使驱动单元绕着减速器输出轴轴心任意角度安装浮动定位,故称之谓液力驱动单元三支点浮动支承。其中液力偶合器2必须如复合泄液式固连在电动机轴上者方可,否则结构上不便组合。

图19-4-8 液力驱动单元三支点浮动支承结构
1—电动机;2—液力偶合器;3—机械制动器;4—直交轴减速器;5—底座;6—推拉杆
复合泄液式液力偶合器除结构紧凑、尺寸小、重量轻等优点之外,另一大优点是使减速器轴不承担其重量,而减免承担附加弯矩和剪切力,即减除交变应力对其影响,因而可减免疲劳破坏、断轴事故的发生。
复合泄液式液力偶合器主要应用于带式输送机、龙门起重机以及球磨机等设备。
国内限矩型液力偶合器部分生产厂家产品型号对照见表19-4-15。
4.3.5 普通型、限矩型液力偶合器的安全保护装置
普通型、限矩型液力偶合器超载时,电动机照常运转,泵轮与涡轮转差大大增加,效率降低,损失的功率转化成热量,使工作液体升温、升压,超过许用温度和压强时,就将引起偶合器喷液引燃或壳体爆裂形成恶性事故,为此必须设置安全保护装置,避免发生事故。
普通型、限矩型液力偶合器的安全保护装置见表19-4-16。
4.3.5.1 普通型、限矩型液力偶合器易熔塞(JB/T 4235—2018)
易熔塞按结构分为三种基本形式:A型易熔塞(图19-4-9),B型易熔塞(图19-4-10),C型易熔塞(图19-4-11)。
技术要求如下。
①材料:35钢或黄铜。
②其余表面粗糙度Ra为12.5μm,锐角倒钝。
③表面镀铜或其他表面处理。
④易熔塞在0.6MPa压力下检查不得渗漏。
易熔塞尺寸应符合图19-4-9~图19-4-11和表19-4-17 的规定。
标记示例:螺纹为M24×1.5,总长L为30mm,A型易熔塞标记为
易熔塞A M24×1.5×30 JB/T 4235—2018
易熔塞易熔合金熔化温度有110℃±5℃,120℃±5℃,140℃±5℃,160℃±5℃,180℃±5℃。
推荐使用易熔塞熔化温度场合:110℃——防爆场合;120℃、140℃——一般使用场合;160℃、180℃——反、正转情况下,频繁启动场合。
易熔合金成分见表19-4-18。
4.3.5.2 刮板输送机用液力偶合器易爆塞技术要求(MT/T 466—1995)
(1)结构形式与安装数量
1)易爆塞的结构形式 图19-4-12是易爆塞的基本结构形式,在不影响安装尺寸互换与安装空间的前提下允许采用其他结构形式。
2)易爆塞尺寸 易爆塞与液力偶合器相连接时的连接尺寸及其外形尺寸详见图19-4-12。
3)易爆塞安装数量
①工作腔直径小于或等于560mm的液力偶合器安装易爆塞的数量最少为1个。


表19-4-16 普通型、限矩型液力偶合器安全保护装置


图19-4-9 A型易熔塞

图19-4-10 B型易熔塞
表19-4-17 易熔塞尺寸 mm


图19-4-11 C型易熔塞
表19-4-18 易熔合金成分


图19-4-12 易爆塞的基本结构形式
②工作腔直径大于560mm的液力偶合器,应按最大发汽量时能安全泄放来确定易爆塞的最少安装数量,并注意质量平衡。
(2)技术要求
1)易爆塞
①1个易爆塞只准许装1个易爆片。
②易爆塞的压紧螺塞的夹紧力矩:T=(5±1.0)N·m。
③易爆塞静态试验爆破压力:ps=(1.4±0.2)MPa。
④易爆塞安全泄放能力:易爆塞用静态爆破压力的爆破片,在动态爆破后应能迅速泄放;不允许在易爆塞爆破后再发生增压现象。
⑤图19-4-12所示结构形式易爆塞的质量要求为(166±0.5)g。
⑥易爆塞的易爆塞体应有预卸压功能。
2)易爆片
①易爆片的内外表面应无裂纹、锈蚀、微孔、气泡和夹渣,不应存在可能影响爆破性能的划伤。刻槽应无毛刺。
②易爆片静态试验爆破压力:ps=(1.4±0.2)MPa。
③易爆片外径为。
④易爆片材料应按能承受180~200℃工作温度来选取。
3)爆破孔板
①爆破孔径;孔两端不允许出现圆角式倒角,外径为
。
②质量要求为。
4.3.6 调速型液力偶合器
调速型液力偶合器主要与电动机相匹配,在输入转速不变情况下,通过调节工作腔充满度(通常以导管调节)来改变输出转速及力矩,充满度的调节是在运转当中进行的,其调节方式如表19-4-19所示。普通型、限矩型液力偶合器均是在运转之前按传递功率大小充入适量的工作液体,因其通常是在额定工况下运转,转差率较小,发热量亦小,靠自身冷却(常在其外壳上设置散热筋片)即可满足散热要求。调速型偶合器则不然,泵轮、涡轮均处在箱体里不与外界接触,散热困难,更因输出转速调节幅度大和传递功率大,故需有工作液体的外循环冷却系统,使工作液体不断地进、出工作腔,以散逸热量和调节工作腔充满度。
设液力偶合器工作腔已有充液量为q,欲使其有Δq的变化量,则需使工作腔进口流量Q1和出口流量Q2不相等,即Δq=Δt(Q1-Q2)。式中Δt是调节时间,若使出口流量Q2保持常量(如保持恒转速下的出口节流-主动喷嘴节流),改变进口流量Q1,则为进口调节;若使进口流量Q1保持常量(如供油泵为定量泵),改变出口流量Q2(导管调节流量),则为出口调节;若同时改变进、出口流量Q1、Q2,则为复合调节。调速型液力偶合器调速原理如表19-4-20所示,调速方式与性能对比如表19-4-21所示。
表19-4-19 充液量常用的调节方式

表19-4-20 调速型液力偶合器调速原理




表19-4-21 调速型液力偶合器调速方式与调速性能对比

4.3.6.1 进口调节式调速型液力偶合器
表19-4-22 进口调节式调速型液力偶合器







4.3.6.2 出口调节式调速型液力偶合器
出口调节式调速型液力偶合器的进口流量为定量(定量泵供油),出口流量由导管进行变量调节,即靠导管口的相对位置(导管开度)来调节出口流量。按液力偶合器结构设置分为伸缩导管式和回转导管式(极少应用)两种。
(1)出口调节伸缩导管式调速型液力偶合器
出口调节伸缩导管式调速型液力偶合器种类繁多,是当前国内外生产最多、应用最广的类型。从液力偶合器箱体外形来看,大致有五种类型(见表19-4-23)。从内部结构的输入、输出轴的支承方式也有五种类型(见表19-4-24)。典型产品见表19-4-25。
表19-4-23 箱体结构类型


表19-4-24 支承结构方式

表19-4-25 出口调节伸缩导管式调速型液力偶合器典型产品结构及特点





(2)出口调节回转导管式调速型液力偶合器
图19-4-13为德国福伊特公司新近开发的SVTW水介质调速型液力偶合器,圆筒状的固定箱体2安装在电动机法兰盘上,泵轮3与导管腔外壳5固连在电动机轴1上,涡轮4与输出轴7固定连接。回转导管6的回转轴中心线与偶合器中心线有偏心距,当扳动手柄10使回转导管回转时就可改变导管腔外壳中的液环厚度,从而调节工作腔充液量和输出转速。导管的回转可以手动,也可以是电动执行器驱动。

图19-4-13 回转导管式调速型液力偶合器
1—电动机轴;2—固定箱体;3—泵轮;4—涡轮;5—导管腔外壳;6—回转导管;7—输出轴;8—进液管;9—出液管;10—手柄
此类型液力偶合器不需冷却系统(清水既是其传动介质又是传热的载体,随进、出口流量而得到散热)和润滑系统(酯润滑的滚动轴承),又无箱体底座,结构极为简单。其特点可由“轻、巧、简、廉”四字概括:
轻——质量极轻;
巧——结构上巧妙的组合;
简——结构极为简单,外形尺寸最小;
廉——成本低廉,经济效益高。
此类水介质液力偶合器尽管具有轻、巧、简、廉四特点,切勿以为只能是小(规格)的。据知该偶合器系列竟有422~1390mm九个规格,最大规格1390mm(立式,750r/min,3800kW),质量有5900kg。
此类水介质液力偶合器的应用领域,主要是高楼供水、自来水厂、供水泵站、农田灌溉等。
4.3.6.3 复合调节式调速型液力偶合器
同时改变工作腔进、出口流量来调速的液力偶合器称为复合调节式调速型液力偶合器。
复合调节式调速型液力偶合器,其调速原理与采用导管排液的出口调节偶合器基本相同。不同之处是该偶合器增设了进、出口的综合配流阀。由图19-4-14可见,综合配流阀7与导管5在操纵时机械联锁。当需要调高输出转速时,顺时针转动操纵手柄,导管5则向内收缩。主滑阀因机械联锁而随之下移,挡住部分甚至全部出油口。于是进油多,出油少,甚至只进不出,所以转速迅速升高。反之,当需要调低转速时,逆时针转动操纵手柄,导管5向外伸出,同时配流阀出口大开,于是进油少,出油多,所以转速迅速降低。当调到某一个工况点后,综合配流阀的开度使供液量与偶合器内的发热量相适应,以保持合适的工作油温(接近等温控制)。因而,进、出口复合调节偶合器不仅调速动作快、反应灵敏,而且能合理利用供液量,效率比较高。它的缺点是结构复杂,成本高,只适合较大规格偶合器用。

图19-4-14 复合调节式调速型液力偶合器原理简图
1—泵轮轴;2—涡轮轴;3—过流孔;4—导管腔;5—导管;6—联锁机构;7—综合配流阀;8—冷却器;9—供油泵
图19-4-15为综合配流阀结构,其中导管控制机构1和凸轮2即是图19-4-14中的联锁机构6。

图19-4-15 综合配流阀结构
1—导管控制机构;2—凸轮;3—主阀芯;4—单向阀
图19-4-16为德国福伊特公司生产的SVL复合调节式调速型液力偶合器,其供油泵6为离心式油泵,由输入轴通过锥齿轮驱动。特点是流量大、压力低,不需溢流阀。电动辅助油泵9向全部滑动轴承供油润滑。输入、输出轴均为带有两支径向滑动轴承和一支轴向推力滑动轴承的简支梁,此双简支梁结构亦称独立支承悬臂式结构,对同轴度要求不高。
此类型液力偶合器运行精度高,能够较好地控制油温,调节得好可达到“等温控制”,传动效率高。但结构复杂、轴向尺寸大。
4.3.7 液力偶合器传动装置
调速型液力偶合器的最高转速只能是3000r/min(二极电动机转速),满足不了工作机更高转速的要求,因而出现了液力偶合器传动装置。
由调速型液力偶合器与齿轮增速(或减速)机构组成的调速装置称液力偶合器传动装置。按齿轮机构所在部位,液力偶合器传动装置可分为前置齿轮式、后置齿轮式和复合齿轮式,齿轮机构有增速的也有减速的。此外,还有一些其他类型的液力偶合器传动装置。

图19-4-16 SVL复合调节式调速型液力偶合器
1—泵轮;2—涡轮;3—外壳;4—箱体;5—工作油;6—供油泵;7—导管;8—综合配流阀;9—辅助油泵
表19-4-26 液力偶合器传动装置的优缺点

表19-4-27 液力偶合器传动装置的分类



表19-4-28 液力偶合器传动装置结构及特点












4.3.8 液力减速器
液力减速(制动)器是涡轮不动的特殊形式的液力偶合器。它不是传动元件,而是耗能的减速制动元件。其结构特点是:涡轮不转动,不输出动力,泵轮和涡轮均采用前倾斜叶片,以增大制动力矩。
图19-4-17为液力减速器诸多结构之一,双工作腔,转子1以花键连接在传动轴3上。转子与定子叶片前倾斜角均为30°。转子随传动轴转动,定子2固定在箱体上,转子和定子共同组成工作腔,充液时转子将机械能转化成液体能,液流以较高的速度和压力冲向定子叶片,定子对液流的反作用力矩即为转子的制动力矩。此时全部液体能转化为热能。被加热的液体通过冷却器冷却后又回到液力减速器中,如此不断循环工作。

图19-4-17 液力减速器
1—泵轮(转子);2—涡轮(定子);3—传动轴;4—冷却循环流道
液力减速器按传动轴转速的高低和工作腔充液量的多少,提供的制动力矩遵从规律。充液少时减速制动力矩低,不需减速制动时不予以充液。λB与腔型、叶片倾斜角、叶片数及充液量有关。液力减速器通常采用30°或45°前倾斜叶片,其泵轮转矩系数约为相同腔型径向平面直叶片普通型液力偶合器的3~10倍。为降低液力减速器制动时产生的轴向力,通常采用双腔型。
由于液力减速器的制动力矩与其转速的平方及工作腔有效直径的五次方成正比,在高转速大直径时有更大的制动力矩,因而比液压制动和摩擦制动的结构尺寸要小得多。液力减速器无机械磨损,可长期无检修的运行,其寿命之长远非液压制动和摩擦制动可比。制动功率越大,其优点越显著。
液力减速器的缺点在于转速下降时制动转矩下降更快。在低于500r/min时制动力矩有波动,在转速为零时完全失去制动能力。故常作为辅助制动与其他制动方式配合使用,通过液力减速器的制动使旋转轴速度降低后,再施以摩擦制动予以刹车,这样可使制动平稳可靠并可防爆。
按用途分类,液力减速器可分为车辆用和固定设备用两种。
4.3.8.1 机车用液力减速(制动)器
当列车在长大坡道下行行驶时,为防止列车下滑超速造成事故,常采用阻尼制动的方式,以限制列车超速。若只采用闸瓦制动,则由于闸瓦温度升高,摩擦因数降低而制动效果变差,闸瓦磨损加快。如交替进行闸瓦制动,则会造成冲击过大,行驶不平稳,且易使驾驶员疲劳。若使用液力减速(制动)器,则这些问题可方便的解决。
图19-4-18为机车用Z510型液力制动器结构。它由内定子2、转子5、外定子6、中间体4、闸板机构3、进油体8以及制动轴9、11组成。内外定子与中间体固定连接,固定在箱体上。转子5通过螺栓与机车动轮的制动轴11相连,而液力制动器的制动轴9 则与转子相连,从而形成机车动轮带动液力制动器转子的结构。

图19-4-18 Z510型液力制动器结构
1—定子内套;2—内定子;3—闸板机构;4—中间体;5—转子;6—外定子;7—外盖;8—进油体;9,11—制动轴;10—导油管;X—制动器中间腔;Y—蜗壳
该液力制动器有如下几个特点。
①采用前倾30°径向平面叶片,转子分长、短叶片,短片上焊有导油管(见图19-4-19)。

图19-4-19 液力制动器转子
1—长叶片;2—短叶片;3—导油管
②定子也采用长、短叶片,其中有两个厚叶片,其上钻有排气孔。
③设有类似于轴流泵的进油体8,进油体压装在转子内,随转子转动,具有相当强的泵油作用,加大了散热器中的循环流量,有利于工作液体散热。
④在中间体上装有闸板操纵阀、充油节流阀、液力制动控制阀、充液量限制阀、双向阀以及测温元件等。
⑤设有闸板机构3,牵引工况时,制动器不充油不工作。闸板闭合,切断制动器循环通路,避免制动器空转时的鼓风损失。当液力制动时,操纵闸板机构,将左右闸板向两边移动,打开制动器循环通道,制动器充油工作,产生制动力矩。
4.3.8.2 汽车用液力减速(制动)器
(1)载重汽车采用液力减速(制动)器的必要性
在山区或矿山使用的大吨位载重汽车,经常需要满载下坡,在长大坡道上频繁制动。若单独使用闸瓦制动,由于制动负荷大、制动时间长,促使闸瓦发热,摩擦因数降低,导致制动性能差、闸瓦磨损快,影响车辆行驶安全性。例如,昆明至思茅公路的元江坡长40km,平均坡度为8%,解放牌卡车点刹车限速运行,由坡顶行驶至坡底需2h左右,测试后轮刹车车瓦的温度竟高达400℃以上,这样高的温度可能使闸瓦烧毁,不仅不安全,还增加了驾驶技术难度,延长了运行时间。而国外很多载重汽车均采用液力减速器,值得借鉴。
为了保证行车安全性,德国交通规则规定:5.5t以上的公共汽车和9t以上的载重汽车必须配备正常制动外的第三制动,要求车辆在6km长、坡度7%的坡道上,能够以30km/h的速度安全行驶。只有应用液力减速(制动)器才能较好地满足上述要求。
(2)汽车用液力减速(制动)器分类(表19-4-31)
图19-4-20为德国福依特公司生产的用于公交汽车、旅游车和大型卡车上的VHBK-130型液力减速器,连接法兰4与汽车变速箱相连,转子5通过传动轴3与汽车万向轴相连并随之转动,定子2与外壳固连。通过操纵电磁换向阀1可打开油路,压缩空气迫使油箱中的油液通过电磁换向阀充入工作腔进行工作。司机可依行车需要按挡[图19-4-20(b)]调节气动阀门,以调节工作腔充液量和选择合适的制动力矩。由工作腔出来的油液经过油/水冷却器散热后再回到油箱中。
表19-4-31 汽车用液力减速(制动)器分类



图19-4-20 VHBK-130型液力减速器
(3)汽车用液力减速(制动)器的控制系统
汽车用液力减速(制动)器的控制系统多种多样,最常用的是气-液联动控制装置。下面以SH380型汽车液力减速(制动)器控制系统为例加以说明,见图19-4-21。当司机欲使用液力减速器时,即踩下气操纵开关4的推杆,使排气阀关闭,进气阀打开,储气筒内的压缩空气经气操纵开关4进入控制阀3顶部的气室,从而推动滑阀下移,打开A、B通道,关闭C、D通道,于是油泵9泵出的工作油便进入液力减速器2的工作腔。工作后的工作液体将出油单向阀5顶开,经滤油器7进入冷却器8,降温后再流回油底壳。与此同时,液力变矩器出油单向阀6在液力减速器排油压力作用下紧闭,其循环油路被隔断。反之,松开气操纵开关4的推杆,控制阀3中的空气逸出,滑阀在弹簧作用下上升,孔口A、B隔绝,C、D接通,液力减速器不能进油,停止工作,而液力变矩器恢复正常工作。

图19-4-21 液力减速(制动)器控制系统示意
1—液力变矩器;2—液力减速器;3—控制阀;4—气操纵开关;5—液力减速器出油单向阀;6—液力变矩器出油单向阀;7—滤油器;8—冷却器;9—油泵
4.3.8.3 固定设备用液力减速(制动)器
固定设备如带式输送机、球磨机、棒磨机等大惯量机械在制动刹车时常采用液力减速(制动)器,尤其下运带式输送机更离不开液力减速(制动)器。
在下运带式输送机从高处向低处输送物料过程中,物料所释放的位能成为带式输送机的附加动力,随着物料位能、输送带倾角和槽形的不同,电机呈不同的运行状态。
1)驱动状态 当物料释放的位能小于输送机的运行阻力时,需要电机驱动输送带运行,输送机的运行工况与平运或上运基本相同。
2)发电状态 当物料释放的位能大于输送机的运行阻力时,物料位能迫使输送机加速运转并对电机做功,使电机超过原有转速,呈发电运行状态。电机向电网反馈电能,同时对系统产生制动作用,如不能制动则输送带飞速下滑,俗称“飞车”。
为了防止下运带式输送机发生“飞车”事故,通常采用大容量电机,使电动机容量大于输送机的制动功率,电机的电磁力矩大于输入的机械力矩。但大容量的电机价格贵、安装困难,又无法有效控制下行速度,而采用液力减速(制动)器,这些问题就可迎刃而解了。
(1)驱动系统
图19-4-22为应用于下运带式输送机的具有液力减速器与机械制动的驱动系统。额定工况下,液力减速器不充液,无制动作用。当输送机加料过多超速时,监控系统发出信号,使液力减速器充入适量工作液体,产生阻尼力矩,控制速度不再上升。液力减速器与自动控制系统相配合,可有效地控制下运带式输送机的运行速度,符合安全要求。
在需要停机时,加大液力减速器的充液量,增加制动力矩,使带速大大降低,当转速降到一定程度后再施以摩擦制动,使设备平稳停机。
(2)控制系统
图19-4-23为某煤矿井下用的下运带式输送机液力减速器控制系统。煤矿井下用液力减速器的控制系统,除具有带式输送机正常运行和正常制动工况的控制功能外,还要具有失电紧急保护控制功能,具体功能见表19-4-32。

图19-4-22 下运带式输送机的具有液力减速器与机械制动的驱动系统

图19-4-23 下运带式输送机液力减速器控制系统
表19-4-32 下运带式液力减速器控制系统功能

4.4 液力偶合器设计
表19-4-33中序号1~5属于科研、生产所需的产品设计,序号6~8为产品应用设计。在诸多类的产品设计中,应用最多的是按照相似理论进行的类比设计,可得到事半功倍的效果。
表19-4-33 液力偶合器设计分类

4.4.1 液力偶合器的类比设计
液力元件的设计是以对叶轮叶栅系统与液流之间的相互作用及能量交换过程的研究作为理论基础的。实际上在液力元件里,叶轮与液流间的能量交换是非常复杂的过程,很难给出理论上的严格解答。
液流在液力元件里的运动是空间三维流动。为使问题简化,目前在设计液力元件时,主要还是采用束流理论(一维理论)。但这样只能求得近似的结果。所以,每设计新型液力元件时,都要经过设计—试制—改进等几个周期。这样,工作量大,周期长,成本高。
目前,在设计液力元件时,为了节省时间,简化设计程序,多采用类比设计的方法。即在已有的性能良好的液力元件模型中,先选定一种原始特性能满足设计要求的液力元件为模型,将其叶栅系统(即由循环圆和叶片组成的系统)按流体力学的相似理论放大或缩小,以满足与动力机的良好匹配。结构方面可参照一般机械结构的设计方法进行设计。
表19-4-34 液力元件的类比设计


4.4.2 限矩型液力偶合器设计
限矩型液力偶合器应用广泛,可满足各类工作机的不同要求。在类比(或相似)设计中,首要的是要选择合乎要求的工作腔模型(腔型)。在选择腔型时要重点考虑过载系数是否合乎要求,同时要考虑到泵轮转矩系数是否合乎有关标准要求。
限矩型液力偶合器的限矩原理见表19-4-13。限矩型液力偶合器的限矩措施如表19-4-35所示。
表19-4-35 限矩型液力偶合器的限矩措施

4.4.2.1 工作腔模型(腔型)及选择
工作腔由循环圆、叶栅系统和流道组成。腔型对液力偶合器性能有决定性影响,其次影响因素为流道的表面光洁度。同一系列液力偶合器在相同工况下和雷诺数在自模区时,具有相同的原始特性,因此在产品设计之初选定(或创建)腔型十分重要。表19-4-36列出各类腔型,供设计时参考。
表19-4-36 部分液力偶合器工作腔几何参数及特性



4.4.2.2 限矩型液力偶合器的辅助腔
(1) 限矩型液力偶合器辅助腔的作用(表19-4-37)
表19-4-37 限矩型液力偶合器辅助腔的作用

(2)限矩型液力偶合器辅助腔的类型
按照静压泄液、动压泄液和复合泄液有三种基本类型及派生类型的各类辅助腔(见表19-4-38)。
(3)辅助腔的容积
首先要满足偶合器过载系数要求,其次是延时启动的需要,同时也要考虑特性曲线的平滑性,避免有较大跌落。
辅助腔容积的确定很复杂,既要满足特性要求又须顾及整体结构尺寸安排。在缺乏已有的设计资料可参照的情况下,只能根据试验资料来确定辅助腔的容积与尺寸。
4.4.2.3 限矩型液力偶合器的叶轮结构
实践表明,限矩型液力偶合器的叶轮结构对其泵轮转矩系数和过载系数均有很大影响。在限制过载系数方面,除设置辅助腔泄液分流之外,设计者常采用适当的叶轮结构来降低过载系数,如表19-4-39所示。
表19-4-38 限矩型液力偶合器辅助腔的类型


表19-4-39 可降低过载系数的叶轮结构

4.4.2.4 工作腔有效直径的确定
工作腔有效直径
(19-4-10)
式中 λB——腔型的额定转速下泵轮转矩系数,min2/m;
Pn——工作机额定功率,kW;
nB——泵轮额定转速,r/min。
在选定的腔型、传递功率和额定转速下,由式(19-4-10)可算得工作腔有效直径,再按表19-4-10“液力偶合器循环圆有效直径系列”圆整为标准规格尺寸,即可进行元件设计。或者在选定腔型后,按表19-4-10规格尺寸进行系列产品设计,在确定工作腔有效直径后,按电机额定转速计算出传递功率。
4.4.2.5 叶片数目和叶片厚度
叶片数目太多,则工作腔有效容积减小,叶片表面与液流摩擦阻力及排挤系数增大,降低传递功率。叶片数目太少又会增大叶片间涡流损失而降低传递功率。表19-4-40为铸铝泵轮叶片数目推荐值。或者按经验公式(19-4-11)确定。
表19-4-40 液力偶合器铸铝泵轮的推荐叶片数

(19-4-11)
式中 D——工作腔有效直径,mm。
根据实际结构及工艺条件,叶片数目可以有所增减。焊接冲压叶片比较薄可适当增加叶片数量,以提高λB。为减少液体流动的排挤,可在涡轮出口采用长短叶片间隔排列。为减少液流脉动而引起的力矩高频波动,通常使涡轮与泵轮的叶片均匀分布,且使数目不相等,即ZT=ZB±(1~3)。实践表明取ZT=ZB±1效果最好。对于泵轮、涡轮叶片数目相等,叶片按分区不均匀布置的方式,因工艺不便而极少采用。叶片厚度与叶轮大小、制造工艺有关,见表19-4-41。
表19-4-41 液力偶合器叶轮叶片厚度(JB/T 9001—2013)

4.4.3 调速型液力偶合器设计
调速型液力偶合器设计在腔型选择(见表19-4-36)、叶轮结构(见表19-4-39)、工作腔有效直径的确定[见式(19-4-11)]和叶片数目等均与限矩型液力偶合器设计有相同或相近的设计方法。而在叶轮强度计算、轴向力计算、导管及其控制、油路系统及配套件等均另有较多的设计工作。
4.4.3.1 叶轮强度计算
限矩型液力偶合器在产品类比设计中加入较多的经验设计,对于高转速、大容量的调速型液力偶合器或液力偶合器调速装置应进行叶轮受力分析和叶轮受力计算。
(1)叶轮受力分析
如图19-4-24所示,涡轮内环有叶片,起到加强筋的作用,而且轮壁内外的油压力PW可相互抵消,因此它的强度条件最好,所以叶轮中,通常着重考虑转动外壳和泵轮的强度计算。
在转速比i接近于1时,流道中的油压力最高,叶轮的应力最大。因此,强度计算以i=1的工况为准。
(2)叶轮轮壁断面形状和厚度的合理设计
液力偶合器叶轮轮壁断面形状和厚度是叶轮强度最主要的因素。设计轮壁的断面形状和厚度时首先以流道的基本形状和尺寸及必要的间隙为基础来确定合理的基本厚度,然后根据等扭矩环原理,向应力较大的根部和结构需要的部分逐步加厚并圆滑过渡,凡应力集中处应加大圆弧。
轮壁断面形状厚度的确定与制造方法有关。例如,采用砂型铸造,轮壁的厚度就不能过薄;采用金属型重力铸造或低压铸造的叶轮,轮壁的厚度与形状则应能满足铸造工艺性要求,确保能够顺序凝固。
(3)影响叶轮强度的主要因素(表19-4-42)

图19-4-24 偶合器泵轮、涡轮和转动外壳上所作用的外力PC—工作轮金属材料在旋转时的离心力;PW—工作油的压力;PA—泵轮和转动外壳彼此传给对方的轴向力;F—轴传给工作轮的轴向推力
表19-4-42 影响叶轮强度的主要因素

(4)叶轮强度计算的圆周速度限制法和传递功率限制法
叶轮强度经验计算最简单的方法是圆周速度限制法和传递功率限制法,通过有限元分析和与被实践证明叶轮强度合格的偶合器进行比较,制订出各种材料和制造方法所制造的叶轮的圆周速度许用值和功率许用值。当所设计的偶合器工作叶轮能同时满足这两项要求时,即可视为满足了强度要求。当超出这一限制要求时,则要在设计中通过材料选择、制造工艺改进和轮壁厚度与形状选择来满足强度要求。叶轮强度计算的圆周速度限制法和功率限制法虽然比较实用,但高转速、大功率偶合器叶轮强度应当采用有限元计算分析。
①叶轮强度计算的圆周速度许用值见表19-4-43(摘自JB/T 9001—2013)
②不同材料、不同制造方法的叶轮转速和传递功率许用值见表19-4-44。
表19-4-43 叶轮圆周速度许用值

表19-4-44 不同材料、不同制造方法的叶轮转速和传递功率许用值

(5)液力偶合器轮壁的基本厚度
与国外偶合器相比,国产偶合器轮壁的基本厚度普遍偏大,这与我国的铸造和热处理技术落后及设计思想过于保守有关。根据实践经验:金属型铸造件的壁厚可以比砂型铸造薄,而限矩型液力偶合器的叶轮壁厚应比调速型液力偶合器的叶轮壁厚薄,涡轮的叶片相当于筋板,且结构与受力状况好,所以壁厚最薄;外壳内无筋板,且受力条件差,壁厚应当最厚,泵轮的壁厚介于两者之间。不同的规格、不同制造方法的叶轮基本壁厚见表19-4-45。
表19-4-45 液力偶合器叶轮基本壁厚推荐值(经验值)

(6)泵轮受力分析(表19-4-46)
表19-4-46 泵轮受力计算

4.4.3.2 叶轮强度有限元分析简介
对于高转速、大功率的液力偶合器与液力偶合器传动装置,应进行三维有限元分析,直观地显示叶轮应力集中部位并求解应力最大值,在满足强度要求的前提下,能够较为准确地为产品的设计、制造提供可靠的依据。
有限元方法是结构分析的一种数值计算方法,其基本思想是将一个连续的求解域离散化,即分割成彼此用节点(离散点)互相联系的有限个单元,在单元体内假设近似解的模式,用有限个节点上的未知参数表征单元的特征,然后用适当的方法,将各个单元的关系式组合成包含这些未知参数的方程组。求解这个方程组,得出各节点的未知参数,然后利用插值函数求出近似解。
结构离散化是静特性有限元分析的前提,也是有限元法解题的重要步骤,其内容包括:把结构分割成有限个单元;把结构边界上的约束用适当的节点约束代替;把作用在结构上的非节点载荷等效地移置为节点载荷;在弹性平面问题中可以把结构分割成三角形、矩形和任意四边形等单元。在空间问题中,可以把结构划分成四面体和六面体单元,常用的有10节点的四面体单元、8节点和20节点六面体单元。
对结构构件进行有限元划分,从理论上讲是任意的,但在实际工作中必须按规律和原则考虑到可行性及经济性进行划分。
网格划分与载荷模型的建立是叶轮有限元分析的重要内容,结合以上分析,总结ANSYS软件用于偶合器工作轮强度有限元分析的过程见表19-4-47。
表19-4-47 有限元分析过程

4.4.3.3 液力偶合器的轴向力
表19-4-48 液力偶合器的轴向力


4.4.3.4 导管及其控制
(1)导管的种类
调速型液力偶合器工作腔充液量的调节方式,应用最多的是导管(亦称勺管)控制,其次是阀门或变量供油泵控制。导管的种类和加工工艺特点见表19-4-49。常用的伸缩直导管见图19-4-25。表层带有导向键槽的中空管筒,在圆周方向有若干排流孔,导管的一端是连接控制机构的柱销孔,另一端是导管口。导管口的形状为等腰梯形(亦有椭圆形的),实践表明等腰梯形能更好地发挥导油功能,降低排油的不稳定因素。
表19-4-49 导管的种类和加工工艺特点


图19-4-25 伸缩直导管

图19-4-26 拨杆式伸缩弯导管控制机构

图19-4-27 伸缩齿条式导管

图19-4-28 回转式导管
按导油流量确定导管内径。在偶合器稳定运行时,导管通过的流量即是供油泵的流量;调速时导管通过的流量应等于供油泵流量加上工作腔充液量变化的流量。经验表明导管的流量应等于两倍供油泵的流量。
导管从100%开度降至0%开度的过程中,时间应为10s左右,即导管应在10s内将偶合器工作腔内的工作液体导空。通常使油液在导管内的流速不得超过12m/s(720m/min)。
液力偶合器工作液体的循环流量通常按Q=(0.185~0.20)PB选取。
导管内径的经验公式是
(19-4-18)
式中 PB——偶合器传递最大功率,kW;
Dn——导管内径,m。
导管在工作状态受到液流的冲击力作用产生一定的挠度,为使导管在导管孔中灵活的滑动,必使之有一定的刚度,而不致出现卡滞现象。但为安装布置的需要,导管外径在保证刚度下要尽量小。导管外径的计算比较复杂,通常采用经验公式:导管外径Dw=(1.3~1.5)Dn,偶合器规格较大、导管较长时取大值。
(2)导管控制机构(表19-4-50)
表19-4-50 调速型液力偶合器导管控制机构分类


图19-4-29 液压缸-连杆式导管控制机构

图19-4-30 角行程电动执行器导管控制机构
1—导管;2—三通法兰;3—刻度板;4—指针;5—曲柄;6—电动执行器
(3)导管排油与调速
导管的功能实质是一种旋喷泵,具有截取旋转油环油液并泵出的作用,与油泵的功能是相同的。
由图19-4-31可见,当导管口端中心距偶合器中心线的半径为Rx时,旋转油环在此处的圆周速度为
(19-4-19)
式中 nB——泵轮及旋转油环的转速,r/min;
Rx——导管口端中心距偶合器中心的半径,m。

图19-4-31 导管排油与调速
1—泵轮;2—涡轮;3—流通孔;4—排油;5—导管;6—甩油片;7—旋转外壳;8—进油管;9—旋转油环
以圆周速度ux旋转的油环,当碰到固定不转但能斜向或直向移动的导管口端时,旋转油环所形成的动能便转化为压能,在迎着旋转油环的导管口处产生一定的压头。按毕托管原理(即伯努利方程),此压头为
(19-4-20)
式中 Hx——距偶合器中心线距离为Rx半径处的导管孔口压头,m(水柱);
ux——旋转油环在该处的圆周速度,m/s。
式(19-4-20)是在液环的自由液面与导管口的中心相一致的情况下建立的,旋转油环液面在此压头下冲入导管而回入油箱,从而减小液环厚度及工作腔充液量,降低偶合器输出转速。当导管缩回、导管口离开液环时,液环增厚(因供油泵不断充油),则工作腔充液量增多、输出转速提高。若导管不动作,则导管流量与供油泵流量相等,工作腔充液量不变,输出转速亦不变。此为出口调节调速机理。
(4)导管控制方式
导管由电动执行器控制可有三种操作控制方式:手动操作、手操电控和自动控制。手动操作为在机旁摇动电动执行器手柄控制导管伸缩,手操电控为在控制室内按电钮操纵电动执行器,此二者均为在导管控制系统里加入人为因素,称为开环控制,见图19-4-32。自动控制为从工程系统(如电厂锅炉)中截取压力、速度、水位、温度等信号经变换器变换成电信号,再经伺服放大器放大为4~20mA电流输入电动执行器,使偶合器的输出转速随信号的变化而自动变化。此为闭环控制,见图19-4-33。

图19-4-32 调速型液力偶合器开环控制原理

图19-4-33 调速型液力偶合器闭环控制原理
4.4.3.5 设计中的其他问题
①对要经常变化工作腔充满度的液力偶合器,工作腔应有通大气的孔,以便在增减循环工作液时使空气出入。气孔位置在叶片端线R2处,(如图19-4-34所示)。一般孔径为ϕ5~6mm,2个孔即可。

图19-4-34 通气孔位置
②在导管调速型液力偶合器的辅助腔中,为了确保液体的线速度,应在辅助腔内壁加些径向筋板。在辅助腔转速为3000r/min时一般筋板高度为2.5~3mm,厚度为3~5mm。
③需补偿液的液力偶合器,补偿液进口原则上开在低压处,即旋转轴线或泵轮液流进口处。供液压力p0=0.06~0.2MPa。
④为了承受拉力和加强密封,外缘螺钉直径不宜过大,但数量要尽量多些。
⑤起离合作用的液力偶合器,为迅速放液,放液阀口要开在高压处,即循环圆最大半径处。
⑥导管尺寸和结构,对出口调节式,一般使导管内径d=(0.02~0.06)D(D为有效直径)。转速高、取小值;转速低、取较大值。供液量小者取小值;供液量大者取大值;对于喷嘴导管调速型(进口调节式),由于喷嘴尺寸的限制,则可做的更小些,以协调升降速时间。
⑦泵轮、涡轮及其旋转零件应进行静平衡或动平衡。
4.4.3.6 油路系统
油路系统主要包括供油系统、润滑系统。
(1)供油系统
供油系统的作用是为了冷却和调速时增减工作腔中存液量并补充旋转外壳间隙密封的漏损。
供油泵一般工作压力为0.2~0.5MPa,在液力偶合器进液口处不低于0.06MPa。供油泵的流量按式(19-4-21)计算
(19-4-21)
式中 Q——发热量;
c——工作液体比热容;
Δt——进出液力偶合器工作液体温差,常取Δt=10~15℃,视冷却器冷却能力而定。
中小功率液力偶合器的供油泵多选用齿轮泵、叶片泵和转子泵。大功率者多用离心泵或螺杆泵。
在重要设备上常设置备用供油泵。
采用滚动轴承的调速型液力偶合器的供油和润滑系统使用统一的油路(图19-4-35)。油泵1从油箱中吸油,经过设置在液力偶合器外部的冷却器2后,流入进油腔,通往工作腔,同时润滑各滚动轴承。安全阀3安装在箱体内。在出油口装有压力表4和温度计5,进油口装有温度计6,这些仪表均安装在箱体外侧上方,可随时监控油路系统中的油温和油压的变化。

图19-4-35 采用滚动轴承的液力偶合器的供油和润滑系统
1—油泵;2—冷却器;3—安全阀;4—压力表;5,6—温度计
(2)润滑系统
液力偶合器的轴承润滑必须保证,特别是大功率、高转速时一般采用强制润滑。
强制润滑系统一般由油箱(可与供油系统共用)、油泵、过滤器、冷却器等构成。润滑系统也可与其他机组润滑系统共用一个泵站。
为了防止突然断电事故,设置高位油箱。在突然断电,润滑系统停止供油时,高位油箱继续供润滑油直至机组停车。高位油箱容量应在断电后供油15min以保证惯性运转的需要。
采用滑动轴承的调速型液力偶合器,其油路系统分为主供油系统、润滑系统及辅助润滑系统(图19-4-36)。其辅助润滑系统单独设置在箱体外。

图19-4-36 采用滑动轴承的液力偶合器油路系统
1—辅助润滑油泵;2—梭阀;3—双联滤油器;4—输出轴轴承;5—推力轴承;6—泵轮轴承;7—输入轴轴承;8—主供油泵;9—冷却器;10,16—节流阀;11,15—压力表;12—安全阀;13,14—温度表
液力偶合器启动前,必须首先启动辅助润滑油泵1,润滑油经梭阀2和双联滤油器3通过专门设置的润滑油路润滑滑动轴承4、5、6和7。
液力偶合器启动后,主供油泵8经箱体外部的冷却器9向工作腔供油。同时,在节流阀10前有一部分油液经梭阀进入润滑油路。当滤油器3后的压力表11显示达到规定的润滑压力(0.14~0.175MPa)后,辅助润滑油泵1停止工作。在液力偶合器正常运转时,滑动轴承由主油泵供油润滑。
在液力偶合器停机过程中,当压力表11显示值降到0.05MPa时,必须立即启动辅助润滑油泵1,及时向各滑动轴承供油润滑。
油路系统中装有安全阀12(安装在箱体内),其开启压力为0.05~0.42MPa。液力偶合器在运转时,分别通过温度表13和14,压力表11和15,及装在各滑动轴承处的测温元件,监控主供油系统和润滑系统的油温和油压。
在液力偶合器运转时,应将工作油油温控制在规定的范围内,即入口油温应高于45℃,出口油温应低于90℃,这可以通过调节冷却器中冷却水的流量来控制。
液力偶合器启动前,油箱内油温应高于5℃,如果低于此值,可用电加热器进行预热。
正常情况下,各滑动轴承的温度不允许超过90℃。若超过,则应停机检查润滑油路。
压力表和温度计大多采用电接点式,出厂时已配备好,用户可根据需要采用报警装置或实行联动控制,以保证液力偶合器安全可靠地运行。
调速型液力偶合器也可设分离式油路系统,立式或圆筒箱体调速型液力偶合器以及其他不便于采用一体化油路系统的调速型液力偶合器,往往采用分离式系统。其特点是供油、润滑系统不在偶合器箱体内,单独设置液压站,用连通管与偶合器进油口与出油口相连,见图19-4-37。

图19-4-37 分离式油路系统图
1—流量计;2—冷却器;3—节流阀;4—压力表;5—滤油器;6—截止阀;7—单向阀;8—供油泵机组
4.4.3.7 调速型液力偶合器的辅助系统与设备成套
在液力偶合器主传动之外的、支持主传动运转的系统,诸如供油与润滑系统、油温与油压监控系统、转速调节控制系统、转速检测系统、液力传动自动控制系统等均称辅助系统。图19-4-38为出口调节伸缩导管调速型液力偶合器辅助系统的典型配置。

图19-4-38 出口调节伸缩导管调速型液力偶合器辅助系统的典型配置
—偶合器自身的构件;
—安装在偶合器上的仪器仪表;
—安装在控制室的仪表;
1—油泵;2—输入轴承;3—背壳;4—涡轮;5—泵轮;6—外壳;7—导管;8—导管壳体;9—输出轴;10—箱体;11—压力表;12—温度表;13—热电阻;14—压力变送器;15—冷却器;16—综合参数测试仪(现场用);17—综合参数测试仪(控制室用);18—转速传感器及测速齿盘;19—转速仪;20—伺服放大器;21—电动操纵器;22—电动执行器;23—液位传感器;24—液位报警器;25—电加热器;26—电加热自动控制器
(1)液力偶合器的辅助系统
大功率的调速型液力偶合器安装在大型设备主传动线上,往往要求有齐全的辅助系统,其组成见表19-4-51。
表19-4-51 液力偶合器辅助系统的组成

(2)液力偶合器的设备匹配成套
在使用中风机或水泵与调速型液力偶合器及电动机是一个单元,成套的匹配设计、选型、安装会带来多方面的好处。可免除设计单位分项选配单机的诸多不便,使设备选型和工程设计更为优化、快捷。可使用户分头对外的设备采购、安装调试、维修服务的工作量和费用大大降低。
通常,工程项目按工艺流程以供风或供水的参数为主导,以风机、水泵为主进行匹配成套工作。但由于引入了价值高、操作复杂的液力偶合器,更兼它连接风机(或水泵)与电机,并可向两者供应润滑油以取代润滑泵站,有时在给定了供风或供水参数的条件下,以液力偶合器为主进行匹配成套及组装更为便捷妥当。
目前,国内已有液力调速双吸离心泵成套机组系列和液力调速渣浆泵成套机组系列(大连液力机械公司设计),可供设计单位或用户选择。
图19-4-39为液力调速双吸离心泵成套机组布置图,加上配套系统构成完整的设备单元。

图19-4-39 液力调速双吸离心泵成套机组布置图
调速型液力偶合器集中了传动系统、润滑系统、供油系统、监控系统、冷却系统(有时还需要加热系统)和转速监控系统。故以液力偶合器为主进行设备成套,有利于配套系统的优化配置,能统一润滑系统,能使整体结构紧凑,成套化程度高、安装精度好,可靠性高,维护费用低,使用寿命长。
4.4.3.8 调速型液力偶合器的配套件
表19-4-52 调速型液力偶合器的配套件







4.4.4 液力偶合器传动装置设计
液力偶合器传动装置通常由出口调节式伸缩导管调速型液力偶合器与齿轮机构组合而成,各类典型结构见表19-4-28。
4.4.4.1 前置齿轮式液力偶合器传动装置简介
图19-4-40所示为前置齿轮式液力偶合器传动装置配套系统。除机械构件之外,辅助配套系统可分为两大类:一类是润滑油与控制油泵送系统;另一类是传动油供油系统。两者均从箱体底部油池1吸油。润滑油与控制油泵送系统包括有机动润滑主泵3、电动辅助润滑泵2、润滑油冷却器4、双腔滤油器5、报警器6及连通伺服阀11和伺服油缸15的油路。传动油供油系统包括有供油泵8、流量控制阀9、工作腔10、导管腔12、导管13、冷却器14,以及控制伺服阀与流量控制阀的凸轮操作机构。
在主机启动前,开动电动辅助润滑泵使各处润滑轴承得以预润滑,在机动润滑泵随主机启动后,便切除电动辅助润滑泵。两个凸轮片套装在电动执行器轴上,一个凸轮片控制着伺服阀和伺服油缸及导管,凸轮的设计使电动执行器的控制电流I与凸轮转角φ、导管升程(开度)、输出转速n2均有线性关系,以便在使用现场能够精确地进行转速调节。另一个凸轮片控制着流量控制阀随时调节进入工作腔的流量与液力偶合器传动装置所传递的额定功率成正比、与工作腔进出油温差成反比,并且是转速比i的三次方函数。在图19-4-40中可见,工作腔、导管腔、冷却器、流量控制阀之间构成工作油的主回路,而由供油泵来的油路为供油支路,冷却器与流量控制阀之间的溢流阀为溢流支路。与流量控制阀联动的凸轮依据导管全程中液力偶合器输出转速n2的高低和按转速比的发热量变化(在i=0.66点发热量达最大值,并依转速比呈正态分布规律)来设计凸轮导程,使进入工作腔的流量在满足工作腔“等温控制”或接近等温控制条件下达到最小值。按此要求,工作腔进油流量由凸轮导程-流量控制阀开度决定,进油流量在转速比i低值时流量小,i高值时流量大,在i=0.66时,流量最大,以后流量又渐小,依此有效地带走液力偶合器随时产生的热量,保持“等温控制”。按照液力偶合器的转速比和发热量,适时地供给所需的最小供油量,可有以下好处。
①“等温控制”,保证液力偶合器不“过热”。
②充分利用工作腔的回油,减低供油泵的流量,减少油流能耗。
③工作腔出口流量小,对导管口的冲击强度低,振动小,利于平衡稳定。且出口流量小,可减少油流能耗。
④在导管开度为零时供给最小供油量,可使最低稳定转速更低,扩大了液力偶合器的调速范围。
可见凸轮控制的变流量供油比恒定大流量供油给液力偶合器带来诸多好处,这也是先进技术使然。

图19-4-40 前置齿轮式液力偶合器传动装置配套系统
1—油池;2—电动辅助润滑泵;3—机动润滑主泵;4—润滑油冷却器;5—双腔滤油器;6—报警器;7—外用润滑管路;8—供油泵;9—流量控制阀;10—工作腔;11—伺服阀;12—导管腔;13—导管;14—冷却器;15—伺服油缸
4.4.4.2 液力偶合器传动装置设计要点
(1)“等温控制”的联动装置
“等温控制”是按偶合器不同工况、工作腔的发热量变化由流量控制阀(综合配流阀)控制工作腔的进油量与导管开度控制的出油量的联合配比,使工作腔油温控制在规定的油温限度以内,避免油温过高影响运行。导管开度与流量控制阀联动控制(即双凸轮控制)达到油温不过热要求。装在电动执行器轴上的两支凸轮片,按控制电流和两只凸轮片各自的转角来控制导管升程(开度)、输出转速和流量控制阀进入工作腔的流量,从而控制工作腔的油温。
(2)泵轮材质与强度计算
由于是高转速大功率的传动部件,必须按不同工艺(锻造、铣削或电火花)选用高强度、高韧性的材质。泵轮强度应进行电算。
(3)高速齿轮对的设计与加工
通常为抵消斜齿轮的轴向力而将两支拼装的斜齿轮组成人字齿轮,使加工精度和装配(啮合)精度均有极高要求,为一般机械加工难以达到。在各类液力偶合器传动装置中,只有后置齿轮减速型的齿轮便于加工和装置。
供油和润滑为两个独立系统,各有一冷却器。供油泵为离心油泵,润滑油泵为齿轮油泵,同由输入轴轴端齿轮驱动。为了滑动轴承在启动前的预先润滑,润滑系统另设一电动润滑油泵,以保证主机启动前和停车后的滑动轴承润滑。
4.4.5 液力偶合器的发热与冷却
液力偶合器运行中因有转速损失而发热,工作液体在传动中既是工作介质同时亦为热量载体。
限矩型和普通型液力偶合器在运行中的功率损失(即发热功率)PS=PB-PT=(1-i)PB,i越小,功率损失越大,制动工况时(i=0)功率损失最大。功率损失表现在工作液体在流道中的冲击损失(特别是叶片顶部的冲击损失)和摩擦损失。损失的功率(发热功率)使工作液体温度升高。当过载严重或过载不严重但时间较长时,液体温度达到密封和油液老化所不允许的程度时,液力偶合器的过热保护装置——易熔塞(限矩型和普通型液力偶合器均装有易熔塞,调速型液力偶合器一般不装易熔塞)中低熔点合金熔化,使液力偶合器向外喷油而中断运行。
普通型和限矩型液力偶合器大多采用自冷式,即靠旋转壳体向外界散热。
液力偶合器的散热功率
(19-4-22)
式中 K——液力偶合器综合散热系数,决定于液力偶合器的结构形式和工作状态;
F——液力偶合器散热表面的面积(包括散热筋片);
Δt——液力偶合器表面温度与环境温度之差。
对自冷式液力偶合器必须Pa≥Ps(Ps为液力偶合器的发热功率)。
调速型液力偶合器、液力偶合器传动装置、液力减速器必须有外冷却系统散热,运行过程的发热功率与转速比i及载荷性质的关系见表19-4-53。
表19-4-53中的相对损失功率仅是转差损失的理论值。在损失功率中转差损失最大,此外还有轴承损失、鼓风损失、导管损失等。因此在计算液力偶合器发热功率(损失功率)时,要全面考虑。虽然最大功率损失系数为0.148,但经验公式是Pa=(0.20~0.23)PB,并以此选用冷却器。
表19-4-53 调速型液力偶合器功率损失

注:为液力偶合器的相对输入功率,PB为液力偶合器的输入功率,Pdn为额定功率。
为液力偶合器的相对损失功率。
为液力偶合器的相对输出功率。
冷却系统的供液量即是供油泵(定量泵)的流量,可按式(19-4-21)确定。
冷却器的选择依据液力偶合器发热功率和冷却介质的温度。
一般冷却器的出口油温高于冷却介质(水或空气)进口温度10℃左右。相差值越大,冷却效果越显著。因此选择冷却器时,需知液力偶合器进、出口油温和冷却器进、出口水温。
以水为冷却介质的冷却器有管式和板式两种结构形式,管式冷却器结构尺寸大,散热系数K值低,散热效果差,但易清洗,抗结垢能力强,使用寿命长。板式冷却器结构紧凑,散热系数K值高,散热能力强,但不易清洗,抗结垢能力差,使用寿命短。
冷却器散热面积A(m2)为
(19-4-23)
式中 Q——液力偶合器运行中发热量,J/h;
K——冷却器的散热系数,管式冷却器K=(628~1047)×103J/(m2·h·℃),板式冷却器K=(837~2930)×103J/(m2·h·℃);
t1,t2——工作油进、出冷却器的温度,℃;
t'1,t'2——冷却水进、出冷却器的温度,℃。
液力偶合器出口油温,一般不超过70~75℃。对于大功率液力偶合器,若工作油和润滑油分别带有冷却器,则润滑油温限制在70℃以下的同时,工作油温可提高到90℃,以提高冷却效果和减小冷却器散热面积。
冷却器所需水量qL(m3/h)为
(19-4-24)
式中 Q——液力偶合器运行中发热量,J/h;
c——水的比热容,c=4186.8J/(kg·℃);
Δt——冷却水进、出口温差,一般管式为5~7℃,板式为7~10℃;
ρ——水的密度,ρ=1000kg/m3。
冷却水进、出口油温、水温选择见表19-4-54。
以上计算有些繁琐,况且冷却器规格有限,即便计算的相当精确,也只能靠挡选取,所以精确计算意义不大,推荐用简化方法计算,见表19-4-55。
表19-4-54 冷却水进、出口油温、水温选择

表19-4-55 调速型液力偶合器冷却器换热面积及冷却水流量简化计算

在寒冷地区的冬季,气温较低,偶合器的工作液体受冷凝结,不利于液力偶合器启动和调速,可以利用偶合器油箱下部的电加热器对工作液体进行加热。一般规定工作液体低于5℃时应当加热。
4.5 液力偶合器试验
液力偶合器元件试验通常包括内特性试验、专题试验和外特性试验。内特性试验主要是测定液力元件内部的速度场和压力场,为现有的设计计算提出修正方法,使之符合实际情况。专题试验是为了满足工作机的要求而进行的特种试验。当转速很高时,离心力导致叶轮破裂,需做离心破坏试验;为了合理地确定结构方案和选择轴承,需进行轴向力试验;为了合理地选择供油泵和冷却器,需作散热温升试验等。一般情况不需进行内特性试验和专题试验。外特性试验包括出厂检验、性能试验、可靠性试验。
4.5.1 限矩型液力偶合器试验
表19-4-56 限矩型液力偶合器试验(JB/T 9004—2015)

4.5.2 调速型液力偶合器试验
表19-4-57 调速型液力偶合器试验(JB/T 4238.1~4238.4—2005)


4.6 液力偶合器选型、应用与节能
调速型液力偶合器的应用见表19-4-58。众多应用实例表明,调速型液力偶合器可节约电能20%~40%,被国家列为推广应用的节能产品。限矩型液力偶合器因其可使电动机降低机座号而节能,亦被国家列为推广应用的节能产品。限矩型液力偶合器应用领域与效益见表19-4-59。
表19-4-58 调速型液力偶合器的应用领域与效益


表19-4-59 限矩型液力偶合器应用领域与效益

4.6.1 液力偶合器运行特点
液力传动由于利用液体在主动、从动件之间传递动力、为柔性传动,具有自动适应性。在传动运行中可有以下特点。
①能使电机空载起步,由于缘故,使之不管调速型还是限矩型液力偶合器均具空载起步特点,在由静到动的起步瞬间(n=0,T=0),电动机只带泵轮空载启动,且转速迅速上升,按力矩与转速平方成正比关系,泵轮与涡轮力矩(两者力矩恒等)迅速提高,当涡轮力矩等于载荷启动力矩后,则涡轮带动载荷设备缓慢起步并升速。故电动机空载起步,而对载荷设备却可满载、平稳启动和加速。图19-4-41为有、无液力偶合器的启动比较。图中带有下角标“D”者为电机直接启动;带有下角标“0”者为装有限矩型液力偶合器的电机启动,可见n0与nD有明显的不同。
②可以提高电动机的启动能力,可以克服异步电动机启动力矩低的缺点,可利用电动机的尖峰力矩去启动载荷。图19-4-41中输出转速为零时,T0明显大于TD,故可降低电动机机座号。

图19-4-41 装与不装限矩型偶合器的电机与载荷启动过程
③对电动机和工作机均有良好的过载保护性能。匹配得合适,即使在工作机卡住不转时,动力机仍能带动泵轮照常转动,并不超载、不失速、不堵转,从而保护电动机不烧毁(或内燃机不熄火),以及传动部件免于损坏。
④降低启动电流的持续时间和减小启动电流平均值。没有液力偶合器时启动电流持续时间长,装液力偶合器后,由于电动机不是直接带动载荷而使启动电流很快降低下来(ID与I0),因而缩短了启动电流的持续时间。
⑤在多电动机驱动时可以平衡功率,便于多机驱动,并可顺序延时启动,使各电动机启动电流相互错开不叠加,大大降低总启动电流峰值。
⑥减缓冲击,隔离扭振,保护设备与传动部件,延长设备使用寿命。
⑦调速型液力偶合器可无级调速,既可机旁手操作,又易于实现远程控制和自动控制。
⑧维护方便,可长时期无检修地运行,而且由于主、从动件不接触,没有机械摩擦,所以寿命长,寿命周期效益高。液力偶合器传动效率高,额定工况时为0.97左右。
⑨应用在工作机为叶片式机械的传动系统中,调速型液力偶合器可以有显著的节能效果;限矩型液力偶合器在合理匹配下,由于降低电动机机座号也有节能效果。
⑩液力偶合器传递功率与输入转速、循环圆直径的三、五次方成正比,故在高转速、大功率下其体积小、性能好的优越性是机械传动、液压传动和电气传动无法相比的。液力偶合器适于与高、低电压的异、同步电动机匹配使用,特别是在高电压、大容量电动机的调速传动中占有主要地位。
液力偶合器在传动中的特点是不能增大或减小传递的力矩,也不能增速。缺点是在运转中随着负载的变化,转速比也相应变化,因此不可能有精确的转速比。
为了说明液力偶合器在传动系统启动过程中的良好作用,这里介绍某公司做过的很有趣的试验。试验中分别以电动机加装FB0.85C限矩型液力偶合器和直接用电动机两种方式驱动直径为710mm,宽500mm,飞轮GD2=1540N·m2(157kgf·m2)的圆盘,进行启动特性试验(图19-4-42)。
当直接用电动机驱动圆盘时,其启动特性曲线如图19-4-42的上半部,启动电流400A。持续时间长达12.8s,启动力矩也比较大(最大值达590N·m)。当加装FB0.85C液力偶合器时,由图19-4-42的下半部可见,启动3s后启动电流由400A降至100A,启动力矩也小(小于343N·m),并随着涡轮转速的上升,启动力矩降至196N·m左右。当启动完毕,两种情况的力矩与电流均接近相等。图中可见采用液力偶合器后电动机(及泵轮)与载荷(及涡轮)分为两步启动(分别以nB与nT起步和升速),且使电动机空载起步。

图19-4-42 启动特性试验
I—电流曲线;T,TT—电动机、液力偶合器输出力矩曲线;n,nB,nT—电动机、泵轮、涡轮转速曲线
4.6.2 液力偶合器功率图谱
表19-4-60 液力偶合器功率图谱

4.6.3 限矩型液力偶合器的选型与应用
4.6.3.1 限矩型液力偶合器的选型
(1)限矩型液力偶合器与电动机的匹配
①保证传动系统的高效率。应使液力偶合器额定工况的输入特性曲线Tn=f(nB)与电动机外特性曲线交于额定工况点。或使液力偶合器额定力矩与电动机的额定力矩相等或接近。
②对电动机的保护功能。应使液力偶合器零速工况i0的输入特性T0=f(nB)曲线交于电动机尖峰力矩外侧的稳定工况区段上。这样,工作机因载荷过大而发生堵转时,电动机也不会堵转而烧毁。另外,液力偶合器的启动过载系数TgQ和最大过载系数Tgmax均须小于电动机的过载系数Td。
③根据载荷性质选择液力偶合器。对于带载荷启动的工作机(如长距离的带式输送机),最好选λ0=λmax的液力偶合器,以利用电动机的最大力矩启动载荷;对于阻力载荷小,惯性载荷占主要成分的工作机(如转子型破碎机),可选λ0稍大于λn的液力偶合器;对于只起离合作用的,可选普通型液力偶合器,λ0≤(4~5)λn。
(2)限矩型液力偶合器与工作机的匹配
①按工作机轴功率选择限矩型液力偶合器而不依电动机功率来选择液力偶合器,经验表明应使工作机、液力偶合器和电动机的额定功率依次递增5%左右,即
工作机∶液力偶合器∶电动机=1.0∶1.05∶1.10
②按工作机载荷特性选液力偶合器。如带式输送机要求启动时间长、载荷曲线平滑、过载系数低,应选用带后辅腔(或加长后辅腔)的限矩型液力偶合器。
③根据使用工况选择偶合器。煤矿井下使用,必须选用防爆型水介质偶合器。露天使用须选用户外型偶合器等。
④根据连接方式选择偶合器。电动机与工作机平行传动,应选用带轮式偶合器;立式传动应选用立式偶合器。
⑤根据液力偶合器与动力机、工作机连接形式而选定偶合器连接结构,例如空心轴套装式、易拆卸式等。
⑥多电动机驱动同一工作机时实行顺序延时启动可大幅度降低启动电流。顺序延时多长为宜,应在前一台电动机启动电流峰值降至平缓时再启动第二台电动机。通常中小型笼型电动机启动时间约为1~2.5s,可将间隔时间(即延时)设3s即可。如此可降低启动电流对电网的冲击,减低变压器的负荷。
⑦功率平衡及调节。多电机驱动同一工作机时,转动快的出力大,超负荷,转动慢的负荷不足,驱动系统总耗损加大。为此可调节偶合器充液量,使之达到功率平衡。
4.6.3.2 限矩型液力偶合器的应用
(1)大惯量设备的启动特性
限矩型液力偶合器多用于大惯量设备。大惯量设备是指运转部件质量大、难以启动的设备,如球磨机、破碎机、磨煤机、刮板输送机、带式输送机等均具有很大的启动惯量并难以启动,通常它们的启动力矩是额定力矩的2~3.5倍,若电动机选型不当或电压波动较大时就难以启动,甚至有时烧毁电动机。
按动力学分析,在载荷启动瞬间作用在电动机轴上的载荷启动力矩为
(19-4-25)
式中 Tc——与转速无关的摩擦阻力矩,是轴承及机械接触摩擦力矩与鼓风阻力矩之和,对具体设备为常量;
Ta——载荷加速力矩,Ta=Jε。
加速力矩与系统的转动惯量J及角加速度ε有正比关系,或者与系统物体质量m,加速度a成正比,而与载荷加速时间t成反比,因此载荷加速时间越短,加速力矩Ta和TZQ就越大。电动机直连传动启动时,构成冲击载荷,加速时间极短,则启动力矩很大而难以启动。若电动机拖不动则形成“闷车”而加长了启动电流持续时间,再严重时就烧毁电动机。加装液力偶合器改善了电动机启动状况,是解决上述问题的有效办法。
(2)电动机启动能力的提高
通常笼型电动机的启动力矩远小于其最大力矩,配以液力偶合器后使其联合工作的启动力矩大为增高(甚至接近电机的最大力矩),且使电动机起步瞬间接近空载启动。
动力机加装液力偶合器传动后,直接负载由工作机改为偶合器泵轮,因偶合器泵轮力矩与其转速的2次方成正比且转动惯量很小,故动力机近似等于带偶合器泵轮空载启动,所以启动轻快平稳、启动时间短、启动电流均值低、对电网冲击小,启动性能得以改善。涡轮启动后输出力矩立即升高(见图19-4-41)。
图19-4-43(a)为电动机带偶合器泵轮启动状态,泵轮与电动机转子同步升速,若外载荷阻力足够大,则泵轮沿oem(i=0)上升与电动机特性曲线交于m点,此时涡轮力矩为om',若阻力较小,则TT为oq's'曲线至b'点,稳定运行。图19-4-43(b)为电动机与偶合器(涡轮)联合输出特性曲线。可见加装液力偶合器后:①偶合器输出力矩om'远大于电动机启动力矩oq;②工作机启动时的加速力矩ΔT2远大于电动机直接驱动时的加速力矩ΔT1。因此既利于电动机的空载启动,而又增大其启动能力。
(3)限矩型液力偶合器的节能效果(表19-4-61)

图19-4-43 装与不装液力偶合器电动机启动特性分析
TZ—工作机负载力矩;Td—电动机转矩;TB—偶合器泵轮力矩;TT—偶合器涡轮力矩;
ΔT1—电动机带偶合器启动时其转子与偶合器泵轮的加速力矩;
ΔT2—工作机启动时的加速力矩;ΔT—电动机直接驱动工作机
时的启动加速力矩;TZ0—工作机启动静阻力矩
表19-4-61 限矩型液力偶合器的节能效果


(4)液力偶合器在典型的大惯量设备上的应用(表19-4-62)
表19-4-62 液力偶合器在典型的大惯量设备上的应用



4.6.4 调速型液力偶合器的选型与应用
调速型液力偶合器多用于风机、泵类的调速运行并有节能效果。
4.6.4.1 我国风机、水泵运行中存在的问题
①单机效率低,国内产品比国外的效率约低5%~10%,在市场竞争条件下制造厂应极力提高产品质量。
②系统运行效率低,据查曾有某钢铁企业机泵实际运行效率仅为6%,这是因为系统单机匹配选型不当,裕度系数过大和不合理的调节方式所造成。
裕度系数过大由两方面造成:一是设计规范的裕度系数过大,“宽打窄用”;另一是单机选型过大,向上靠挡,宁大勿小。最终造成整套系统“大马拉小车”欠载运行的不合理匹配状况。
图19-4-44中A点是额定点(高效点),由于机泵选型过大(流量QA过大),需节流调节流量使运行点偏离至B点降到所需流量QB,则机泵效率由ηmax降到ηB,浪费能源。若采用调速调节流量至QB,则可仍保持机泵的高效率而节约能源。

图19-4-44 机泵偏离额定点运行时的效率
③大多数企业仍在沿用落后技术管道闸阀节流方式,先进的调节方式应用尚少。若改为调速调节可节能20%~40%。
④运行管理粗放,风机放空,水泵回流,跑、冒、滴、漏现象随处可见,使能源浪费严重。专家认为加强管理可拿回10%能源。
因此,大力开展机泵节能改造,刻不容缓,利国利民。
4.6.4.2 风机、水泵调速运行的必要性
表19-4-63 风机、水泵调速运行的必要性

4.6.4.3 各类调速方式的比较
对于交流电动机拖动的工作机,其转速表达式通常可以写成
(19-4-27)
式中 nD——电动机转速;
i——调速装置输出/输入转速比;
iC——机械传动装置的转速比。
故 (19-4-28)
式中 f——电动机用电频率,Hz;
p——电动机极对数;
S——电动机转差率;
ST——调速装置转差率。
由式(19-4-28)可见,由交流电动机拖动的工作机转速调节由以下参数变化决定:
①改变电动机用电频率f,如变频调速;
②改变电动机极对数p,如变极调速;
③改变电动机转差率S,如定子调压调速、转子串电阻调速、串级调速;
④改变调速装置转差率ST,如电磁滑差离合器调速、液力偶合器调速、液黏调速离合器调速。
除液力偶合器和液黏调速离合器为机械调速方式外,其他均为电气调速方式。在电气调速方式中,电磁滑差离合器为独立的单体调速装置,其他均为控制电动机调速。变极调速、变频调速和定子调压调速,三者属于笼型电动机调速;转子串电阻调速和串级调速属于绕线型电动机调速。
表19-4-64为各类调速方式的比较,其中应用较为广泛的是变频调速和液力偶合器调速。
表19-4-64 各类调速装备技术经济性能比较

注:T为力矩,c为常数,n为转速。
4.6.4.4 应用液力偶合器调速的节能效益
表19-4-65 应用液力偶合器调速的节能效益

4.6.4.5 风机、泵类调速运行的节能效果
节能是一种相对概念,在完成相同产量情况下,乙比甲减少了能源消耗,则乙相对于甲就是节能产品。随着技术进步,节能产品的概念非一成不变的,风机、泵类调速运行的节能效果,是与节流调节的耗能比较的结果。所谓节流调节,就是用关小阀门开度提高管网阻力办法来调节流量。
不改变管网曲线,通过改变风机、水泵的转速从而改变特性曲线来进行流量调节的称为调速调节,调速调节能够节能,这是由离心式风机、水泵自身的特性决定的。
当离心式风机、水泵的转速从n改变到n'后,其流量Q、压头H及功率P的关系如下
Q'/Q=n'/n, H'/H=(n'/n)2, P'/P=(n'/n)3
即流量与转速的1次方成正比,压头与转速的2次方成正比,功率与转速的3次方成正比。由此可见,若风机、水泵等离心式机械的转速降低1/2,则功率降低为原来的1/8。许多变工况运行的风机、水泵,采用调速运行其节能效果相当显著。在图19-4-45中,当流量由Q1降至Q2,若用节流调节,所耗功率相当于OH2BQ2所围起来的面积,而采用调速调节,则所消耗功率相当于OH3CQ2所围起来的面积,两者比较,阴影斜线部分相当于节省功率,显然节能相当可观,而且流量调节幅度越大,节能越高。

图19-4-45 水泵节流调节与调速调节耗能比较
4.6.4.6 风机、泵类流量变化形式对节能效果的影响
表19-4-66 风机、泵类流量变化形式对节能效果的影响


4.6.4.7 调速型液力偶合器的效率与相对效率
液力偶合器特性之一是效率等于转速比(即η=i),不管是调速型还是限矩型液力偶合器均有此特性。但在谈及功率损耗则另有一番状况。对于恒力矩载荷的调速,相对损耗功率等于1减去效率(即,即最大损耗功率在i=0.33点,其值为全功率的0.67。对于风机、水泵(P∝n3)类型载荷,相对损耗功率
,最大值在i=0.66点,
(理论值),即最大损耗功率为额定功率的0.148倍。损耗功率值在i=0~0.97区间上呈正态分布规律,在i=0.66点有极值。在i=0和i=0.97处损耗功率极少。因此,风机、水泵在低转速比运行时,虽然效率不高,但因输入功率小,损耗功率很少,故仍有调速节能意义。
为了避免人们把风机、水泵调速运行中的损耗功率与效率等同看待,液力传动中特引入一个相对效率的概念。
额定功率与任意工况损失功率之差与额定功率之比称为相对效率,即
(19-4-29)
显然,最大损失功率工况(i=2/3),即为最低相对效率工况,此时
将代入上式,得最低相对功率
因此,与额定工况运行相比,液力调速的相对效率范围为0.852~0.97。
调速型液力偶合器与限矩型液力偶合器在运行中输入转速基本不变,在较低输出转速时它们的损耗功率有明显不同。这是由于外载荷的变化和工作腔充液量不同所致。限矩型液力偶合器在较低输出转速时工作腔充液量变化不很大(有部分工作液体泄入辅助腔),其泵轮从动力机仍吸收不小的功率,故有较大的损耗功率。而调速型液力偶合器则不同,在较低输出转速时,工作腔充液量较低,则泵轮从动力机吸收较小功率,损耗功率较小。调速型液力偶合器运行中相对损耗功率见表19-4-67,在额定工况i=0.97时,相对损耗功率PS/PH=0.029,i=0.66时PS/PH最大值为0.148,可见液力调速的功率损失并不很大,在低转速比的调速状态下仍有明显的节能效益。
表19-4-67 液力调速相对损耗功率状况

4.6.4.8 调速型液力偶合器的匹配
调速型液力偶合器与异步电机匹配使用,适用范围很广,归纳起来可适用于图19-4-46所示五类典型的载荷。调速型液力偶合器应用于不同类型载荷,会有不同的工作区域和调速范围。图中纵坐标TK=T/TH为相对力矩,T为载荷力矩,TH为额定转差率下偶合器输出力矩。各条细实线为在不同导管开度时偶合器的特性曲线。图中分为四个区域:Ⅰ、Ⅳ为启动区域;Ⅱ为调速工作区域;Ⅲ为超载区域。5条粗实线为各类典型载荷的特性曲线:曲线1为递增力矩曲线,力矩随转差率的上升而增加。例如输送高黏度液体的泵的特性曲线。曲线2为恒力矩曲线,例如带式输送机、斗式提升机的载荷特性。曲线3为递减力矩曲线,例如调压运行的锅炉给水泵载荷特性。曲线4为抛物线力矩曲线,例如无背压运行的透平式风机、水泵载荷特性。曲线5为陡降力矩曲线,例如恒压运行的锅炉给水泵载荷特性。

图19-4-46 调速型液力偶合器与各类载荷的匹配及调速范围(调节特性)
传动系统稳定运行的必要条件是液力偶合器某一导管开度的特性曲线与载荷特性曲线相交。两曲线交角越大,运行越稳定;接近平行则不稳定。交点的纵、横坐标值即为该工况点的相对力矩和转速比。
液力偶合器与某种工作机联合工作的调速范围,为在区域Ⅱ中该种工作机载荷曲线的横坐标的区间长度(即从最小转速比至额定转速比)。如图中抛物线力矩载荷(曲线4)的调速范围,一般为i=0.25~0.97(最大调速范围可达i=0.20~0.97)。恒力矩载荷(曲线2)调速范围i=0.4~0.97(最大调速范围i=0.33~0.97)。
通过对图19-4-46的分析,可得出如下结论。
液力偶合器的调速范围主要决定于载荷特性,液力偶合器自身因素影响较小。同一台液力偶合器对于不同特性的载荷,则有不同的调速范围。
调速范围的大小既决定于载荷特性,又决定于匹配状况。例如图19-4-46中曲线2若向上或向下平移(即变换工作机规格和改变匹配状况),会引起调速范围的改变。其他载荷曲线上、下平移时效果亦同。
曲线3、4、5所代表的载荷,在减小液力偶合器充满度、降低转速时驱动功率大幅度下降,与管路节流调节流量相比有明显的节能效果;而曲线1、2类型载荷在调低转速时不能降低能源消耗,即不节能。
液力偶合器的额定转差率决定于匹配状况。通常调速型液力偶合器额定转差率范围SH=1.5%~3%。其中SH=1.5%对应着传递功率范围下限值;SH=3%对应着传递功率范围上限值。在进行匹配时,为减小液力偶合器额定工况发热和减少冷却水的消耗(缺水地区此点尤为必要),应选液力偶合器规格稍大一些,则SH接近1.5%;若为了传递较大功率,应使TK高些,则SH大些。图19-4-46中的匹配使TK=75%,表明载荷力矩T仅为液力偶合器额定力矩TH的0.75倍,则运行中偶合器的转差率SH<3%。这意味着偶合器选得稍许大了些,这样可有较小的转差率,较宽的调速范围,较大的过载能力。
4.6.4.9 调速型液力偶合器的典型应用与节能
表19-4-68 调速型液力偶合器的典型应用与节能





4.7 液力偶合器可靠性与故障分析
4.7.1 基本概念
可定量描述的可靠性,是指系统、产品或零部件等在规定的条件下和规定的时间内,完成规定功能(无故障)的概率,一般称为可靠度。可以认为,可靠度是用时间尺度来描述的产品质量。可靠性工作是为了确定产品可靠性和如何获得产品的高可靠性这两个基本问题而开展的各种活动。可靠性活动贯穿于产品的设计、制造、检验、试验、环境处理,以及安装维修、运行操作等产品整个的寿命过程中,疏忽任何一个环节都可能降低它的可靠度。可靠性工程的根本任务是要采用一切措施,尽量减少和避免各类故障,尽可能地延长产品的使用寿命,提高产品的以时间(寿命)来度量的质量指标。故产品的故障(失效)分析和对策研究,应是可靠性工程的核心问题。
液力偶合器故障的分类见表19-4-69。
表19-4-69 液力偶合器故障的分类

4.7.2 限矩型液力偶合器的故障分析
液力元件的零部件大致有三大类:第一类是液力元件的专有零部件,由它们决定元件的特殊功能,如工作轮、旋转壳体、易熔塞等,此外工作介质也可归入此类;第二类是通用机械零部件,如轴类、连接盘、箱体、齿轮、齿轮泵等;第三类是标准件,如紧固件、橡胶密封件、轴承、压力表、温度表等。对限矩型液力偶合器来说,通用机械零部件极少, 故障往往是由专用件和标准件引起的,它们的故障模式主要有以下几种:
①漏油,输出功率达不到规定要求;
②滚动轴承损坏,一般是泵轮一侧的轴承损坏居多;
③泵轮和旋转壳体外表损坏;
④起不到应有的限矩作用,造成电机烧毁事故;
⑤花键损坏(滚键);
⑥造成减速器输入轴断轴事故。
漏油与输出功率不足是密切相关的。限矩型液力偶合器在不同充液量下有不同的传递功率能力,漏油会使工作腔充满度下降,势必引起传递功率不足。如果因骨架油封失效,将有滴油现象,容易发现。如若泵轮或旋转壳体因铸造质量缺陷而有微细渗油(出汗),则只能在高速旋转时才会出现,往往不易发觉,是一种潜在的失效因素,这种失效是渐发性的,可以通过停机补油恢复工作能力,因此后果一般并不严重。
此外,充液过多使电动机达不到额定转速或工作机卡死、负载过大等外部因素也会出现输出转速偏低的情况。漏油或充液量不足也可能使易熔塞经常熔化,这也是一种非正常工作状态。减速器输入轴断轴,主要是因其承担液力偶合器重量,在轴的危险断面引起的附加弯矩、剪力和工作扭矩。剪、弯、扭联合应力的主应力,对危险断面构成旋转中的交变应力。即使交变应力值不大,在高速转动中应力的交替变化,也易使危险断面发生疲劳断裂而最后断轴。有效的解决办法是不使减速器输入轴承担液力偶合器重量,而由电动机轴承受。
液力偶合器在运转中发生故障必须及时排除,不应拖延以致酿成事故。表19-4-70限矩型液力偶合器的常见故障及排除方法。
图19-4-47为限矩型液力偶合器“工作不正常”的故障树。故障树是一种特殊的倒立树状逻辑因果关系图,它十分直观和逻辑清晰。建故障树的基本方法是首先确定一个“顶事件”作为分析目标,它是一个不希望出现的事件。从它开始,在不断回答“怎么会引起这一事件”这个问题的过程中,寻找导致这一事件的原因,一直追溯到导致“顶事件”发生的各种原因,称这些基本原因为“底事件”或“原始事件”。在“顶事件”与“底事件”之间,可以有若干“中间事件”。所有这类事件都用一些约定的图形符号(GB 4888—2009)加以表示,并用一些直线和逻辑符号按它们之间的因果逻辑关系连接起来,形成一个倒树形的逻辑框图,就成为一般所称的“故障树”或“失效树”。如果各个“底事件”的发生概率可以得知,还可以根据故障树所确定的逻辑关系计算“顶事件”的发生概率,并由此确定系统的可靠度值。因此,故障树分析方法既可用于进行可靠性设计的定性评估,也是一种很有利于计算机使用的分析失效信息流的演绎分析方法。表19-4-71为故障树分析中使用的符号和名词术语。

图19-4-47 限矩型液力偶合器“工作不正常”的故障树
表19-4-70 限矩型液力偶合器的常见故障及排除方法

表19-4-71 故障树分析中的符号和名词术语(摘自GB 4888—2009)


4.7.3 调速型液力偶合器的故障分析
调速型液力偶合器的故障形式主要有:
①轴承损坏;
②调速系统故障;
③供油、润滑系统故障;
④叶轮损坏;
⑤严重漏油;
⑥输出转速降不下来。
漏油是调速型液力偶合器的常见故障之一,由于有油液的冷却系统、导管的调节等增加了漏油因素,故比限矩型液力偶合器更易出现漏油事故。漏油影响外观质量和污染环境,是用户十分关注的故障形式。对于运转工作质量的影响,不同结构形式的液力偶合器影响程度是不同的。对于油液循环呈闭式回路结构,油液的泄漏使工作介质数量减少,势必影响到最高输出转速的下降和调节特性的变化;而对于开式回路结构,少量的漏损不直接对液力偶合器的特性产生影响,油箱存油量的变化范围成为补偿环节。只要采取措施使油液的外漏变成内漏,从动力特性角度来说,泄漏对可靠性就不产生什么影响了。
表19-4-72为调速型液力偶合器的常见故障与排除方法,供用户在维护中参考。
表19-4-72 调速型液力偶合器的常见故障及排除方法




4.8 液力偶合器典型产品及其选择
液力偶合器典型产品按限矩型液力偶合器、调速型液力偶合器和液力偶合器传动装置三大类型加以展示。限矩型液力偶合器以静压泄液式、动压泄液式和复合泄液式三类加以介绍。
限矩型液力偶合器的选型主要依据工作机的功率和技术性能要求来确定。
①根据工作机的功率和转速确定规格大小。
②根据工作机的技术性能要求确定液力偶合器的结构形式,例如煤矿井下具有一定斜度的带式输送机应选择YOXFZS型较为合适。
③订购限矩型液力偶合器时应提供液力偶合器输入、输出端有关连接尺寸如孔(或轴)径、长度及键槽等,并应提供电动机型号、功率、额定转速及减速器型号等,以免订货有误。
4.8.1 静压泄液式限矩型液力偶合器
表19-4-73 YOXJ液力偶合器主要性能参数

注:工作机为连续工作制时,表中效率取较大值,而传递功率按较小值选取;若为间歇工作制时则表中效率可取较小值而传递功率按较大值选取。
表19-4-74 YOXJ液力偶合器结构尺寸 mm


注:1. 生产厂商:长沙第三机床厂、大连营城液力偶合器厂(除表中规格型号外还有YOXJA各规格)。
2. △—按客户要求设计;未列入表的原有连接形式继续生产,有特殊要求的请与生产厂联系。
3. 连接方式:A型—异端输入、输出直连型,同轴度要求高且需可靠定位;B型—异端输入、输出弹性板连接型,安装时允许有少量角位移(<1.5°);NZ型—内轮驱动带制动轮弹性块连接型,安装时允许有少量径向位移(<0.5mm)和少量角位移(<1.5°);T型—同端输入、输出型,适用T带、V带、齿形带、链轮等方式传动;MT型—异端输入、输出弹性联轴器连接型,安装时允许少量径向位移(<0.5mm)和少量角位移(<1.5°)。
4.8.2 动压泄液式限矩型液力偶合器
表19-4-75 动压泄液式限矩型液力偶合器(油介质)规格选用(传递功率) kW

注:此表用于根据液力偶合器的输入转速和传递功率选定规格大小,同一型号规格的液力偶合器水介质比油介质传递功率大15%左右,选型时应注意。括号中的规格为非标,不推荐选用。
4.8.2.1 YOX、YOXⅡ、TVA外轮驱动直连式限矩型液力偶合器
表19-4-76 YOX、YOXⅡ、TVA外轮驱动直连式限矩型液力偶合器技术参数

注:1. 对YOXⅡ560,()中的数据为电动机轴≥ϕ100时。
2. YOX即GB/T 5837—2008规定的YOXD。
3.生产厂商:大连液力机械有限公司、广东中兴液力传动有限公司、沈阳市煤机配件厂、大连营城液力偶合器厂、北京起重运输机械设计研究院、长沙第三机床厂。
4. YOX(YOXD)为动压泄液式偶合器的基本形式,由其可衍生多种其他型号产品。
5. YOXⅡ型为带式输送机专用配套产品。
6.TVA型为大连液力机械有限公司引进德国福伊特(VOITH)公司技术产品。
7.传递功率见表19-4-75。
4.8.2.2 YOXⅡZ外轮驱动制动轮式限矩型液力偶合器
表19-4-77 YOXⅡZ外轮驱动制动轮式限矩型液力偶合器技术参数 mm

注:1. YOXⅡZ是带式输送机专用的配套产品。
2. 生产厂商:广东中兴液力传动有限公司、沈阳市煤机配件厂、大连液力机械有限公司、大连营城液力偶合器厂、中煤张家口煤矿机械有限责任公司。
3. 传递功率见表19-4-75。
表19-4-78 YOXnz制动轮式、YOXp式液力偶合器技术参数


注:1.生产厂商:上海交大南洋机电科技有限公司。
2.订货须注明选用偶合器的输入、输出端孔径、长度、键宽、槽深、公差等数据和带轮的技术参数,制动轮可按用户制作。
3.表中产品的过载系数均为2~2.5,额定转差率≤4%。
4.8.2.3 水介质限矩型液力偶合器
水介质液力偶合器工作介质为清水或水基难燃液。其结构须有如下特点:①腔内钢铁构件须进行防腐蚀、防锈蚀处理;②滚动轴承与腔内水液须设隔离密封;③须设置易熔塞与易爆塞。
表19-4-79 YOXD***A水介质液力偶合器技术参数 mm

注:1. 生产厂商:中煤张家口煤矿机械有限公司。
2. 此类偶合器传动介质为水,适用于防燃、防爆、防油污染的工作环境,常用于煤矿井下。此类偶合器专用于刮板输送机。
表19-4-80 YOXsj水介质液力偶合器技术参数 mm


注:1.生产厂商:广东中兴液力传动有限公司。
2.传动介质为水,适用于防燃、防爆、防油污染的工作环境,常用于煤矿井下。
3.按GB/T 5837—2008规定,型号应为
表19-4-81 YOXA水介质液力偶合器技术参数 mm

注:1. 生产厂商:沈阳市煤机配件厂。
2. 表中规格分为平键、花键两种连接方式。
3. 按GB/T 5837—2008规定,型号应为
4. 传递功率见表19-4-75。
表19-4-82 YOXS水介质液力偶合器技术参数

注:1.生产厂商:大连营城液力偶合器厂。
2.传递功率见表19-4-75。
3.按GB/T 5837—2008,型号应为
表19-4-83 YOXS、TVAS水介质液力偶合器技术参数 mm


注:1. 生产厂商:大连液力机械有限公司。
2. 传递功率见表19-4-75。
3. 按GB/T 5837—2008规定,型号应为
4.8.2.4 加长后辅腔与加长后辅腔带侧辅腔的限矩型液力偶合器
表19-4-84 YOXY、YOXYS液力偶合器技术参数 mm


注:1. 生产厂商:大连液力机械有限公司、沈阳市煤机配件厂。
2. 加长后辅腔与加长后辅腔带侧辅腔者均可使设备延长启动时间、降低启动力矩,使启动变得更“软”,更柔和。
3. 传递功率见表19-4-75。
4. 图中轴孔内紧定螺栓为选配件。
表19-4-85 YOXV、YOXVS液力偶合器技术参数 mm


注:1.生产厂商:广东中兴液力传动有限公司。
2.加长后辅腔与加长后辅腔带侧辅腔者均可使设备延长启动时间、降低启动力矩、使启动变得更“软”、更柔和。
3.图中轴孔内紧定螺栓为选配件。
表19-4-86 YOXV、YOXVS型液力偶合器技术参数 mm

注:1.生产厂:大连营城液力偶合器厂。
2. YOXV、YOXVS均可使设备延长启动时间、降低启动力矩、使启动变得更软、更柔和。
3.传递功率见表19-4-75。
表19-4-87 YOXV、YOXVC液力偶合器技术参数 mm


注:1.生产厂商:中煤张家口煤矿机械有限责任公司。
2. YOXV、YOXVC均可使设备延长启动时间、降低启动力矩,使启动变得更“软”、更柔和。
4.8.2.5 加长后辅腔与加长后辅腔带侧辅腔制动轮式限矩型液力偶合器
表19-4-88 YOXYⅡZ、YOXYSⅡZ液力偶合器技术参数 mm

注:1.生产厂商:沈阳市煤机配件厂。
2. YOXYⅡZ、YOXYSⅡZ均为带式输送机专用配套产品,可使设备延长启动时间、降低启动力矩,使启动变得更“软”、更柔和。
3.传递功率见表19-4-75。
4.图中轴孔内紧定螺栓为选配件。
表19-4-89 YOXYZ、YOXYSZ液力偶合器技术参数 mm

注:1.生产厂商:大连液力机械有限公司。
2. YOXYZ、YOXYSZ均为带式输送机专用配套产品,可使设备延长启动时间、降低启动力矩,使启动变得更“软”、更柔和。
3.传递功率见表19-4-75。
4.图中轴孔内紧定螺栓为选配件。
表19-4-90 YOXVⅡZ、YOXVCⅡZ液力偶合器技术参数 mm


注:1.生产厂商:中煤张家口煤矿机械有限责任公司。
2. YOXVⅡZ、YOXVCⅡZ均为带式输送机专用配套产品,均可使设备延长启动时间、降低启动力矩,使启动变得更“软”、更柔和。
表19-4-91 YOXVⅡZ、YOXVSⅡZ液力偶合器技术参数 mm


注:1.生产厂商:广东中兴液力传动有限公司。
2. YOXVⅡZ、YOXVSⅡZ均为带式输送机专用配套产品,可使设备延长启动时间、降低启动力矩,使启动变得更“软”、更柔和。
3.图中轴孔内紧定螺栓为选配件。
4. YOXVSⅡZ图中序号7为轴承座。
表19-4-92 YOXVWZ(YOXVⅡZ)液力偶合器技术参数 mm

注:1.生产厂商:大连营城液力偶合器厂。
2. YOXVWZ(YOXVⅡZ)为带式输送机专用配套产品,可使设备延长启动时间、降低启动力矩,使启动变得更“软”、更柔和。
3.传递功率见表19-4-75。
表19-4-93 YOXVYZ液力偶合器技术参数 mm

注:1.生产厂商:大连营城液力偶合器厂。
2.加长后辅腔易拆卸式偶合器与制动轮式偶合器的组合,具有两种偶合器的特点。
3.传递功率见表19-4-75。
4.安装时,F尺寸一定要大于E尺寸,L2尺寸要足够,以保证偶合器顺利装拆。
5. d1、d2分别为输入、输出端尺寸。
4.8.2.6 加长后辅腔内轮驱动制动轮式限矩型液力偶合器
表19-4-94 YOXVFZ型液力偶合器技术参数 mm

注:1.生产厂商:大连营城液力偶合器厂。
2.加长后辅腔可使设备延长启动时间、降低启动力矩,使启动变得更“软”、更柔和。
3.传递功率见表19-4-75。
4.8.3 复合泄液式限矩型液力偶合器
复合泄液式限矩型液力偶合器为内轮驱动,既有动压泄液又有静压泄液,故称复合泄液。复合泄液既有静压泄液结构简单的特点又有动压泄液动态反应快速的优点。它只有泵轮、涡轮和外壳三支盘形构件,而无后辅腔外壳,故结构简单、轴向尺寸小、重量轻、过载系数低。输出端连接简便,轮毂可直接装入制动轮,且使两者总长度相同。输入端固连在电动机轴上,由其承担偶合器重量而非减速器承担,故可减免减速器断轴事故的发生。上述特点使其特别适合三支点浮动支承液力驱动单元的需要。
复合泄液式限矩型液力偶合器近年有较快的发展。
表19-4-95 YOXF、YOXFZ液力偶合器技术参数

注:1.生产厂商:北京起重运输机械设计研究院。
2. YOXFZ制动轮以螺栓紧固在轮毂上,卸掉制动轮即成YOXF偶合器,两者外形尺寸全同。
3. 表中质量不含制动轮。表中△、☆尺寸均由用户提供。
4.传递功率见表19-4-75。
5. d1、d2分别为输入、输出端尺寸。
6.特别适用于三支点浮动支承液力驱动单元。
表19-4-96 YOXFZ液力偶合器技术参数 mm

注:1.生产厂商:大连液力机械有限公司、沈阳市煤机配件厂。
2.表中YOXFZ代表着YOXF。YOXFZ制动轮以螺栓紧固在轮毂上,卸掉制动轮,即成YOXF液力偶合器,两者外形尺寸全同。
3.传递功率见表19-4-75。
4. d1、d2分别为输入、输出端尺寸。
表19-4-97 YOXF复合泄液式液力偶合器技术参数


注:1.生产厂商:长沙三业液力元件有限公司。
2.订货可带制动轮,则型号为YOXFD。YOXFD与YOXF外形尺寸全同。
3. d1、d2分别为输入、输出端尺寸。
4.特别适用于三支点浮动支承液力驱动单元。
表19-4-98 YOXF(MT)、YOXF(Z)液力偶合器技术参数 mm


注:1.生产厂商:长沙第三机床厂。
2.传递功率见表19-4-75。
3.联轴器安装要求:径向位移≤0.5mm;轴线角位移≤1.5°。
4.特别适用于三支点浮动支承液力驱动单元。
表19-4-99 YOXF、YOXL液力偶合器技术参数 mm

注:1.生产厂商:大连营城液力偶合器厂。
2. YOXF为复合泄液式,YOXL为立式外轮驱动液力偶合器。
3.传递功率见表19-4-75。
表19-4-100 YOXFP型液力偶合器技术参数 mm

注:1.生产厂商:北京起重运输机械设计研究院。
2.传递功率见表19-4-75。
4.8.4 调速型液力偶合器
调速型液力偶合器是一种依靠液体动能来传递扭矩,依靠导管伸缩或其他方式调节工作腔内充液量进行调速的柔性传动装置,它具有改善传动品质和调速节能的双重功能,优点突出,用途广泛,被国家八部委联合推荐为国家级节能产品。
4.8.4.1 出口调节安装板式箱体调速型液力偶合器
调速型液力偶合器广泛地应用于风机、泵类的传动,在应用中可获得如下优点。
①离心机械(风机、泵类)应用液力偶合器调速运行,节能显著,节电率达20%~40%。
②可使电动机空载启动,可利用电动机尖峰力矩启动载荷,提高电动机启动能力,降低电动机启动时峰值电流的延续时间,降低对电网的冲击,降低电动机装机容量。
③可使工作机平稳、缓慢启动,减少因难于启动而引起的故障。
④减缓冲击、隔离扭振,防止动力过载,保护电动机、工作机不受损坏。
⑤能协调多机均衡驱动,可实现顺序延时启动,功率平衡,同步运行。
⑥易于实现对工作机的自动控制。
⑦操作简便,便于维护,养护费用低。
⑧设备投资费用低,使用寿命长,可反复多次大修。
⑨结构简单可靠,无机械磨损,适应各种恶劣的工作环境。
表19-4-101 YOTGC调速型液力偶合器技术参数 mm


注:1.生产厂商:各厂家相同规格,型号各有差异,参数稍有不同。大连液力机械有限公司(YOTGC、GST、GWT)、沈阳市煤机配件厂(YOTGC)、北京起重运输机械设计研究院(YOTGC)、大连营城液力偶合器厂(YOTCB)、广东中兴液力传动有限公司(YOTCS)、大连创思福液力偶合器成套设备有限公司(YOTCG)、烟台禹城机械有限公司(YOTCG)、长沙第三机床厂(YOTCG)。
2.此类液力偶合器的额定转差率为1.5%~3%。用于T∝n2的离心式机械时,其调速范围为1~1/5;用于T=C恒扭矩机械时,其调速范围为1~1/3。
3. GST50、GWT58为引进英国技术产品。
4.防爆型的标记为在型号后加B。
表19-4-102 YOTGCD调速型液力偶合器技术参数 mm


注:1.生产厂商:各厂家相同规格,型号各有差异,参数稍有不同。大连液力机械有限公司(YOTGCD)、大连营城液力偶合器厂(YOTCD)、北京起重运输机械设计研究院(YOTPC)、广东中兴液力传动有限公司(YOTCP)、大连创思福液力偶合器成套设备有限公司(YOTCGP)、烟台禹城机械有限公司(YOTCGP)。
2.此类液力偶合器的额定转差率为1.5%~3%。用于T∝n2的离心式机械时,其调速范围为1~1/5;用于T=C恒扭矩机械时,其调速范围为1~1/3。
3.此类液力偶合器结构紧凑,外形尺寸较小,振动值较低。
表19-4-103 YOT箱体对开式调速型液力偶合器技术参数 mm


注:1.生产厂商:上海七一一研究所。
2.按GB/T 5837—2008规定,YOT应为YOTC。
3.此类液力偶合器的额定转差率为1.5%~3%。用于T∝n2的离心式机械时,其调速范围为1~1/5;用于T=C恒扭矩机械时,其调速范围为1~1/3。
表19-4-104 YOTFC调速型液力偶合器技术参数 mm


注:1.生产厂商:各厂家相同规格,型号各有差异,参数稍有不同。大连液力机械有限公司(YOTFC)、广东中兴液力传动有限公司(YOTCH)、大连创思福液力偶合器成套设备有限公司(YOTCHP)、烟台禹成机械有限公司(YOTCHP)。
2.此类液力偶合器的额定转差率1.5%~3%。用于T∝n2离心式机械时,其调速范围为1~1/5;用于T=C恒扭矩机械时,其调速范围为1~1/3。
表19-4-105 YOTCH调速型液力偶合器技术参数 mm


注:1.生产厂商:上海交大南洋机电科技有限公司。
2.结构紧凑,轴向尺寸较小。
3.按GB/T 5837—2008规定,型号应为YOTCH。
4.8.4.2 回转壳体箱座式调速型液力偶合器
表19-4-106 YOTHC回转壳体式调速型液力偶合器技术参数 mm


注:1.生产厂商:大连液力机械有限公司、北京起重运输机械设计研究院。
2.此类液力偶合器额定转差率1.5%~3%。用于T∝n2离心式机械时,其调速范围为1~1/5;用于T=C恒扭矩机械时,其调速范围为1~1/3。
表19-4-107 YOTCK调速型液力偶合器技术参数


注:1.生产厂商:广东中兴液力传动有限公司。
2.此类液力偶合器用于离心式机械时,其调速范围为1~1/5;用于恒扭矩机械时,其调速范围为1~1/3。
4.8.4.3 侧开箱体式调速型液力偶合器
表19-4-108 SVTL调速型液力偶合器技术参数


注:1.生产厂商:广东中兴液力传动有限公司。
2. SVTL系引进德国福伊特(VOITH)公司技术产品。
表19-4-109 YOTCL调速型液力偶合器技术参数


注:1.生产厂商:长沙第三机床厂。
2.侧开式箱体,结构简单紧凑,尺寸较小,质量较轻。
4.8.4.4 阀控式调速型液力偶合器
表19-4-110 YOTGF调速型液力偶合器技术参数 mm

注:1.生产厂商:两厂家生产,规格相同,参数全同,型号各有差异。大连液力机械有限公司(YOTGF)、北京起重运输机械设计研究院(YOTK)。
2.新近研发的新产品,结构紧凑,与各类调速型液力偶合器同规格相比,尺寸最小、质量最轻。
3.侧开式箱体,供油泵外置,便于拆装,并可根据设备对启动快与慢的不同需求,更换供油泵及其流量。
4.此类液力偶合器额定转差率1.5%~3%。用于T∝n2离心式机械时,其调速范围为1~1/5;用于T=C恒扭矩机械时,其调速范围为1~1/3。
5.按GB/T 5837—2008规定,型号应为YOTV。
4.9 液力偶合器传动装置
4.9.1 前置齿轮增速式液力偶合器传动装置
表19-4-111 YOCQZ液力偶合器传动装置技术参数 mm

注:1.生产厂商:大连液力机械有限公司。
2.表中*为输出最高转速,根据用户需要确定。
3.额定转差率为1.5%~3%,最高总效率≥95%。
4.用于T∝n2离心式机械时,调速范围为1~1/5;用于T=C恒扭矩机械时,调速范围为1~1/3。
表19-4-112 YOTFQZ液力偶合器传动装置技术参数

注:1.生产厂商:广东中兴液力传动有限公司。
2.按GB/T 5837—2008规定,型号应为YOCQZ。
表19-4-113 YOTZ液力偶合器传动装置技术参数 mm

注:1.生产厂商:上海七一一研究所。
2.按GB/T 5837—2008规定,型号应为YOCQZ。
3.额定转差率1.5%~3%。用于T∝n2离心式机械时,调速范围为1~1/5;用于T=C恒扭矩机械时,调速范围为1~1/3。
表19-4-114 YOCQA、OH46、OY55液力偶合器传动装置技术参数


注:1.生产厂商:沈阳鼓风机集团有限公司(原沈阳水泵厂)。
2.按GB/T 5837—2008规定,型号应为YOCQZ。
3.额定转差率1.5%~3%。用于T∝n2离心式机械时,调速范围为1~1/5;用于T=C恒扭矩机械时,调速范围为1~1/3。
表19-4-115 CO46液力偶合器传动装置技术参数


注:1.生产厂商:上海电力修造总厂有限公司,生产CO46、YOT51、YOT51A、YOT46-550各规格产品。
2.按GB/T 5838—2008规定,上述产品型号应为YOCQZ。
3.各规格参数请向生产厂索取。
表19-4-116 YOCQ500H液力偶合器传动装置技术参数 mm

注:1.上海交大南洋机电科技有限公司产品。
2.外形尺寸以供货时提供的实际外形尺寸为准。
3.按GB/T 5837—2008规定,型号应为YOCQZ。
表19-4-117 YOTFY液力偶合器传动装置技术参数

注:1.生产厂商:沈阳福瑞德泵业液力机械制造有限公司。
2.按GB/T 5837—2008规定,型号应为YOCQZ。
4.9.2 后置齿轮减速式液力偶合器传动装置
表19-4-118 YOCHJ、YOCHJJ液力偶合器传动装置技术参数 mm

注:1.生产厂商:大连液力机械有限公司。
2.型号标注示例:输入转速为1500r/min,输出最高转速为900r/min的YOCHJ650型液力偶合器传动装置标注为YOCHJ650/1500/900。
3. YOCHJJ650的第二个J为加装液力减速器的含义,其最大制动力矩为5500N·m。
4.此类液力偶合器传动装置的额定转差率1.5%~3%,其输出的最高转速(即型号中后一个*处标注的转速),根据用户需要确定,一般最小为输入转速的1/3。其最高总效率≥95%。
5.此类液力偶合器传动装置用于T∝n2的离心式机械时,其调速范围为1~1/5;用于T=C的恒扭矩机械时,其调速范围为1~1/3。
表19-4-119 YOTCHJ液力偶合器传动装置技术参数


注:1.生产厂商:广东中兴液力传动有限公司。
2.按GB/T 5837—2008规定,型号应为YOCHJ。
表19-4-120 YOCHJ液力偶合器传动装置性能参数 mm


注:生产厂商:大连创思福液力偶合器成套设备有限公司、烟台禹成机械有限公司。
表19-4-121 YOCH×××B、YOCH×××H型液力偶合器传动装置技术参数 mm


注:1.生产厂商:上海交大南洋机电科技有限公司。
2.按GB/T 5837—2008规定,型号应为YOCHJ。
3.外形尺寸以供货时提供的实际外形尺寸为准。
4.9.3 后置齿轮增速式液力偶合器传动装置
表19-4-122 YOCHZ液力偶合器传动装置技术参数

注:1.生产厂商:大连液力机械有限公司。
2.此为后置齿轮增速式液力偶合器传动装置,*号为输出最高转速,根据用户需要确定。
3.此类液力偶合器传动装置额定转差率1.5%~3%,最高总效率≥95%。
4.此类液力偶合器传动装置用于T∝n2离心式机械时,其调速范围为1~1/5;用于T=C恒扭矩机械时,其调速范围为1~1/3。
4.9.4 组合成套型液力偶合器传动装置
由调速型液力偶合器与增(减)速齿轮箱连接,安装在基础油箱之上,配以供油、润滑系统,构成组合成套型液力偶合器传动装置,便于制造、安装、拆卸,整套设备成本较低,只是尺寸稍大。
表19-4-123 YOCQ前置齿轮箱增速式组合成套型液力偶合器传动装置技术参数 mm


注:生产厂商:大连创思福液力偶合器设备有限公司、烟台禹成机械有限公司。
表19-4-124 YOCHJJ后置齿轮箱减速式组合成套型液力偶合器传动装置技术参数 mm


注:生产厂商:大连创思福液力偶合器成套设备有限公司。
表19-4-125 YOCHZ后置齿轮箱增速式组合成套型液力偶合器传动装置技术参数 mm


注:生产厂商:大连创思福液力偶合器有限公司、烟台禹成机械有限公司。
4.9.5 后置齿轮减速箱组合型液力偶合器传动装置[偶合器正(反)车箱]
偶合器正(反)车箱是石油钻机上常用的液力偶合器传动装置,与电动机或柴油机配套用以驱动钻井泵或其他设备。图19-4-48为偶合器正(反)车箱结构与传动原理,输入端与电动机或柴油机连接,输出端与钻井泵或其他设备连接。以前的液力驱动装置用的是液力变矩器,因其效率低、载荷大时冒黑烟,改用阀控式调速型液力偶合器,则传动效率高并减少油耗用量。

图19-4-48 偶合器正(反)车箱结构与传动原理
1—偶合器;2—中间轴;3—输出轴;4—供油泵;5—箱体;6—供油泵传动轴

图19-4-49 单机泵组偶合器正车箱传动示意
图19-4-49、图19-4-50为偶合器正、反车箱在钻井泵上的应用。两者减速箱结构不同,万向轴位置与转向均不同。表19-4-126所示为某型号偶合器正(反)车箱技术参数。

图19-4-50 单机泵组偶合器反车箱传动示意
表19-4-126 YOTZ(F)J700/750型调速型偶合器正(反)车箱技术参数

注: 1.生产厂商:大连恒通液力机械有限公司。
2.当外界温度低于-20℃ 时,应采用8号液力传动油。
4.10 国内外调速型液力偶合器标准情况与对照
迄今,尚无液力偶合器国际标准。已有国家标准的只有中国和苏联(ΓОСТ 17171—72液力偶合器型式与基本参数)。国际上著名的英国FLUIDRIVE公司和德国VOITH公司也只有技术规范而尚未构成正式标准。
从对比表的备注中折算的泵轮转矩系数(均折算成S=3.0%时的λB 0.97)来看,我国国标性能参数低于英国FLUIDRIVE公司技术水平,而高于德国VOITH公司、苏联国标ΓОСТ 17171—72的技术水平。
国内外调速型液力偶合器标准参数对比见表19-4-127。国内外几种典型调速型液力偶合器系列比较见表19-4-128。
中国YOTC为符合GB/T 5837—2008标准的调速型液力偶合器系列规格,小于560的规格为R20优先数系,与苏联ΓОСТ 17171—72相同;大于650的规格为R80/5优先数系,与英国FLUIDRIVE公司GST调速型液力偶合器系列、德国VOITH公司调速型液力偶合器系列基本相同,均为大规格档次较稀以便生产批量集中。苏联的系列中大规格档次较密。
表19-4-129为我国现行液力偶合器相关标准。
表19-4-127 国内外调速型液力偶合器标准参数对比

表19-4-128 国内外几种典型调速型液力偶合器系列比较 mm

注:表中带括号者为不推荐的暂时保留规格。
表19-4-129 我国现行液力偶合器相关标准
