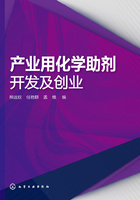
2.3 橡胶助剂
橡胶广泛用于交通运输、机械制造、土木建筑、医疗卫生、化工生产等各个行业。某些特种橡胶更是军工、国防和科技尖端事业的主要材料。
橡胶在硫化之前,其分子之间没有交联作用,缺乏良好的物理和力学性能,基本上没有实用价值。在橡胶加工过程中,添加助剂的目的主要有三:①经过热处理或其他方式使之产生交联,形成三维网状结构,能够承受拉伸和压缩应力,具有硬度和弹性等一系列的良好物理和力学性能;②便于制造过程的工艺操作,如具有一定的塑性、分散性、黏着力等;③在保证质量的前提下,降低成本。
现行的橡胶加工用添加剂,按用途分类如下:①橡胶硫化助剂,包括硫化剂(交联剂)、促进剂、活化剂和防焦剂等;②橡胶防护助剂,包括抗氧剂、抗臭氧剂、抗屈挠龟裂剂、光稳定剂、紫外光吸收剂、有害金属抑制剂、物理防老剂、防白蚁剂、防霉剂等;③橡胶补强助剂,包括炭黑、白炭黑、金属氧化物、无机盐、树脂等;④橡胶黏合助剂,间甲白体系和钴盐体系黏合剂和胶黏剂;⑤工艺操作助剂,包括塑解剂、增溶剂、增塑剂、软化剂、均匀剂、润滑剂、分散剂、增黏剂、隔离剂、脱模剂等;⑥特殊助剂,包括着色剂、发泡剂、消泡剂、增稠剂、膏化剂、湿润剂、乳化剂、稳定剂、凝固剂、热敏剂、抗蹼剂、防腐剂、保存剂、阻燃剂、抗静电剂和芳香剂等。
对橡胶助剂的基本要求是:①具有高度的分散性,粉状料的粒度愈细,可分散性愈好;②有一定的湿润性,增强黏着力;③原材料中不含或少含水分,含水量一般限制在1%以下;④清洁纯净,杂质尽可能少;⑤无毒,对人体无害。
橡胶助剂起源于天然橡胶的硫化。经过数十年的研究,直到20世纪20~30年代,随着硫化促进剂2-巯基苯并噻唑及其次磺酰胺衍生物以及对苯二胺类防老剂的工业化,橡胶助剂基本形成体系。国外橡胶助剂的生产相当集中,德国的拜耳公司和美国的孟山都公司是最主要的生产厂家。中国橡胶助剂(指有机助剂)的生产始于1952年。目前,橡胶助剂中,硫化促进剂和防老剂两类助剂的产量大约为生胶消耗量的4%。橡胶助剂主要是硫化剂、促进剂、活化剂、防焦剂、防老剂等。
2.3.1 应用目的及工艺
2.3.1.1 硫化剂
虽然橡胶具有很多优良性能,但生胶本身仍存在着很多缺点,单纯使用生胶不能制得满足各种使用要求的橡胶制品。所谓硫化是使橡胶线型分子通过硫化剂的“架桥”而变成立体网状结构,从而使橡胶的物理力学性能得到明显的改善。在一定条件下能使橡胶发生硫化的物质统称为硫化剂。
橡胶用的硫化剂不全是硫,其他的一些物质也可以作为硫化剂,一般分为无机和有机两大类。前一类有硫黄、一氯化硫、硒、碲等;后一类有含硫的促进剂(如促进剂TMTD,又名促进剂T)、二硫化双(N,N-四甲基二硫双硫羰胺、二硫化四甲基秋兰姆、福美双)、有机过氧化物(如过氧化苯甲酰)、醌肟化合物、多硫聚合物、氨基甲酸乙酯、马来酰亚胺衍生物等。橡胶硫化剂包括元素硫、硒、碲,含硫化合物,过氧化物,醌类化合物,胺类化合物,树脂类化合物,金属氧化物以及异氰酸酯等。用得最普遍的是元素硫和含硫化合物,该硫化剂属于对人体的有害物质。常见的工业硫黄的添加剂TMTD、TETD(化学名称:二硫化四乙基秋兰姆)等在硫化时可产生致癌的N-亚硝基二甲胺。目前铂金硫化剂(硫化温度低,硫化速度快)作为硅橡胶的硫化剂,在某些特殊产品中得到重要应用。硫化剂适用于各类天然橡胶和合成橡胶,根据需要,不同的硫化剂品种可配合使用。
硫化过程是个十分复杂的过程,但一般认为:硫黄分子在常态下是8原子的环状结构,溶于胶料中的硫黄在硫化温度下,在约30J/mol分子的能量作用下,即开环、生成链状的双基硫。根据不同条件,硫环断裂后可生成自由基(电子对均裂)或离子基(电子对异裂——得失电子)的双基性硫。实际上由于橡胶大分子双键上的极化作用,降低了开环能量,所以在140℃左右即可开环。双基性硫与橡胶大分子在双键处或α-碳原子处反应时,可能在一根分子链上生成“分子内的化合物”,也可能在两根分子链之间生成“分子间的化合物”,即产生交联。
总的规律是:随着硫黄量的增加,抗张强度、耐热性、耐溶剂性、耐水性均提高,而弹性、冲击强度下降,橡胶发脆。
2.3.1.2 硫化促进剂
凡能促进硫化反应的物质,均称为硫化促进剂,简称促进剂。在胶料中加入促进剂的主要作用是:①加快硫化速度,缩短硫化时间,降低硫化温度,提高生产率;对于含量很高的硬质胶料,促进剂的加入可缩短硫化时间一半以上。②提高或改善物理力学性能;对于硬质胶,使用促进剂也能提高强度,但不如软质胶的明显。③相应减少硫化剂(硫黄)用量,降低生产成本,由此引起的“喷硫”现象,保证制件的外观质量。所以,促进剂是胶料配方中不可缺少的材料之一。
橡胶硫化促进效能是衡量促进剂品质的重要标准,国内外对促进剂的表征主要从硫化促进特性和硫化胶的物理力学性能两个方面来进行。硫化促进特性主要考察的是硫化速度、门尼焦烧时间、正硫化时间、正硫化温度、过硫化阶段的硫化平坦性和抗硫化返原性等方面。而胶料的物理力学性能主要考察的是硫化胶的硬度、弹性、拉伸性能、摩擦性能以及热老化性能等。实际上,促进剂的效能取决于它所赋予胶的物理力学性能,而硫化胶中交联键的性质(类型和密度)对它的应用和工作特性起决定性作用。硫化胶的强度和动态力学强度不仅取决于聚合物链本身的性能,而且与总交联网中网络支承链的数量(指两个连接点之间的连接链)直接有关,交联密度决定着网络支承链的数量。据报道,硫化胶的硬度和定伸应力随着交联密度的增加而增加,撕裂强度、疲劳寿命、韧性和拉伸强度开始随交联密度的增加而增加,达到某一最大值后则随交联密度的增加而降低。滞后性能和永久变形特性则随交联密度的增加而降低。
2.3.1.3 硫化活化剂
能提高有机促进剂活性的物质,被称作硫化活性剂。活性剂具有充分发挥促进剂的效力,对硫化反应起活化作用,同时可以提高硫化胶的交联度和耐热性。活性剂作用:①加速发挥有机促进剂的活性和促进作用,减少促进剂用量,缩短硫化时间;②提高硫化胶的热稳定性,提高交联密度,减少交联键中的硫原子数。一般来说,在硫化体系中促进剂和活性剂是必不可少的。尽管这些助剂不属于交联剂范畴,但又和交联剂密不可分。
2.3.1.4 防焦剂
随着橡胶工业生产的发展和橡胶制品性能的提高,在加工过程中相继出现了橡胶生热量增大的问题。为了防止或延缓胶料在硫化前的加工和停放过程中发生早期硫化(“焦烧”),确保加工过程中的安全性,当调整硫化体系难以达到需要的操作安全时,现在普遍采用的方法是在工艺加工过程中添加少量的防焦剂(或称焦烧防止剂、阻滞剂),由此可以很简便地满足减缓胶料焦烧性能的要求,同时增加胶料或胶浆的储存寿命。防焦剂尽管配用量极少,但配入胶料后,对胶料性能或多或少有一些不良影响,因此一般尽可能不用。效果较好的防焦剂有N-亚硝基苯胺(防焦剂NDPA)和N-环己基硫化酞酰亚胺(防焦剂PVJ、CTP)等,前者用量0.3~1份,后者用量0.1~0.5份。最广泛采用的是氧化锌,用量3~5份。
胶料在储存和加工过程中因受热的作用会发生早期硫化(交联),并失去流动性和再加工的能力,这就是焦烧现象。胶料的焦烧是橡胶加工过程中常见的问题之一。特别是在具有现代特征的高温、快速、高效加工工艺中和配用容易引起焦烧的配合剂(如补强树脂、间甲白体系黏合剂、细粒子炭黑等),焦烧问题更容易发生。焦烧可以通过调整硫化体系解决,但要小心引起胶料性能的改变,可以通过冷却来改善胶料储存或加工条件,但需要复杂的装备。现在广泛认为,配用防焦剂是最为简单易行的防止焦烧的方法。因此,防焦剂成为橡胶加工安全的一个重要操作助剂。
2.3.1.5 防老剂
橡胶及其制品(主要指软质胶制品)在生产、使用及储存等过程中,经常产生性能自然变坏的现象,或者是变硬变脆,或者是软化发黏,失去弹性,不能使用。这种现象,被统称为“老化”。
橡胶老化的产生原因有许多方面,主要是由氧化而引起。为了防止橡胶及其制品的老化,常在生胶料中添加防老化剂——防老剂来延缓。防老剂分为物理防老剂和化学防老剂,前者加入橡胶后能在橡胶表面生成薄膜,保护橡胶及其制品不被氧化,如石蜡等物质;后者则可阻止或消除氧对橡胶的氧化作用,从而达到防止橡胶老化的目的,它们是多种多样的有机低分子化合物。
橡胶在热和氧的作用下,橡胶分子中与双键相邻位置上的碳原子所带的氢原子,或叔碳原子上的氢原子都很容易被氧夺走,使胶分子成为化学性质非常活泼的游离基R·及ROO·,这些游离基会自动袭击其他橡胶分子,并连续不断地(即连锁地)产生大量的R·、ROO·和ROOH,继而自动断裂生成许多低分子量的醛、醇、酯等物质,因而破坏了橡胶大分子的线型长链结构,破坏了橡胶的弹性。
抗氧化的化学防老剂一般都含有化学性质非常活泼的氢原子,其通式可用AH表示。当橡胶中有它存在时,则它的活性氢原子便能迅速与R·及ROO·等游离基结合而成为化学性质稳定的化合物,亦即及时阻止或消除这些游离基的生成,不使橡胶氧化的自动催化反应进行下去,从而起到阻止橡胶氧化的作用。
2.3.1.6 补强剂和填充剂
橡胶制品中使用的填料的种类很多,按其在橡胶中的主要作用可分为补强性填料和增容性填料。补强性填料的主要作用是提高橡胶制品的硬度和机械强度,如耐磨性、撕裂强度、拉伸应力、拉伸强度等,作为补强剂或活性填料。后者的主要作用则是增加胶料容积,从而节约生胶、降低成本,调整和改善结合剂及成型料的工艺性能,当然也具有一定的补强作用。特别是由于生胶的类型不同,也使补强剂和填充剂之间的界限难以划分。
根据填料的化学组成和形状可以将其分成粒状填料、树脂填料、纤维填料三大类。粒状填料是橡胶业中应用最广泛的一类,主要有炭黑、白炭黑和其他矿物填料,树脂是近年来发展起来的,主要是用于橡胶补强的一类填料,主要有改性酚醛树脂、聚苯乙烯树脂、木质素等。纤维类填料在橡胶中的应用也比较早,但不及前两类广泛,主要有石棉、玻璃纤维、有机短纤维(如聚酯纤维、聚酰胺纤维)等。采用纤维填料补强橡胶可获得良好效果,其硫化胶具有高拉伸强度及良好的动态性能,而且耐热、耐腐蚀、耐压缩变形性好;提高纤维和橡胶的黏合作用,即提高两者的结合力,是充分发挥纤维补强效果的关键。
在橡胶制品中,每一种填充剂的用量都有一个“填充极限”,在此限度内可以使制品的性能得到较好的改善和提高。如果超过此限度,制品的性能反而降低。例如:炭黑本是橡胶最好的补强填充剂,但其用量也不是愈多愈好,而总是有一个极限值或“峰值”,在峰值之前,随着用量增加,补强效果就增加,过极限峰值补强效果反而下降。一般橡胶制品中填充剂添加量只能加入50~60份,否则,会使成型料过于刚硬,难以进行包辊混料、磨碎、滚压成型及模压成型。
此外,对于填充剂的使用,也和其他助剂一样,常常是两种或多种并用,以使相互“取长补短”,特别是为了改善成型料的工艺性能,更需如此,反之,如单独使用一种填充剂,常常得不到理想的填充效果。例如:加入滑石粉可以提高成品磨具的耐热性能和有助于磨具表面粗糙度的改善,但是单独使用它时,会使结合剂及成型料混制时极易断裂、散碎。如果并用一些能增大胶料密实性的填充剂(如氧化铁等),就可改善上述性能。
2.3.2 技术发展趋势
进入21世纪,国内外橡胶加工助剂的发展趋势主要有以下几点:①高效、无毒、无污染、低成本成为产品的主要发展方向,防焦剂、对苯二胺类防老剂、新型催化剂已成为研究热点产品。②防老剂将向低(非)污染、不变色、长效方向发展;中间体对苯二胺类的清洁化生产工艺研究。对氨基二苯胺作为对苯二胺类防老剂的重要原料,其质量和成本直接关系到防老剂4020[N-(1,3-二甲基丁基)-N'-苯基对苯二胺]、4010NA(N-异丙基-N'-苯基对苯二胺)的性能、应用和推广。甲酰苯胺还原法、硝基氯苯与苯胺缩合法的生产过程污染严重,因此急需开发硝基苯清洁化生产对氨基二苯胺的新工艺。③新型硅橡胶、氟橡胶、丙烯酸酯类橡胶等生产中相应的助剂品种、体系的配套。氟橡胶、硅橡胶和丙烯酸酯类等新型橡胶应用前景广阔,但适于其生产的助剂及相关体系不匹配,这已制约了新型橡胶制品的发展。因此,进行相应的助剂品种及体系配套研究,将是今后橡胶助剂的一个发展方向。④随着致癌性萘胺防老剂、能分解出亚硝基胺类促进剂的禁用,无毒害、绿色环保型加工助剂普遍受到欢迎。
国内橡胶助剂目前存在问题:①助剂产品结构和品种结构不合理,质量参差不齐。例如为满足高温、快速、高效橡胶加工工艺要求,国外已大量使用高效次磺酰胺类促进剂(其用量已达到促进剂市场总量的55%),易制备、技术含量低的噻唑类促进剂的比例已降至28%。而国内恰好相反,噻唑类衍生物依然占据促进剂市场(约43%)主导地位。②生产规模小、主导助剂产品的研发滞后。随着市场竞争日趋剧烈,国际著名企业间实行兼并重组、依托科技求发展成为趋势。国内中小助剂厂家众多,技术研究力量薄弱、资金不足,已严重制约企业发展以及具有市场竞争实力的新型助剂的开发。③生产过程三废污染严重。④绿色贸易壁垒成为国产橡胶助剂及其制品出口的障碍,特别是涉及致癌毒性的萘胺类防老剂、能分解出亚硝基胺类的促进剂,在橡胶制品中已被西方国家禁用,但国内替代品的研发生产却相对滞后。⑤助剂生产的中间体、原料与产品发展不匹配。
国外橡胶助剂企业的生产能力和专业化水平更加突出,橡胶助剂的生产在国外长期集中在少数几家著名的化工企业中,近年来经过多次并购整合,形成了目前的世界4大橡胶助剂生产商:①富莱克斯公司。1995年由排名世界第一的孟山都公司和排名第四的阿克苏诺贝尔公司将其橡胶助剂业务合并成立橡胶助剂专业公司,产品包括防老剂、促进剂、不溶性硫黄和防焦剂等系列化品种,品牌为广大橡胶企业熟知。②康普顿公司。近年收购了世界著名的尤尼罗伊尔化学公司和Witco公司的橡胶助剂业务,极大地增强了其橡胶助剂核心业务。③LANXESS。LANXESS是由拜耳公司进行业务整合,将其有机中间体、橡胶助剂和聚合物部门等从核心业务部门中剥离出来成立的新公司,2005年1月在德国法兰克福上市。目前该公司员工约19600名,年销售额50亿欧元。该公司的助剂产品齐全,历史悠久,在西欧、美国等国家和地区都有极高的市场份额。④爱格富集团。爱格富是捷克第一大化工公司,也是原东欧最主要的橡胶助剂生产公司,生产促进剂、防老剂和防焦剂等多种助剂。其促进剂和对苯二胺类防老剂占全球市场份额的15%,其硫化促进剂CBS(或CZ,化学名称N-环己基-2-苯并噻唑次磺酰胺)、NS(或TBBS,化学名称N-叔丁基-2-苯并噻唑次磺酰胺)主要供应固特异、普利司通、米其林、倍耐力等世界著名轮胎生产商。
由上可以看出,国外公司通过强强联合进一步扩大了规模经济,并且形成了更加专业的跨国公司,其生产能力、科技开发能力和专业化水平都更加突出。与此同时,四大橡胶助剂生产商正在积极开发海外市场,特别是对中国市场更加关注和重视,加快了在中国建生产厂的步伐。在新产品的研究与开发方面的动向主要有以下几点。
(1)技术进步、技术创新需要大量的优秀科技人才,但橡胶助剂行业作为精细化工的一个分支,人才一直奇缺,企业的生产一般靠重复建设、扩大规模来实现效益的提高,技术创新能力差,人才培养机制不健全。因此有必要建立一个开放型的工程技术服务平台,采取请进来、走出去的方式,通过项目合作,把科研单位、大专院校、企业等一些优秀的专业技术人才聚集到一块,共同完成项目的研究开发和工程化集成,培养和造就一支具有创新意识、较强科技攻关能力、善于经营管理、勇于参与市场竞争的优秀科技人才队伍,从而实现人才的良性循环。
(2)整合人力资源,加强创新能力和研究开发,实现品种系列化与服务技术化,集合全行业优势,依托助剂行业研发能力,不断满足市场需要。
(3)橡胶助剂新产品的研发是我国橡胶助剂工业综合水平的体现,更是现代橡胶工业最经济、最关键的一环。我国橡胶助剂行业普遍存在着生产技术互相抄袭、缺乏新产品和新技术的开发能力、重复建厂的问题,自主创新能力严重不足,大多数企业只能生产有限的大路货产品,缺乏具有自主知识产权的新型产品,一些体现发展方面的关键技术还掌握在外国人手中,这使得我国橡胶助剂的生产企业有沦落为国外大型助剂生产商的廉价加工基地的危险,庞大的中国橡胶工业如果长期没有自主知识产权的橡胶助剂产品,将直接影响到橡胶工业的发展。我国橡胶助剂只有努力开发具有自主知识产权的产品,才能逐步走向良性发展,才能摆脱受制于人的局面。新产品的开发,可以从以下几个方面进行突破:①高效、多功能型的品种。防老剂重点发展长效、综合性能好的产品,如4020、RD(或抗氧剂224,化学名称2,2,4-三甲基-1,2二氢化喹啉聚合体)和DTPD(化学名称N,N'-二甲苯基对苯二胺)等,促进剂重点发展长效、硫化速度快、硫化性能好的产品,如次磺酰胺类产品NS、TBSI[化学名称N-叔丁基-双(2-苯并噻唑)次磺酰胺]、CBBS[化学名称N-环己基-双(2-巯基苯并噻唑)次磺酰胺]、XT580[化学名称N-(脂肪基代)苯并噻唑次磺酰胺]和DTDC(化学名称二硫化-N,N'-二己内酰胺)等。②低毒和无毒产品。随着人们环保意识的增强,越来越多的国家制定了一系列的规章制度和法律条文严格限制有毒有害物质的使用,因此橡胶助剂行业应重点发展低毒和无毒产品,以逐步淘汰那些有毒有害的产品。③低环芳烃和无锌助剂的开发。适应未来的国际发展趋势,加大开发低环芳烃产品力度,积极准备应对未来国外无锌助剂的要求,采取相应的对策,开发可替代的新产品。
(4)规范我国橡胶助剂行业产品标准体系,增强行业整体竞争能力。权威性的材料质量评价体系和相关技术法规、标准是进行产品生产活动的技术行为规范,是推广先进的科技成果、提高其生产水平的指导性文件,是提高产品质量、增强其国际市场竞争力的技术依据。
目前我国的标准大多是围绕加工生产制定的生产型标准体系,而发达国家的标准是针对市场有较强适应性的贸易型标准体系,目前我国的标准体系不能完全适应国际市场的需要。我国橡胶助剂行业标准化体系中的一些技术参数与要求尚未等效于国际标准,难以适应当今的全球化市场经济的需要,制约了我国橡胶助剂行业的发展及其产品的国际竞争力。
(5)应对国外贸易壁垒,积极准备应对措施。随着REACH法规的实施,对我国企业而言,目前最重要的工作是尽快在有关部门及商、协会的组织协调下,与上下游企业,尤其是与欧盟的客户进行沟通,弄清楚自己经营的化学品或下游制成品中的化学品是否需要注册,何时完成注册,并尽快按法规要求搜集注册所需数据和信息;开展GLP实验室认证,关注国际市场的发展动态,积极应对;密切关注欧盟的危险品名单和授权动态,做好产品转型准备。
2.3.3 现行主要品种简介
2.3.3.1 硫化剂
①硫黄。黄色固体物质,广泛应用于天然橡胶及部分合成橡胶中。常用的硫黄有硫黄粉、升华硫黄(又称硫黄华)和沉淀硫黄三种。硫黄不溶于水,稍溶于乙醇和乙醚,溶于二硫化碳和四氯化碳。它的特点是硫化橡胶耐热性低、强度高、对铜线有腐蚀作用,适用于天然橡胶和某些合成橡胶。在电线电缆橡胶配方中,硫黄用量大约在0.2~5份之间,但由于促进剂的加入,可使硫黄用量相应减少。
②金属氧化物。金属氧化物主要用于氯丁橡胶、氯磺化聚乙烯等的硫化剂,常用的有氧化锌、氧化镁、氧化铅、四氧化三铅等。
氧化锌,相对密度为5.6,是一种白色粉末,无毒、无味。氧化锌在橡胶中应用比较广泛,在通用型氯丁橡胶中常与氧化镁并用,作为主硫化剂。在天然橡胶及其他烯烃橡胶中,它可作为促进剂的活化剂,除此之外还兼有补强作用,在耐日光老化的橡胶中起屏蔽紫外线的作用。氧化锌在天然橡胶和丁基橡胶中的用量为5~10份,在氯丁橡胶中与氧化镁并用的一般用量为5份。
氧化镁,氧化镁在氯丁橡胶中作为副硫化剂使用,混炼时能防止氯丁橡胶先期硫化,能提高氯丁橡胶的抗拉强度、拉伸强度和硬度,能中和卤化橡胶等在硫化时或在其他氧化条件下所产生的少量硫化氢,对氯磺化聚乙烯橡胶能赋予其良好的物理力学性能,特别是永久变形比较小。但其耐水性较差,一般用量为3~7份。氧化镁为白色疏松粉末,相对密度为3.2,在空气中能逐渐吸收水分和二氧化碳变成碱式碳酸镁而使活性降低,故应严格密封保管。
③树脂类硫化剂。树脂类硫化剂主要是一些热固性的烷基酚醛树脂和环氧树脂。用烷基酚醛树脂硫化不饱和碳链橡胶和丁基橡胶,可显著提高硫化胶的耐热性。常用的主要品种是苯酚甲醛树脂,如叔丁基苯酚甲醛树脂和叔辛基苯酚甲醛树脂等。环氧树脂对羧基橡胶及氯丁橡胶均有较好的硫化效果,其硫化橡胶耐屈挠性好。
④秋兰姆。全名为二硫化四甲基秋兰姆,商品名为TMTD,是电线电缆橡胶中使用比较广的硫化剂,又可作硫化促进剂,纯品熔点为147~148℃,相对密度为1.29,为灰白色粉末。它是天然橡胶的超速促进剂,在100℃时可分解生成自由基,故可进行橡胶交联。使用秋兰姆作硫化剂可改善橡胶的耐热性和耐老化性能。其硫化曲线平坦,不易燃烧,适用于天然橡胶、丁苯橡胶、丁腈橡胶以及一切含有双键的不饱和橡胶。在一般的耐热橡胶中,秋兰姆的用量为2~3份;在连续硫化橡胶配方中,用量为2~5份;作促进剂用时,用量为0.3~0.5份。
2.3.3.2 硫化促进剂
目前使用的促进剂大都是有机促进剂,硫化促进剂中有的带苦味(如硫化促进剂M),有的使制品变色(如硫化促进剂D),有的有硫化作用(如硫化促进剂TT),有的兼具防老作用或降解作用(如硫化促进剂M)等。根据作用的速度,可分为:①超超速级,二硫代氨基甲酸盐、黄原酸盐类;②超速级,秋兰姆;③准超速级,噻唑、次磺酰胺类;④中速级,胍类;⑤慢速级,醛胺类、硫脲类。此外,还有后效性促进剂等,主要是含氮和含硫的有机化合物,有醛胺类(如硫化促进剂H)、胍类(如硫化促进剂D)、秋兰姆类(如硫化促进剂TMTD)、噻唑类(如硫化促进剂M)、二硫代氨基甲酸盐类(如硫化促进剂ZDMC)、黄原酸盐类(如硫化促进剂ZBX)、硫脲类(如硫化促进剂NA-22)、次磺酰胺类(如硫化促进剂CZ)等。按照酸碱性分类:①酸性促进剂,噻唑、秋兰姆、二硫代氨基甲酸盐、黄原酸盐类;②碱性促进剂,胍类和醛胺类;③中性促进剂,次磺酰胺类和硫脲类。一般根据具体情况单独或混合使用,有机促进剂主要作为氯丁橡胶、氯磺化聚氯乙烯橡胶、氯乙醇橡胶、聚丙烯酸酯橡胶用的促进剂,适于金属氧化物作硫化剂,尤以氧化镁、氧化锌作硫化剂时效果更好。在一般制品中用量为0.25~1.5份,在54-1(W)型氯丁橡胶耐水制品中用量为0.2~0.5份,并要配以10~20份的一氧化铅。
(1)橡胶硫化促进剂ETU(NA-22) 化学名称乙烯硫脲,其性状是:在乙醇中结晶的产品为针状结晶,从戊醇中结晶的产品为柱状结晶,相对密度1.42~1.43,熔点203~204℃,有苦味,易溶于水,溶于甲醇、乙二醇和吡啶,不溶于丙酮、乙醇、氯仿、汽油、甲苯等。
(2)硫化促进剂DETU 化学名称N,N'-二乙基硫脲,白色晶形料(颗粒),相对密度1.10,有吸湿性,易溶于丙酮、乙醇,溶于水,难溶于汽油。其促进效力低且抗焦烧性能差,对二烯类橡胶已很少使用,但在特殊情况下,如用秋兰姆硫化物等作为硫黄给予体时,其具有活性剂的作用。硫脲类促进剂对氯丁橡胶的硫化有独特的效能,可制得抗张强度、硬度、压缩永久变形等性能良好的氯丁硫化橡胶。DETU与NA-22相比,焦烧及硫化较快,但硫化平坦性较好,易分散、不喷霜,用量较大时,可进行高温高速硫化,特别适用于压出制品的连续硫化。其也是丁基胶用促进剂、三元乙丙橡胶的硫化剂,对于天然橡胶、氯丁橡胶、丁腈橡胶和丁苯橡胶有抗氧化作用,一般用作制造工业制品、特种电线、海绵制品等。
(3)硫化促进剂 MBT(M) 化学名称2-硫醇基苯并噻唑,是天然橡胶的中速促进剂,兼有增塑剂的功效,产品标准为GB/T 11407,系灰白色或淡黄色粉末,微臭,有苦味,无毒,相对密度1.42~1.52,初熔点170.0~173.0℃,易溶于乙酸乙酯、丙酮、氢氧化钠及碳酸钠的稀溶液中,溶于乙醇,不易溶于苯,不溶于水和汽油,储存稳定。其可用于天然橡胶与合成橡胶的中速硫化促进剂,兼有增塑剂的功效,具有宽广的硫化范围,可单独使用,或与二硫代氨基甲酸盐类、秋兰姆类、胍类和其他碱性促进剂并用。其主要用于制造轮胎、胶带、胶鞋和其他工业橡胶制品,因有苦味,不适用于食品工业橡胶制品;在氯丁橡胶中可作为硫化延缓剂,硫化临界温度低,易使胶料引起早期硫化。
(4)促进剂808(正丁醛苯胺缩合物) 棕红色或琥珀色黏稠油状液体,有特殊气味,闪点186℃,具有溶于苯、乙醇、丙酮、汽油等有机溶剂,不溶于水的优良特点,需隔绝空气储藏,适用于加压、蒸汽或热空气硫化的橡胶制品,制造承受高强度动态应力的高弹性橡胶制品,同时广泛应用于乳胶丝、绝缘漆(聚氨酯漆、聚酯漆、漆包线漆)等起到固化剂和促进剂作用。
(5)促进剂ZDEC(或ZDC、EZ) 化学名称二乙基二硫代氨基甲酸锌,白色粉末(颗粒),锌含量13.0%~15.0%,初熔点≥174℃,密度为1.66g/L,溶于二硫化碳、苯、氯仿、乙醇、乙醚,不溶于水和稀碱,储存稳定,可用于天然橡胶、合成橡胶及乳胶用超促进剂。含高ZDEC的乳胶可以使用一周而不致有早期硫化现象,是噻唑类促进剂的良好活化剂。ZDEC在混炼胶中有防老剂的作用,能改善硫化橡胶的耐老化性能,不变色、不污染、分散容易。
(6)促进剂ZDBC(或BZ) 化学名称二甲基二硫代氨基甲酸锌,ZDBC和ZDMC与ZDEC是同系物,其理化性能相似,但在锌含量、初熔点、密度等方面略有差别。特别是ZDMC,溶于稀碱、二硫化碳、苯、丙酮和二氯甲烷,微溶于氯仿,难溶于乙醇、四氯化碳、乙酸乙酯。ZDBC作为天然橡胶与合成橡胶用超促进剂以及乳胶用一般促进剂,特别适用于对压缩变形有要求的丁基橡胶和耐老化性能优良的丁腈橡胶,也适用于三元乙丙橡胶。ZDBC硫化温度100℃,低温时活性较强,焦烧倾向大,混炼时易引起早期硫化,在三元乙丙橡胶、丁基橡胶等制品中效果显著。使用ZDBC需氧化锌活化,也需加入硬脂酸,但硬脂酸用量大时有延迟硫化的作用。ZDBC用噻唑和次磺酰胺促进剂改性,可在很宽的硫化温度范围内使用。其作助促进剂时用量为 0.1~0.3份,作主促进剂时用量为0.25~2.0份,与噻唑类促进剂并用能提高制品的拉伸应力和回弹性,在胶乳胶料中一般用量为0.3~1.5份。
(7)橡胶防老增效剂MMBZ(或ZMTI、ZMMBI) 化学名称2-硫醇基甲基苯并咪唑锌盐,白色粉末,锌含量16.0%~18.0%,初熔点≥270.0℃,无毒、无臭,有苦味,可溶于丙酮、乙醇,不溶于苯、汽油、水,储藏稳定,主要作为非污染性防老剂品种之一,在性能上和防老剂 MBZ 相似,用于天然橡胶、丁苯橡胶、顺丁橡胶、丁腈橡胶等合成橡胶,抗热老化作用明显,通常和胺类、酚类防老剂并用时具有协同效应,提高制品耐热氧老化性能。其与促进剂M、DM 一起使用时,具有抑制有害金属的加速老化作用,通常用于透明橡胶制品,浅色和艳色橡胶制品。ZDBC在橡胶中易分散,无污染,是浅色、艳色及透明橡胶制品防护助剂的最佳选择品种之一,对混炼胶硫化特性的影响明显小于防老剂 MB,通常不必因使用ZDBC而调整硫化体系。ZDBC在天然胶乳发泡制品中可作辅助敏化剂使用,泡沫结构均匀,效果比 MB 好。
其他新型促进剂包括以下几种:TDEC(化学名称二乙基二硫代氨基甲酸碲)、TBZTD(化学名称二硫化四苄基秋兰姆)、ZBEC(化学名称二苄基二硫代氨基甲酸锌)、OTOS(化学名称N-氧二亚乙基硫代氨基甲酰-N'-氧二亚乙基次磺酰胺)、ZBPD[化学名称二硫代磷酸-O',O-二-碳(一至十四)-烷基酯锌盐]、ZMBT(或者MZ,化学名称2-巯基苯并噻唑锌盐)、TMTM(化学名称一硫化四甲基秋兰姆)、MBTS(或者DM,化学名称二硫化二苯并噻唑)等。
2.3.3.3 活化剂
能增加有机促进剂的活性,使之充分发挥效能,从而减少促进剂用量或缩短硫化时间的物质被称为硫化活化剂。活化剂作用是加速发挥有机促进剂的活性和促进作用,减少促进剂用量,缩短硫化时间,提高硫化橡胶的热稳定性,提高交联密度,减少交联键中的硫原子数。几乎所有的有机促进剂都必须加入活化剂,才能充分发挥其作用,活化剂仅以少量加入橡胶胶料中就能提高硫化度。在橡胶配方中,经常使用的活化剂一般分为无机活化剂和有机活化剂两类。无机活化剂主要有金属氧化物、氢氧化物和碱式碳酸盐等;有机活化剂主要有脂肪酸类、胺类、皂类、多元醇和氨基醇等。
(1)金属氧化物 常用的是氧化锌、氧化铅、氧化镉。氧化锌对电子的亲和能力强,所以对促进剂的表面吸附作用大,其活性作用也最强。氧化锌主要作为天然橡胶、合成橡胶的活化剂,颗粒细小,呈球状,具有很大的表面积,具有良好的分散性与良好的吸附性,因而能促进橡胶的硫化、活化,具有补强防老化作用,能加强硫化过程,达到稳定物性,加工安全性提高,大幅度降低不良率,提高橡胶制品耐撕裂、耐磨性。
(2)有机酸 由于氧化锌不溶于橡胶,故单独使用时,其活性作用不能充分发挥,而必须与硬脂酸一起使用,先产生能溶于橡胶的硬脂酸锌后,再发挥其作用,所以少量硬脂酸加入硫黄硫化的橡胶中,可以起到助促进剂的作用。
(3)胺类 大多数是高沸点的液体,目前橡胶制品不使用,具体型号品种如下。
①活化剂463。化学组成是2,2'-二硫代双(4,4-二叔丁基-3-甲基苯酚),是一种黄色至深褐色树脂状物质。在废天然橡胶中的用量为0.1%~0.4%,在废丁苯橡胶中为0.4%~0.8%,在废丁腈橡胶和氯丁橡胶中为0.7%~2.0%。
②活化剂420。化学组成是2,2-二硫代双(6-叔丁基对苯酚),是多烷基苯酚二硫化物的混合物,是一种深褐色黏稠液体。在天然橡胶、丁苯橡胶、丁腈橡胶和氯丁橡胶等废胶再生时的用量为1.0%~2.0%,在中性和微酸性介质中效率较高,在碱性介质中活性急剧下降。
③活化剂901。化学组成是多烷基芳香烃二硫化物,是一种黄褐色至深褐色油状液体。在天然橡胶、丁苯橡胶、氯丁橡胶和丁腈橡胶等废胶再生时的用量分别是0.5%~0.8%、0.8%~1.5%、2.0%~3.0%和2.0%~3.0%。其适宜在中性和微酸性介质中使用,在碱性介质中活性下降。
④活化剂MSP-S。化学组成是2,2-二硫代双(二甲基辛基苯酚),在常温下为棕红色胶状物,80℃时的流动性好。在天然橡胶再生时的用量为0.3%~0.4%,在合成废橡胶再生时的用量为2.0%左右。使用MSP-S时,最好选用松焦油类的酸性软化剂。
⑤活化剂WR-510。在常温下为稀稠状液体,可替代活化剂420和松香,在生产再生胎面胶时一般用量为0.5%左右,其他再生胶的用量为0.25%左右。
⑥活化剂B450。可替代活化剂420,一般用量为0.4%~0.5%左右,其特点是可使水抽法脱硫的时间缩短一半以下,降低工艺成本200~400元。
⑦活化剂6810(22-S)。化学组成是间二甲苯二硫化物,黄色油状液体。
⑧活化剂703。化学组成是二甲苯二硫化物,深褐色油状液体。
⑨活化剂2624。化学组成是2,4-异丙苯基苯酚二硫化物,是一种深褐色油状液体。
其他型号还有Z311、MJ、多功能硫化活化剂Struktol A-73等。
硫化活化剂一般是用两种型号的活化剂按质量比1∶1复配使用,与溶剂及其他组分的配方比例通常是:活化剂∶环己酮∶乙二醇乙醚乙酸酯∶二甲苯∶PU光油B-100=7∶4∶16∶15∶1.4。
2.3.3.4 防焦剂
防焦剂,又名硫化延缓剂,一般包括亚硝基化合物、有机酸类和次磺酰胺类等。任何防焦剂都应当符合橡胶加工性能要求,即具有优良的防焦性能;对不同促进剂和焦种选择性小;对其他配合剂不敏感;对胶料的硫化特性和硫化胶性能无不良影响;储存稳定和操作性能好;不结块、不飞扬、易分散、不喷霜;符合工艺安全和卫生要求。
①有机酸类。常用的有草酸、琥珀酸、乳酸、邻苯二甲酸酐、水杨酸、苯甲酸、油酸等,其中以邻苯二甲酸酐、水杨酸使用较多,如水杨酸、苯甲酸、邻乙酸苯甲酸、邻苯二甲酸酐。此类化学品防焦能力弱,对促进剂品种选择性大,会降低硫化速度和硫化胶性能,对皮肤有刺激作用。其中较常用的是邻苯二甲酸酐,可以用于浅色橡胶制品,而且仅对碱性促进剂DPG、MBT促进剂有效,对NOBS、TMTD无效。
②亚硝基化合物类。如N-亚硝基二苯胺、N-亚硝基-苯基-β-萘胺、N-亚硝基-2,2,4-三甲基-1,2-二氢喹啉聚合物,其中常用的是N-亚硝基二苯胺(NDPA)。与有机酸不同,该类防焦剂对常用的噻唑类和次磺酰胺类促进剂都有较好的防焦作用。
③次磺酰胺类防焦剂。该防焦剂是含有S—N键的一系列化合物,但这些物质影响成品的物理力学性能,不宜多用。
近年出现的新型防焦剂CTP(或PVI,化学名称N-环己基硫代邻苯二甲酰亚胺)有优良的防焦效果,通过掌握用量,可有效地控制焦烧时间。其物化性质如下:浅黄褐色结晶(从正庚烷中重结晶的产品为白色晶体),溶于丙酮、苯、甲苯、乙醚和乙酸乙酯,不溶于水,可溶于热的四氯化碳、乙醇和庚烷,可燃,低毒,可用于天然橡胶和合成橡胶,能有效地防止胶料在加工过程中发生焦烧,提高生产效率,同时对于已经经受高热或有轻微焦烧的胶料具有复原作用。防焦剂CTP广泛应用于可用硫黄硫化的弹性体,与各种通用促进剂并用都有良好的防焦效果,无论是开放或高温快速密炼,均可以采用一段混炼工艺而有效阻止焦烧,可以与促进剂M、DM、TMTD和有效或半有效硫化体系并用改善胶料性能,以提高压延和压出的生产效率。其有利于提高橡胶和镀黄铜钢丝的黏合,被广泛应用于各种通用型橡胶以及包括丁腈橡胶、乙丙或三元乙丙橡胶、丁基橡胶和氯丁橡胶等特种橡胶,储存时应避免过高或过低的温度和湿度,置于通风干燥处,避免受潮。
2.3.3.5 防老剂
橡胶用化学防老剂的品种也很多,已有100多种,但制造软弹性橡胶制品只用过防老化剂甲(又叫“防老剂A”)和防老剂丁(又叫“防老剂D”)两种。
①防老剂A(化学名称N-苯基-α-萘胺)。纯品为无色片状结晶,因含有甲苯胺及苯胺,故在日光与空气中渐变为黄褐色或紫色(但不影响效力),密度1.16~1.17g/cm3,熔点低于52℃,闪点188℃,易燃,可溶于汽油,不溶于水。防老剂A易溶于生胶中,防热氧化效果好。但是有毒性,常接触会刺激皮肤使之发炎,故生产使用不久,便改用防老剂D。
②防老剂D(化学名称N-苯基-β-萘胺)。防老剂D可用于天然橡胶和合成橡胶,对热氧化防护作用良好,并稍优于防老剂A。在生胶中易分散,但在生胶中溶解只有1.5%,比防老剂A差。故用量一般不超过2份,过多则会引起喷霜。
2.3.3.6 补强剂和填充剂
在橡胶制品(包括橡胶磨具)中,填充剂具有十分重要的作用。在实际工作中必须根据橡胶的种类、生胶的可塑性、结合剂中的含硫量、成型料的磨料含量、粒度以及成品的用途与要求等的不同,加以适当选择,并通过实际试验来加以确定。橡胶制品中常用的填料有炭黑、氧化镁、氧化锌、氧化铁、酚醛树脂、环氧树脂、碳酸镁、黏土、氧化钙、冰晶石、硬橡胶粉等。其中,炭黑是软橡胶结合剂的主要填料。
炭黑是天然气或石油产品不完全燃烧的产物。根据制造方法不同,可分为接触法炭黑(如槽法炭黑、混气炭黑和滚筒炭黑等)、炉法炭黑(如油炉法炭黑和气炉法炭黑等)和热裂法炭黑(如乙炔炭黑等);根据工艺性能和物理性能,可分为硬质炭黑和软质炭黑两种;根据所用原材料,可分为瓦斯炭黑、乙炔炭黑等。
在橡胶工业实际应用中,习惯以炭黑对橡胶的补强效果和加工性能来命名,如高耐磨炉黑(HAF)、超耐磨炉黑(SAF)、中超耐磨炉黑(ISAF)、快压出炉炭黑(FEF)、半补强炉炭黑(SRF)和细粒子热裂炭黑(FT)等。常用填充剂的技术指标见表2-3。
表2-3 常用填充剂的技术指标
