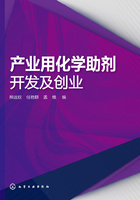
2.1 聚合物合成用助剂
合成塑料、合成纤维和合成橡胶都是以合成高分子树脂为基本组分的有机材料。高分子树脂是将具有反应活性的单体,经过本体、溶液、乳液以及悬浮等工程实施方法聚合得到的,在聚合工艺设计中,为了提高聚合反应的速率和选择性,控制聚合物的结构、分子量及其分布指数,使反应顺利进行,在不同的聚合实施方法中需加入不同功能作用的助剂。聚合物合成用助剂在聚合反应体系中用量很少,但作用却非常显著:既可改变聚合反应速率,提高转化率和收率,又可为聚合反应提供相适宜的介质条件,控制反应发生的场所和聚合产物的形态,使聚合反应顺利进行,还可调节聚合物分子的结构、大小和分子量分布,保障聚合物的设计功能。
聚合物合成用助剂包括引发剂、聚合催化剂、分散剂、乳化剂、阻聚剂、分子量调节剂、扩链剂、溶剂等。
2.1.1 应用目的及工艺
2.1.1.1 引发剂、聚合催化剂
①引发剂。在由单体合成得到聚合物的聚合反应中,能激起单体分子活化而产生自由基的物质,称为引发剂,指一类容易受热分解成自由基(即初级自由基)的化合物,在工程上可用于引发烯类、双烯类单体的自由基聚合和共聚合反应,也可用于不饱和聚酯的交联固化和高分子交联反应。自由基聚合的引发首先是产生自由基,最常用的是引发剂的受热分解或两组分引发剂的氧化还原分解产生的自由基,也可以用加热、紫外光照、高能辐射以及电解等方法产生自由基。此外是自由基与单体作用打开双键而形成另一个新自由基。生成的新的自由基可以与单体进行下一步增长反应。
由于引发剂的结构不同,在加热时分解生成初级自由基的速率不同。因此,引发剂种类的选择是基于所需要的最佳的聚合温度,当需要低温聚合时,则选用易分解的活性高的引发剂,能在较低温度下,具有足够高的分解速率。通常控制引发剂浓度在0.1mo1/L,其生成初级自由基的速率在10-7~10-6mol/L范围较合适。因此,要是聚合需在较高的温度下进行,则选用活性低的,在较高温度下能达到上述的分解速率。为此有不同类型的引发剂供不同聚合温度和条件下选用。在设计的聚合温度范围内,引发剂有适当的分解速率常数,不同的引发剂具有不同的分解速率,而且分解温度对于分解速率的影响也不尽相同。在高分子合成工业中,正确、合理地选择和使用引发剂可以提高聚合反应速率、缩短聚合反应时间,从而提高生产效率。
适宜作引发剂的是那些具有键断裂能量不超过104.5~167.2kJ/mol的化合物,破坏这些键,要求加热温度为50~150℃,这也是一般烯类单体自由基聚合的温度范围。工程上用作自由基聚合反应引发剂的化合物主要是过氧化物,其中大多数是有机过氧化物,还有偶氮化合物和过硫酸盐以及氧化还原引发体系。
从聚合的实施方法来区分,经典的乳液聚合发生的场所主要在乳化束“胶粒”内,所使用的是水溶性引发剂(反相乳液聚合则相反),如过氧化氢、过硫酸钾或过硫酸铵等;本体聚合、悬浮聚合及溶液聚合的引发中心在单体相或有机溶剂相中,因此应该选择油溶性引发剂,如有机过氧化物或偶氮化合物;如果用水作溶剂进行溶液聚合,则应选用水溶性引发剂。按照分解速率的需要选择引发剂,则要依据聚合操作方式和反应温度来确定:在连续聚合和间歇聚合工艺中,由于反应物料在反应区域的停留时间不同,控制聚合反应温度也要有所不同,这时就要根据引发剂的分解活化能或引发剂的半衰期做选择。在连续聚合反应过程中,引发剂的半衰期要远小于单体在反应器中的平均停留时间;而间歇聚合过程中引发剂的分解温度范围窄,应选用高活化能的引发剂,如要求引发剂缓慢分解,则选用低活化能引发剂。选用不同半衰期的引发剂进行复合,采用复合引发剂可使聚合反应在整个反应过程中保持在一定的速率下进行,从而缩短聚合反应周期。
②聚合催化剂。聚合反应用的催化剂与其他化学反应用的催化剂有所不同,它们不仅起到提高反应速率的效果,还是某些聚合反应必不可少的,即使不需要加快聚合速率也必须使用。例如:乙烯基单体、二烯烃单体、环氧类单体在阳离子、阴离子或配合催化剂作用下,可以经离子聚合反应和配位聚合转变为高分子量聚合物。环状化合物,如环醚、环酯、环酰胺、环烯烃、环硅氧烷等都要在催化剂激发下才能开环聚合。
按照工艺实施方法区分,对于催化剂的水/油溶性、催化效力等的考量,与上述引发剂的选择基本类同。
2.1.1.2 分散剂、乳化剂
①分散剂。在采用悬浮法生产高聚物时,为了使不溶于水的单体在机械搅拌下分散为油珠状液滴并悬浮在水相中,此时添加的物质称为分散剂或悬浮剂,其作用是在单体油珠表面形成一层保护膜,以保障聚合物微粒保持分散状态,防止结块。
在悬浮聚合法生产球状聚合物的过程中,为了防止早期液滴间和中后期聚合物颗粒间的并聚,必须添加能使单体均匀分散于水相介质的分散剂。在搅拌特性固定的条件下,分散剂的种类、性质和用量成为控制颗粒特性的关键因素。按传统习惯,悬浮聚合分散剂可分为水溶性高分子和非水溶性无机粉末两大类。粉末状无机分散剂主要用于甲基丙烯酸甲酯、苯乙烯等单体的珠状悬浮聚合,聚合结束后,吸附在聚合物珠粒表面的无机分散剂可以用稀酸洗去,保持聚合物制品的透明性。
②乳化剂。为使两种互不相溶的液体形成稳定的胶体分散体系而添加的物质,称为乳化剂。乳化剂的作用主要是降低连续相与分散相之间的界面张力,即降低界面自由能,使液滴聚集的能力大为降低,并在液滴表面上形成双电层或薄膜。由于相同的电荷相斥,从而阻止液滴的相互聚集,生成稳定的乳化液。乳化剂属于表面活性剂范畴,各自具有不同的亲水/亲油平衡(HLB)值,HLB值是衡量表面活性剂乳化效力的重要物性参数。在聚合物的合成过程中,只有乳液聚合工艺才使用到乳化剂,阴离子表面活性剂是应用最为广泛的乳化剂,它也常常与非离子型表面活性剂复配使用。连续相为水相、分散相为油相的乳化液被称为水包油型(O/W)乳化液,与之相对应的,连续相为油相、分散相为水相的乳化液被称为油包水型(W/O)乳化液,乳化液聚合在很多的情况下都是水包油型的乳化体系。
乳化剂的添加方式是先将它溶解/分散于溶性相同的液相中,然后在相近的温度和搅拌下与另一相混合/乳化。乳化剂的使用量必须高于其临界胶束浓度(CMC),一般是1%~4%(质量分数)。
2.1.1.3 阻聚剂、分子量调节剂、扩链剂
阻聚剂、分子量调节剂、扩链剂三者都是控制单体聚合活性和聚合产物分子量大小的添加剂,它们的使用目的是很容易理解的。
①阻聚剂。聚合用的某些单体分子中含有不饱和键,反应活性较高。为了保障它们在储存、运输或精制过程中稳定,不发生不可控的自发聚合,需要添加某些物质——阻聚剂。阻聚剂是极易与自由基形成稳定化合物的小分子化合物,能够有效阻止游离基的链式聚合反应。同时,某些聚合反应结束前也需要加入阻聚剂来终止聚合反应的继续进行,使其聚合度稳定。
根据抑制聚合反应的机理,将能终止每个自由基而使聚合反应停止,直到它们完全耗尽的物质称为阻聚剂或抑制剂,而只能使自由基活性减弱,减慢聚合反应速率,但不能终止反应的物质称为阻滞剂。
②分子量调节剂。能够调节或控制高聚物分子量和减少聚合物链支化的物质称为分子量调节剂,又称为调节剂或聚合调节剂,在乳化法制橡胶中经常采用。用作分子量调节剂的物质的链转移常数较大,在聚合体系中的用量,一般为单体质量的0.1%~1.0%(质量分数),它们可显著调节高聚物的分子量,缩小分子量的分布指数,从而改善高聚物的加工性能,提高产品应用性能。
③扩链剂。在纤维与聚氨酯橡胶的生产中,常使用某些含活泼氢的如醇类或胺类等化合物,使之与带异氰酸酯端基的预聚物反应,在其分子链上形成硬链段,并使分子链段扩展延长。因此,这类化合物被称为扩链剂。
扩链剂对高分子材料的回收及工程塑料的改性、提高高分子材料的品质和降低生产成本效果显著。在低特性黏度的缩聚物中添加扩链剂,添加量为1%~3%,其特性黏度值可提高30%,从而使回收塑料有更大分子量,使熔融黏度、力学性能、防水解性能以及产品切片的加工能力、生产效率均得到提高。扩链剂通常用于PC、PA、PET、PBT等聚酯类塑料及其再生利用,亦适用于多种塑料的共混回收利用及加工,减少产物的支链,从而提高树脂的热稳定性。
2.1.2 技术发展趋势
化学助剂行业发展的专业性越来越强。随着经济水平对于高分子材料要求的提高,新材料技术和化工产业的不断进步,高分子材料化学助剂产业整体呈现快速发展的态势,表现为化学助剂新品种的不断出现,需求数量的较快增长以及化学助剂性能的不断改进。化学助剂种类的日趋繁杂使得没有一家化学助剂企业能够经营所有类别的化学助剂,国际同行业巨头往往根据自身技术优势和经营特点选择几大类别的化学助剂进行生产经营,呈现出化学助剂行业发展的较强专业性。
中国化学助剂行业发展市场潜力巨大。中国在高分子材料领域的高速发展,使我国已成为全球高分子材料化学助剂需求的增长重心。良好的市场前景促使巴斯夫、DSM等国际高分子材料巨头纷纷将高分子材料产能向中国扩张或转移,进一步促进对高分子材料化学助剂的需求增长。
中国高分子材料化学助剂行业处于加速发展阶段。由于我国高分子材料化学助剂行业起步晚,行业的整体发展水平与国际水平还存有差距,表现为:企业单一经营/规模较小、具有新结构的助剂产品匮乏、化学助剂应用技术服务能力较差、行业集约化程度不够、产品未形成集约化规模经营、高端产品少、许多产品品种未形成系列化。最近十年,中国化学助剂行业呈现快速发展的态势,专业化、规模化、技术型企业不断出现和发展,部分企业已经在全球具有很好的知名度。尤其在抗老化化学助剂领域,中国企业已经形成与国际企业同台竞争的态势。同时中国化学助剂行业的多年分散发展,为国内优秀企业的产业并购、市场先期培育、技术积累创造了良好资源。
高效化、多样化、复合化、系列化、环保化已成为高分子材料化学助剂发展总的趋势。
(1)高效化 高效化是指在确定助剂用量的情况下实现效果最大化,主要途径为助剂的高分子量化。普通的助剂分子量较低,容易挥发、迁移、渗出,降低了助剂的效能,而高分子量化可降低挥发性、迁移性,提高热稳定性、耐水解能力、与材料的相容性,而使助剂的效能得以充分发挥。如受阻胺光稳定剂(HALS)高分子量化后不仅提高了热稳定性、相容性、耐迁移性、耐渗出性,还降低了毒性和扩大了应用范围。高分子量的抗氧化剂1010比低分子量抗氧化剂1076的耐迁移性、耐水解能力明显改善。
(2)多样化 高分子材料化学助剂的多样化不仅在于新品种的出现和应用高分子材料范围的扩大,更在于其作用途径的多样化。高分子材料化学助剂的功能是由其相应的官能团结构决定的:一方面,传统的官能团结构不断得到改进和完善,使产品序列不断丰富;另一方面,新的官能团结构不断被发现,使助剂发挥作用的途径呈现多样化。例如,碳自由基捕获物种的发现,促使材料抗氧体系由二元复合向三元复合体系发展,并产生更多的新型抗氧化剂品种。
(3)复合化 复合化是各种高分子材料化学助剂的共混,目的是令高分子材料化学助剂具有多功能性和增强协同效应,使应用简单方便。现代的复合技术已非初期的几种助剂简单混合,已发展成为多组分协同性能的研发,各组分之间协同机理的研究和协同组分的开发将是高分子材料化学助剂复合应用技术研发的关键。
如由高分子质量受阻胺稳定剂与具有高效热稳定性、金属离子螯合性的若干光稳定剂,采用偶合技术将不同结构的受阻胺稳定剂融合在一起,制成新型光稳定剂,不仅降低迁移速率,还发挥不同结构受阻胺稳定剂的协同效果,更增加耐受长期高热氧化降解的能力,性能优于其他通用的光稳定剂。
(4)系列化 系列化指通过对同一类助剂产品的结构和其应用性能发展规律的分析研究,本着高效化、环保化的基本要求,在全面的技术经济评价基础上设计同一类新结构的化学助剂产品。将系列化的新助剂产品的主要参数、类型、性能、基本结构等做出合理的安排与计划,以协调同类产品、配套产品和目标高分子材料之间更加合理的协同关系,从而充分发挥助剂产品的协同效应和协配性,获得更好的市场通用性。同时产品的系列化可使助剂制造商根据市场的动向和特殊要求,机动灵活地开发新品种,既能及时满足市场的需要,又可保持企业生产组织的稳定,最大限度地节约设计力量。
(5)环保化 随着环保法规日益严格和可持续发展的需要,环保化将成为化学助剂发展的重点。一方面是化学助剂制造过程的清洁生产工艺的开发,节能减排;另一方面是发展环境友好助剂,限制或禁止使用对人体和自然环境有毒有害的助剂。
2.1.3 现行主要品种简介
2.1.3.1 引发剂、聚合催化剂
(1)引发剂 自由基引发剂有多种分类方法,按引发剂的分子结构,可以分为偶氮类、过氧化物类和氧化还原类。也可以按照其溶解性能,分为水溶性引发剂(如无机类的过硫酸盐、过氧化氢、水溶偶氮引发剂等)和油溶性(溶于单体或有机溶剂)的有机类引发剂。可以按照引发剂的分解方式,将引发剂分为热分解型和氧化还原分解型两类。或者按照引发剂的使用温度范围,分为:a.高温(100℃以上)类,如烷基过氧化物、烷基过氧化氢物、过氧化酯等;b.中温(40~100℃)类,如偶氮二异丁腈、过氧化二酰、过硫酸盐等;c.较低温(0~40℃)类,如氧化还原引发体系。因此,应根据聚合反应的温度要求来选择引发剂。如果高温引发剂在中温范围使用,则分解速率过低,而使聚合时间延长;如果中温引发剂用于高温范围聚合,则分解速率过快,引发剂过早消耗,在低聚合转化率阶段就停止反应。
①偶氮类引发剂。偶氮二异丁腈AIBN是最常用的偶氮类引发剂,一般在45~65℃下使用,其优点是均匀分解,只形成一种自由基,无其他副反应,另一优点是比较稳定,可以纯粹状态安全储存,但80~90℃时也急剧分解;缺点是有一定毒性,分解速率较低,属于低活性引发剂,常用于自由基型加聚反应,如乙酸乙烯酯、丙烯酸酯、丙烯腈、氯乙烯单体聚合及其自由基反应的引发剂,泡沫橡胶、塑料(聚氯乙烯、聚烯烃、聚氨酯、聚乙烯醇、丙烯腈与丁二烯共聚物、氯乙烯共聚物、丙烯腈与丁二烯苯乙烯共聚物、聚异氰酸酯、聚醋酸乙烯酯、聚酰胺、聚酯)发泡剂,还可用作有机合成试剂。AIBN分解后形成的异丁腈(二甲基-氰基-甲基)自由基是碳自由基,缺乏脱氢能力,还能用作接枝聚合的引发剂。
偶氮二异庚腈(ABVN)是在AIBN基础上发展起来的活性较高的偶氮类引发剂,其引发速率高,有逐步取代AIBN的趋势。偶氮二异丁酸二甲酯(AIBME)引发性适中,更重要的是其聚合过程易控,产品转化率高,分解产物残渣易处理。
水溶性偶氮引发剂普遍适用于高分子合成的水溶液聚合与乳液聚合中。与一般类型的偶氮引发剂相比,水溶性偶氮引发剂引发效率高,产品的分子量相对比较高、水溶性好,且残留体少。水溶性偶氮引发剂是将原来的油溶性的有机引发剂(如偶氮二异丁腈)转变成为水溶性的,扩大了使用范围,若带有端基,还可以用于制备遥爪聚合物。将水溶性偶氮引发剂引发丙烯酰胺聚合,聚合温度为35~90℃,一般温度在40℃左右就可以,聚合时间平均在4h,得到的聚丙烯酰胺的分子量在1400万~1800万之间,产品的溶解性好。在阳离子乳液及功能高分子的制备中也有不俗的表现。
目前流行的偶氮引发剂产品有2,2'-偶氮双(N-2-甲氧基-2-甲基丙酰胺)(商品代号VA-057),英文名为2,2'-azobis[N-(2-carboxyethyl)-2-methylpropionamidine]hydrate,外观为微黄色粉末,可水溶,熔点97℃,在水中10h的半衰期分解温度为57℃,Wako公司的产品,规格25g的价格约780元。类似的引发剂还有:2,2'-偶氮双(N-丁基-2-甲基丙酰胺)、4,4'-偶氮双(4-氰基缬草酸)、2,2'-偶氮双[N-(2-羧基乙基)-2-甲基丙脒]n水合物、1,1'-偶氮双(环己烷-1-甲腈)、2,2'-偶氮双(N-环己基-2-甲基丙酰胺)、2,2'-偶氮双[2-(2-咪唑并啉-2-基)丙烷]、2,2'-偶氮双[2-(2-咪唑并啉-2-基)丙烷]二盐酸盐、2,2'-偶氮双[2-(2-咪唑并啉-2-基)丙烷]二硫酸二水合物、2,2'-偶氮双(4-甲氧基-2,4-二甲基戊腈)、(2RS,2'RS)-偶氮双(4-甲氧基-2,4-二甲基戊腈)、2,2'-偶氮双{2-甲基-N-[1,1-二(羟甲基)-2-羟基乙基]丙酰胺}、2,2'-偶氮双{2-甲基-N-[2-(1-羟基丁基)]丙酰胺}、2,2'-偶氮双[2-甲基-N-(2-羟基乙基)丙酰胺]、偶氮二异丁基脒盐酸盐、2,2'-偶氮双[N-(2-丙烯基)-2-甲基丙酰胺]、二甲基2,2'-偶氮双(异丁酸)。
②过氧化物类引发剂。过氧化合物的通式为R—O—O—H或R—O—O—R,可被看作是过氧化氢H—O—O—H的衍生物,R为烷基、酰基、碳酸酯基和磺酰基。由于取代基的不同,可得到不同类型的过氧化物,用作引发剂时,它们活性次序一般为:过氧化二碳酸酯类>过氧化二酰类>过氧化酯类>过氧化二烷基类。其原因是它们所连基团不同,过氧键的牢固程度也不相同:供电基团、空间位阻大的基团以及能提高分解产物的自由基稳定性的基团的引入都有利于过氧键的分解。
过氧化碳酸酯可以看成不稳定碳酸的衍生物,所以容易分解。过氧化碳酸酯可分为三类:一是过氧化二碳酸酯,二是过氧化碳酸酯,三是二过氧化碳酸酯。目前使用较多的是过氧化二碳酸酯,主要用于低温和中温引发,主要有过氧化二碳酸二异丙酯(IPP)、过氧化二碳酸二(2-乙基己酯)(EHPD)、过氧化二碳酸二环己酯(DCPD)、过氧化二碳酸二(4-叔丁基环己酯)。
过氧化二苯甲酰(BPO)按二步分解:有单体存在时,第一步均裂成的苯甲酰氧自由基可以引发聚合;无单体存在时,进一步分解成苯基自由基,并析出CO2,但分解并不完全。其他的有过氧化二(4-氯苯甲酰)、过氧化二乙酰、过氧化二(3,5,5-三甲基己酰)、过氧化二辛酰、过氧化二(十二酰)。完全对称的二酰基氧化物引发剂活性较高,就其化学结构而言,芳酰类比较稳定,过氧化酰类引发剂中α-H越少越稳定,二酰氧化物活性更高,一般单独使用。氧化苯甲酰在工业上广泛用作乙烯、丙烯酸、苯乙烯、乙酸乙烯酯、氯乙烯等单体聚合引发剂,还可以用作二甲基硅橡胶及合成橡胶的硫化剂,聚酯、硅树脂及不饱和聚酯的固化剂。
过氧化酯常见的主要是过氧羧酸的叔丁酯,因为伯醇和仲醇的过氧酸酯分解时不产生自由基,而进行离子分解。过氧化酯的分解速率介于过氧化二酰和过氧化二烷基物之间。
二烷基过氧化物主要用于高温引发(>100℃),常见的有过氧化二异丙苯、过氧化二叔丁基。按一级分解反应产生烷氧自由基,其分解速率一般不受溶剂影响。有机过氧化氢物可用于高温引发,主要有异丙苯过氧化氢。若加入亚铁盐作还原剂,可组成氧化还原体系。
无机过氧类引发剂易溶于水,多用于乳液聚合和水溶液聚合,主要有过硫酸盐(钾、钠或铵盐)。
由于过氧化物稳定性低,在制备和储存时应非常小心。为安全起见,市售的过氧化二苯甲酰往往含较多量的水分,在科研中最好取少量进行重结晶,纯化后再使用。过氧化物引发剂有氧化性,易使产品带颜色。
③氧化还原类引发剂。上述偶氮类和过氧化物类引发剂,其分解活化能都是在83.6~146.3kJ/mol,50~100℃才能较快分解,这就限制了它们在低温下使用的可能性。很多单体在低温下聚合可以避免支化、交联等副反应,从而获得质量较好的聚合物,因此,需要通过氧化还原反应产生自由基来适应这一要求。
氧化还原引发体系是利用还原剂和氧化剂之间的电子转移所生成的自由基引发聚合反应。由于氧化还原引发体系分解活化能(约40~60kJ/mol)很低,常用于引发低温(0~50℃)聚合反应。
在氧化还原类引发剂中,三丁基氢化锡通过参与反应来降低引发剂的分解温度。一般与AIBN联用。对于环化、偶联、卤代烃脱卤素反应,这种引发活力可归结于锡-碳原子与氢-卤素原子之间键能的差异(键能大小:Sn—H<Sn—Br,C—H>C—Br)。除三丁基氢化锡外,可与AIBN联用的试剂还有:三(三甲硅基)硅烷、苯硫酚、二苯基膦、三苯基锗烷+加压CO等。常用的氧化还原引发体系主要有以下几种。
a.过硫酸盐-亚铁氧化还原体系。这种体系由过氧化物或过硫酸盐、水溶性金属盐和辅助还原剂组成。这种体系由于生成硫酸可使pH值降低。此体系在丁苯乳液聚合中用得较多。
b.过硫酸盐-亚硫酸盐氧化还原体系。过硫酸盐-亚硫酸盐氧化还原体系应用非常广泛。常用的还原剂为亚硫酸盐、甲醛化亚硫酸氢盐(雕白粉)、硫代硫酸盐、连二亚硫酸盐、亚硝酸盐和硫醇等。该体系的特点是一个分子的过氧化物能够生成两个自由基,引发效率较高(但两个初级自由基如果不能迅速扩散分离,仍有发生偶合终止的可能)。生成的初级自由基易受氧的作用而破坏,所以聚合反应必须用惰性气体隔氧,尤其在反应初期。由于该反应体系形成硫酸,所以反应体系的pH值降低,因此在聚合中往往加入缓冲剂。这种引发体系常用于丁苯乳液聚合、乙酸乙烯酯乳液聚合、丙烯酸酯乳液聚合及丙烯酸酯和苯乙烯的多元共聚乳液聚合。
c.过氧化物-叔胺氧化还原体系。有机过氧化物-胺引发体系属于油溶性氧化还原引发体系,如过氧化苯甲酰和N,N-二甲基苯胺组合的氧化还原引发体系。其引发过程先形成极性配合物,然后分解产生自由基。这种氧化还原引发体系引发效率较低,而且N,N-二甲基苯胺的存在使聚合物泛黄,通常不用来合成线型高聚物,而用于分子内含若干双键的线型低聚物。如不饱和聚酯树脂的室温固化过程,此时,液态的不饱和聚酯树脂(通常加有苯乙烯单体)经自由基共聚合反应转变为固态的体型结构的高聚物。有机过氧化氢与芳香叔胺引发体系主要用于厌氧胶的引发。
d.过氧化氢与金属盐组成的氧化还原体系。
e.四价铈盐和醇、胺、硫醇等组成的氧化还原体系。
氧化还原引发体系除了上述几种类型外,还有由非过氧化物组成的体系,如铈盐与醇、醛、酮胺、硫醇等组成的氧化还原引发体系。这种氧化还原体系在淀粉、纤维素、聚乙烯醇等作主链的接枝共聚反应中用得较多。当用纯粹的水溶性过硫酸盐作接枝聚合引发剂时,随着引发自由基的产生,同时生成小分子自由基,常导致均聚物增多,接枝效率一般不超过50%。用铈盐等的氧化还原引发体系可使接枝效率达到90%。以含羟基聚合物的接枝反应为例,运用这种反应,可以对淀粉、纤维素、聚乙烯醇等进行接枝,以制取高分子吸水树脂及高分子絮凝物等。
(2)聚合催化剂
①阳离子聚合催化剂。阳离子聚合催化剂是一些能释放出质子或碳正离子的酸类物质,主要有如下几种。
a.质子酸,通过自身解离,释放质子进行引发。
b.路易斯酸,即广义的酸:AlCl3、BF3、SnCl4、ZnCl2、TiCl4等,它本身没有质子,不能引发单体聚合,常常加入微量的物质——质子给予体(有时称为助催化剂),如H2O、ROH、HX、ROR、RX等,是一类重要的阳离子聚合催化剂;路易斯酸进行引发反应的特点是先与上述微量物质形成配合物,释放出H+或碳正离子R+;必须注意,上述助催化剂使用量很小时即表现出显著影响,含量过多时,反而成为阻聚剂,务必控制其添加量。
c.其他能生成稳定有机阳离子的盐类,如:Ph3C+SbF6、C7SbF6、Et4N+SbCl6、n-C4H9EtN+SbCl6、(C6H5)3CCl、AgClO3等,其碳(氮)正离子犹如无机盐中的金属离子那样,原已存在于这些有机正离子盐中。缺电子的碳与烯烃或芳香基团与具有未共享的电子对(O、N、S)的原子共轭,使正电荷分散在较大的区域内,碳正离子的稳定性提高,但这种碳正离子的活性过小,只能引发较活泼的单体,如大多数芳香族类、N-乙烯基咔唑与乙烯基醚类等。
d.能引发某些单体做阳离子聚合的高能辐射线。在阳离子聚合中,反应介质的特性起重要作用,反应介质的溶剂化能力增加,聚合速度和聚合度也增加。如采用介电常数较小的溶剂,除使聚合速度减小外,还能观察到动力学级数的升高。
②阴离子聚合催化剂。阴离子聚合催化剂是一些碱性物质,或广义的碱,即能给出电子的物质——“亲核试剂”,大致可分为三类:
a.氨基钾(钠),可以使普通烯类单体苯乙烯、丙烯腈、甲基丙烯酸甲酯等很好聚合。
b.金属锂(钠)及有机锂(钠),可使二烯类单体聚合,所得到的聚合物为顺式或反式1,4的立体异构,且随所用溶剂的不同而变化。
c.醇钠(钾)等催化剂,可使环氧乙烷类单体进行开环聚合。
前两类聚合反应都属碳负离子聚合,后一类聚合反应属于氧阴离子聚合。
阴离子聚合是以阴离子为增长活性中心而进行的链式加成,其活性中心是阴离子而不是自由基,在许多阴离子型反应体系中,不存在自发的终止反应,属于活性聚合。具有以下的特点:ⅰ.合成聚合物的平均分子量可以以简单的化学计量来控制;ⅱ.调节引发与增长反应的动力学,可制得分子量分布非常窄(近似于泊松分布)的聚合物;ⅲ.通过把不同的单体依次加入活性聚合物链中,可以合成真正的嵌段共聚物;ⅳ.用适当的试剂进行选择性的终止,可以合成具有特定功能团的聚合物。
工程上实现阴离子聚合反应是有条件的,任何可能影响离子对形态、破坏催化剂的因素对聚合反应和产物的结构都有严重的影响,如阴离子型聚合对水含量极为敏感。因此,阴离子聚合绝不能用水作为反应介质,单体与反应介质中水的含量也应严格地控制在允许的范围之内;对于像醇、酸等其他带有活泼氢、O2和CO2一类能破坏催化剂,导致失去活性的杂质,其含量也应该严格控制在1×10-6级以下。
③配位聚合催化剂。由元素周期表中第ⅥB~Ⅷ族过渡金属化合物(如Ti、W、V、Ni、Co、Cr、Mo,通常是其卤化物),与元素周期表中第ⅠA~ⅢA族金属(如Al、Cd、Mg、Be、Zn、Li等)的烷基化合物或氢化物组成的催化体系常称为Ziegler-Natta催化剂,对α-烯烃聚合、二烯烃的聚合及环氧单体的开环聚合均有较高的活性,该催化剂体系属于配合结构,所以称为配位聚合催化剂。
为提高配合催化剂的活性,常在配合催化剂中加入第三组分,它们常含有给电子性的N、O和S等化合物。
将催化剂载体化,可以扩大催化剂的比表面积,增加活性组分的有效活性中心。所用载体大多数是镁的化合物,如MgO、MgCl2、MgSO4、Mg(OH)2、MgCl2·6H2O、MgCO3·Mg(OH)2·5H2O(碱式碳酸镁)等。
④开环聚合聚合催化剂。大多数杂环化合物,如环醚、环缩醛、环硫醚、环酯、环酰胺、环有机硅氧烷等均可在催化剂作用下开环聚合生成高聚物。开环聚合催化剂可以是离子催化剂,如OH-、OR-、H+或Na+、BF3等,也可以是中性分子,如H2O。配合催化剂也已广泛用于环状单体的开环聚合。
a.阳离子开环聚合催化剂。阳离子开环聚合催化剂主要包括质子酸和路易斯酸,一般用其进行聚合机理和动力学的研究。用于环醚阳离子开环聚合的主要有质子酸,如HBF4、HClO4、CF3COOH、CF3SO3H;路易斯酸,如BF3、SnCl4、AlCl3、SbCl5、Et3OBF4、Et3O+PF6、CF3SO3Et、Ph3CPF6、(PhCHOCH3)(SbCl)以及含铑化合物,路易斯酸催化阳离子开环聚合需要以H2O作为助催化剂;稳定的碳正离子盐,如(C6H5)3C+SbCl、烷基化剂或胺盐等。
b.阴离子开环聚合催化剂。碱金属的氢氧化物和醇盐可用来催化环氧化物进行阴离子开环聚合制得端羟基聚醚。一般常用的开环聚合催化剂有烷氧基碱金属化合物RONa、ROLi等,氢氧化物、氢化物、萘钠等碱性化合物以及酰胺、叔胺等有机化合物。这类催化剂的反应属于阴离子型逐步加聚反应,催化过程中容易发生链转移反应,导致分子量较低、产品分布较宽、不饱和度高等一系列缺点,影响产品性能。另外,聚合反应结束后,催化剂残留物必须从聚醚产物中分离出来。
20世纪80年代初,美国科诺科公司和联合碳化物公司将碱土金属化合物用作脂肪醇与环氧烷烃聚合的催化剂,得到的产物具有较窄的分子量分布和较低的小分子游离醇含量。由于碱土金属化合物的碱性低于碱金属化合物,因此可减少PO异构化的程度,从而降低聚醚多元醇的末端不饱和度。此类催化剂包括:乙酸钙、氢氧化钡、羧酸镁、复合金属氧化物及氢氧化物等。这类催化剂具有如下优点:催化机理与碱金属化合物相似,其工艺简单,易于工业化;有明显的窄分布效果;多元醇的不饱和度降低,反应可在较高的温度下进行,提高了反应速率,缩短了聚合周期;伯羟基含量较高。
c.分子型开环催化剂。H2O可用于环酰胺聚合,例如环己酰胺的开环聚合反应。
d.配位开环配合催化剂。环醚单体的阴离子或阳离子聚合很难获取高分子量的聚醚,而配位聚合能弥补这方面的不足。用于环醚聚合的配位催化剂种类较多,除锌、铝的化合物外,还有其他一些具有中等亲核性和较高路易斯酸性的化合物,如铁、镉、钴的化合物都是代表性的配位催化剂。另外,一些稀土元素的化合物也可用作配位催化剂。大部分配位催化剂是双组分或三组分的,通常包含一种烷基金属化合物和一种含活性氢的化合物,如水、醇(硫醇)、酚、酸及胺类等。按照组分的不同,大致可分为:Fe(Ⅲ)催化剂;以烷基金属为基础的催化剂;烷氧基铝催化剂;双金属催化剂;其他催化剂等。
Fe(Ⅲ)催化剂是发现得最早的氧化烯烃配位聚合催化剂,首次报道的环氧烷烃开环聚合的配位催化剂是由Pruitt和Baggett发现的Fe3+系催化剂,主要有Fe(OR)3/H2O等体系,Colcough和Borkovec分别对Fe(OR)3/H2O催化剂活性中心的结构进行了研究,认为它是催化剂部分水解后形成的配合物。
烷基金属催化剂主要有AlEt3、Al(i-Bu)3、ZnEt2、MgEt2、CaEt2等,其本身活性很低,但与别的物质形成配合物或螯合物时,活性极高。该催化剂主要分为2类:烷基铝、烷基锌体系;金属卟啉体系。
烷基铝、烷基锌体系催化剂主要指烷基铝与一些改性组分,如水、醇、酸及胺等组成的催化剂。它是氧化烯烃配位聚合中最为常用的一类催化剂。目前,已工业化生产的氯醚橡胶及环氧氯丙烷橡胶均采用该类催化剂制备。烷基铝为路易斯酸,本身也可引发氧化烯烃的阳离子聚合,但其催化活性低且只能得到分子量低的聚合物。后来研究者提出了烷基铝/水体系和烷基铝/磷酸2种催化体系,显著提高了活性。同时,Furukawa等也提出了以烷基锌为基础的催化体系。用烷基铝、烷基锌体系催化剂获得的聚合物往往表现出较宽的分子量分布,这意味着催化剂缔合体活性中心的多样性。从聚合反应的结果来看,这两类催化剂有以下特点:聚合过程中增长链与引发剂(催化剂)之间的链转移较慢,导致聚合物的分子量和链末端基团难以有效控制;存在多个活性中心;有较好的立体定向性;催化剂用量大,即催化效率低,一般情况下加入1g催化剂,聚合物产率低于100g。因此,无论是从技术的角度还是成本的角度,这两类催化剂都不适用于开环催化。
20世纪70年代末,人们发现金属卟啉配合体系对环氧化物的开环聚合具有催化作用。这类催化剂主要由有机配体(卟啉及其衍生物)、中心金属离子及与其结合在一起的亲核性富电子基团组成。金属卟啉配合体系虽然在合成窄分布高聚物方面效果较好,但反应速率慢,将路易斯酸与卟啉体系结合,显著加快某些反应的反应速率。由于金属卟啉配合物在反应中的不稳定性,近年来,除设计位阻型卟啉外,还出现了高分子负载型卟啉,具有潜在的应用前景。
Jacobs和Dubious等研究发现,烷氧基铝(如异丙氧基铝)作为催化剂时,环氧烷烃聚合反应行为明显有别于上述讨论的烷基铝系催化剂。在特定的反应条件下,这类化合物表现出“真正的催化作用”,即催化剂中的一个金属中心原子能产生许多条分子链,如反应体系中存在少量醇类时,聚合物活性链的总数是该醇和异丙氧基铝分子数的总和。也就是说,聚合物的分子量可由单体与醇和异丙氧基铝的物质的量比例来调节,且聚合物具有较窄的分子量分布,这使得制备带官能团的聚醚产物(如多元醇)成为可能。尽管烷氧基铝催化剂中不存在碱性的活性中心,但在该催化体系下生成的聚合物还是含有一定量的不饱和端基。
双金属氰化物(DMC)催化剂最早由美国轮胎橡胶公司发现,是一种用于开环聚合的新型高效催化剂,可用于生产聚醚多元醇、聚酯多元醇和聚醚聚酯多元醇。相对于传统的KOH催化剂,用DMC催化剂催化生产的聚醚多元醇具有较高的分子量和较窄的分子量分布以及较低的不饱和度。经General Tire & Rubber公司、Shell公司、旭硝子公司及ARCO公司多年的研究与应用表明,Zn3[Co(CN)6]2和Zn3[Fe(CN)6]2是进行环氧化物开环聚合最活泼、最有效的双基金属氰化配合物催化剂。目前,就国外环氧化物开环聚合催化剂的发展而言,Zn3[Co(CN)6]2与二甘醇二甲醚或H2O形成的配位复合配合物催化剂的研究和开发最为活跃。
Ziegler-Natta催化剂同样可用于环状单体的开环聚合,而且在工业上的意义越来越重要。
2.1.3.2 分散剂、乳化剂
①聚合分散剂。悬浮聚合体系是热力学不稳定体系,需要靠分散剂和稳定剂使系统稳定。分散剂的作用一是可以降低水的表面张力,使单体更易于分散成小液珠;二是吸附在液珠的表面,保护液珠在相互碰触时不至于合并、黏结、分散不良。工业上一般是同时使用阴离子型和非离子型两种分散剂复合协调起作用,同时添加pH缓冲稳定剂。
从相对于聚合介质的溶解性而言,分散剂可分为水溶性高分子和不溶于水的高分散性无机粉末两种类型。这种水溶性高分子中同时具有亲水基团和亲油基团(但不属于经典的表面活性剂,譬如乳化剂),这种双亲结构使分散剂分子彼此之间呈定向排列,稳定地分布在单体相与水相的界面层上,形成凝胶保护层,从而保证单体液滴呈分散状态,防止聚合产物相互黏结。不溶于水的高分散性无机粉状物,其分散机理是粉状物被水润湿后,存在于单体液滴之间,当两个液滴靠近时,界面被粉状物隔离而阻止黏结。分散剂的最低用量应该能够完全覆盖单体液滴的界面,通常为水量的0.1%~1%(质量分数),具体数量要依据悬浮聚合产物颗粒的粒径要求而增减。
目前,市场上的水溶性高分子分散剂仍然以聚乙烯醇为主,技术发展方向是根据所设计的聚合产物性能,如吸油性、分子量大小及其分布等开发具有不同分子量、醇解度、黏性指数等的PVC。无机分散剂正逐步向功能化和精细化方向发展,具体而言就是向研发小粒径(粒径0.1~10μm)、窄粒径分布(分布系数1~2)、大比表面积(比表面积50~500m2/g)及球形、多孔结构发展。
②聚合体系用乳化剂。一般以水为溶剂的乳液聚合体系组成如下:水质量占乳液体系的60%~80%,单体为乳液油相的20%~40%,一般采用水溶性引发剂,其用量为单体的0.1%~1.0%,若采用氧化还原体系引发剂可使聚合反应在低温下进行。乳化剂占单体量的2%~10%,时常需使用分子量调节剂(如十二烷硫醇、异丙醇等)来调节聚合物的聚合度,并可减少聚合物链的支化,调节剂的用量一般为单体量的0.1%~5%。同时,为了有利于引发剂的分解和保持乳液的稳定,还要添加适量的pH缓冲剂(如磷酸盐等),用以调节和稳定介质的pH值。
通常而言,对乳化剂的选择,是根据乳化对象和工艺要求来确定的,乳化剂(或者复合乳化剂)的亲水-亲油平衡(HLB)值是选择乳化剂的首要依据;乳化剂在被乳化物中易于溶解时,乳化效果较好;乳化剂的憎水基团一定要与被乳化物有很好的亲和力,且与被乳化物结构越相似时,两者间的亲和力越强,不但乳化力强,而且乳化剂的用量也可以减少,乳化液的稳定性也越高;因为阳离子型乳化剂与乳液粒子带有同种电荷而相互排斥,一般易获得稳定的乳化液。
在乳液聚合体系中,乳化剂虽然不直接参加化学反应,但它却是最重要的组分之一。乳化剂的种类和浓度将直接影响引发速率及链增长速率,也会决定聚合物性能、聚合物的分子量及分子量分布,以及影响与乳液性质有关的乳胶粒浓度、乳胶粒的尺寸及尺寸分布等。乳化剂选择是否合理,不仅涉及乳液体系是否稳定,生产过程能否正常进行以及其后的储存及应用是否安全可靠,而且也关系到聚合物的成本。
乳化剂的HLB值仅供选择乳化剂时参考,因为它既不能确定所需乳化剂的浓度,又不能确定所生产的乳液的稳定性,但从实践中知道对于甲基丙烯酸甲酯的乳液聚合,HLB值为12.1~13.7的乳化剂可获得较为稳定的胶乳,HLB值为11.8~12.4时适用于丙烯酸乙酯的乳液聚合,甲基丙烯酸甲酯与丙烯酸乙酯共聚(各50%)选择HLB值时,11.95~13.05的乳化剂较为恰当。
阴离子表面活性剂对电解质的化学稳定性较差,生成的胶乳微粒的粒度较小,胶乳稳定性好,聚合过程中不太容易产生凝聚块。因此使用阴离子表面活性剂时易得到固含量高而稳定的胶乳。非离子表面活性剂对电解质的化学稳定性良好,但聚合反应速率较慢,所得微粒粒径较大,聚合过程中易产生凝聚块。由于以上特点,工业生产中乳液聚合主要使用阴离子乳化剂或阴离子乳化剂与非离子乳化剂混合的乳化剂,很少单独使用非离子乳化剂。混合乳化剂中提高非离子乳化剂的比例可提高胶乳对电解质的化学稳定性,并增大胶乳微粒的平均粒径。混合乳化剂形成的胶束,其分子数小于阴离子或非离子乳化剂两者单独形成的胶束,因而使产品胶乳微粒分布加宽。
在一般聚合过程中,乳化剂的用量应超过其临界胶束浓度(CMC)值,还与聚合物的分子量、单体用量、要求生产的胶乳粒子的粒径大小等因素有关。其用量一般为单体量的2%~10%,增加乳化剂用量,反应速率加快,但回收未反应单体时,容易产生大量泡沫,使操作处理困难。因此,通常用量是在单体量的5%以下,甚至少于1%。
阴离子表面活性剂是乳液聚合工业中应用最为广泛的乳化剂,通常是在pH>7的条件下使用。重要的有:脂肪酸盐R—COOM,例如肥皂(硬脂酸钠)、松香酸盐C19H29COOM(例如歧化松香酸钠);烷基硫酸盐ROSO3M,例如十二醇硫酸钠;烷基磺酸盐R—SO3M,例如十六烷基磺酸钠;烷基芳基磺酸盐。
在乳液聚合工业中很少使用阳离子型乳化剂,原因在于胺类化合物具有阻聚作用或易于发生其他副反应,例如可被过氧化物引发剂转化。因此工业上要求制取正电荷的胶乳时,通常先用阴离子或非离子型表面活性剂作为乳化剂进行聚合反应,聚合完成后,搅拌下小心地加入阳离子表面活性剂溶液,使之转化为微粒外层具有正电荷的胶乳。
用离子型表面活性剂形成的胶乳粒子外带静电荷,能够阻止粒子聚集,所以胶乳的机械稳定性高,但遇到酸、碱、盐电解则易产生破乳现象,因此胶乳的化学稳定性较差。
非离子型表面活性剂一般可分为两类:聚氧化乙烯的烷基或芳基酯或醚类,环氧乙烷和环氧丙烷的共聚物。聚氧化乙烯的烷基或芳基酯或醚类,烃基的碳原子数大约为8~9;n值为2~100,一般为5~50。环氧乙烷和环氧丙烷的共聚物的分子量通常为2000~8000,其中环氧乙烷组分占40%~80%。乳液聚合时,选用非离子型表面活性剂所得胶乳粒子较大。要求降低胶乳微粒粒径时,聚合过程中可加少量阴离子型表面活性剂。
乳液聚合过程中通常用的乳化剂是拉开粉、十二烷基硫酸钠、乳化剂OP、乳化剂EI等。
拉开粉为阴离子型表面活性剂,又名拉开粉BX、渗透剂BX,化学组成是二异丁基萘磺酸钠。由丁醇、精萘在硫酸存在下发生缩合反应,再用发烟硫酸磺化,然后用氢氧化钠中和,最后用次氯酸钠漂白、沉降、过滤得到。
十二烷基硫酸钠是一种白色至微黄色结晶粉末,也属于阴离子型表面活性剂,又叫AS、K12、发泡粉。十二烷基硫酸钠盐即月桂醇硫酸钠(SDS),具有良好的乳化、起泡、发泡、渗透、去污和分散性能。由十二醇(月桂醇)和氯磺酸在40~50℃下经硫酸化生成月桂基硫酸酯,加氢氧化钠中和后,经漂白、沉降、喷雾干燥而成。或者在32℃下将氮气通过气体喷口进入反应器,同时通入月桂醇,再将液体三氧化硫通入闪蒸器,然后将硫酸化产物急骤冷却,打入老化器,促使上述反应完全均匀,最后用碱中和。当pH值至7~8.5时出料即得液体成品,喷雾干燥得固体成品。
乳化剂OP-10是烷基酚与环氧乙烷的缩合物,又叫烷基酚聚氧乙烯醚,属非离子型表面活性剂,是乳化剂OP系列里的一种型号。国外相应商品名分别为Igepal CA-630、Triton X-100或Igepal CO-630等,国内也称TX-10。乳化剂OP-10的主要用途是用作合成纤维油剂、漂染中的扩散剂、匀染剂、油田起泡剂、湿润剂、缓凝剂、泥浆活化处理剂、工业净洗剂、橡胶乳化剂等。乳化剂OP-10一般是表面活性剂与矿物油和油脂的混合物,其主要成分是由辛基酚或壬基酚在氢氧化钠(或钾)催化下,与环氧乙烷发生缩聚反应制得。
乳化剂EI是由非离子型表面活性剂与阴离子型表面活性剂复配而成的复合乳化剂,其外观是浅黄色微黏液体,pH值为6~7,对一般酸碱稳定。
2.1.3.3 阻聚剂、分子量调节剂、扩链剂
①阻聚剂。为了避免烯类单体在运输、储藏等过程中发生聚合,往往会向单体中加入少量阻聚剂,在使用前再将它除去。阻聚剂在聚合过程中产生诱导期(即聚合速度为零的一段时间),诱导期的长短与阻聚剂含量成正比,阻聚剂消耗完后,诱导期结束,即按无阻聚剂存在时的正常速度进行。一般,阻聚剂为固体物质,挥发性小,在蒸馏单体时即可将它除去。阻聚剂对苯二酚能与氢氧化钠生成可溶于水的钠盐,所以可用浓度为5%~10%的NaOH溶液洗涤除去,氯化亚铜和三氯化铁等无机阻聚剂也可用碱洗除去。
a.酚类阻聚剂。多元酚及取代酚是一类应用广泛、效果较好的阻聚剂,但必须在单体中溶解有氧时才显示阻聚效果,其阻聚机理是酚类被氧化成相应的醌、与链的自由基结合而起阻聚作用。在酚类阻聚剂存在下,使过氧化自由基很快终止,确保在单体中有足够量氧,可以延长阻聚期。
b.醌类阻聚剂。醌类阻聚剂是常用的分子型阻聚剂,用量0.01%~0.1%便能达到预期的阻聚效果,但对不同的单体阻聚效果存在差异。对苯醌是苯乙烯、乙酸乙烯有效的阻聚剂,但对丙烯酸甲酯和甲基丙烯酸甲酯仅起缓聚作用。醌类的阻聚机理可能是醌与自由基进行加成或歧化反应,生成醌型或半醌型自由基,再与活性自由基结合,得到没有活性的产物。每一分子对苯醌能终止的自由基数大于1,甚至达到2。将四氯苯醌、1,4-萘醌等加入含苯乙烯的不饱和聚酯树脂中能起到良好的阻聚作用,提高储存稳定性;四氯苯醌是乙酸乙烯的有效阻聚剂,但对丙烯腈无阻聚效果。
c.芳烃硝基化合物阻聚剂。芳烃硝基化合物的阻聚效果不如酚类,只适用于乙酸乙烯、异戊二烯、丁二烯、苯乙烯,但对(甲基)丙烯酸酯类没有阻聚作用,硝基苯通过与自由基生成稳定的氮氧自由基而起阻聚作用。
d.无机化合物阻聚剂。无机盐通过电荷转移发挥阻聚作用,氯化铁阻聚效率高,并能按化学计量1∶1淬灭自由基,硫酸钠、硫化钠、硫氰酸铵能用作水相阻聚剂。
e.氧气的阻聚作用。氧气分子有两个未配对的电子,常被视为双自由基,能起阻聚和引发双重作用,低温时则起阻聚作用。氧气能与交联剂的自由基和大分子链自由基反应生成活性低的过氧化自由基,在室温或稍高温度下都不能引发共聚合反应。这种氧的阻聚作用使不饱和聚酯树脂与空气接触的表面固化不完全而发黏。但在高温时,氧与自由基生成的过氧化物自由基能分解成活性较高的自由基,从而引发聚合反应。当氧在单体中的溶解度达10-3mol/L时,就有强烈的阻聚作用。如:盛装厌氧包装胶的容器不能装得太满就是保障容器内有足够量的氧气,阻止进一步聚合而使储存稳定,有些聚合体系中需要通入惰性气体以避免氧的阻聚作用。
选择阻聚剂品种时,除了要求其具有较高的阻聚率,还应考虑阻聚剂在单体中的溶解度,与单体的适应性(以便采用蒸馏或化学方法在聚合反应之前除去)以及价格等因素。最好选择是在室温下稳定,在设计的反应温度下能迅速分解起阻聚作用,这样就可以减少麻烦,不必从单体中脱除,又能保证聚合反应顺利进行,还要求阻聚剂的残留不影响聚合物的物理力学性能和产品外观。
在工程应用中,通常采用几种阻聚剂配合使用,以提高阻聚效果。例如,在不饱和聚酯树脂聚合时,加入对苯二酚、叔丁基邻苯二酚和环烷酸铜3种阻聚剂,对苯二酚活性最强,在与苯乙烯和聚酯混溶时可耐高温(130℃左右),在1min内不起共聚作用,可以安全混合稀释。叔丁基邻苯二酚在高温下阻聚效果很差,但在稍低温度(例如60℃)时,其阻聚效果比对苯二酚高25倍,可有较长的储存期。环烷酸铜在室温下起阻聚作用,但是高温时又有促进作用。另外,在富氧氛围下,对叔丁基邻苯二酚和吩噻嗪、对苯二酚和二苯胺混合使用,其阻聚效果比任一种单独使用时高约300倍。阻聚剂用量要适量,过多则有害无益。例如,碘的用量在4~10mol/L时具有阻聚效果,但超过此量却会引发聚合反应,而且碘一般不单独使用,需配以少量碘化钾,增加溶解度,提高阻聚效率。
目前,工程上使用较多的阻聚剂是多元酚类、芳二胺类、醌类、硝基化合物、亚硝基化合物、有机硫化合物等。添加量一般依据单体的自聚合活性高低确定,范围约0.01%~0.1%(质量分数)。其中,TMHP0(代号ZM-701,化学名称2,2,6,6-四甲基-4-羟基哌啶氮氧自由基),还有对羟基苯甲醚(MEHQ,代号ZJ-705)、氮氧自由基吩噻嗪(代号PTZ)、N,N-二正丁基二硫代氨基甲酸铜等是常用的高效阻聚剂。2,6-二硝基对甲酚添加在苯乙烯精制系统中,可防止苯乙烯聚合。二乙基羟胺在乙烯基单体中也常作为自动聚合形成共轭烯烃的高效阻聚剂,是丁苯乳液聚合过程非常优异的终止剂,也是不饱和油类及树脂的抗氧化剂,还是光敏树脂、感光乳剂、合成树脂的良好稳定剂。
②分子量调节剂。在加成型的自由基聚合中,链转移常数较大的物质会引起链转移反应发生,形成支化型高分子,可以通过添加量的多少和添加时机来控制分子量。因此,容易引发链转移反应的化合物就是自由基聚合的分子量调节剂,也叫链转移剂。在缩合聚合中,用来调节聚合物分子量的物质往往是与原料单体具有相同官能团的单官能团或多官能团的化合物,在高分子合成行业里又分别称为“封端剂”或“支化剂”。常用的链转移剂是硫醇类化合物,如月桂基硫醇、巯基乙酸酯等,新近开发的α-甲基苯乙烯二聚体可以作为替代硫醇的高效分子量调节剂,同时还避免了硫醇类的难闻气味和毒性。黄原酸衍生物、仲醇和叔醇等也可以用作乳液聚合的分子量调节剂。涤纶和尼龙树脂合成中常用的封端剂是乙酸,对合成聚碳酸酯则常用苯酚作为分子量调节剂。
在自由基聚合过程中,调节剂引发链转移后,会形成一个新的自由基,这种自由基仍然有引发活性,不影响聚合反应速率。在本体聚合中,油溶性调节剂能够很均匀地溶于聚合体系中,不存在调节剂的浓度差和扩散快慢而导致对聚合反应的影响。乳液聚合为多相体系,反应开始时,所加入的调节剂溶解在单体液滴中,聚合反应的场所在乳胶粒中,调节剂分子只有从单体液滴中扩散到乳胶粒内后才能起到调节作用。对二烯类单体的乳液聚合,加入调节剂可减少支化和交联,改善聚合物的性能。
从工程学的角度而言,如果过程属于化学反应控制的,调节剂能够得到及时供应,分子量调节作用可以有效发挥。但是如果过程是扩散控制的,聚合场所内消耗掉的调节剂得不到及时补充,就不能及时满足链转移反应的需要,调节剂的调节作用就得不到充分发挥。
分子量调节剂的种类较多,一般分为如下几类。
a.脂肪族硫醇类。脂肪族硫醇化合物是乳液聚合法生产橡胶时普遍采用的分子量调节剂。脂肪族硫醇的碳链长度可影响硫醇的活性,较长和较短碳链的硫醇都不适宜用作分子量调节剂,一般来说,含10~12个碳原子的硫醇最活泼。在聚合过程中,不但可调节聚合物的分子量,而且可减少支化作用,还能加快聚合反应速率。正十二碳硫醇和叔十二碳硫醇是目前工业中广泛采用的分子量调节剂。
b.黄原酸二硫化物类。此类化合物主要用作橡胶硫化过程的促进剂,其中二硫化二异丙基黄原酸酯(促进剂DIP)经常用作乳液聚合法生产橡胶的分子量调节剂,俗称为调节剂丁。
c.多元酚类。多元酚类化合物主要用作阻聚剂,在聚合过程中用来捕灭链自由基,其目的也是调节聚合物的分子量。
③扩链剂。扩链剂又称链增长剂,是能与线型聚合物链上的官能团反应而使分子链扩展、分子量增大的物质,常用于提高聚氨酯、聚酯等产品的力学性能和工艺性能。扩链剂为含羟基或氨基的低分子量多官能团的醇类或胺类化合物,常用的醇类扩链剂有1,4-丁二醇(BDO)、1,6-己二醇、甘油、三羟甲基丙烷、二甘醇(DEG)、三甘醇、新戊二醇(NPG)、山梨醇、二乙氨基乙醇(DEAE)等。胺类扩链剂有邻氯苯胺(MOCA,即聚氨酯橡胶硫化剂)、用甲醛改性制作的液体MOCA、乙二胺、N,N-二羟基(二异丙基)苯胺(HPA)等。
氢醌-二(β-羟乙基)醚(HQEE),用作聚氨酯胶黏剂的扩链剂时,其产品耐热性、硬度及弹性都高于一般的扩链剂。2-咪唑烷酮是一个具有亚氨基活性氢的广泛使用的扩链剂。巯基丙酸和巯基丙酸盐在聚合反应中既可以作为链转移剂,也可以作为交联剂。由次级丁胺硅烷为主配制成的Wacker-SB-72产品是硅树脂合成时的良好扩链剂。由美国Ethyl公司开发的牌号为Ethacure100的新型扩链剂二乙基甲苯二胺(DET-DA),是由两种异构体组成,与NCO的反应速率比MOCA快约30倍;美国Albemarle公司生产的牌号为Ethacure300的聚氨酯扩链剂二甲硫基甲苯二胺[DMTDA,又名二氨基二甲硫基甲苯(DADMT)],是二甲硫基甲苯二胺两种异构体的混合物,扩链的胶黏剂耐碱性好,因为室温下是液体,比MOCA使用更方便。