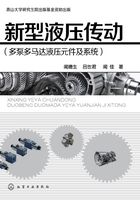
第一节 液压泵概述
液压泵是液压传动系统中将机械能转换成液体压力能的重要动力元件,是液压传动系统的心脏,它是将电动机(或其他原动机)输入的机械能转变成液压能的能量转换装置,其作用是给液压系统提供足够的压力油。
一、液压泵原理简介
在液压传动系统中,液压泵都是容积式泵,是靠密封工作腔的容积变化进行工作的。如图1-1所示,以简单的单活塞泵为例来简要阐述液压泵的工作原理。

图1-1 单活塞泵原理简图
1—曲柄;2—连杆;3—活塞;4—缸体;5,6—单向阀;7—油箱
由活塞3和缸体4以及单向阀5、6组成一个可以封闭的工作腔室A,当曲柄连杆机构1和2带动活塞在缸体内做往复直线运动时,就可以使工作腔室A的容积发生周期性变化。当活塞向缸体外侧(图中左侧)移动时,工作腔室A的容积逐渐增大,形成真空,油箱7中的液体(液压油)在大气压的作用下,经单向阀6进入工作腔,使工作腔A充满液压油,这就是泵的吸油过程。在吸油过程中,单向阀5在系统压力作用下始终保持关闭状态。当活塞向内(图中向右)移动时,工作腔容积变小,油液因受到压缩而使其压力升高,这时单向阀6因腔内的压力升高而处于关闭状态,当工作腔内的压力升高到系统的压力时,单向阀5被打开,泵向液压系统供给压力油,这就是压油过程。当曲柄1在电机或其他原动机的带动下做连续的圆周运动时,活塞泵的工作腔周期性地实现上述过程,使液压油源源不断地供给液压系统。
由以上的分析可以归纳出构成容积泵必须具备以下基本条件。
①结构上能够实现可变的密闭容积。
②具有适时可以控制吸、排油的配流装置。
由于周期性变化容积组成的结构不同,控制吸压油的配流装置不同,液压泵可分为柱塞泵、齿轮泵、叶片泵三大类。
二、齿轮泵原理简介
依靠缸体与啮合齿轮间形成的工作容积的变化和移动来输送液体或使之增压的泵为齿轮泵。齿轮泵是一种常用的液压泵,主要特点是结构简单、制造方便、价格低廉、体积小、重量轻、自吸性能好、对油液污染不敏感、工作可靠;其主要缺点是流量和压力脉动大、噪声大、排量不可调。
齿轮泵被广泛地应用于采矿设备、冶金设备、建筑机械、工程机械、农林机械等各个行业。齿轮泵按照其啮合形式的不同,有外啮合和内啮合两种,其中外啮合齿轮泵应用较广,而内啮合齿轮泵则多为辅助泵。
1.外啮合齿轮泵的工作原理
图1-2为外啮合齿轮泵的工作原理,由于齿轮两端面与泵盖的间隙以及齿轮的齿顶与泵体内表面的间隙都很小。因此,一对啮合的轮齿将泵体、前后泵盖和齿轮包围的密封容积分隔成左、右两个密封工作腔。当原动机带动齿轮如图示方向旋转时,左侧的轮齿不断退出啮合,其密封工作腔容积逐渐增大,形成局部真空,油箱中的油液在大气压力的作用下经泵的吸油口进入吸油腔。右侧的轮齿不断进入啮合,随着齿轮的转动,吸入的油液被齿间转移到右侧的密封工作腔。右侧进入啮合的轮齿使压油腔容积逐渐减小,把齿间油液挤出,从压油口输出,压入液压系统。这就是齿轮泵的吸油和压油过程。齿轮连续旋转,泵连续不断地吸油和压油。

图1-2 外啮合齿轮泵工作原理
2.内啮合齿轮泵的工作原理
内啮合齿轮泵有渐开线齿形齿轮泵和摆线齿形齿轮泵两种。
图1-3所示为内啮合渐开线齿轮泵工作原理,内啮合渐开线齿轮泵主要由主动齿轮1、从动齿轮2、月牙板3、轴及轴承、侧板等组成。其工作原理为:相互啮合的主动齿轮1和从动齿轮2与侧板围成的密封容积被月牙板3和齿轮的啮合线分隔成两部分,即形成吸油腔和压油腔。当传动轴带动小齿轮按图示方向旋转时,外齿轮同向旋转。图中上半轮齿脱开啮合,密封容积逐渐增大,形成局部真空度,油液在大气压作用下进入密封容积内,即吸油;下半轮齿进入啮合,使其密封容积逐渐减小,油液被挤压,压力增大,即排油。

图1-3 内啮合渐开线齿轮泵工作原理
1—主动齿轮;2—从动齿轮;3—月牙板;4—吸油腔;5—压油腔
内啮合渐开线齿轮泵与外啮合齿轮泵相比,其结构紧凑,重量轻,噪声小,效率高,还可以做到无困油现象。它的不足之处是齿形复杂,用专门的高精度加工设备才能生产出来。随着科技水平的发展,内啮合渐开线齿轮泵将会有更广阔的应用前景。
内啮合摆线齿轮泵又称为摆线转子泵,它具有结构紧凑,零件少、工作容积大,转速高,运动平稳等优点。
由于齿数较少(一般为4~7个),其流量脉动比较大,啮合处间隙泄漏大,通常作为润滑、补油等辅助泵使用。图1-4为内啮合摆线齿轮泵工作原理,在内啮合摆线齿轮泵中,外转子1和内转子2只差一个齿,中间没有月牙板,内、外转子的轴心线有一偏心距e。内转子为主动轮,内、外转子与两侧配油板间形成密封容积。内、外转子的啮合线又将密封容积分为吸油腔和压油腔。当内转子按图示方向转动时,左侧密封容积逐渐变大,形成局部真空度,油液在大气压作用下进入密封容积内,即吸油;右侧密封容积逐渐变小,油液被挤压,压力增大,即排油。

图1-4 内啮合摆线齿轮泵工作原理
1—外转子;2—内转子
此外,螺杆泵也是齿轮泵的一种特殊结构形式,其原理与结构特点如图1-5所示。

图1-5 螺杆泵结构原理简图
1—从动螺杆;2—吸油腔;3—主动螺杆;4—压油腔
螺杆泵中由于主动螺杆3和从动螺杆1的螺旋面在垂直于螺杆轴线的横截面上是一对共轭摆线齿轮,故又称为摆线螺杆泵。螺杆泵的工作机构主要由互相啮合且装于定子内的三根螺杆组成,中间一根为主动螺杆,由电机带动,旁边两根为从动螺杆,另外还有前、后端盖等主要零件。螺杆的啮合线把主动螺杆和从动螺杆的螺旋槽分割成多个相互隔离的密封腔。随着螺杆的旋转,这些密封工作腔一个接一个地在左端形成,并不断地从左向右移动。主动螺杆每转一周,每个密封工作腔便移动一个螺旋导程。因此,在左端吸油腔,密封油腔容积逐渐增大,进行吸油,而在右端压油腔,密封油腔容积逐渐减小,进行压油。由此可知,螺杆直径越大,螺旋槽越深,泵的排量就越大;螺杆越长,吸油腔2和压油腔4之间密封层次越多,泵的额定压力就越高。
螺杆泵的优点是:结构简单紧凑,体积小,动作平稳,噪声小,流量和压力脉动小,螺杆转动惯量小,快速运动性能好,因此已较多地应用于精密机床的液压系统中。其缺点是:由于螺杆形状复杂,加工比较困难。
三、叶片泵原理简介
由叶片作用产生周期性变化的密封容积的泵称为叶片泵。叶片泵具有排油均匀、工作平稳、噪声小等特点。根据转子每转一周的吸、压油次数不同,叶片泵可分为单作用叶片泵和双作用叶片泵。一般单作用叶片泵往往是做成变量泵结构,双作用叶片泵则只能做成定量泵结构。
1.单作用叶片泵的工作原理
单作用叶片泵主要由配油盘、转子、定子、叶片、壳体等零件组成,如图1-6所示。叶片泵的定子具有圆柱形的内表面,转子上有均布槽,矩形叶片安放在转子槽内,并可在槽内滑动。转子中心与定子中心不重合,有一个偏心距e。

图1-6 单作用叶片泵原理
1—配油盘;2—传动轴;3—转子;4—定子;5—叶片;6—壳体
当转子回转时,叶片靠自身的离心力贴紧定子的内表面,并在转子槽里做往复运动。定子、转子、叶片和配油盘间形成了若干个密封工作容积。
当发动机带动转子按逆时针方向旋转时,右边的叶片逐渐伸出,相邻两叶片间的空间容积逐渐增大,形成局部真空,从吸油口吸油;左边的叶片被定子的内表面逐渐压进槽内,两相邻叶片间的空间容积逐渐减小,将工作油液从压油口压出。在吸油腔与压油腔之间有一段封油区,把吸油腔和压油腔隔开,称作过渡区。
当转子不断地旋转,泵就不断地吸油和排油。这种叶片泵的转子转一周,各叶片间容积只吸、排油各一次,因此叫单作用叶片泵。改变偏心距e便可改变泵的流量,成为变量叶片泵。
2.双作用叶片泵工作原理
图1-7为双作用叶片泵的工作原理,它的作用原理和单作用叶片泵相似,不同之处在于定子内表面是由两段长半径圆弧、两段短半径圆弧和四段过渡曲线组成,且定子和转子是同心的,当转子逆时针方向旋转时,密封工作腔的容积在左上角和右下角处逐渐减小,为压油区;在左下角和右上角处逐渐增大,为吸油区。

图1-7 双作用叶片泵原理
吸油区和压油区之间有一段封油区将吸、压油区隔开。这种泵的转子每转一周,每个密封工作腔完成吸油和压油动作各两次,所以称为双作用叶片泵。由于双作用叶片泵有两个吸油区和两个排油区,并且各自的中心夹角是对称的,所以作用在转子上的油压作用力互相平衡。因此,这种泵也称为平衡式叶片泵。
四、柱塞泵原理简介
由柱塞作用产生周期性变化的密闭容积的泵为柱塞泵。柱塞泵是通过柱塞在柱塞孔内往复运动时密封工作容积的变化来实现吸油和排油的。由于柱塞与缸体内孔均为圆柱表面,滑动表面配合精度高,所以这类泵的特点是泄漏小,容积效率高,可以在高压下工作。根据柱塞排列方式的不同,柱塞泵可分为轴向式和径向式两种。
1.轴向柱塞泵的原理
轴向柱塞泵可分为斜盘式和斜轴式两大类,图1-8所示为斜盘式轴向柱塞泵的工作原理。泵由传动轴、斜盘、柱塞、缸体、配流盘等主要零件组成,斜盘2和配流盘4是不动的,传动轴1带动缸体3和柱塞5一起转动,柱塞5靠弹簧等机械装置压紧在斜盘上。

图1-8 斜盘式轴向柱塞泵原理
1—传动轴;2—斜盘;3—缸体;4—配流盘;5—柱塞
当传动轴按图1-8所示方向旋转时,柱塞5在其沿斜盘自下而上回转的半周内在弹簧作用下逐渐向缸体外伸出,使缸体孔内密封工作腔容积不断增加,产生局部真空,从而将油液经配流盘4上的进油口吸入;柱塞在其自上而下回转的半周内又被斜盘逐渐向里推入,使密封工作腔容积不断减小,将油液从配流盘出油口向外排出,缸体每转一转,每个柱塞往复运动一次,完成一次吸油动作。改变斜盘的倾角,就可以改变密封工作容积的有效变化量,实现泵的变量。
图1-9为斜轴式轴向柱塞泵的工作原理,传动轴5的轴线相对于缸体3存在倾角,柱塞2与传动轴圆盘之间用相互铰接的连杆4相连。

图1-9 斜轴式轴向柱塞泵原理
1—配流盘;2—柱塞;3—缸体;4—连杆;5—传动轴
当传动轴5沿图示方向旋转时,连杆4就带动柱塞2连同缸体3一起绕缸体轴线旋转,柱塞2同时也在缸体的柱塞孔内做往复运动,使柱塞孔底部的密封腔容积不断增大或缩小,通过配流盘1上的窗口实现吸油和排油。
与斜盘式泵相比较,斜轴式泵由于缸体所受的不平衡径向力较小,故结构强度较高,可以有较高的设计参数,其缸体轴线与驱动轴的夹角较大,变量范围较大;但外形尺寸较大,结构也较复杂。目前,斜轴式轴柱塞泵的使用相当广泛。
在变量形式上,斜盘式轴向柱塞泵靠斜盘摆动变量,斜轴式轴向柱塞泵则为摆缸变量;因此,后者的变量系统的响应较慢。
2.径向柱塞泵的原理
图1-10是径向柱塞泵的工作原理,由图可见,径向柱塞泵的柱塞径向布置在缸体上;在转子2上径向均匀分布着数个柱塞孔,孔中装有柱塞5;转子2的中心与定子1的中心之间有一个偏心量e。在固定不动的配流轴3上,相对于柱塞孔的部位有相互隔开的上下两个配油窗口,该配油窗口又分别通过所在部位的两个轴向孔与泵的吸、排油口连通。当转子2旋转时,柱塞5在离心力及机械回程力作用下,它的头部与定子1的内表面紧密接触,由于转子2与定子1存在偏心,所以柱塞5在随转子转动时,又在柱塞孔内做径向往复滑动,当转子2按图示箭头方向旋转时,上半周的柱塞皆往外滑动,柱塞孔的密封容积增大,通过轴向孔吸油;下半周的柱塞皆往里滑动,柱塞底部的密封工作容积缩小,通过配流轴向外排压力油。

图1-10 径向柱塞泵的工作原理
1—定子;2—转子;3—配流轴;4—衬套;5—柱塞;6—吸油腔;7—压油腔
当移动定子,改变偏心量的大小时,泵的排量就发生改变;当移动定子使偏心量从正值变为负值时,泵的吸、排油口就互相调换,因此,径向柱塞泵可以是单向或双向变量泵,为了流量脉动率尽可能小,通常采用奇数柱塞。
径向柱塞泵的径向尺寸大,结构较复杂,自吸能力差,并且配流轴受到径向不平衡液压力的作用,易于磨损,这些都限制了它的工作转速和输出压力的提高。