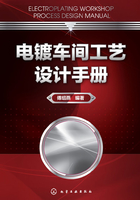
第4章 镀覆层选择和标识方法
4.1 金属的防护方法
防止金属腐蚀的方法大致可以分为表面保护层防腐蚀、阴极保护和腐蚀介质的处理等三种方法。
4.1.1 表面保护层防腐蚀
表面保护层的作用在于将金属表面与周围介质隔离,从而可以防止或减少金属制品腐蚀,达到保护的目的,这是最普遍而最重要的金属防腐蚀方法。
根据构成表面保护层物质的不同,可以把保护层分为三类,如表4-1所示。
表4-1 表面保护层分类

表面防腐蚀保护层的分类见图4-1。

图4-1 表面防腐蚀保护层的分类
电镀层的种类见图4-2。

图4-2 电镀层的种类
4.1.2 阴极保护
阴极保护即电化学保护,阴极保护方法既可以用外电源通电来实现,也可以在被保护的金属上连接一个电位更负的金属来实现。阴极保护有两种方法,见表4-2。
表4-2 阴极保护方法

4.1.3 腐蚀介质的处理
腐蚀介质的处理实质上可以归纳为两个方面,见表4-3。
表4-3 腐蚀介质的处理方法

4.2 镀层要求和分类
(1)电镀目的
①保护金属零件表面,防止腐蚀。
②装饰制品表面,使外表美观。
③提高零件表面的硬度和耐磨性能。
④提高零件表面的功能性性能,如导电性、导磁性、耐热性、减磨性、钎焊性、反光能力、防反光能力、抗氧化及耐酸性等功能。
⑤节约及代替有色金属或贵金属。
⑥修复磨损零件。
⑦热处理时的局部保护,如防止局部渗碳的镀铜、防止局部渗氮的镀锡等。
(2)镀层要求
不同的制品,对镀层的要求也不同,但就其共性来说,对电镀层、化学转化膜有下列要求。
①镀层与基体、镀层与镀层之间,应有良好的结合力。
②镀层应完整、平整、结晶细致紧密、孔隙尽可能少。
③镀层具有规定的厚度,并在制品的主要表面上,厚度应比较均匀。
④镀层、化学转化膜应具有规定的各项指标,如光亮度、色彩、硬度、耐蚀性等化学、物理性能。
(3)镀层的分类
从目前应用于生产中的金属镀层有单金属镀层、合金镀层、化学镀层等。镀层分类的方法很多,一般分类如表4-4所示。
表4-4 镀层的分类

4.3 镀覆层选择
电镀层和化学转化膜的选择,必须考虑的因素:
①零件的工作环境、储存和使用条件以及使用期限。
②镀覆层的使用目的和要求。
③镀覆层与被镀零件材质、性能的适应性。
④镀覆层及其镀覆工艺不应降低基体材料的力学性能。
⑤被镀零件的种类、材料,前面加工的状态和性质。
⑥被镀零件的结构、形状、加工方法、表面粗糙度和尺寸公差。
⑦电镀层、化学处理转化膜层的特性和应用范围。
⑧与镀层、化学转化膜相接触的金属(接触偶)的材料、性质。
⑨带有螺纹连接、压合、搭接、铆接、点焊、单面焊等的组件,因存在缝隙,原则上不允许在溶液中镀覆。
4.3.1 互相接触的金属或镀层的选择
不同金属、镀层互相接触时,在有腐蚀性的环境中就会发生接触腐蚀,即活性较高的金属(阳极金属)加速腐蚀,而活性较低的金属(阴极金属)减缓腐蚀。故在选择互相接触的金属或镀层时,必须注意到不同金属接触腐蚀的影响。选择互相接触的金属、镀层可参考表4-5。
表4-5 选择互相接触的金属、镀层的建议


①铜、镍、铬复合镀层。
②铜、镍复合镀层。
③碳素钢和低合金钢。
④锌、铜复合镀层。
⑤1Cr18Ni9Ti的不锈钢。
⑥沿海地区(无工业大气影响)属1级。
⑦沿海地区(无工业大气影响)属0-1级。
不同金属材料的防护方法也有所不同,根据材料特性及所要求的防腐、装饰、特殊功能等,来选择其防护体系。
4.3.2 防护性镀覆层
防护性镀覆层的主要作用是保护零件防止其遭受腐蚀。钢铁件的防护性镀覆层有:镀锌、镀镉、镀锡、镀锡-锌合金、镀镉-钛合金、镀锌-镉合金、镀铅-锡合金等镀层;钢铁件的磷化处理、氧化处理。铝及其合金件的氧化处理,镁合金件氧化处理,铜及其合金件钝化处理等化学处理转化膜。
防护性镀覆层的选择以及它的特性和用途见表4-6。
表4-6 防护性镀覆层的选择以及它的特性和用途


4.3.3 防护-装饰性镀覆层
防护-装饰性镀覆层主要目的是使零部件的外表美观,并应具有较好的耐蚀性,以保证产品在有腐蚀性和摩擦的环境中,能保持一定的光亮外观。
装饰性镀层广泛采用镀铜/镍/铬、铜-锡合金/铬、锌-铜合金/铬等各种多层镀层。此外,光亮镀锌、镀镉经铬酸盐钝化和着色后,也越来越多地用作装饰镀层。
防护-装饰性镀覆层的选择以及它的特性和用途见表4-7。
表4-7 防护-装饰性镀覆层的选择以及它的特性和用途



4.3.4 高硬度的耐磨镀覆层
属于这一类的镀层有镀硬铬、化学镀镍、镀铁、镀铑、镀合金以及铝及铝合金的硬质阳极氧化处理等。
选择提高镀层的表面硬度、耐磨性,可参见表4-8。
表4-8 高硬度和耐磨镀层的特性和用途

4.3.5 功能性镀覆层
属于这一类的镀层有很多,选择各种功能性镀覆层,参见表4-9。
表4-9 各种功能性镀覆层

4.4 各种金属零件防护体系的选择
各种金属零件,如铁基合金、铝及铝合金、镁合金、铜及铜合金及钛合金等,在大气环境中工件的机械零件,需要有保护层,有时还需要具有特殊功能。下面介绍各种金属零件在大气环境中的各种条件下防护体系的选择,供参考。
4.4.1 钢铁零件防护体系的选择
碳钢、合金钢、铸铁、铸钢及含铬18%以下的耐蚀钢等,抗蚀能力不强,在大气、水、海水及海洋环境中容易腐蚀,除在液压油中工作外,通常需要防护层。含铬18%(质量分数)以上的耐蚀不锈钢除有特殊要求外,一般不需要防护层,为增加抗蚀能力,需进行钝化处理。钢铁零件除防护、装饰外,有时还需具有特殊功能,如硬度、耐磨、导电、反光、防反光、磁性、耐酸以及热处理的局部保护等。
钢铁零件防护体系的选择见表4-10。
表4-10 钢铁零件防护体系的选择

4.4.2 铝及铝合金零件防护层的选择
铝及铝合金的表面处理方法及镀覆层的选择见表4-11。
表4-11 铝及铝合金的表面处理方法及镀覆层的选择

4.4.3 镁合金零件防护层的选择
镁合金的表面处理方法及防护层的选择见表4-12。
表4-12 镁合金的表面处理方法及防护层的选择

4.4.4 铜及铜合金零件防护层的选择
铜及铜合金零件防护层的选择见表4-13。
表4-13 铜及铜合金零件防护层的选择

4.4.5 钛合金零件防护层的选择
钛合金零件防护层的选择见表4-14。
表4-14 钛合金零件防护层的选择[5]

4.4.6 其他金属零件防护层的选择
其他金属零件防护层的选择见表4-15。
表4-15 其他金属零件防护层的选择

4.5 镀覆层厚度系列、应用范围及其特性
各种镀层厚度取决于使用环境条件、使用寿命以及镀层类型等因素。各种镀层厚度系列中所涉及的镀层类型及服役环境条件等,分别叙述如下。
(1)镀层类型
①铜镀层类型 铜镀层用下列符号表示:
a表示从酸性溶液中镀出的延展、整平性铜。
②镍镀层类型 镍镀层的种类用下列符号表示:
b表示全光亮镍;
p表示机械抛光的暗镍或半光亮镍;
s表示非机械抛光的暗镍,半光亮镍或缎面镍;
d表示双层或三层镍;
dp表示从预镀溶液中电沉积延展性镍。
双层或三层镍电镀层的有关要求见表4-16。
表4-16 双层或三层镍电镀层要求

①规定镍层的含硫量是为了说明所用的镀镍溶液种类。
③铬镀层类型 铬镀层的类型和厚度用下列符号表示:
r表示普通铬(常规铬),厚度为0.3μm;
mc表示微裂纹铬,厚度为0.3μm;
mp表示微孔铬,厚度为0.3μm。
生产微裂纹铬时,某些工序为达到所必需的裂纹样式,要求坚硬、较厚(约0.8μm)的铬镀层。在这种情况下,镀层标识应包括最小局部厚度:Cr mc(0.8)。
(2)镀层服役环境条件
镀层的各类服役环境条件的环境举例。
5——极其严酷。在极严酷的室外环境下服役,要求长期保护基体。
4——非常严酷。在非常严酷的室外环境下服役。
3——严酷。在室外海洋性气候或经常下雨潮湿的室外环境下服役。
2——中度。在可能产生凝露的室内环境下服役。
1——温和。在气氛温和干燥的室内环境下服役。
(3)表示基体金属的化学符号
表示基体金属(或合金基体中的主要金属)的化学符号,后接一斜线“/”,如下:
Fe/表示基体为钢铁;
Zn/表示基体为锌或锌合金;
Cu/表示基体为铜或铜合金;
Al/表示基体为铝或铝合金;
Mg/表示基体为镁或镁合金;
Ti/表示基体为钛或钛合金;
PL/表示基体为塑料。
4.5.1 锌镀层厚度系列及应用范围
(1)锌镀层厚度
锌镀层厚度取决于使用条件。在GB/T 9799—2011《金属及其他无机覆盖层 钢铁上经过处理的锌电镀层》(本标准使用翻译法等同采用ISO 2081:2008《金属及其他无机覆盖层 钢铁上经过处理的锌电镀层》)的附录C(资料性附录)中表示出锌镀层厚度与制品使用条件的关系,见表4-17。
表4-17 锌电镀层+铬酸盐转化膜中性盐雾试验的耐蚀性


说明:表4-17中给出了各种使用条件下达到防护要求的厚度值(即锌电镀层经铬酸处理后的最小局部厚度)。
①对于某些重要的应用,使用条件为3时,锌电镀层的最小厚度建议由14μm代替12μm。
②对于直径不到20mm的螺纹件,镀层的最小厚度建议为10μm;对于铆钉、锥形针、开口销和垫片之类的工件,其镀层的最小厚度建议为8μm。
③漂洗和烘干:对于六价铬转化膜,为防止六价铬酸盐的溶解,如果铬酸盐处理后用热水漂洗,则漂洗时间应尽可能短。为防止铬酸盐膜脱水产生裂纹,工件的干燥温度应与所采用的铬酸盐类型保持一致(通常最高干燥温度为60℃)。
④表4-17中的中性盐雾试验持续时间为基体金属腐蚀(红锈)开始时,锌+铬酸盐转化膜的中性盐雾的耐蚀性。
⑤锌电镀层腐蚀(白锈)开始时铬酸盐转化膜的耐蚀性,见表4-18。
表4-18 锌电镀层腐蚀(白锈)开始时铬酸盐转化膜的耐蚀性

注:铬酸盐转化膜代号见表4-19。
(2)铬酸盐转化膜和其他辅助处理的标识
①铬酸盐转化膜标识 表4-19列出了铬酸盐转化膜代号(标识)及每类铬酸盐转化膜按ISO 3892测出的大致表面密度(单位面积的质量)。
表4-19 铬酸盐转化膜的类型、外观和表面密度(GB/T 9799—2011)

转化膜的封闭:为了进一步提高耐蚀性,铬酸盐转化膜可以进行封闭处理。封闭是在铬酸盐膜上涂上有机物或无机物,这样可以增强铬酸盐膜在高温下的耐蚀性。转化可以通过在转化膜上浸或喷聚合物的水溶液来实现,也可以通过在铬酸盐转化液中加入合适的有机物来进行。
②其他辅助处理的标识 如果需要进行其他辅助处理(非转化后处理),其代号标识见表4-20。
表4-20 非转化后处理(GB/T 9799—2011)

(3)锌电镀层标识示例
锌电镀层标识,按以下顺序明确指出基体材料、降低应力的要求、底镀层的类型和厚度(有底镀层时)、锌电镀层的厚度、镀后热处理要求、转化膜的类型和/或辅助处理。
①基体材料的标识 应用其化学符号标识,如果是合金,则应标明主要成分。例如,Fe表示铁或钢、Zn表示锌合金、Cu表示铜及铜合金、Al表示铝及铝合金。
②热处理要求的标识 SR表示电镀前消除应力的热处理、ER表示电镀后降低氢脆敏感性的热处理;在圆括号中标明最低温度(℃);热处理持续时间用小时(h)计。
【例】 SR(210)1,表示电镀前消除应力热处理,在210℃下处理1h。
③锌电镀层标识示例
【例1】 铁或钢(Fe)上厚度为12μm的锌电镀层(Zn12),镀层经彩虹色化学转化处理(C),其标识为:
电镀层GB/T 9799-Fe/Zn12/C
【例2】 铁或钢(Fe)上厚度为25μm的锌电镀层(Zn25);为降低氢脆,镀后在190℃下热处理8h[ER(190)8];镀层经过不透明铬酸盐处理(D),并用有机封闭剂进行封闭(T2),其标识为:
电镀层GB/T 9799-Fe/Zn25/ER(190)8/D/T2
【例3】 同示例2,但工件在镀前进行降低应力热处理,200℃下持续最短时间为3h,其标识为:
电镀层GB/T 9799-Fe/SR(200)3/Zn25/ER(190)8/D/T2
4.5.2 镉镀层厚度系列及应用范围
(1)镉镀层厚度
镉镀层厚度取决于使用条件。在GB/T 13346—2012《金属及其他无机覆盖层 钢铁上经过处理的镉电镀层》(本标准使用翻译法等同采用ISO 2082:2008《金属及其他无机覆盖层 钢铁上经过处理的镉电镀层》)的附录C(资料性附录)中表示出镉镀层厚度与制品使用条件的关系,见表4-21。
表4-21 镉加铬酸盐转化膜耐中性盐雾腐蚀性

说明:如果进行铬酸盐处理,表4-21中给出了所需镉镀层的最小厚度。镉镀层的厚度取决于使用条件的严酷程度,以确保所需的耐蚀性。
①对于一些重要的应用,建议最低按使用条件3,镉镀层局部厚度为14μm。
②对于螺纹直径20mm以下的零件,推荐的最小厚度为10μm。
③对于铆钉、锥形针、开口销和垫圈,推荐的最小厚度为8μm。
④清洗和烘干:如果在铬酸盐处理后用热水作最终清洗,则为防止六价铬的溶解,清洗时间尽可能短。为防止铬酸盐转化膜脱水而开裂,干燥温度应与所采用的铬酸盐类型保持一致(通常最高干燥温度不超过60℃)。
⑤表4-21中的中性盐雾试验时间,为基体金属腐蚀(红锈)开始时,镉加铬酸盐转化膜的中性盐雾的耐蚀性。
(2)镉镀层上的铬酸盐转化膜的耐腐蚀性
镉镀层上的铬酸盐转化膜的耐腐蚀性见表4-22。
表4-22 镉镀层上的铬酸盐转化膜的耐腐蚀性

注:铬酸盐转化膜代号见表4-23。
(3)铬酸盐转化膜类型、外观和表面密度
铬酸盐转化处理溶液通常呈酸性,并含有六价铬或三价铬盐以及能够改变转化膜外观和硬度的其他盐类。镉镀层通过不同溶液的处理可以获得光亮、彩虹色、橄榄绿色和黑色的钝化膜。彩虹膜也可在碱性或磷酸溶液中褪色得到透明薄膜。表4-23根据ISO 3892测量给出了各种类型铬酸盐转化膜近似表面密度(单位面积的质量)。
表4-23 铬酸盐转化膜类型、外观和表面密度(GB/T 13346—2012)

(4)铬酸盐转化膜的其他后处理
①封闭 为了提高防腐蚀性能,可通过有机或无机产品对铬酸盐转化膜进行封闭处理。可用聚合物水溶液浸渍或喷涂对转化膜进行封闭。
②转化膜的后处理 转化膜后处理的处理类型和代号,如表4-24所示。
表4-24 转化膜后处理的处理类型和代号(GB/T 13346—2012)

(5)镉镀层标识示例
镉镀层标识,应按照下列顺序排列:基体金属、时效处理要求、底镀层厚度和类型、表面镉镀层厚度、电镀后热处理要求、转化膜类型和/或后处理。
①基体金属材料的标识 应用其化学符号标识,例如,Fe表示铁或钢。
②热处理要求的标识 SR表示电镀前降低应力热处理、ER表示电镀后消除氢脆的热处理;在圆括号中标明最低温(℃);热处理持续时间用小时(h)表示。
【例】 SR(210)1,表示电镀前在210℃下进行1h降低应力的热处理。
③镉镀层标识示例
【例1】 在铁或钢上电镀12μm厚度的镉及彩色钝化膜(C)处理。
其标识为:电镀层GB/T 13346-Fe/Cd12/C
【例2】 在铁或钢上电镀25μm厚度的镉,电镀后在190℃下进行8h消除氢脆的热处理,标识为ER(190)8,增加不透明铬酸盐转化膜(D)及有机封闭剂封闭的后处理(T2)。
其标识为:电镀层GB/T 13346-Fe/Cd25/ER(190)8/D/T2
【例3】 同示例2,但要在电镀前于200℃下进行至少3h降低应力的热处理,标识为SR(200)3。
其标识为:电镀层GB/T 13346-Fe/SR(200)3/Cd25/ER(190)8/D/T2
4.5.3 铜镀层厚度系列及应用范围
工程用铜电镀层的厚度主要取决于应用范围及使用条件。在GB/T 12333—1990《金属覆盖层 工程用铜电镀层》中,规定了铜电镀层的厚度系列。该标准适用于工程用途的铜电镀层,例如在热处理零件表面起阻挡层作用的铜电镀层;拉拔丝加工过程中要求起减磨作用的铜电镀层;作锡镀层的底层防止基体金属扩散的铜电镀层等。但不适用于装饰性用途的铜电镀层和铜底层及电铸用铜镀层。
工程用铜电镀层的最小厚度要求及应用实例,如表4-25所示。
表4-25 铜电镀层的厚度系列

注:1.引自GB/T 12333—1990《金属覆盖层 工程用铜电镀层》。
2.螺纹零件镀铜时,应避免螺纹的牙顶上镀的太厚。为了使牙顶上的镀层厚度不超过允许的最大厚度值,可以允许其他表面上镀层的厚度比规定值略小。
4.5.4 锡镀层厚度系列及应用范围
锡镀层按厚度分类,并分别用于不同的使用条件时,各类最小厚度值的规定,见表4-26。
表4-26 锡镀层最小厚度

①锌铜合金基体材料上的底镀层的要求。当存在下列的任一原因时,某些基体表面可要求底镀层:a.防止扩散;b.保持可焊性;c.保证附着强度;d.提高耐蚀性。
②特定基体材料上底镀层的要求:a.难清洗的基体材料。某些基体材料,如磷-青铜、铍-青铜合金和镍-铁合金,由于其表面氧化膜特性,镀锡均难于作化学清洗前处理,如果要求锡镀层可焊性能,加镀最小局部厚度为2.5μm的镍层或铜底层可能是有益的。b.铝、镁和锌合金。这些合金容易受到稀酸或碱的侵蚀,因此,在制品电镀以前,需要特殊处理,包括沉积一层厚度为10~25μm的厚铜或黄铜或锌底镀层。
注:引自GB/T 12599—2002《金属覆盖层 锡电镀层技术规范和试验方法》。
4.5.5 镍镀层厚度系列及应用范围
镍镀层厚度系列引自GB/T 9798—2005《金属覆盖层 镍电沉积层》(本标准等同采用ISO 1458:2002《金属覆盖层 镍电沉积层》)。该标准规定了在钢铁、锌合金、铜和铜合金、铝和铝合金上装饰性和防护性镍电镀层的要求,以及在钢铁、锌合金上铜+镍电镀层的要求。
无铜底层、有铜底层及无铬面层的装饰性镍镀层,适用于防止使用中的摩擦或触摸导致镀层变色或取代铬作面层的镀件。也适用于对变色要求不同的镀件。耐蚀性取决于覆盖层的种类和厚度。一般来说,相同厚度的多层镍比单层镍防护性能更好。
下列各表给出了不同厚度和种类镀层的标识,以及镀件暴露于相应服役条件下镀层选择的指南。
钢铁上镍和铜+镍镀层的厚度规定见表4-27。
表4-27 钢铁上镍和铜+镍镀层的厚度规定

①GB/T 9798—2005表的“3——严酷”中原是Fe/Ni30s,但Fe/Ni30s已经有了,是否应为Fe/Ni30d(表中所注的①为编著者所加)。
锌合金上镍和铜+镍镀层的厚度规定见表4-28。
表4-28 锌合金上镍和铜+镍镀层的厚度规定

①GB/T 9798—2005表的“2——中度”中原是Zn/Ni15b,但Zn/Ni15b已经有了(重复),是否应为Zn/Ni15s。
②GB/T 9798—2005表的“2——中度”中原是Zn/Cu10a Ni15b,但Zn/Cu10a Ni15b已经有了(重复),是否应为Zn/Cu10a Ni15s。
铜或铜合金上镍镀层的厚度规定见表4-29。
表4-29 铜或铜合金上镍镀层的厚度规定

铝或铝合金上镍镀层的厚度规定见表4-30。
表4-30 铝或铝合金上镍镀层的厚度规定

4.5.6 工程用铬镀层厚度系列及应用范围
一般把维氏硬度[1]在6865MPa以上的铬镀层定为功能性镀铬中的工业镀铬,也称工程镀铬。而在实际中是用铬镀层厚度来区分的,一般认为大于5μm厚度时为工程镀铬。
工程用铬镀层常在基体金属上直接电镀,以提高耐磨性,增强抗摩擦、腐蚀能力,减小静摩擦力或摩擦力,减少“咬死”的黏结,以及修复尺寸偏小或磨损的工件。为防止严重腐蚀,电镀铬前可采用镍或其他金属底层,或采用合金电镀来提高铬镀层的耐蚀性,如镀铬-钼合金。工程用铬镀层的厚度见表4-31。
表4-31 工程用铬镀层的典型厚度

注:引自GB/T 11379—2008《金属覆盖层 工程用铬镀层》。
4.5.7 镍+铬和铜+镍+铬电镀层厚度系列
电镀装饰性的镍+铬和铜+镍+铬电镀层,可用于增强零件外观装饰和防腐性能,而防腐性能取决于镀层的厚度和类型。
本电镀层厚度系列,引自GB/T 9797—2005《金属覆盖层 镍+铬和铜+镍+铬电镀层》。该标准规定了在钢铁、锌合金、铜和铜合金、铝和铝合金上,提供装饰性外观和增强防腐性的镍+铬和铜+镍+铬电镀层的要求,规定了不同厚度和种类镀层的标识,提供了电镀制品暴露在对应服役环境条件下镀层厚度选用的指南。
镍+铬和铜+镍+铬电镀层根据暴露环境条件,所规定的厚度系列见以下各表。
钢上的镍+铬镀层的厚度规定见表4-32。
表4-32 钢铁上的镍+铬镀层的厚度规定

钢上的铜+镍+铬镀层的厚度规定见表4-33。
表4-33 钢铁上的铜+镍+铬镀层的厚度规定

锌合金上的镍+铬镀层的厚度规定见表4-34。
表4-34 锌合金上的镍+铬镀层的厚度规定

注:在表中服役条件“1——温和”中的“镀层标识”中有3个同样的Zn/Ni8b Cr r,可能有笔误。如①原标准中为Zn/Ni8b Cr r,是否应为Zn/Ni8p Cr r;②原标准中也是Zn/Ni8b Cr r,是否应为Zn/Ni8s Cr r。表中所注的①、②为编著者所添加的,本注仅供参考。
锌合金上的铜+镍+铬镀层的厚度规定见表4-35。
表4-35 锌合金上的铜+镍+铬镀层的厚度规定

铜和铜合金上的镍+铬镀层的厚度规定见表4-36。
表4-36 铜和铜合金上的镍+铬镀层的厚度规定

铝或铝合金上的镍+铬镀层的厚度规定见表4-37。
表4-37 铝和铝合金上的镍+铬镀层的厚度规定

4.5.8 塑料上镍+铬电镀层厚度系列
塑料上镍+铬电镀层厚度系列,引自GB/T 12600—2005《金属覆盖层 塑料上镍+铬电镀层》。该标准规定了塑料上有或无铜底层的镍+铬装饰性电镀层的要求,该标准允许使用铜或者延展性镍作为底镀层,以满足热循环试验要求。该标准不适用于工程塑料的电镀层。
塑料上的电镀层根据暴露环境条件,所规定的厚度系列见以下各表。
塑料上镍+铬镀层的厚度规定见表4-38。
表4-38 塑料上镍+铬镀层的厚度规定

塑料上铜+镍+铬镀层的厚度规定见表4-39。
表4-39 塑料上的铜+镍+铬镀层的厚度规定

4.5.9 铅镀层厚度系列及应用范围
铅镀层均匀、细致、柔软、延展性好,多用于减摩部位,可改善磨合。由于铅在空气中能形成一层致密的氧化保护膜,所以有良好的抗氧化侵蚀作用。在含有硫的工业气氛中,以及周围有水的环境里,性能稳定。铅镀层厚度系列及应用范围见表4-40。
表4-40 铅镀层厚度系列及应用范围[5]

4.5.10 铁镀层厚度系列及应用范围
镀铁作为一种模具制造、磨损件的尺寸修复和表面强化等的手段,在机械、交通运输、印刷制板等领域获得广泛应用。镀铁的应用范围及镀层厚度见表4-41。
表4-41 镀铁的应用范围及镀层厚度[1]

4.5.11 银镀层厚度系列及应用范围
由于银比较昂贵,银镀层一般不适用于作防护,除少量作为装饰镀层(如乐器、首饰、装饰品、工艺品等)外,大多利用其高导电性、高反光性及防粘接等功能在特殊条件下使用。银镀层厚度的要求见表4-42。在日本工业标准(JIS)H0411《镀银层检验方法》中,将银镀层厚度分为7个等级,现列入表4-43中,供参考。
表4-42 银镀层厚度及应用范围

表4-43 镀银层厚度分级参数[日本工业标准(JIS)H0411]

注:耐磨性试验采用落砂法。让40目左右的砂粒从管径为5mm的漏斗落到45°角放置的试片上,露出底层为终点,落砂量为450g,落下距离为1000mm,测量所需时间。测量第1、2级别的镀层时,所用管径为4mm,落砂量为110g,落下距离为200mm。
4.5.12 金镀层厚度系列及应用范围
金镀层具有优异的耐高温、耐蚀性和化学稳定性,能长期保持其光泽和永久接触电阻。但硬度低,含有银、铜、锡、钴、镍等的金合金镀层,硬度比纯金镀层高2~3倍,被称为硬金镀层。金镀层和金合金镀层厚度系列及应用范围见表4-44。
表4-44 金镀层和金合金镀层厚度系列及应用范围

①引自参考文献[5]。
4.5.13 锌合金铸件防护装饰性镀层的厚度
锌合金铸件防护装饰性(镀铜+镍+铬)镀层厚度要求,根据零件使用环境,可参考表4-45所列的镀层厚度系列选用。
表4-45 锌合金铸件镀铜+镍+铬镀层厚度系列[1]

4.5.14 化学镀镍-磷合金镀层厚度系列
化学镀镍-磷合金镀层可改善防腐蚀性能和提高耐磨性能。一般而言,当镀层中磷含量增加到8%(质量分数)以上时,耐腐蚀性能将显著提高;而随着镀层中磷含量减少至8%以下时,耐磨性能会得到提高。通过适当的热处理,将会大大提高磷含量镀层的显微硬度,从而提高了镀层的耐磨性。
(1)耐磨性镀层的厚度
为了以最小的化学镀镍-磷合金镀层厚度,获得最佳耐磨性,基体材料的表面应平整无孔。在粗糙或多孔的工件表面,为了将基体材料对镀层特性的影响减到最小,镍-磷镀层应更厚一些。
满足耐磨性使用要求的最小化学镀镍-磷合金镀层厚度见表4-46。
表4-46 满足耐磨性使用要求的最小化学镀镍-磷合金镀层厚度

注:引自GB/T 13913—2008《金属覆盖层 化学镀镍-磷合金镀层规范和试验方法》。
可以通过控制化学镀镍-磷沉积过程,来获得具有能够满足不同使用要求特性的镍-磷镀层。表4-47列出不同使用条件下镀层的种类和磷含量。
表4-47 不同使用条件下推荐采用的镍-磷镀层的种类和磷含量

注:引自GB/T 13913—2008《金属覆盖层 化学镀镍-磷合金镀层规范和试验方法》。
(2)修复性镀层的厚度
用于修复磨损的工件和挽救超差的工件,采用的化学镀镍-磷修复性镀层的厚度为≥125μm。
高磷含量(≥10%,质量分数)的镀层,比低磷或中磷的镀层,具有较低的内应力、较高的延展性和较高的耐腐蚀性,更适合于修复磨损或超差工件的修复性镀层。
当镀层厚度超过125μm时,有时在化学镀镍-磷之前,采用预电镀镍底层。
(3)提高可焊性镀层的厚度
提高诸如铝以及其他难焊接的合金的可焊性,采用的化学镀镍-磷镀层的厚度为2.5μm。
(4)预镀底层
电镀底层的目的是减少沉积过程中,那些会降低沉积效率的元素的污损危害。另外,电镀金属底层能阻止杂质从基体金属扩散到化学镀镍-磷镀层,并有助于提高结合力。
①含微量镁和锌的基体金属,可电镀2~5μm厚的镍或铜底层。
②含微量铬、铅、钼、锡、钛或钨的基体金属,可电镀2~5μm厚的镍底层。
③可以在钢底层和化学镀镍-磷镀层之间闪镀镍层。
4.5.15 铜-锡合金镀层厚度系列
由于铜-锡合金镀层具有良好的耐蚀性和优良的钎焊性能。广泛用于电子、电器制品的防腐蚀和改善焊接性能,也用于其他制品的防护装饰镀层(作中间镀层)。
铜-锡合金镀层厚度系列,引自JB/T 10620—2006《金属覆盖层 铜-锡合金电镀层》,该标准规定了在不同环境条件下对铜-锡合金镀层厚度的要求和镀层的标识。
(1)铜-锡合金镀层厚度
将铜-锡合金镀层按锡含量高低和不同的使用环境条件分类,表4-48中规定了每种使用环境对应的最小厚度值。
表4-48 不同使用环境条件下对应的铜-锡合金镀层厚度要求

注:1.通常情况下,高锡铜-锡合金镀层硬度高、耐蚀性好,宜用于装饰性镀层,但镀层较脆,不能经受变形。低锡铜-锡合金镀层孔隙率低、耐蚀性较好,也具有良好的钎焊性,宜用于电子电气产品的电镀保护层。
2.引自JB/T 10620—2006《金属覆盖层 铜-锡合金电镀层》。
(2)铜-锡合金镀层标识示例
铜-锡合金镀层标识由基体金属(或合金基体中主要成分)、镀层组成的化学符号(Cux-Sn,x表示合金镀层中铜的平均含量)、镀层最小厚度值(μm)等三部分组成。其镀层标识按以下示例中的顺序明确指出基体金属、镀层组成和镀层厚度。
【例1】 在钢基体(Fe)上电镀5μm厚度的铜含量为90%(质量分数)的铜-锡合金镀层。
其标识为:电镀层JB/T 10620-Fe/Cu(90)-Sn5
【例2】 在黄铜基体(Cu-Zn合金)上电镀3μm厚度的铜含量为85%(质量分数)的铜-锡合金镀层。
其标识为:电镀层JB/T 10620-Cu-Zn/Cu(85)-Sn3
4.6 金属镀覆及化学处理标识方法
国家标准GB/T 13911—2008《金属镀覆和化学处理标识方法》,适用于金属和非金属制件上进行电镀、化学镀及化学处理的标识。铝及铝合金表面化学处理的标识方法可参照本标准规定的通用标识方法。对金属镀覆和化学处理有的在该标准中未予规定的要求时,允许在有关的技术文件中加以说明。现将该标准摘略如下。
4.6.1 标识的组成部分
标识通常由下列4部分组成:
第1部分:包括镀覆方法,该部分为组成标识的必要元素。
第2部分:包括执行的标准和基体材料,该部分为组成标识的必要元素。
第3部分:包括镀层材料、镀层要求和镀层特征,该部分构成了镀覆层的主要工艺特性,组成的标识随工艺特性的变化而变化。
第4部分:包括每部分的详细说明,如化学处理的方式、应力消除的要求和合金元素的标注。该部分为组成标识的可选择元素(见本章4.7典型镀覆层的标识示例)。
金属镀覆和化学后处理的通用标识见表4-49。
表4-49 单金属及多层镀覆及化学后处理的通用标识

4.6.2 标识方法的排列顺序
金属镀覆及化学处理标识方法的排列顺序说明:
①镀覆方法应用中文表示。为便于使用,常用中文电镀、化学镀、机械镀、电刷镀、气相沉积等表示。
②本标准号为相应镀覆层执行的国家标准号或者行业标准号;如不执行国家或行业标准,应标识该产品的企业标准号,并注明该标准为企业标准,不允许无标准号产品。
③标准号后连接短横杠“-”。
④基体材料用符号表示,见表4-50常用基体材料的表示符号,对合金材料的镀覆必要时还必须标注出合金元素成分和含量。
⑤基体材料后用斜杠“/”隔开。
⑥当需要底镀层时,应标注底镀层材料、最小厚度(μm),底镀层特征有要求时,应按典型标识(见本章4.7节典型镀覆层的标识示例)规定,注明底镀层特征符号,如无要求,允许省略。如果不需要底镀层,则不需标注。
⑦当需要中镀层时,应标注中镀层材料、最小厚度(μm),中镀层特征有要求时,应按典型标识(见本章4.7节典型镀覆层的标识示例)规定,注明中镀层特征符号,如无要求,允许省略。如果不需要中镀层,则不需标注。
⑧应标注面镀层材料及最小厚度标识。面镀层特征有要求时,应按典型标识(见本章4.7节典型镀覆层的标识示例)规定,注明面镀层特征符号,如无要求,允许省略。
⑨镀层后处理为化学处理、电化学处理和热处理,标注方法见本章的有关章节的各类镀层标识规定。
⑩必要时需标注合金镀层材料的标识,二元合金镀层应在主要元素后面加括号注上主要元素含量,并用一横杠连接次要元素,如Sn(60)-Pb表示锡-铅合金镀层,其中锡质量含量为60%;合金成分含量无需标注或不便标注时,允许不标注。三元合金标注出两种元素成分的含量,依次类推。
4.6.3 金属镀覆方法及化学处理常用符号
金属材料用化学元素符号表示,合金材料用其主要成分的化学元素符号表示,非金属材料用国际通用缩写字母表示。常用基体材料的表示符号见表4-50。典型镀覆层的标识见下面各种镀层的标识示例。
表4-50 常用基体材料的表示符号

4.7 典型镀覆层的标识示例
4.7.1 金属基体上镍+铬和铜+镍+铬电镀层标识
金属基体上镍+铬、铜+镍+铬电镀层的标识,见GB/T 9797《金属覆盖层 镍+铬和铜+镍+铬电镀层》标识的规定。铜、镍、铬镀层特征标识符号见表4-51。典型标识示例如下,非典型标识见GB/T 9797。
【示例1】 电镀层GB/T 9797-Fe/Cu20a Ni30b Cr mc
该标识表示:在钢铁基体上镀覆20μm延展并整平铜+30μm光亮镍+0.3μm微裂纹铬的电镀层。
【示例2】 电镀层GB/T 9797-Zn/Cu20a Ni20b Cr mc
该标识表示:在锌合金基体上镀覆20μm延展并整平铜+20μm光亮镍+0.3μm微裂纹铬的电镀层。
【示例3】 电镀层GB/T 9797-Cu/Ni25p Cr mp
该标识表示:在铜合金基体上镀覆25μm半光亮镍+0.3μm微孔铬的电镀层。
【示例4】 电镀层GB/T 9797-Al/Ni20s Cr r
该标识表示:在铝合金基体上镀覆20μm缎面镍+0.3μm常规铬的电镀层。
4.7.2 塑料上镍+铬电镀层标识
塑料上镍+铬、铜+镍+铬电镀层的标识,见GB/T 12600《金属覆盖层 塑料上镍+铬电镀层》标识的规定。铜、镍、铬镀层特征标识符号见表4-51。标识示例如下。
表4-51 铜、镍、铬镀层特征标识符号

【示例1】 电镀层GB/T 12600-PL/Cu15a Ni10b Cr mp(或mc)
该标识表示:塑料基体上镀覆15μm延展并整平铜+10μm光亮镍+0.3μm微孔或微裂纹铬的电镀层。
【示例2】 电镀层GB/T 12600-PL/Ni20dp Ni20b Cr mp
该标识表示:塑料基体上镀覆20μm延展镍+20μm光亮镍+0.3μm微孔铬的电镀层。
示例2中的dp表示从专门预镀溶液中电镀延展性柱状镍镀层。
4.7.3 金属基体上装饰性镍、铜+镍电镀层标识
金属基体上镍、铜+镍电镀层的标识,见GB/T 9798《金属覆盖层 镍电沉积层》标识的规定。铜、镍、铬镀层特征标识符号见表4-51。标识示例如下。
【示例1】 电镀层GB/T 9798-Fe/Cu20a Ni25s
该标识表示:钢铁基体上镀覆20μm延展并整平铜+25μm缎面镍的电镀层。
【示例2】 电镀层GB/T 9798-Fe/Ni30p
该标识表示:钢铁基体上镀覆30μm半光亮镍的电镀层。
【示例3】 电镀层GB/T 9798-Zn/Cu10a Ni15b
该标识表示:锌合金基体上镀覆10μm延展并整平铜+15μm全光亮镍的电镀层。
【示例4】 电镀层GB/T 9798-Cu/Ni10b
该标识表示:铜合金基体上镀覆10μm全光亮镍的电镀层。
【示例5】 电镀层GB/T 9798-Al/Ni25b
该标识表示:铝合金基体上镀覆25μm全光亮镍的电镀层。
4.7.4 钢铁上锌电镀层、镉电镀层的标识
钢铁基体上锌电镀层、镉电镀层的标识,见GB/T 9799《金属及其他无机覆盖层 钢铁上经过处理的锌电镀层》和GB/T 13346《金属及其他无机覆盖层 钢铁上经过处理的镉电镀层》标识的规定。标识中有关锌电镀层、镉电镀层化学处理及分类符号见表4-52。标识示例如下。
表4-52 电镀锌和电镀镉后铬酸盐处理的表示符号

【示例1】 电镀层GB/T 9799-Fe/Zn25c1A
该标识表示:在钢铁基体上电镀锌层至少为25μm,电镀后镀层光亮铬酸盐处理。
【示例2】 电镀层GB/T 13346-Fe/Cd8c2C
该标识表示:在钢铁基体上电镀镉层至少为8μm,电镀后镀层彩虹铬酸盐处理。
4.7.5 工程用铬电镀层标识
工程用铬电镀层的标识见GB/T 11379 《金属覆盖层 工程用铬镀层》的规定。标识中工程用铬电镀层的特征符号见表4-53。为确保镀层与基体金属之间的结合力良好,工程用铬在镀前和镀后有时需要热处理。镀层热处理特征符号见表4-54。标识示例如下。
表4-53 工程用铬电镀层特征符号

表4-54 热处理特征符号

【示例1】 电镀层GB/T 11379-Fe//Cr50hr
该标识表示:在低碳钢基体上直接电镀厚度为50μm的常规硬铬的电镀层。
【示例2】 电镀层GB/T 11379-Al//Cr250hp
该标识表示:在铝合金基体上直接电镀厚度为250μm的微孔硬铬的电镀层。
【示例3】 电镀层GB/T 11379-Fe//Ni10sf/Cr25hr
该标识表示:在钢基体上电镀底镀层为10μm厚的无硫镍+25μm厚的常规硬铬的电镀层。
【示例4】 电镀层GB/T 11379-Fe/[SR(210)2]/Cr50hr/[ER(210)22]
该标识表示:在钢基体上电镀厚度为50μm的常规硬铬电镀层,电镀前在210℃下进行消除应力的热处理2h,电镀后在210℃下进行降低脆性的热处理22h。
标识时有以下两点需要注意。
①铬镀层及面镀层和底镀层的符号,每一层之间按镀层的先后顺序用斜线(/)分开。镀层标识应包括镀层的厚度(以μm计)和热处理要求。工序间不作要求的步骤应用双斜线(//)标明。
②镀层热处理特征标识,如[SR(210)1]表示在210℃下消除应力处理1h。
4.7.6 工程用镍电镀层标识
工程用镍电镀层标识见GB/T 12332《金属覆盖层 工程用镍电镀层》的规定。标识中工程镍镀层类型、含硫量及延展性标识见表4-55。为确保镀层与基体金属之间的结合力良好,工程用镍在镀前和镀后有时需要热处理。镀层热处理特征符号见表4-54(见工程用铬电镀层的热处理特征符号表)。标识示例如下。
表4-55 不同类型的镍电镀层的符号、硫含量及延展性

【示例1】 电镀层GB/T 12332-Fe//Ni50sf
该标识表示:在钢基体上电镀最小局部厚度为50μm、无硫的工程用镍电镀层。
【示例2】 电镀层GB/T 12332-Al//Ni75pd
该标识表示:在铝合金基体上电镀最小局部厚度为75μm、无硫的、镍层含有共沉积的碳化硅颗粒的工程用镍电镀层。
【示例3】 电镀层GB/T 12332-Fe/[SR(210)2]/Ni25sf/[ER(210)22]
该标识表示:在高强度钢基体上电镀的最小局部厚度为25μm、无硫的工程用镍电镀层,电镀前在210℃下进行消除应力的热处理2h,电镀后在210℃下进行降低脆性的热处理22h。
注意,镍或镍合金镀层及底镀层和面镀层的符号,每一层之按镀层的先后顺序用斜线(/)分开。镀层标识应包括镀层的厚度(以μm计)和热处理要求。工序间不作要求的步骤应用双斜线(//)标明。
4.7.7 化学镀(自催化)镍-磷合金镀层标识
化学镀镍-磷镀层的质量与基体金属的特性、镀层及热处理条件有密切关系(见GB/T 13913《金属覆盖层 化学镀镍-磷合金镀层 规范和试验方法》的说明和规定)。所以化学镀镍-磷镀层的标识包括所规定的通用标识外,必要时还包括基体金属特殊合金的标识、基体和镀层消除内应力的要求、化学镀镍-磷镀层中的磷含量。双斜线(//)将用于指明某一步骤或操作没有被例举或被省略。
化学镀镍-磷镀层应用符号NiP标识,并在紧跟其后的圆括弧中填入镀层磷含量的数值,然后再在其后标注出化学镀镍-磷镀层的最小局部厚度(μm)。
典型标识示例如下,非典型的化学镀层的标识参见GB/T 13913。
【示例1】 化学镀镍-磷镀层GB/T 13913-Fe<16Mn>[SR(210)22]/NiP(10)15/Cr0.5[ER(210)22]
该标识表示:在16Mn钢基体上化学镀含磷量为10%(质量分数),厚15μm的镍-磷镀层,镍-磷镀层前要求在210℃温度下进行22h的消除应力的热处理,化学镀镍后再在其表面电镀0.5μm厚的铬。最后在210℃温度下进行22h的消除氢脆的热处理。
【示例2】 化学镀镍-磷镀层GB/T 13913-Al<2B12>//NiP(10)15/Cr0.5//
该标识表示:在2B12铝合金基体上化学镀含磷量为10%(质量分数),厚15μm的镍-磷镀层,化学镀镍后再在其表面电镀0.5μm厚的铬。
【示例3】 化学镀镍-磷镀层GB/T 13913-Cu<H62>//NiP(10)15/Cr0.5//
该标识表示:在铜合金基体上镀覆与【示例1】相同的镀层,不需要热处理。
4.7.8 工程用银和银合金电镀层标识
工程用银和银合金电镀层的标识见ISO 4521标识的规定。银和银合金镀层常用厚度见表4-56。典型标识示例如下,非典型标识参见ISO 4521。
表4-56 银和银合金镀层常用厚度

注:必要时,银和银合金镀层的厚度也可采用2μm的倍数。
【示例1】 电镀层ISO 4521-Fe/Ag10
该标识表示:在钢铁金属基体上电镀厚度为10μm的银电镀层。
【示例2】 电镀层ISO 4521-Fe/Cu10 Ni10 Ag5
该标识表示:在钢铁金属基体上电镀厚度为10μm的铜电镀层+10μm的镍电镀层+5μm的银电镀层。
【示例3】 电镀层ISO 4521-Al/Ni20 Ag5
该标识表示:在铝或铝合金基体上电镀厚度为20μm的镍镀层+5μm的银电镀层。
4.7.9 工程用金和金合金镀层标识
工程用金和金合金镀层的标识见ISO 4523标识的规定。如果需要表示金的金属纯度时,可在该金属的元素符号后用括号( )列出质量分数,精确至小数点后一位。金和金合金镀层常用厚度见表4-57。标识示例如下。
表4-57 金和金合金镀层常用厚度

【示例1】 电镀层ISO 4523-Fe/Au(99.9)2.5
该标识表示:在钢铁金属基体上电镀厚度为2.5μm纯度为99.9%(质量分数)的金电镀层。
【示例2】 电镀层ISO 4523-Fe/Cu10 Ni5 Au1
该标识表示:在钢铁金属基体上电镀厚度为10μm的铜镀层,再电镀厚度为5μm的镍镀层后,电镀1μm的金电镀层。
【示例3】 电镀层ISO 4523-Al/Ni20 Au0.5
该标识表示:在铝或铝合金基体上电镀厚度为20μm的镍镀层后,电镀0.5μm的金电镀层。
4.7.10 金属基体上锡和锡合金镀层标识
金属基体上锡电镀层、锡-铅合金电镀层、锡-镍合金电镀层的表面特征,在某些情况下与镀层的使用要求有关(见GB/T 12599、GB/T 17461、GB/T 17462的说明)。锡和锡合金镀层的标识应包括镀层表面特征内容(见表4-58),合金电镀层应在主要金属符号后用括号标注主要元素的含量。非典型标识参见GB/T 12599、GB/T 17461、GB/T 17462,典型标识示例如下。
表4-58 锡和锡合金镀层表面特征符号

【示例1】 电镀层GB/T 12599-Fe/Ni2.5 Sn 5f
该标识表示:在钢或铁基体金属上,镀覆2.5μm镍底镀层+5μm锡镀层,镀后应用熔流处理。
【示例2】 电镀层GB/T 17461-Fe/Ni5 Sn60-Pb 10f
该标识表示:在钢或铁基体金属上,镀覆5μm镍底镀层+10μm公称含锡量为60%(质量分数)的锡-铅合金镀层,并且镀后经过热熔处理。
【示例3】 电镀层GB/T 17462-Fe/Cu2.5 Su-Ni 10
该标识表示:在钢或铁基体金属上,镀覆2.5μm铜底镀层+10μm锡含量无要求的锡-镍合金电镀层。